- お役立ち記事
- Fundamentals and scale-up of stirring technology, optimal selection of stirrers, various performance evaluation methods, and their key points
Fundamentals and scale-up of stirring technology, optimal selection of stirrers, various performance evaluation methods, and their key points
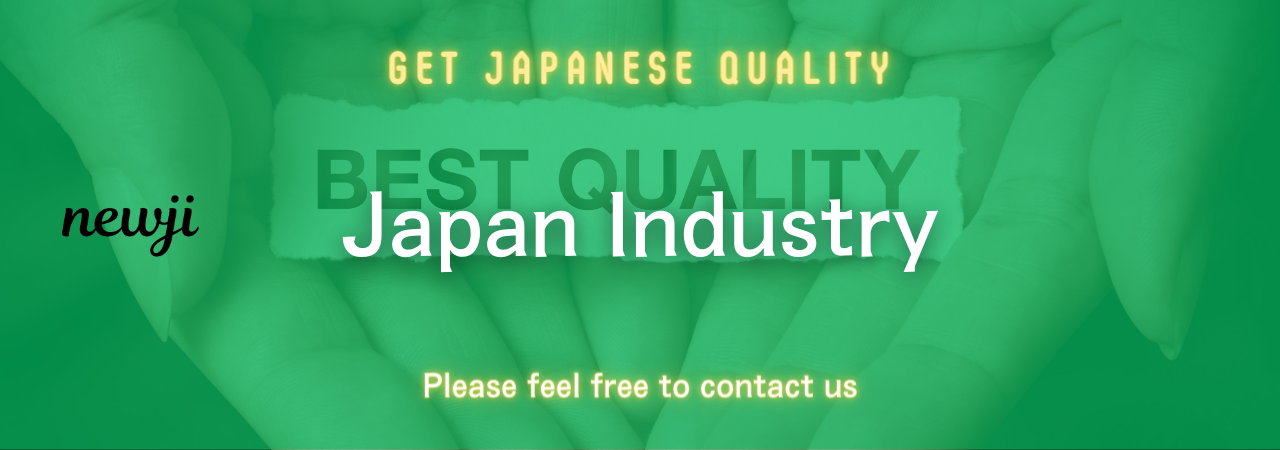
目次
Introduction to Stirring Technology
Stirring technology is essential in various industries, from pharmaceuticals to food processing, where mixing substances is crucial for product formulation and quality.
Understanding the fundamentals of stirring technology can significantly impact the efficiency and effectiveness of mixing processes.
This article explores the basics of stirring technology, the criteria for selecting the optimal stirrers, and the methods used to evaluate their performance.
By delving into these topics, you can make informed decisions that enhance production processes.
Fundamentals of Stirring Technology
Stirring technology revolves around the method of agitating liquids or mixtures to achieve uniformity or facilitate chemical processes.
At its core, stirring involves the movement of a liquid to create turbulence and shear forces, which are essential for breaking up particles, dissolving solids, or emulsifying liquids.
The choice of stirrer design and operation parameters can affect the process efficiency, energy consumption, and final product quality.
Types of Stirring Techniques
1. **Mechanical Stirring**: This is the most common form and involves using a mechanical device, such as a mixer or agitator that physically rotates inside the mixture.
2. **Magnetic Stirring**: Utilizes a rotating magnetic field to spin a magnetic bar submerged in the liquid.
3. **Ultrasonic Stirring**: Employs high-frequency sound waves to agitate the particles within a solution, often used for delicate or sensitive mixtures.
Each method has its unique applications and benefits, making it essential to choose the right technique based on the material characteristics and desired outcome.
Scale-Up of Stirring Technology
Scaling up stirring technology is a critical process in industrial applications.
It involves transitioning from laboratory-scale equipment to larger, production-scale systems while maintaining efficiency and product quality.
Challenges in Scaling Up
1. **Maintaining Uniform Mixing**: Larger volumes can create challenges in maintaining homogeneous mixtures without introducing new variables such as dead zones.
2. **Energy Efficiency**: Larger systems require more power; thus, ensuring energy usage does not disproportionally increase is vital.
3. **Process Consistency**: The ability to replicate mixing results on a larger scale precisely is crucial for maintaining consistent product quality.
4. **Process Dynamics**: The fluid dynamics change as the stirred volume increases, necessitating adjustments to mixing parameters.
