- お役立ち記事
- Fundamentals and practical points of DC motor control design
月間76,176名の
製造業ご担当者様が閲覧しています*
*2025年3月31日現在のGoogle Analyticsのデータより
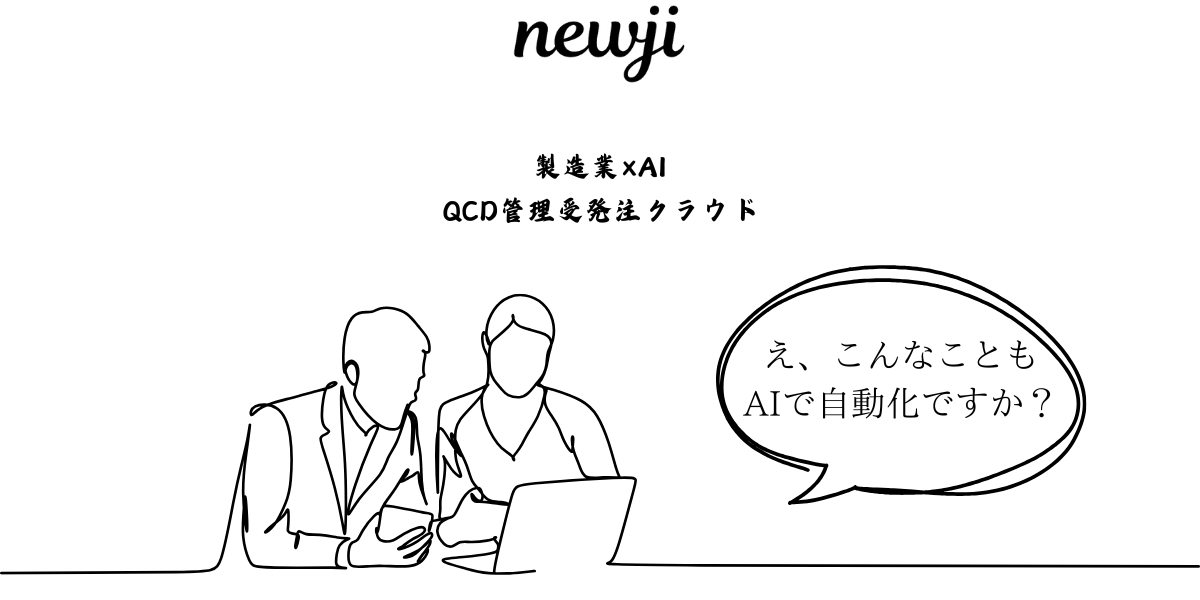
Fundamentals and practical points of DC motor control design
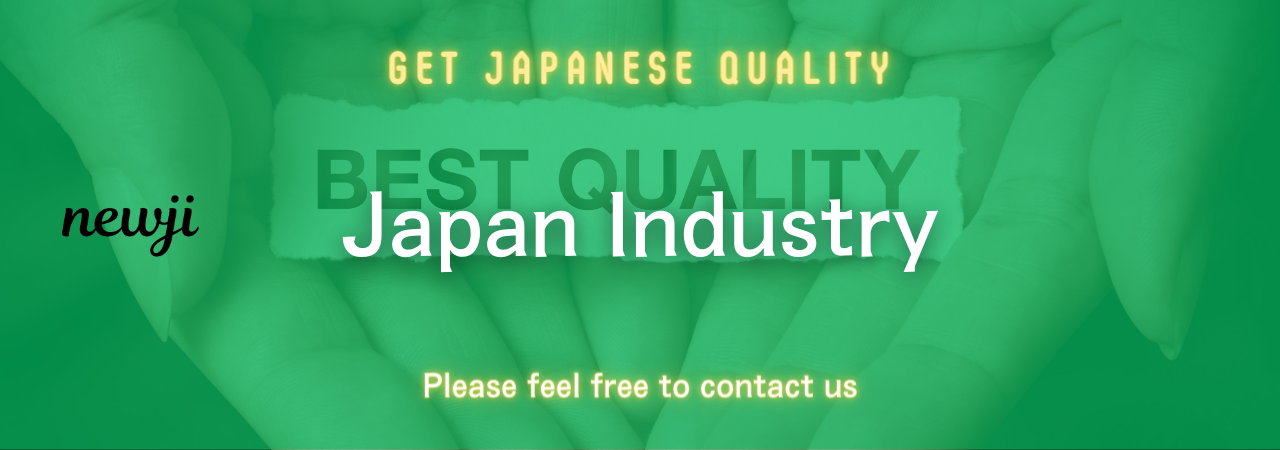
目次
What is a DC Motor?
A DC motor is a type of electric motor that runs on direct current electricity.
These motors are widely used in various applications due to their ability to provide precise control of speed and torque.
