- お役立ち記事
- Fundamentals and mechanisms of metal fatigue and application to fatigue life prediction and fatigue-resistant design using FEM
Fundamentals and mechanisms of metal fatigue and application to fatigue life prediction and fatigue-resistant design using FEM
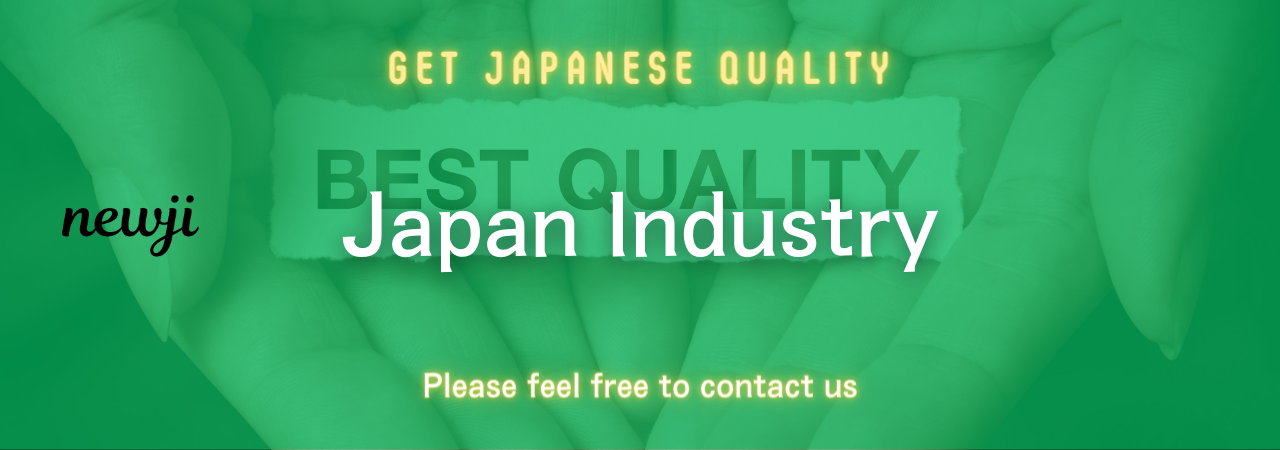
目次
Understanding Metal Fatigue
Metal fatigue is a progressive and localized structural damage that occurs when a material is subjected to cyclic loading.
This phenomenon is significant in engineering and can lead to the failure of structures or components, even if the applied load is below the yield strength of the material.
Understanding the fundamentals of metal fatigue is crucial for designing components that endure repetitive stress without failing.
The concept of metal fatigue revolves around the repeated application of stress or strain.
Over time, the material develops small cracks, which can grow and eventually lead to fracture.
This type of damage is typically undetectable by visual inspection until it is critically advanced.
The Mechanism of Metal Fatigue
The mechanism of metal fatigue involves three primary stages: crack initiation, crack propagation, and final fracture.
Initially, small microcracks form due to the material’s imperfections or stress concentrations.
These microcracks can nucleate at microscopic levels of material defects or surface discontinuities.
During the crack propagation stage, the microcracks begin to expand with each loading cycle.
The rate of crack growth depends on several factors, including the magnitude of the applied stress, the characteristics of the material, and the environment in which the material operates.
Eventually, the crack reaches a critical size, leading to final fracture.
At this point, the component can no longer withstand the applied load, resulting in catastrophic failure.
Factors Affecting Metal Fatigue
Several factors influence metal fatigue, including material properties, stress levels, loading frequency, environmental conditions, and surface treatment.
– **Material Properties:**
Different metals have varying resistance to fatigue.
For example, some high-strength alloys may be more prone to fatigue due to their brittleness, while ductile materials might absorb more energy before crack initiation.
– **Stress Levels:**
The level of applied stress significantly impacts the fatigue life of a material.
Higher stress levels lead to faster crack initiation and propagation.
– **Loading Frequency:**
The frequency of cyclic loading also affects fatigue life.
Higher frequencies often accelerate the fatigue process due to increased stress cycles over time.
– **Environmental Conditions:**
Corrosive environments can exacerbate metal fatigue by accelerating crack growth.
