- お役立ち記事
- Fundamentals and optimization technology of pump hydraulic design and application to fluid-related vibration countermeasures
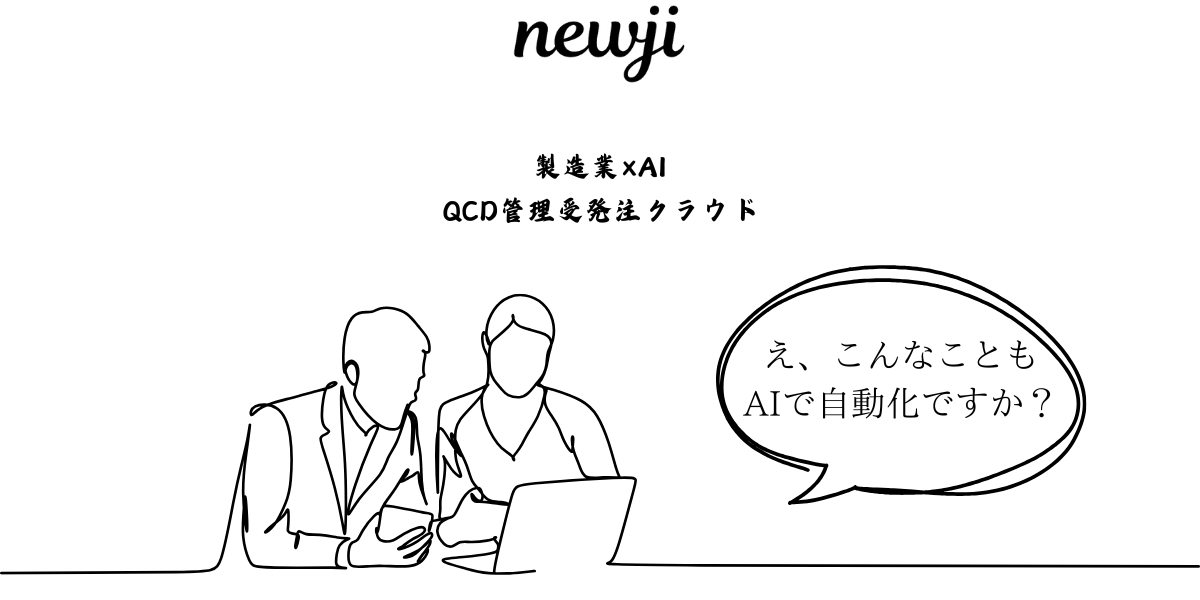
Fundamentals and optimization technology of pump hydraulic design and application to fluid-related vibration countermeasures
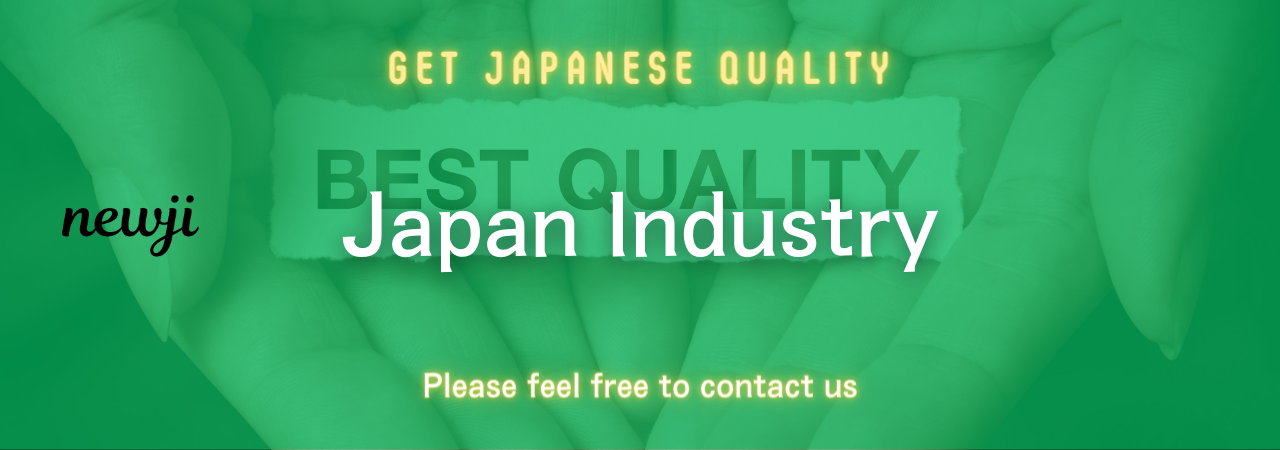
目次
Introduction to Pump Hydraulic Design
Pump hydraulic design is a crucial aspect of engineering that directly impacts the efficiency and performance of fluid systems.
Understanding the fundamentals of pump design helps engineers create systems that are both effective and reliable.
This involves the careful consideration of fluid dynamics, mechanical components, and system requirements to optimize performance.
The primary objective of pump design is to create a device capable of moving fluid efficiently from one point to another.
This process requires an understanding of how fluids behave within the system and a careful selection of pump components to suit specific applications.
By focusing on key design principles, engineers can ensure that pumps operate efficiently and effectively, minimizing energy consumption and maximizing output.
Core Principles of Hydraulic Design
The design of a hydraulic pump involves several core principles that must be addressed to ensure optimal operation.
These principles include the selection of pump type, impeller design, and materials used in construction.
