- お役立ち記事
- Fundamentals and strength design of plastic gears and noise reduction technology
月間76,176名の
製造業ご担当者様が閲覧しています*
*2025年3月31日現在のGoogle Analyticsのデータより
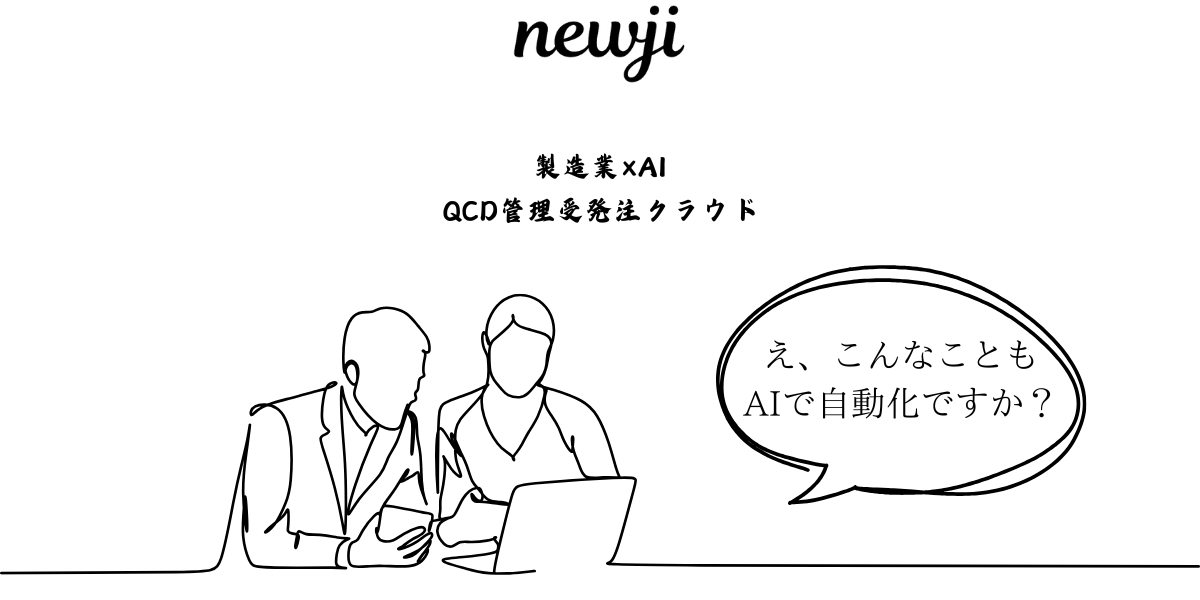
Fundamentals and strength design of plastic gears and noise reduction technology
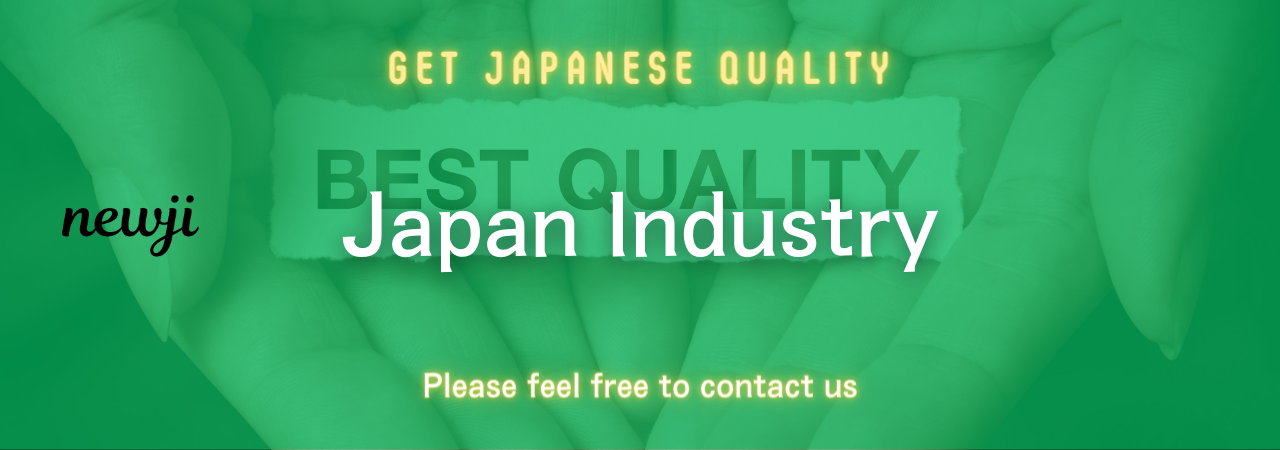
Plastic gears serve as a pivotal component in numerous applications, offering a lightweight, cost-effective, and versatile solution for transmitting power in machinery.
Although they were once considered inferior to metal gears for critical applications, advancements in material technology and design capabilities have significantly enhanced their performance and reliability.
目次
Basics of Plastic Gears
Plastic gears are crafted from various polymer materials, including nylon, acetal, and polycarbonate, each offering unique benefits.
These materials contribute to plastic gears’ lightweight nature and resistance to corrosion.
Plastic gears are distinctly quieter and absorb shock more efficiently than metal gears, making them appealing for certain applications.
