- お役立ち記事
- Fundamentals of aerodynamic design using CAE (CFD: Computational Fluid Analysis) and application to optimal design
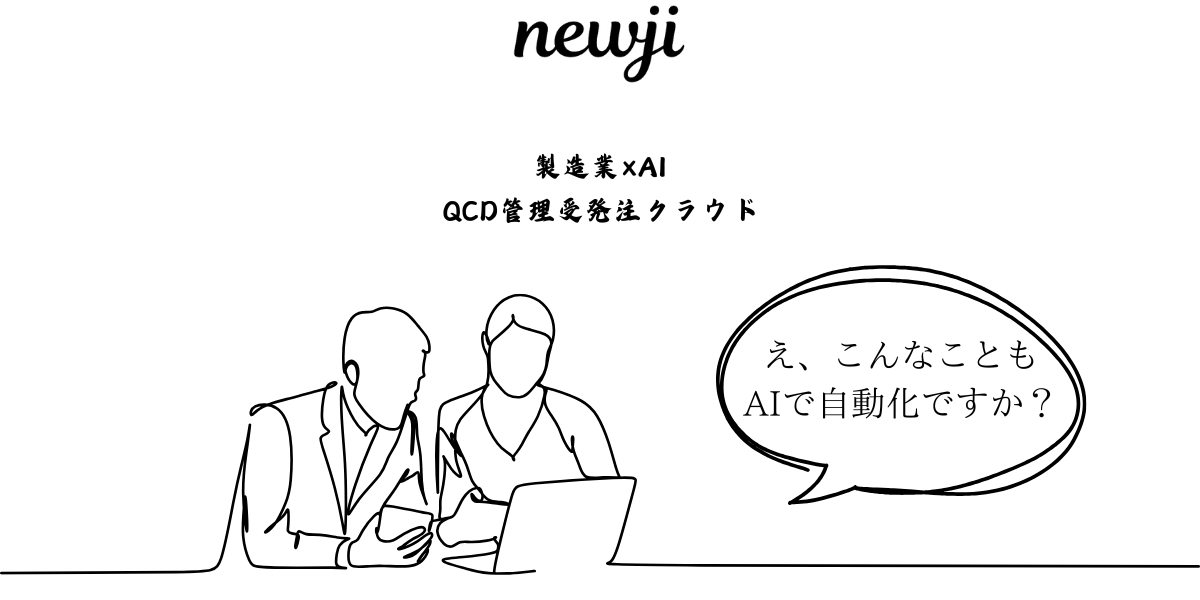
Fundamentals of aerodynamic design using CAE (CFD: Computational Fluid Analysis) and application to optimal design
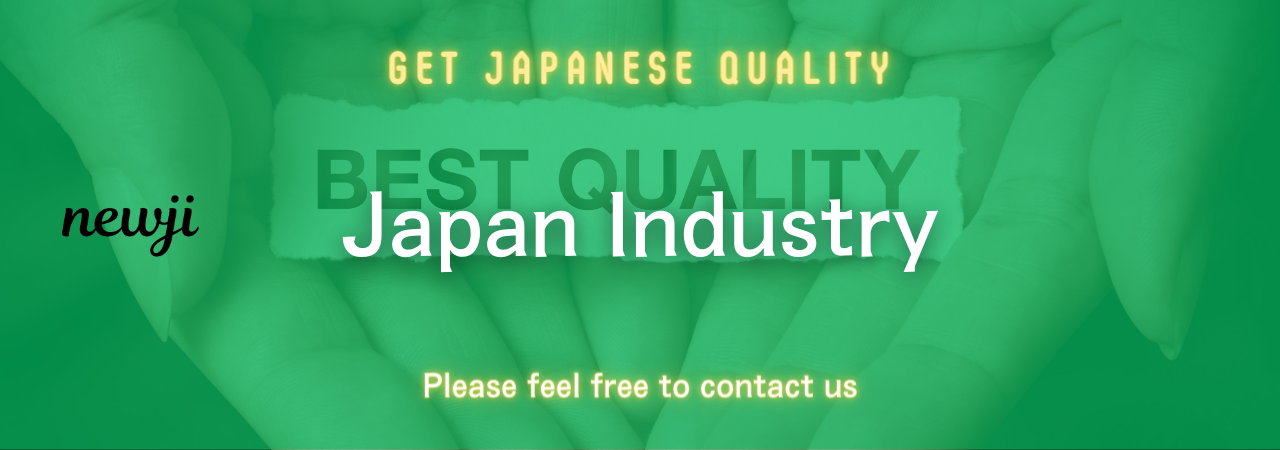
Understanding the fundamentals of aerodynamic design is essential in many industries, ranging from automotive to aerospace.
Computational Fluid Dynamics (CFD) plays a significant role in achieving this, using simulations to predict how fluids (gases and liquids) flow over surfaces.
In simpler terms, CFD helps engineers visualize air movement around objects, such as cars and planes, to design more efficient and effective shapes.
The application of CFD in the optimal design process allows engineers to test and modify designs virtually, reducing the need for physical prototypes and costly real-world testing.
目次
What is Aerodynamic Design?
Aerodynamic design refers to the way an object is shaped to allow air to flow over it smoothly.
This design is critical in reducing drag and enhancing lift, thereby improving the performance and efficiency of vehicles, aircraft, and even buildings.
A streamlined design ensures less resistance, leading to better speed, fuel efficiency, and overall performance.