Selection of Pump Type
There are various types of pumps available, each suited to different applications.
Centrifugal pumps, for instance, are commonly used for moving large volumes of fluid at lower pressures.
They utilize rotational energy to impart velocity to the fluid, converting kinetic energy into pressure energy.
Positive displacement pumps, on the other hand, are suitable for applications requiring high pressure and precise flow rates.
These pumps work by trapping a fixed amount of fluid and displacing it, allowing for consistent flow regardless of pressure changes.
Impeller Design
The impeller is a critical component in a pump, affecting its efficiency and performance.
An impeller’s design must consider factors such as size, number of blades, and blade angle to optimize flow and reduce energy losses.
Different impeller designs, such as closed, semi-open, or open, offer varying levels of efficiency and are selected based on the specific requirements of the application.
Careful computational analysis and testing are often necessary to determine the best impeller design.
Material Selection
The materials used in pump construction must withstand the operating conditions, including pressure, temperature, and the corrosive nature of the fluid being transported.
Common materials include stainless steel, cast iron, and various polymers, each selected based on compatibility with the fluid and environmental conditions.
Choosing the right materials extends the pump’s lifespan and reduces maintenance costs by preventing corrosion and wear.
Optimization Techniques in Pump Design
Optimizing pump performance involves fine-tuning design elements to achieve the best balance between efficiency, cost, and durability.
Several advanced techniques can be employed to enhance pump operation and performance.
Computational Fluid Dynamics (CFD)
CFD is a powerful tool that allows engineers to simulate fluid flow within a pump.
By creating detailed models, CFD helps visualize issues such as turbulence and recirculation, enabling engineers to make informed design improvements.
CFD simulations provide valuable insights into how design changes affect performance, allowing for optimization that reduces energy consumption and increases output efficiency.
Variable Speed Drives (VSD)
VSDs are employed to adjust the pump’s operating speed to match system requirements, offering significant energy savings.
By modulating the pump speed, VSDs reduce wear and tear, extend equipment life, and decrease operational costs.
Incorporating VSDs into pump systems allows for adaptable performance, responding dynamically to changes in demand without compromising efficiency.
Advanced Impeller Designs
Innovations in impeller designs, such as the implementation of non-clogging features or anti-cavitation geometries, improve the reliability and efficiency of pumps.
These designs help reduce blockages and cavitation-related issues, which are common causes of pump failure.
By enhancing impeller geometry, engineers can decrease maintenance needs and extend the operational life of pumps.
Fluid-Related Vibration Countermeasures
Addressing vibrations in fluid systems is crucial for maintaining pump reliability and performance.
Excessive vibrations can lead to mechanical failures, piping stress, and reduced efficiency.
Understanding Vibration Causes
Vibrations in pump systems can be caused by several factors, including operational conditions, design flaws, or external influences.
Common sources include unbalanced rotating parts, pressure fluctuations, and improper pump-piping interactions.
Identifying the root causes of vibration is the first step in implementing effective countermeasures.
Vibration Analysis and Diagnostics
Vibration analysis involves using specialized equipment to monitor and diagnose vibration sources and levels within a pump system.
By analyzing vibration patterns, engineers can pinpoint problematic areas and develop targeted solutions to mitigate vibrations.
Regular monitoring and diagnostics are essential for early detection of potential issues, preventing costly repairs.
Design Modifications and Balancing
Implementing design modifications, such as improving support structures or enhancing shaft alignment, can alleviate vibration problems.
Balancing rotating components reduces unbalanced forces, directly mitigating vibration levels.
Engineering solutions like vibration dampers or isolation systems further reduce vibrational impact on the system, enhancing overall reliability.
Conclusion
Pump hydraulic design is a complex yet vital aspect of engineering, ensuring fluid systems operate efficiently and effectively.
By understanding core design principles and utilizing advanced optimization techniques, engineers can develop pumps that are both innovative and reliable.
Addressing fluid-related vibration issues through careful analysis and design modifications ensures longevity and efficiency in pump systems.
Together, these elements form the foundation of successful pump design, benefiting industries that rely on fluid transport and management.
資料ダウンロード
QCD調達購買管理クラウド「newji」は、調達購買部門で必要なQCD管理全てを備えた、現場特化型兼クラウド型の今世紀最高の購買管理システムとなります。
ユーザー登録
調達購買業務の効率化だけでなく、システムを導入することで、コスト削減や製品・資材のステータス可視化のほか、属人化していた購買情報の共有化による内部不正防止や統制にも役立ちます。
NEWJI DX
製造業に特化したデジタルトランスフォーメーション(DX)の実現を目指す請負開発型のコンサルティングサービスです。AI、iPaaS、および先端の技術を駆使して、製造プロセスの効率化、業務効率化、チームワーク強化、コスト削減、品質向上を実現します。このサービスは、製造業の課題を深く理解し、それに対する最適なデジタルソリューションを提供することで、企業が持続的な成長とイノベーションを達成できるようサポートします。
オンライン講座
製造業、主に購買・調達部門にお勤めの方々に向けた情報を配信しております。
新任の方やベテランの方、管理職を対象とした幅広いコンテンツをご用意しております。
お問い合わせ
コストダウンが利益に直結する術だと理解していても、なかなか前に進めることができない状況。そんな時は、newjiのコストダウン自動化機能で大きく利益貢献しよう!
(Β版非公開)