- お役立ち記事
- Fundamentals and mechanisms of grinding and application to high-precision machining
月間76,176名の
製造業ご担当者様が閲覧しています*
*2025年3月31日現在のGoogle Analyticsのデータより
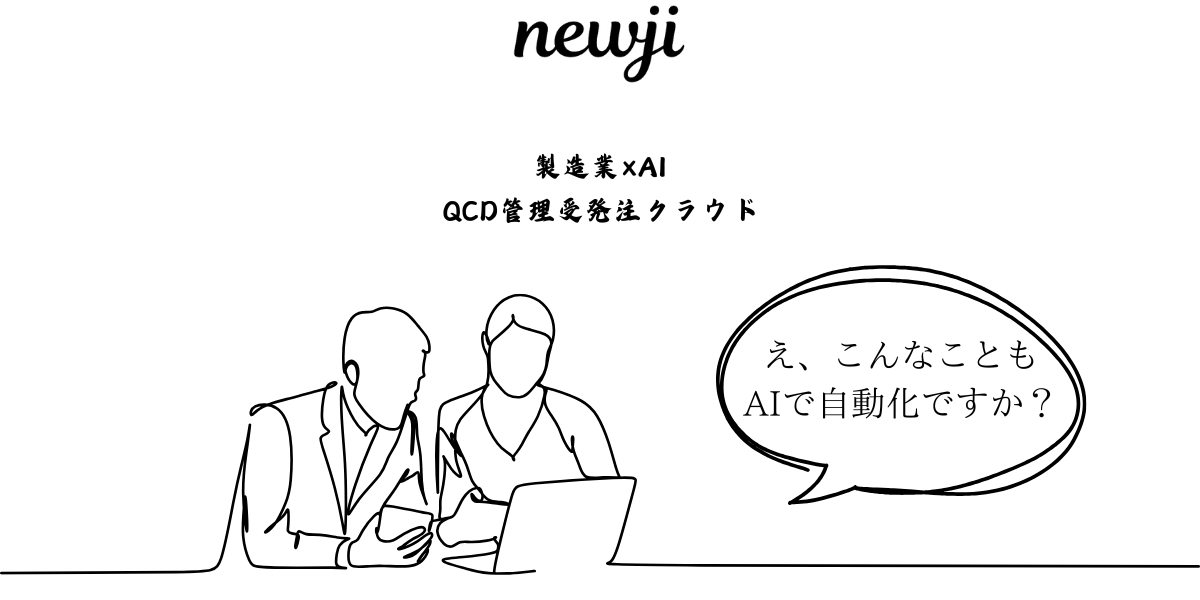
Fundamentals and mechanisms of grinding and application to high-precision machining
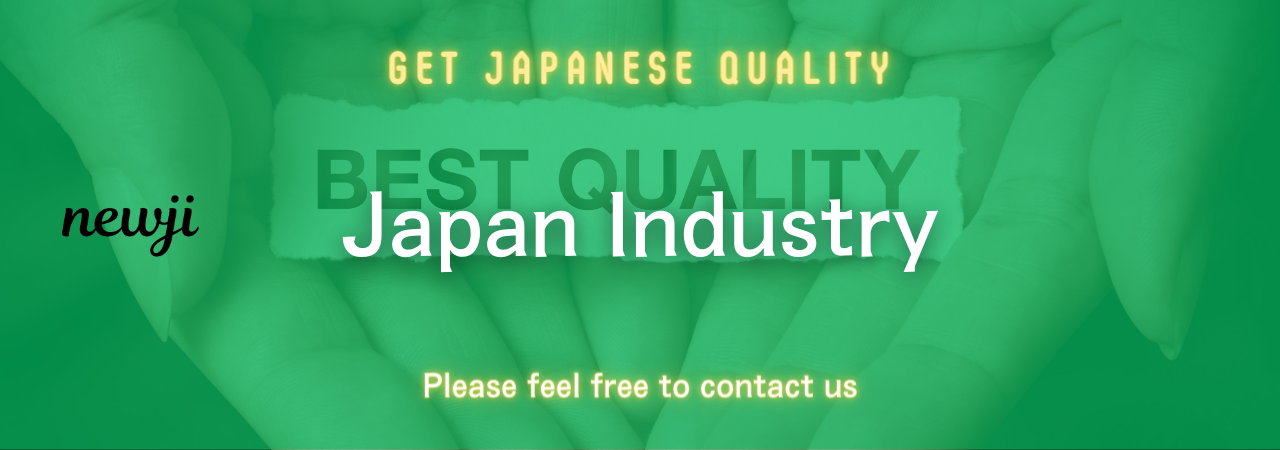
目次
Understanding Grinding: The Basics
Grinding is a crucial process used in manufacturing and machining to refine and shape materials to precise specifications.
It is a popular technique for achieving high precision and fine surface finishes.
Grinding involves using an abrasive wheel as a cutting tool to remove small amounts of material from a workpiece.
This process is essential for achieving the desired size or shape of a product, ensuring its function and quality.
The abrasive wheel, made of abrasive grains and a bonding matrix, performs the cutting action.
As the wheel rotates, these grains engage with the workpiece to remove material bit by bit.
Grinding is widely recognized not just for high-precision machining tasks but also for the significant role it plays in shaping different materials.
Mechanisms of the Grinding Process
Grinding works on the principle of abrasion, where the abrasive wheel comes into contact with the workpiece, cutting away small fragments.