The manufacturing process for plastic gears typically involves injection molding, which allows for mass production and reduces overall costs.
This process provides flexibility in gear design, enabling intricate shapes and features that would be costly and challenging to achieve with metal gears.
Applications of Plastic Gears
Plastic gears are widely utilized in industries such as automotive, consumer electronics, and healthcare.
In automotive applications, they are found in power windows, seat adjusters, and dashboard components.
The toys and consumer electronics sectors use plastic gears in products like printers, small household appliances, and toys.
In the healthcare industry, plastic gears are used in medical devices and diagnostic equipment due to their biocompatibility and ease of cleaning.
Plastic is also preferred in applications where electrical insulation is critical, adding to its versatility.
Strength Design of Plastic Gears
The strength design of plastic gears is critical to ensuring reliability and durability.
Material selection is crucial, as different polymers have varying mechanical properties, such as tensile strength, modulus of elasticity, and fatigue resistance.
Key Considerations for Strength
1. **Material Selection**: Evaluate the polymer’s mechanical properties to match application requirements.
2. **Load and Speed**: Ensure that the gear can handle the expected load and speed without excessive wear or deformation.
3. **Environmental Conditions**: Consider the operational temperature and exposure to chemicals, moisture, or UV radiation, as these factors can affect polymer performance.
4. **Geometry and Size**: The size and geometry of the gear teeth influence the load distribution and contact stresses.
5. **Reinforcement**: Adding fillers or reinforcements like glass fibers can enhance the strength and thermal stability of plastic gears.
Design Strategies
To optimize the strength of plastic gears, engineers employ various design strategies.
Advanced computer-aided design (CAD) software and simulations, such as finite element analysis (FEA), allow precise modeling of load distribution and stress points.
This insight aids in refining gear design to achieve desired performance criteria.
Reducing the gear module (the ratio of pitch diameter to the number of teeth) and increasing the pressure angle can decrease contact stress and improve strength.
Balancing the need for smooth operation with adequate stiffness is crucial for long-term performance.
Noise Reduction in Plastic Gears
One of the notable advantages of plastic gears is their potential for noise reduction compared to metal gears.
Noise levels are a vital consideration in applications where silence is desirable, such as office equipment, home appliances, and automobiles.
Factors Contributing to Noise Reduction
1. **Material Damping**: Plastic’s inherent damping properties absorb vibrations better than metal, reducing noise generation.
2. **Lower Friction**: Polymers often exhibit lower coefficients of friction, which minimizes noise from sliding contacts.
3. **Design Flexibility**: The flexibility in design allows optimization of tooth geometry for smoother meshing.
4. **Sound Insulation**: Plastic’s insulating properties help in containing and dampening sound more effectively than metals.
Techniques for Enhancing Noise Reduction
To further enhance noise reduction, designers can incorporate helical or double-helical gear designs, which provide smoother and quieter operation due to continuous tooth contact.
Ground gear teeth can improve the surface finish and minimize deviations that contribute to noise.
Applying coatings or lubricants to gear surfaces reduces friction and vibration, which is beneficial in noise-sensitive applications.
Challenges in Plastic Gear Design
Despite their advantages, designing plastic gears comes with its own set of challenges.
Accurate prediction of gear performance under varying operational conditions is essential but complex due to the viscoelastic nature of polymers.
Creep and deformation over time under continuous load need to be accounted for during the design phase.
Furthermore, ensuring dimensional stability during and after the manufacturing process is crucial.
Plastics can experience shrinkage and warping, affecting their tolerance and fit.
Future Trends and Developments
As technology progresses, the demand for improved plastic gear solutions is set to rise.
Research and development efforts focus on creating polymers with enhanced mechanical characteristics and broadening their application range.
Nanocomposite materials and 3D printing techniques are promising areas of exploration.
These advancements aim to push the boundaries of traditional applications, making plastic gears more suitable for high-load and high-temperature environments.
Through continuous innovation, plastic gears are poised to play an increasingly significant role in various industries, striking a balance between performance, cost, and sustainability.
資料ダウンロード
QCD管理受発注クラウド「newji」は、受発注部門で必要なQCD管理全てを備えた、現場特化型兼クラウド型の今世紀最高の受発注管理システムとなります。
ユーザー登録
受発注業務の効率化だけでなく、システムを導入することで、コスト削減や製品・資材のステータス可視化のほか、属人化していた受発注情報の共有化による内部不正防止や統制にも役立ちます。
NEWJI DX
製造業に特化したデジタルトランスフォーメーション(DX)の実現を目指す請負開発型のコンサルティングサービスです。AI、iPaaS、および先端の技術を駆使して、製造プロセスの効率化、業務効率化、チームワーク強化、コスト削減、品質向上を実現します。このサービスは、製造業の課題を深く理解し、それに対する最適なデジタルソリューションを提供することで、企業が持続的な成長とイノベーションを達成できるようサポートします。
製造業ニュース解説
製造業、主に購買・調達部門にお勤めの方々に向けた情報を配信しております。
新任の方やベテランの方、管理職を対象とした幅広いコンテンツをご用意しております。
お問い合わせ
コストダウンが利益に直結する術だと理解していても、なかなか前に進めることができない状況。そんな時は、newjiのコストダウン自動化機能で大きく利益貢献しよう!
(β版非公開)