- お役立ち記事
- Fundamentals of adhesion technology, defect countermeasures, and long-term reliability evaluation technology using curing rate measurement methods and accelerated tests
月間77,185名の
製造業ご担当者様が閲覧しています*
*2025年2月28日現在のGoogle Analyticsのデータより
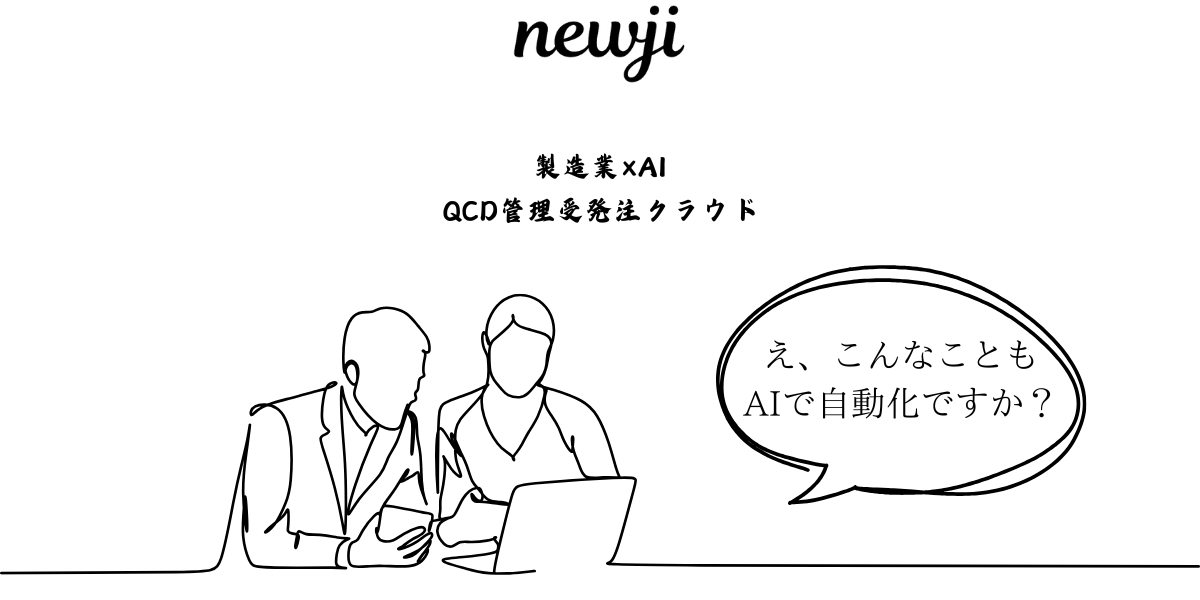
Fundamentals of adhesion technology, defect countermeasures, and long-term reliability evaluation technology using curing rate measurement methods and accelerated tests
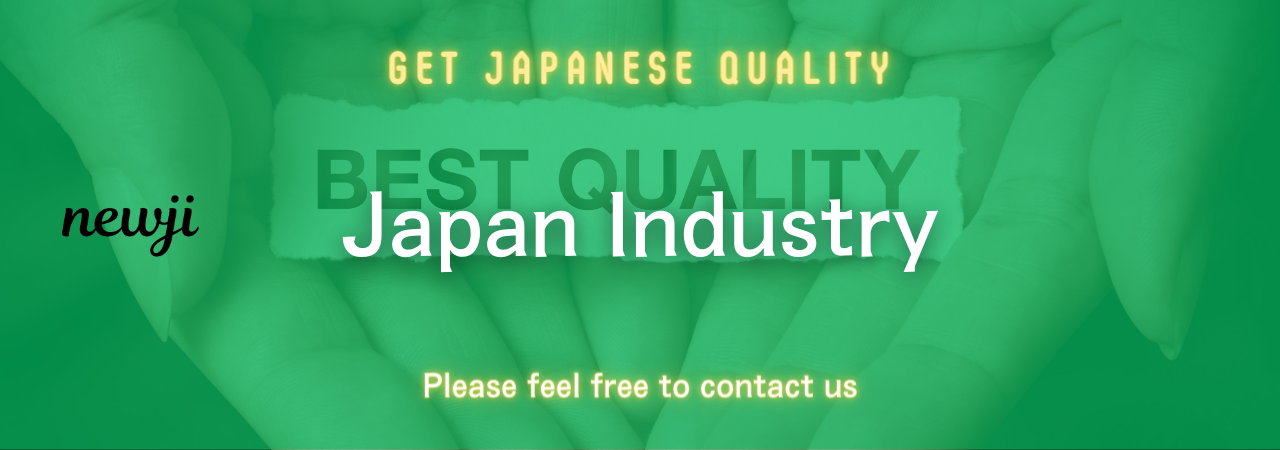
目次
Introduction to Adhesion Technology
Adhesion technology plays a crucial role in various industries, from automotive to electronics, where high-strength bonds are necessary for ensuring the durability and safety of products.
The process involves joining two surfaces using adhesives, which are often made from a variety of chemical compounds designed to optimize their bonding properties.
Understanding the fundamentals of adhesion technology is vital for improving product performance and longevity.
Basics of Adhesion
Adhesion refers to the attraction between different substances when they come into contact.
In the context of adhesion technology, this involves creating a strong bond between two materials, often through the use of an adhesive.
Several factors influence the effectiveness of this bond, including surface roughness, surface energy, and the chemical nature of the materials involved.
