- お役立ち記事
- Fundamentals and practical points of “Toyota-style why-why analysis” and application to prevention of defects
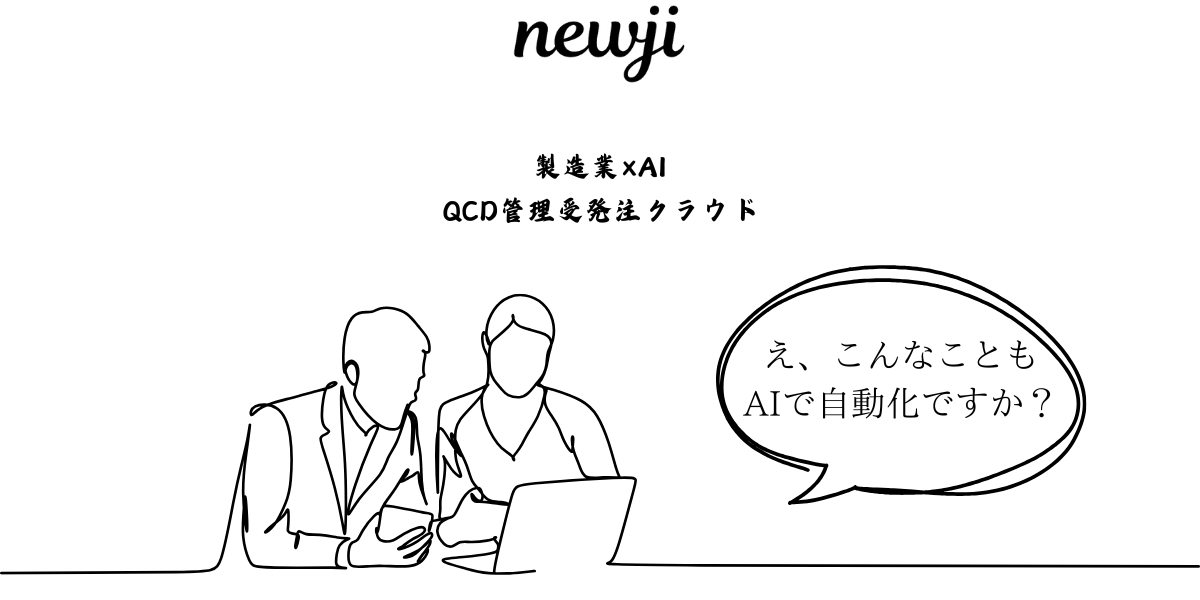
Fundamentals and practical points of “Toyota-style why-why analysis” and application to prevention of defects
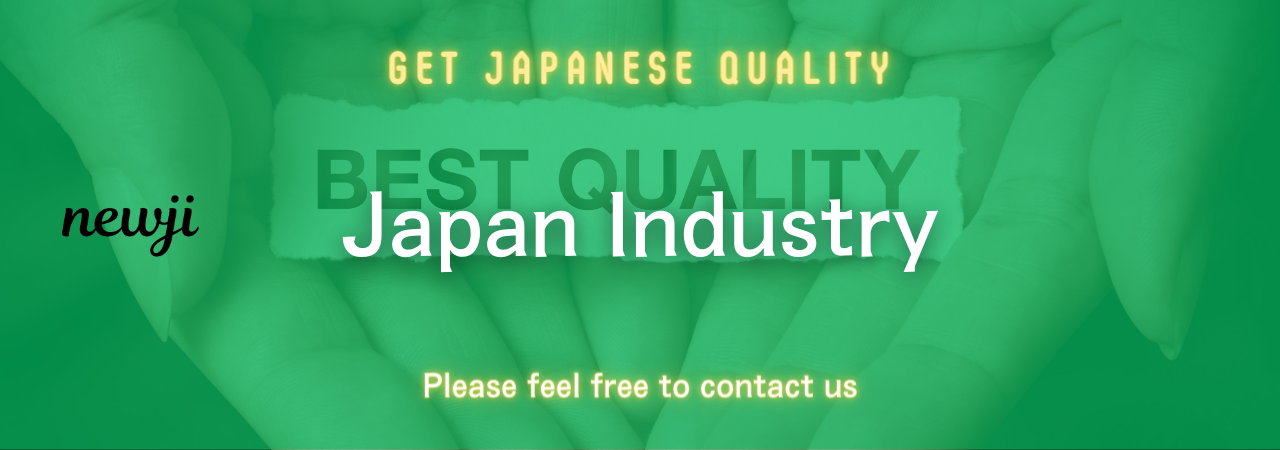
目次
Understanding the Toyota-Style Why-Why Analysis
The Toyota-style why-why analysis is a problem-solving technique developed by the Toyota Motor Corporation.
It’s a systematic process that digs deeper into issues by asking “why” questions repeatedly.
The goal is to uncover the root causes of problems, rather than just addressing the symptoms.