Aerodynamic principles are applicable in many fields, impacting the design of products we interact with daily.
Introduction to CFD: Computational Fluid Dynamics
Computational Fluid Dynamics (CFD) is a branch of fluid mechanics that uses numerical analysis and data structures to solve and analyze problems involving fluid flows.
By solving the Navier-Stokes equations that describe fluid motion, CFD provides in-depth insights into fluid dynamics for various applications.
Engineers use CFD software to simulate the interaction of gases and liquids with surfaces and observe how changes in design can affect performance.
CFD simulations are invaluable as they allow for the testing of multiple scenarios and variables, such as speed, pressure, and temperature, thereby optimizing designs before any physical construction occurs.
The Importance of CFD in Aerodynamic Design
One of the main advantages of using CFD in aerodynamic design is the ability to visualize complex flow patterns that cannot be easily observed in wind tunnels or through experimentations.
It allows engineers and designers to identify potential issues in the initial design phase, saving time and cost by accurately predicting how changes will affect performance.
Furthermore, CFD can simulate real-world conditions and many parameters that would be difficult to recreate in physical testing.
This capacity for detailed analysis leads to more innovative designs that are functional, efficient, and sustainable.
Applications of CFD in Various Industries
CFD is widely used in the automotive industry for designing car shapes that minimize air resistance, thus improving fuel efficiency and speed.
In aerospace, it significantly impacts aircraft design by optimizing wing shapes and fuselage for improved lift and reduced drag.
The benefits of CFD extend to other fields such as architecture, where it is used to design energy-efficient buildings by analyzing wind patterns, heating, and ventilation.
In sports engineering, CFD helps in refining sports equipment, ensuring better performance for athletes.
The breadth of CFD applications continues to expand as technology advances and new challenges arise.
Design Optimization Through CFD
Design optimization using CFD involves iterating the design parameters to achieve the best possible configuration under given constraints.
This process includes changing shapes, sizes, and orientations of objects to attain superior aerodynamic properties.
The digital nature of CFD makes it an ideal tool for optimization, where multiple design iterations can be tested without physical prototypes.
Software tools can automatically adjust design variables, assess performance, and refine designs to achieve optimal results.
CFD Tools and Software
Several software packages are available for executing CFD simulations effectively.
These tools come with advanced solvers and capabilities to address a wide array of fluid dynamics challenges.
Popular CFD tools include ANSYS Fluent, OpenFOAM, and SolidWorks Flow Simulation; each offers unique features that cater to different industries.
Selecting the right tool depends on the specific needs of a project, such as the complexity of simulations required and the desired level of precision.
The Role of Engineers in CFD
While CFD software provides powerful tools for simulation, the role of engineers is crucial in interpreting the data and making informed decisions.
Engineers need to understand the principles of fluid dynamics to set up simulations correctly and validate results.
Their expertise is essential in identifying the most critical factors to focus on during the design process, ensuring that the applications of CFD lead to efficient, practical designs.
Challenges in CFD
Despite the benefits of CFD, there are challenges that need addressing.
One of the main obstacles is the high computational power needed for complex simulations, making them resource-intensive and sometimes costly.
Moreover, setting up simulations correctly requires precise input data and parameters, which can make the process time-consuming.
Interpreting the simulation results also demands a high level of expertise, as incorrect interpretations can lead to poor design decisions.
Future of CFD in Aerodynamic Design
Advancements in computing power and technology are paving the way for more accurate and faster simulations.
Artificial intelligence and machine learning are beginning to play roles in automating and optimizing CFD processes, making future aerodynamic design more efficient and innovative.
As these technologies develop, CFD will become more accessible and integrated across industries, further revolutionizing how designs are tested and improved.
In conclusion, the fundamentals of aerodynamic design using CFD are pivotal in enhancing the performance and efficiency of various products and systems.
Through simulation and optimization, CFD offers unparalleled insights into fluid dynamics, allowing engineers to design for optimal aerodynamic outcomes.
As technology continues to evolve, the use and capabilities of CFD in aerodynamic design promise to unlock new possibilities, shaping the future of innovation through informed and optimal design choices.
資料ダウンロード
QCD調達購買管理クラウド「newji」は、調達購買部門で必要なQCD管理全てを備えた、現場特化型兼クラウド型の今世紀最高の購買管理システムとなります。
ユーザー登録
調達購買業務の効率化だけでなく、システムを導入することで、コスト削減や製品・資材のステータス可視化のほか、属人化していた購買情報の共有化による内部不正防止や統制にも役立ちます。
NEWJI DX
製造業に特化したデジタルトランスフォーメーション(DX)の実現を目指す請負開発型のコンサルティングサービスです。AI、iPaaS、および先端の技術を駆使して、製造プロセスの効率化、業務効率化、チームワーク強化、コスト削減、品質向上を実現します。このサービスは、製造業の課題を深く理解し、それに対する最適なデジタルソリューションを提供することで、企業が持続的な成長とイノベーションを達成できるようサポートします。
オンライン講座
製造業、主に購買・調達部門にお勤めの方々に向けた情報を配信しております。
新任の方やベテランの方、管理職を対象とした幅広いコンテンツをご用意しております。
お問い合わせ
コストダウンが利益に直結する術だと理解していても、なかなか前に進めることができない状況。そんな時は、newjiのコストダウン自動化機能で大きく利益貢献しよう!
(Β版非公開)