- お役立ち記事
- Fundamentals of acoustic emission testing and application to higher reliability of condition monitoring technology
月間77,185名の
製造業ご担当者様が閲覧しています*
*2025年2月28日現在のGoogle Analyticsのデータより
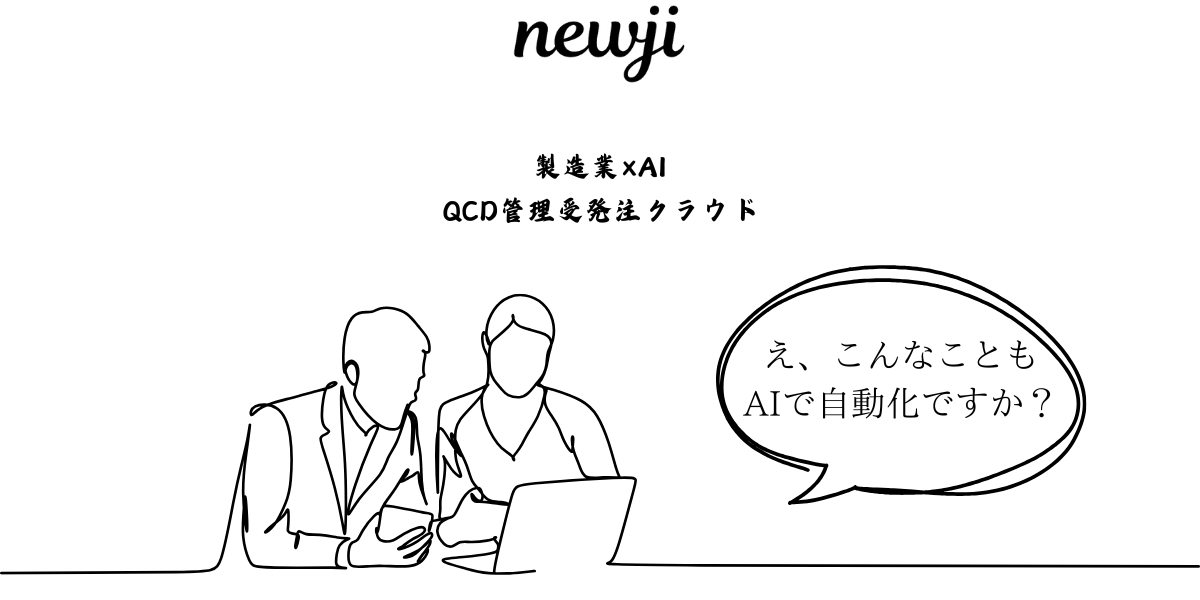
Fundamentals of acoustic emission testing and application to higher reliability of condition monitoring technology
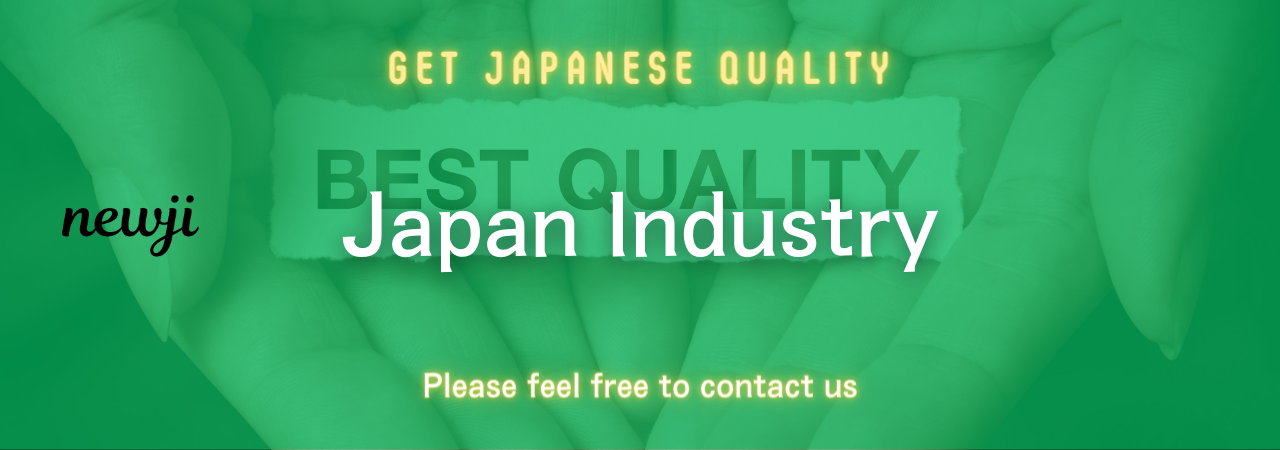
目次
Understanding Acoustic Emission Testing
Acoustic emission testing (AET) is a powerful nondestructive testing technique used to monitor the integrity of structures and materials.
It is based on the detection of transient elastic waves produced by a sudden redistribution of stress.
When materials undergo strength changes due to various reasons like cracking or deformation, they emit energy in the form of sound waves, which can be detected and analyzed.
AET is particularly effective in revealing hidden flaws, as it allows for continuous monitoring without needing to disassemble or destroy the test object.
