- お役立ち記事
- Fundamentals of adhesion and peeling, and visualization and modeling techniques for the peeling process
Fundamentals of adhesion and peeling, and visualization and modeling techniques for the peeling process
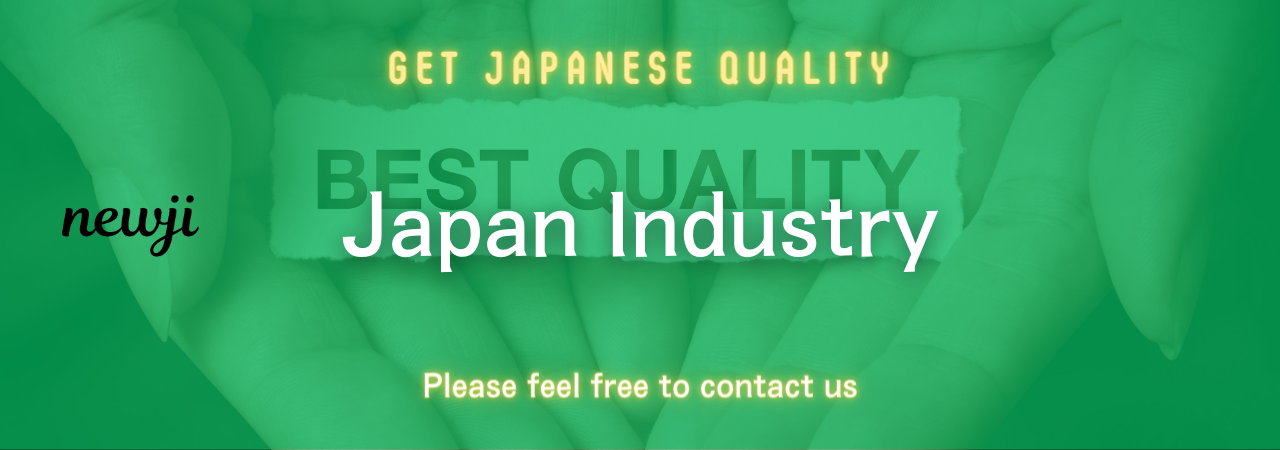
目次
Understanding Adhesion and Peeling
Adhesion is the force that holds two different surfaces together.
It is a result of molecular interactions between the surfaces, including chemical bonds, van der Waals forces, and electrostatic forces.
Adhesion is an important concept in various fields, including materials science, engineering, and biology.
Its applications span from everyday items like tapes and labels to advanced technologies such as microelectronics and medical implants.
On the other hand, peeling is the process of separating two surfaces that are bonded together.
Understanding the fundamentals of adhesion and peeling is crucial for developing materials and products that require specific bonding and debonding properties.
In many cases, controlling the peeling process is as important as achieving the initial adhesion.
Mechanisms of Adhesion
Several mechanisms contribute to adhesion between surfaces.
Chemical bonding is one of the strongest forms of adhesion, where atoms from different surfaces form covalent or ionic bonds.
This type of adhesion is typically seen in chemical coatings and is characterized by high durability and resistance to environmental factors.
Another mechanism is mechanical interlocking, where surfaces bond due to their physical shapes.
This is common in porous or rough surfaces where one material fills the voids of another, creating a mechanical anchor.
Van der Waals forces are weak intermolecular forces that arise from temporary shifts in electron density.
They play a significant role in adhesion, especially in non-polar materials like plastics.
While these forces are weaker compared to chemical bonds, they collaborate over large areas, contributing to overall adhesion.
Lastly, electrostatic forces result from the attraction between charged surfaces.
In processes like electroplating, electrostatic adhesion can be very effective.
Understanding these mechanisms helps in designing materials with desired adhesion properties.
Factors Affecting Adhesion
Several factors can influence the effectiveness of adhesion between two surfaces.
Surface roughness is one major factor, as rougher surfaces provide more area for mechanical interlocking and increase adhesion.
However, excessive roughness can sometimes lead to weaker adhesive bonds due to poor contact between the surfaces.
Surface energy also plays a crucial role in adhesion.
Materials with high surface energy tend to form stronger adhesive bonds because they can interact more effectively with adhesives.
This is why treatments like plasma or flame can enhance adhesion by increasing surface energy.
Temperature and humidity can affect adhesion as well.
High temperatures can soften adhesives, reducing their mechanical strength, while low temperatures might make them brittle.