This is known as corrosion fatigue, where the interplay between mechanical stress and chemical reactions reduces the material’s resistance.
– **Surface Treatment:**
Techniques such as shot peening or surface polishing can enhance fatigue life.
These methods help in reducing surface stress concentrations, thus delaying crack initiation.
Fatigue Life Prediction
Predicting the fatigue life of a component is essential in engineering to ensure reliability and safety.
One common method for fatigue life prediction is the S-N curve (Stress-Number of cycles), which represents the relationship between the cyclic stress and the number of cycles to failure.
Engineers use this curve to estimate the fatigue life under specific loading conditions.
Additionally, fracture mechanics approaches are employed to predict the growth of existing cracks.
This involves using mathematical models to estimate the progression of cracks under cyclic loading.
Knowing the rate of crack growth allows engineers to determine when a component may need maintenance or replacement.
Fatigue-Resistant Design Using FEM
Finite Element Method (FEM) is a powerful tool used in fatigue-resistant design.
FEM involves creating a detailed computational model of a component and simulating the mechanical behavior under various load conditions.
Benefits of Using FEM
– **Detailed Analysis:**
FEM allows for a comprehensive analysis of stresses and strains within a component, helping identify potential fatigue hotspots.
– **Optimization:**
By simulating different design scenarios, engineers can optimize structures for better fatigue performance, ensuring that stress concentrations are minimized.
– **Material Customization:**
FEM can help in selecting appropriate materials and surface treatments tailored to specific operational requirements, enhancing fatigue resistance.
– **Predictive Maintenance:**
With FEM models, it is easier to predict potential fatigue failures and plan maintenance strategies accordingly, improving the overall safety and reliability of the system.
Applying FEM in Fatigue-resistant Design
1. **Model Creation:**
Creating an accurate FEM model is crucial.
This involves defining the geometry, material properties, boundary conditions, and loading scenarios.
2. **Simulation:**
Conduct simulations to assess stress distributions and identify critical stress regions.
This step is vital for determining areas susceptible to fatigue.
3. **Validation:**
Validate the FEM model with experimental results to ensure its accuracy.
This involves comparing simulation data with physical stress tests and adjusting the model as necessary.
4. **Design Modification:**
Based on FEM results, make necessary modifications to the design.
This could include changing material specifications, altering component geometries, or implementing surface treatments to improve fatigue resistance.
5. **Iterative Process:**
Fatigue-resistant design is often an iterative process, requiring multiple cycles of simulation and design adjustments to achieve the desired level of performance.
In conclusion, understanding the fundamentals and mechanisms of metal fatigue is essential for predicting fatigue life and designing fatigue-resistant components.
The application of FEM significantly enhances this process by providing a detailed and flexible approach to analyzing and improving designs.
Through careful consideration of material properties, stress levels, and environmental conditions, engineers can create durable and reliable components that withstand the test of time and repetitive use.
資料ダウンロード
QCD調達購買管理クラウド「newji」は、調達購買部門で必要なQCD管理全てを備えた、現場特化型兼クラウド型の今世紀最高の購買管理システムとなります。
ユーザー登録
調達購買業務の効率化だけでなく、システムを導入することで、コスト削減や製品・資材のステータス可視化のほか、属人化していた購買情報の共有化による内部不正防止や統制にも役立ちます。
NEWJI DX
製造業に特化したデジタルトランスフォーメーション(DX)の実現を目指す請負開発型のコンサルティングサービスです。AI、iPaaS、および先端の技術を駆使して、製造プロセスの効率化、業務効率化、チームワーク強化、コスト削減、品質向上を実現します。このサービスは、製造業の課題を深く理解し、それに対する最適なデジタルソリューションを提供することで、企業が持続的な成長とイノベーションを達成できるようサポートします。
オンライン講座
製造業、主に購買・調達部門にお勤めの方々に向けた情報を配信しております。
新任の方やベテランの方、管理職を対象とした幅広いコンテンツをご用意しております。
お問い合わせ
コストダウンが利益に直結する術だと理解していても、なかなか前に進めることができない状況。そんな時は、newjiのコストダウン自動化機能で大きく利益貢献しよう!
(Β版非公開)