This monitoring plays a crucial role in industries where safety and reliability are paramount, such as aerospace, nuclear energy, and civil structures.
How Acoustic Emission Testing Works
The fundamental principle behind AET involves sensors attached to a test object.
These sensors detect high-frequency sound waves that are typically not audible to the human ear.
The emission source could be micro-cracking in metals, fiber breakage in composites, or phase transformations.
Once the signals are captured, they are transmitted to data acquisition systems where they are amplified and converted into digital signals for analysis.
The analysis involves distinguishing between useful signals indicative of structural issues and background noise.
Signal parameters such as amplitude, energy, and duration are key in identifying different types of defects.
Advanced software tools help interpret the data, allowing engineers to pinpoint the location of defects and assess their severity.
Applications of Acoustic Emission Testing
AET has a broad range of applications, each benefiting from its nondestructive nature and ability to provide real-time monitoring.
Here are some of the most common fields where AET is applied:
Aerospace Industry
In the aerospace sector, the structural integrity of materials is critical for safety.
AET is used extensively to inspect aircraft structures, such as fuselages and wings, for fatigue cracks.
It helps in detecting the early onset of cracks, ensuring that timely maintenance can be carried out before issues escalate.
Power Generation
For the nuclear and conventional power plants, AET is employed to monitor pressure vessels, piping systems, and turbines.
It aids in detecting corrosion, material degradation, and other defects that could lead to system failures.
This preemptive detection is vital to prevent hazardous situations and unplanned downtimes.
Bridges and Civil Infrastructure
Civil engineering structures like bridges and dams undergo a lot of stress over time due to environmental factors and load conditions.
AET provides an effective solution for the inspection and maintenance of such infrastructures.
Continuous monitoring helps in identifying weak points or damages, allowing for repairs before deterioration progresses.
Oil and Gas Industry
Pipe networks and storage tanks in the oil and gas industry are susceptible to cracks and leakages.
Using AET, operators can detect acoustics produced by leaking materials, enabling them to address the issue swiftly and reduce the risk of environmental contamination.
Advantages of Acoustic Emission Testing
One of the significant benefits of AET is its ability to monitor entire structures without needing to disconnect or dismantle any part.
This capability makes it highly time-efficient and cost-effective, as it reduces downtime significantly.
Additionally, because AET can detect signals indicative of defects while they occur, it provides a way to forecast potential failures before they develop into major problems.
The technique’s sensitivity allows it to detect even minute flaws, capturing the earliest events of structural fatigue.
This early detection aids in extending the service life of structures while maintaining safety standards.
In essence, it serves as a predictive maintenance tool, allowing engineers to anticipate and mitigate failures instead of merely reacting to them.
Challenges and Limitations
While AET offers numerous advantages, it does face certain limitations.
The presence of background noise can sometimes interfere with the clear detection of emission signals.
This necessitates the use of advanced filtering and signal differentiation techniques to ensure accurate assessments.
Additionally, interpreting AET data requires skilled personnel.
Experts must distinguish between innocuous emissions and those indicative of structural faults, which can sometimes be challenging.
AET is also dependent on the propagation of acoustic waves, which can be influenced by the geometry and material of the object tested.
The complexity of some structures might cause sound waves to behave unpredictably, potentially complicating data interpretation.
Future of Acoustic Emission Testing in Condition Monitoring
As technology advances, the realm of AET is expected to grow, integrating innovations such as machine learning and artificial intelligence.
These technologies could enhance the capability of systems to distinguish between various defect signatures automatically, reducing the need for human intervention.
The move towards smarter sensors that can relay real-time data and provide quicker diagnostics is anticipated.
With the integration of wireless technology, AET can become more accessible and versatile, applicable to more challenging environments.
Ultimately, the role of AET in condition monitoring will likely continue to expand, providing more reliable, efficient ways to ensure the safety and longevity of vital structures across numerous industries.
As its applications broaden, acoustic emission testing stands as a cornerstone technology in proactive maintenance strategies.
資料ダウンロード
QCD管理受発注クラウド「newji」は、受発注部門で必要なQCD管理全てを備えた、現場特化型兼クラウド型の今世紀最高の受発注管理システムとなります。
ユーザー登録
受発注業務の効率化だけでなく、システムを導入することで、コスト削減や製品・資材のステータス可視化のほか、属人化していた受発注情報の共有化による内部不正防止や統制にも役立ちます。
NEWJI DX
製造業に特化したデジタルトランスフォーメーション(DX)の実現を目指す請負開発型のコンサルティングサービスです。AI、iPaaS、および先端の技術を駆使して、製造プロセスの効率化、業務効率化、チームワーク強化、コスト削減、品質向上を実現します。このサービスは、製造業の課題を深く理解し、それに対する最適なデジタルソリューションを提供することで、企業が持続的な成長とイノベーションを達成できるようサポートします。
製造業ニュース解説
製造業、主に購買・調達部門にお勤めの方々に向けた情報を配信しております。
新任の方やベテランの方、管理職を対象とした幅広いコンテンツをご用意しております。
お問い合わせ
コストダウンが利益に直結する術だと理解していても、なかなか前に進めることができない状況。そんな時は、newjiのコストダウン自動化機能で大きく利益貢献しよう!
(β版非公開)