Humidity can lead to moisture adsorption, which can weaken the interfacial bonds and lead to failure.
Lastly, the presence of contaminants such as oils, dust, or grease can drastically reduce adhesion.
Proper surface cleaning is usually necessary to ensure optimal bonding.
Peeling Process and Its Importance
Peeling refers to the separation of two adhered surfaces, and its understanding is important in applications like labels, tapes, and films.
The process is characterized by the initiation and propagation of a crack at the interface between the surfaces.
One important factor in the peeling process is the peel force, which is the force required to separate the adhered surfaces.
This force can depend on the angle of peeling, the rate of peeling, and the environment in which peeling occurs.
Materials designed for easy peel applications typically have lower peel forces, allowing for effortless removal.
Peeling is not just about removing materials. It is also critical in failure analysis, where understanding the peeling can help diagnose bonding issues in adhesives, coatings, or laminates.
For example, in the electronics industry, peeling tests can indicate the reliability of soldered connections.
Visualization Techniques for Peeling
To effectively study the peeling process, visualization techniques are employed.
These techniques provide insights into the interface phenomena and help identify factors influencing the peeling behavior.
One popular method is optical microscopy, which allows observation of the peeling front.
This method is useful for capturing real-time images of the process as it occurs.
However, it may be limited by resolution when dealing with very fine interfaces.
Another advanced technique is Scanning Electron Microscopy (SEM), which offers high-resolution imaging of the peeling process.
SEM can provide detailed images of the adhesion interfaces and any microstructural changes occurring during peeling.
This technique is valuable in research environments where precise analysis is necessary.
An emerging technique is Digital Image Correlation (DIC), which involves tracking and analyzing the movement of patterns on the surfaces during peeling.
DIC provides quantitative data about displacement and strain, enabling the study of mechanical behavior throughout the peeling process.
Modeling Techniques for the Peeling Process
Modeling techniques play a significant role in predicting and understanding the peeling process.
These methods are crucial for designing materials and processes with predictable peeling behaviors.
Finite Element Analysis (FEA) is a widely used modeling technique that simulates the mechanical behavior of materials during peeling.
By using FEA, researchers can predict crack initiation, propagation, and the resulting peel forces under different conditions.
This approach is particularly beneficial for optimizing adhesive formulations and understanding failure mechanisms.
Another technique is Cohesive Zone Modeling (CZM), which focuses on simulating the interface layer where separation occurs.
CZM helps to predict the peel strength and energy required for peeling by incorporating adhesion and separation laws into the model.
This method is often used for characterizing the toughness of adhesive joints.
In multiphysics modeling, various physical phenomena involved in the peeling process, such as thermal, mechanical, and chemical interactions, are considered simultaneously.
This comprehensive approach allows for a detailed understanding of the peeling process under complex conditions.
Multiphysics modeling is gaining popularity for its ability to provide holistic insights into material behavior.
Through these visualization and modeling techniques, industries can strategically manage adhesion and peeling to enhance product performance and reliability.
By mastering the fundamentals and leveraging modern techniques, advancements in adhesive technologies continue to flourish, driving innovation across multiple fields.
資料ダウンロード
QCD調達購買管理クラウド「newji」は、調達購買部門で必要なQCD管理全てを備えた、現場特化型兼クラウド型の今世紀最高の購買管理システムとなります。
ユーザー登録
調達購買業務の効率化だけでなく、システムを導入することで、コスト削減や製品・資材のステータス可視化のほか、属人化していた購買情報の共有化による内部不正防止や統制にも役立ちます。
NEWJI DX
製造業に特化したデジタルトランスフォーメーション(DX)の実現を目指す請負開発型のコンサルティングサービスです。AI、iPaaS、および先端の技術を駆使して、製造プロセスの効率化、業務効率化、チームワーク強化、コスト削減、品質向上を実現します。このサービスは、製造業の課題を深く理解し、それに対する最適なデジタルソリューションを提供することで、企業が持続的な成長とイノベーションを達成できるようサポートします。
オンライン講座
製造業、主に購買・調達部門にお勤めの方々に向けた情報を配信しております。
新任の方やベテランの方、管理職を対象とした幅広いコンテンツをご用意しております。
お問い合わせ
コストダウンが利益に直結する術だと理解していても、なかなか前に進めることができない状況。そんな時は、newjiのコストダウン自動化機能で大きく利益貢献しよう!
(Β版非公開)