Successful adhesion requires proper surface preparation and the right choice of adhesive for the materials and the conditions they will be exposed to.
Types of Adhesives
There are various types of adhesives used in adhesion technology, each with unique properties and applications.
Common types include:
1. **Epoxy Adhesives**: Known for their strong bonding capabilities and resistance to chemicals and heat, epoxies are widely used in construction, automotive, and aerospace industries.
2. **Acrylic Adhesives**: These are versatile adhesives that offer good bond strength and are often used in signage, automotive, and electronics industries.
3. **Polyurethane Adhesives**: Noted for their flexibility and impact resistance, polyurethane adhesives are commonly applied in construction and the manufacturing of footwear and furniture.
4. **Silicone Adhesives**: These adhesives are known for their ability to withstand extreme temperatures and environmental conditions, making them ideal for applications in electronics and industrial sealing.
Defect Countermeasures in Adhesion
Even with the best practices in place, defects can occur during the adhesion process.
Addressing these potential issues is essential for maintaining the integrity of the bond and the overall quality of the product.
Common Adhesion Defects
Some common defects in adhesion include:
– **Incomplete Curing**: This occurs when the adhesive does not properly harden, often due to insufficient time, temperature, or humidity control during the curing process.
– **Adhesive Failure**: This happens when the adhesive itself becomes weak, often due to chemical degradation or exposure to unfavorable environmental conditions.
– **Cohesive Failure**: This occurs when the adhesive bond is broken, not at the interface between adhesive and substrate, but within the adhesive itself.
– **Surface Contamination**: Any dirt, oil, or moisture on surfaces to be bonded can significantly reduce the adhesive strength.
Strategies for Defect Prevention
To prevent defects in adhesion, several strategies can be employed:
1. **Surface Preparation**: Ensuring surfaces are clean and free of contaminants before applying adhesive is crucial.
Techniques like sandblasting, priming, or chemical cleaning can enhance adhesion.
2. **Appropriate Selection of Adhesives**: Choosing the right adhesive for the application and environmental conditions is key.
Consider the materials involved, and the operational environment, including temperature and humidity.
3. **Controlled Curing Conditions**: Following manufacturer guidelines for curing times and conditions, such as temperature and pressure, will help in achieving optimal bond strength.
Evaluating Long-term Reliability
For products using adhesion technology, long-term reliability is a significant concern.
Ensuring the adhesive bond maintains its strength over time, even under potentially harsh conditions, is vital.
Curing Rate Measurement Methods
Measuring the curing rate of adhesives is essential for verifying the bond’s strength and integrity over its service life.
Common methods include:
– **Differential Scanning Calorimetry (DSC)**: This method measures the heat flow associated with transitions in adhesives, providing insights into the curing process and degree of cure.
– **Dynamic Mechanical Analysis (DMA)**: DMA evaluates the mechanical properties of the cured adhesive over a range of temperatures, indicating its thermal reliability.
– **Rheometry**: This method assesses the flow and deformation behavior of the adhesive, allowing for adjustments in formulation or application process to enhance performance.
Accelerated Tests for Long-term Performance
Accelerated testing simulates long-term environmental conditions to predict the adhesive bond’s performance over time.
These tests help in identifying potential weaknesses and making necessary adjustments.
– **Environmental Aging Tests**: These involve exposing the adhesive bond to harsh conditions such as high humidity, temperature fluctuations, and UV radiation.
– **Thermal Cycling Tests**: This test involves repeatedly exposing the bond to extreme temperature changes to assess its resilience to thermal expansion and contraction.
– **Mechanical Stress Tests**: These tests simulate the physical stresses the adhesive bond will face in real-world applications, such as vibration and impact.
Conclusion
Understanding the fundamentals of adhesion technology is crucial for optimizing the performance and durability of products across various industries.
By employing effective defect countermeasures and evaluating long-term reliability through curing rate measurement methods and accelerated tests, manufacturers can ensure the adhesive bonds maintain their strength and integrity over time.
This knowledge is essential for improving product safety and ensuring customer satisfaction in an increasingly competitive market.
資料ダウンロード
QCD管理受発注クラウド「newji」は、受発注部門で必要なQCD管理全てを備えた、現場特化型兼クラウド型の今世紀最高の受発注管理システムとなります。
ユーザー登録
受発注業務の効率化だけでなく、システムを導入することで、コスト削減や製品・資材のステータス可視化のほか、属人化していた受発注情報の共有化による内部不正防止や統制にも役立ちます。
NEWJI DX
製造業に特化したデジタルトランスフォーメーション(DX)の実現を目指す請負開発型のコンサルティングサービスです。AI、iPaaS、および先端の技術を駆使して、製造プロセスの効率化、業務効率化、チームワーク強化、コスト削減、品質向上を実現します。このサービスは、製造業の課題を深く理解し、それに対する最適なデジタルソリューションを提供することで、企業が持続的な成長とイノベーションを達成できるようサポートします。
製造業ニュース解説
製造業、主に購買・調達部門にお勤めの方々に向けた情報を配信しております。
新任の方やベテランの方、管理職を対象とした幅広いコンテンツをご用意しております。
お問い合わせ
コストダウンが利益に直結する術だと理解していても、なかなか前に進めることができない状況。そんな時は、newjiのコストダウン自動化機能で大きく利益貢献しよう!
(β版非公開)