This method helps organizations implement effective solutions that prevent recurrences.
The process typically involves asking “why” five times, or until the true source of the problem is revealed.
Each answer guides the next question, building a chain of reasoning that uncovers deeper insights.
This technique is intuitive and easily adopted, making it valuable across various industries.
How Toyota-Style Why-Why Analysis Works
Start by clearly defining the problem at hand.
Ensure it’s specific and comprehensible, so that everyone involved understands the issue.
Ask the first “why” to determine the immediate cause.
This question should address why the problem is occurring in the present context.
After identifying the initial cause, inquire further with another “why.”
This step delves into why the immediate cause happened.
It’s crucial to explore beyond surface-level factors.
Continue this process, with each “why” building on the previous answer.
This layered questioning allows for a comprehensive exploration of potential causes.
After several iterations, typically five, you should reach a fundamental issue.
This root cause is often less apparent at first glance.
Addressing it prevents the recurrence of surface problems.
Example of Toyota-Style Why-Why Analysis
To illustrate this method, consider a manufacturing line where defective products have been identified:
1. Why are there defects in the products?
– The machines aren’t calibrating correctly.
2. Why aren’t the machines calibrating correctly?
– The sensors are malfunctioning.
3. Why are the sensors malfunctioning?
– They haven’t been maintained properly.
4. Why haven’t they been maintained properly?
– The maintenance schedule doesn’t include regular sensor checks.
5. Why doesn’t the schedule include sensor checks?
– There’s a lack of understanding of sensor importance in maintenance planning.
Through this process, we identify the root cause: inadept maintenance planning.
Now, the company can focus on training and updating schedules.
Practical Points for Conducting Why-Why Analysis
While the technique seems straightforward, there are practical nuances to consider when conducting why-why analysis:
Engage a Collaborative Team
Involve a diverse team with varied perspectives.
Each member can provide insights based on their experience and expertise.
This collaboration results in a more comprehensive analysis.
Stay Focused on the Issue
During the process, it’s easy to veer off with tangential issues.
Keep the analysis aligned with the main problem to prevent distractions.
Document Your Findings
Record each question and answer to ensure the analysis is thorough.
This documentation helps in reviewing the entire problem-solving process.
It also serves as a future reference for similar issues.
Validate the Root Cause
Once a root cause is identified, validate it with data and additional insights.
Ensure it’s the true underlying issue before developing solutions.
This step helps avoid addressing false conclusions.
Develop and Implement Solutions
After validating the root cause, develop targeted solutions.
These solutions should directly address the identified issue.
Implement them effectively and monitor outcomes to ensure success.
Applying Why-Why Analysis for Defect Prevention
Toyota-style why-why analysis is particularly beneficial for preventing defects.
By addressing the root causes, businesses can significantly reduce the likelihood of recurring issues.
Identify Common Problems
Before defects occur, regularly conduct why-why analyses on common issues.
This proactive approach helps anticipate potential problems.
It safeguards quality and improves product reliability.
Integrate with Quality Management Systems
Align the why-why analysis with existing quality management systems.
This integration streamlines processes and ensures consistency in problem-solving.
Train Employees in the Method
Equip employees with the skills to conduct why-why analysis confidently.
Training fosters a culture of inquiry and continuous improvement.
It empowers teams to tackle issues effectively at every level.
Conclusion
Toyota-style why-why analysis is a powerful tool for uncovering root causes of problems.
Its straightforward approach enables organizations to prevent recurrences by addressing fundamental issues.
By engaging teams, staying focused, and validating findings, businesses can improve operations significantly.
This method’s application in defect prevention enhances product quality and reliability, driving long-term success.
資料ダウンロード
QCD調達購買管理クラウド「newji」は、調達購買部門で必要なQCD管理全てを備えた、現場特化型兼クラウド型の今世紀最高の購買管理システムとなります。
ユーザー登録
調達購買業務の効率化だけでなく、システムを導入することで、コスト削減や製品・資材のステータス可視化のほか、属人化していた購買情報の共有化による内部不正防止や統制にも役立ちます。
NEWJI DX
製造業に特化したデジタルトランスフォーメーション(DX)の実現を目指す請負開発型のコンサルティングサービスです。AI、iPaaS、および先端の技術を駆使して、製造プロセスの効率化、業務効率化、チームワーク強化、コスト削減、品質向上を実現します。このサービスは、製造業の課題を深く理解し、それに対する最適なデジタルソリューションを提供することで、企業が持続的な成長とイノベーションを達成できるようサポートします。
オンライン講座
製造業、主に購買・調達部門にお勤めの方々に向けた情報を配信しております。
新任の方やベテランの方、管理職を対象とした幅広いコンテンツをご用意しております。
お問い合わせ
コストダウンが利益に直結する術だと理解していても、なかなか前に進めることができない状況。そんな時は、newjiのコストダウン自動化機能で大きく利益貢献しよう!
(Β版非公開)