The basic principle behind DC motors is the interaction between the magnetic fields generated by the stator and the rotor.
Components of a DC Motor
Understanding the components of a DC motor is essential for designing effective motor control systems.
A typical DC motor comprises several key parts:
– **Stator**: This stationary part of the motor supplies a magnetic field through either permanent magnets or electromagnets.
– **Rotor**: Also known as the armature, this rotating component is where the electrical current interacts with the magnetic field.
– **Commutator and Brushes**: These components facilitate the current flow to the rotor, allowing for rotation by reversing the current direction within the motor.
How DC Motor Control Works
DC motor control focuses on managing the speed, direction, and torque of the motor.
This control is achieved by manipulating the voltage and current supplied to the motor.
Speed Control
Speed control in DC motors can be accomplished using various methods such as voltage control, armature resistance control, and field flux control.
– **Voltage Control**: Adjusting the voltage supplied to the motor can change its speed.
Higher voltage typically results in a higher speed.
– **Armature Resistance Control**: By adding external resistance in series with the armature, the motor speed can be varied.
– **Field Flux Control**: Altering the strength of the magnetic field can control the speed, where decreasing the field strength increases the speed.
Direction Control
The direction in which a DC motor rotates can be changed by reversing the current flow through either the armature or the field winding.
This can be performed using switches or H-bridge circuits, enabling bidirectional motor control.
Torque Control
Torque in a DC motor is proportional to the armature current and the field flux.
By adjusting these parameters, the torque produced by the motor can be controlled to meet specific application requirements.
Fundamentals of DC Motor Control Design
Designing an effective DC motor control system involves understanding the fundamental parameters and considering certain practical points.
Understanding Parameters
– **Voltage Requirements**: It is essential to know the voltage range for efficient motor operation and control.
– **Current Ratings**: Ensure the motor driver circuit can handle the current demands of the motor to prevent overheating or damage.
– **Speed and Torque Characteristics**: Understand the motor’s performance curve, which details how speed and torque vary with different loads and voltages.
Control Strategies
Several control strategies are often employed in DC motor design, including:
– **PWM (Pulse Width Modulation) Control**: A widely used technique where the voltage applied to the motor is switched on and off at a high frequency.
Adjusting the duty cycle of the PWM signal effectively controls the motor speed.
– **Feedback Control**: Closed-loop systems use feedback devices like encoders to monitor motor speed and position, allowing for precise control by comparing the desired and actual motor performance.
Practical Points for DC Motor Control Design
When designing a DC motor control system, several practical considerations can ensure optimal performance and longevity of the system.
Thermal Management
Proper thermal management is crucial in preventing overheating.
This can be achieved by using heat sinks, fans, or better insulation, as well as ensuring that all components are within their thermal limits during operation.
Protection Mechanisms
Include protective devices such as fuses, circuit breakers, and thermal cutoffs to guard against overcurrent situations and potential motor burnout.
Implementing short-circuit protection is also critical for safety and system integrity.
Selecting Suitable Components
Choose appropriate electronic components and materials that can withstand the environmental conditions and electrical demands of the application.
Emphasize quality and durability to ensure system reliability.
Sustainability and Maintenance
Design the motor control system with sustainable practices in mind, ensuring that it meets energy efficiency standards.
Additionally, establish maintenance procedures to regularly inspect and service the motor and control system for long-term operation.
By understanding these fundamentals and practical considerations, engineers and designers can develop efficient and reliable DC motor control systems for various applications.
資料ダウンロード
QCD管理受発注クラウド「newji」は、受発注部門で必要なQCD管理全てを備えた、現場特化型兼クラウド型の今世紀最高の受発注管理システムとなります。
ユーザー登録
受発注業務の効率化だけでなく、システムを導入することで、コスト削減や製品・資材のステータス可視化のほか、属人化していた受発注情報の共有化による内部不正防止や統制にも役立ちます。
NEWJI DX
製造業に特化したデジタルトランスフォーメーション(DX)の実現を目指す請負開発型のコンサルティングサービスです。AI、iPaaS、および先端の技術を駆使して、製造プロセスの効率化、業務効率化、チームワーク強化、コスト削減、品質向上を実現します。このサービスは、製造業の課題を深く理解し、それに対する最適なデジタルソリューションを提供することで、企業が持続的な成長とイノベーションを達成できるようサポートします。
製造業ニュース解説
製造業、主に購買・調達部門にお勤めの方々に向けた情報を配信しております。
新任の方やベテランの方、管理職を対象とした幅広いコンテンツをご用意しております。
お問い合わせ
コストダウンが利益に直結する術だと理解していても、なかなか前に進めることができない状況。そんな時は、newjiのコストダウン自動化機能で大きく利益貢献しよう!
(β版非公開)