The rate at which material is removed is determined by the grinding wheel’s properties, including the grain size, hardness, and the bond type holding the grains together.
Abrasive Grain Size
The grain size of the abrasive wheel is a critical factor that influences the grinding process.
Smaller grains produce a finer surface finish but may reduce the rate of material removal.
Conversely, larger grains can remove material more quickly but may leave a rougher finish.
Hardness
The hardness of the abrasive is also significant.
Harder abrasives can cut through tougher materials, making them suitable for various applications.
However, choosing the optimal hardness ensures efficiency without excessively wearing down the wheel.
Bond Type
The bond type in the grinding wheel dictates how the grains are held together.
Different bond types affect both the wheel’s performance and longevity.
Bonds may be vitrified, resin-based, or metal-based, each offering unique characteristics suitable for specific machining tasks and materials.
High-Precision Machining with Grinding
High-precision machining demands meticulous attention to detail, where grinding shines as a pivotal technique.
To achieve high precision, the parameters of the grinding process must be finely tuned.
Key factors include the speed of the grinding wheel, the feed rate of the workpiece, and cooling methods to manage the heat generated during the process.
Wheel Speed and Workpiece Feed Rate
Achieving high precision often starts with the correct wheel speed and feed rate.
An appropriate wheel speed ensures the abrasive engages smoothly, minimizing chatter or excessive heat build-up.
Simultaneously, the feed rate controls the speed at which the workpiece moves, which affects both surface finish and removal rate.
Heat Management
Heat generated by friction during grinding can alter a workpiece’s properties, leading to defects.
Therefore, effective cooling methods such as using cutting fluids or applying air jets are essential to prevent thermal damage, ensuring the dimensional integrity of precision components.
Surface Finish and Tolerances
Precision grinding’s goal is not only to meet dimensional specifications but also to achieve a high-quality surface finish.
Maintaining tight tolerances ensures component compatibility within mechanical systems.
This is especially crucial in industries such as aerospace, automotive, and electronics, where even minor deviations can lead to significant issues.
Applications of Grinding in Industry
Grinding finds its application across an array of industries, owing to its versatility and effectiveness. From tool-making to advanced technological sectors, grinding plays an integral role in manufacturing processes.
Tool Manufacturing
Tool making often requires durable tools with intricate shapes and minimal tolerances.
Grinding delivers the precision necessary for creating cutting edges and drill bits, ensuring high-performance tools suitable for various machining applications.
Aerospace and Automotive Industries
In aerospace and automotive sectors, grinding is used to produce components that must adhere strictly to safety and performance standards.
Precision grinding for jet engine parts or vehicle transmissions ensures operational reliability, where even the smallest imperfection can lead to catastrophic failures.
Medical Equipment
The medical industry demands components with stringent cleanliness and precision standards.
Grinding is utilized to manufacture surgical instruments and implants, which require smooth, biocompatible surfaces.
Ensuring precision in medical applications not only enhances performance but also increases patient safety.
Future Trends in Grinding Technology
As industries continue to evolve, so does the need for efficient and precise grinding techniques.
Emerging trends focus on automation, advanced materials, and environmentally friendly practices.
Automation and Robotics
Incorporating automation into grinding processes reduces human error and increases production efficiency.
Robotics, combined with computer numerical control (CNC) systems, enables consistent results, optimized accuracy, and minimized waste.
Advanced Materials
As new materials such as composites and ceramics develop, grinding technology must adapt to handle these harder, more complex substances.
Innovations in abrasive materials and bonding agents are vital to maintaining efficacy.
Sustainable Practices
There is a growing emphasis on creating sustainable processes within the manufacturing industry.
Recycling grinding effluents, using eco-friendly coolants, and reducing energy consumption are steps toward minimizing the environmental impact of grinding activities.
In conclusion, the fundamentals and mechanisms of grinding are vital to various manufacturing and machining operations, providing high precision and quality in component fabrication.
As technology advances, adapting grinding processes to meet these new demands ensures that this age-old technique remains relevant and essential to modern industrial applications.
資料ダウンロード
QCD管理受発注クラウド「newji」は、受発注部門で必要なQCD管理全てを備えた、現場特化型兼クラウド型の今世紀最高の受発注管理システムとなります。
ユーザー登録
受発注業務の効率化だけでなく、システムを導入することで、コスト削減や製品・資材のステータス可視化のほか、属人化していた受発注情報の共有化による内部不正防止や統制にも役立ちます。
NEWJI DX
製造業に特化したデジタルトランスフォーメーション(DX)の実現を目指す請負開発型のコンサルティングサービスです。AI、iPaaS、および先端の技術を駆使して、製造プロセスの効率化、業務効率化、チームワーク強化、コスト削減、品質向上を実現します。このサービスは、製造業の課題を深く理解し、それに対する最適なデジタルソリューションを提供することで、企業が持続的な成長とイノベーションを達成できるようサポートします。
製造業ニュース解説
製造業、主に購買・調達部門にお勤めの方々に向けた情報を配信しております。
新任の方やベテランの方、管理職を対象とした幅広いコンテンツをご用意しております。
お問い合わせ
コストダウンが利益に直結する術だと理解していても、なかなか前に進めることができない状況。そんな時は、newjiのコストダウン自動化機能で大きく利益貢献しよう!
(β版非公開)