Addressing these challenges requires a thorough understanding of fluid dynamics and the interplay between mixer design and operational parameters.
Optimal Selection of Stirrers
Choosing the right stirrer is integral for achieving efficient and effective mixing.
The selection process should consider the nature of the mixture, the specific stirring requirements, and the performance metrics valued for the application.
Factors to Consider
1. **Viscosity of the Material**: Highly viscous substances require paddle or anchor stirrers to create sufficient shear and blending forces.
2. **Mixing Speed and Scale**: High-speed stirrers are perfect for rapid dispersal of solids or immiscible liquids, whereas slower speeds reduce shear on sensitive or fragile substances.
3. **Chemical Compatibility**: The materials used in the construction of the stirrer must be compatible with the chemicals in the mixture to prevent corrosion or degradation.
4. **Temperature Sensitivity**: Some processes may require temperature-controlled equipment, impacting the choice of stirrer material and design.
5. **Geometry of the Mixing Vessel**: The size and shape of the tank will influence the design choice and configuration of the stirrer.
By analyzing these factors, you can select the most appropriate stirrer to optimize mixing efficiency.
Performance Evaluation Methods
Assessing the performance of stirring technology is critical to ensuring process efficiency and product quality.
Various evaluation methods are employed to gauge the effectiveness of a stirring setup.
Key Evaluation Techniques
1. **Qualitative Evaluation**: Visual inspection and manual sampling can provide initial insights into the uniformity and consistency of the mix.
2. **Quantitative Measurements**: These include methods such as rheological analysis, which measures the flow behavior of complex fluids, and particle size distribution analysis to quantify degree of dispersion.
3. **Process Monitoring Tools**: Technologies like in-line viscometers and real-time imaging enable continuous observation of the mixing process, providing valuable performance data.
4. **Computational Fluid Dynamics (CFD)**: CFD simulations offer detailed insights by modeling fluid interactions and predicting the outcomes of different stirring configurations.
These evaluation methods help in fine-tuning the stirring process, ensuring that production goals are met effectively and efficiently.
Key Points for Effective Use of Stirring Technology
1. **Understand Material Properties**: A comprehensive understanding of the properties of the materials being mixed ensures accurate stirring method selection.
2. **Ensure Proper Maintenance**: Regular maintenance and calibration of stirring equipment help retain efficiency and prolong their lifespan.
3. **Adjust Parameters as Needed**: Be prepared to tweak stirring speeds, duration, and configurations based on real-time feedback and performance data.
4. **Stay Updated on Innovations**: Advances in stirring technologies can offer new solutions to existing challenges, thus it’s beneficial to remain informed about the latest developments.
By considering these key points, you can maximize the benefits of stirring technology in your processes.
Conclusion
Stirring technology is an intricate yet essential part of various industrial processes, pivotal in achieving efficient mixing and maintaining product quality.
Understanding the fundamentals, scaling up strategically, selecting the right equipment, and evaluating performance are key to optimizing mixing operations.
By applying these principles, businesses can enhance operational productivity while ensuring consistent, high-quality outcomes.
資料ダウンロード
QCD調達購買管理クラウド「newji」は、調達購買部門で必要なQCD管理全てを備えた、現場特化型兼クラウド型の今世紀最高の購買管理システムとなります。
ユーザー登録
調達購買業務の効率化だけでなく、システムを導入することで、コスト削減や製品・資材のステータス可視化のほか、属人化していた購買情報の共有化による内部不正防止や統制にも役立ちます。
NEWJI DX
製造業に特化したデジタルトランスフォーメーション(DX)の実現を目指す請負開発型のコンサルティングサービスです。AI、iPaaS、および先端の技術を駆使して、製造プロセスの効率化、業務効率化、チームワーク強化、コスト削減、品質向上を実現します。このサービスは、製造業の課題を深く理解し、それに対する最適なデジタルソリューションを提供することで、企業が持続的な成長とイノベーションを達成できるようサポートします。
オンライン講座
製造業、主に購買・調達部門にお勤めの方々に向けた情報を配信しております。
新任の方やベテランの方、管理職を対象とした幅広いコンテンツをご用意しております。
お問い合わせ
コストダウンが利益に直結する術だと理解していても、なかなか前に進めることができない状況。そんな時は、newjiのコストダウン自動化機能で大きく利益貢献しよう!
(Β版非公開)