- お役立ち記事
- Fundamentals of aluminum alloys, casting technology, and selection points for optimal casting methods
月間77,185名の
製造業ご担当者様が閲覧しています*
*2025年2月28日現在のGoogle Analyticsのデータより
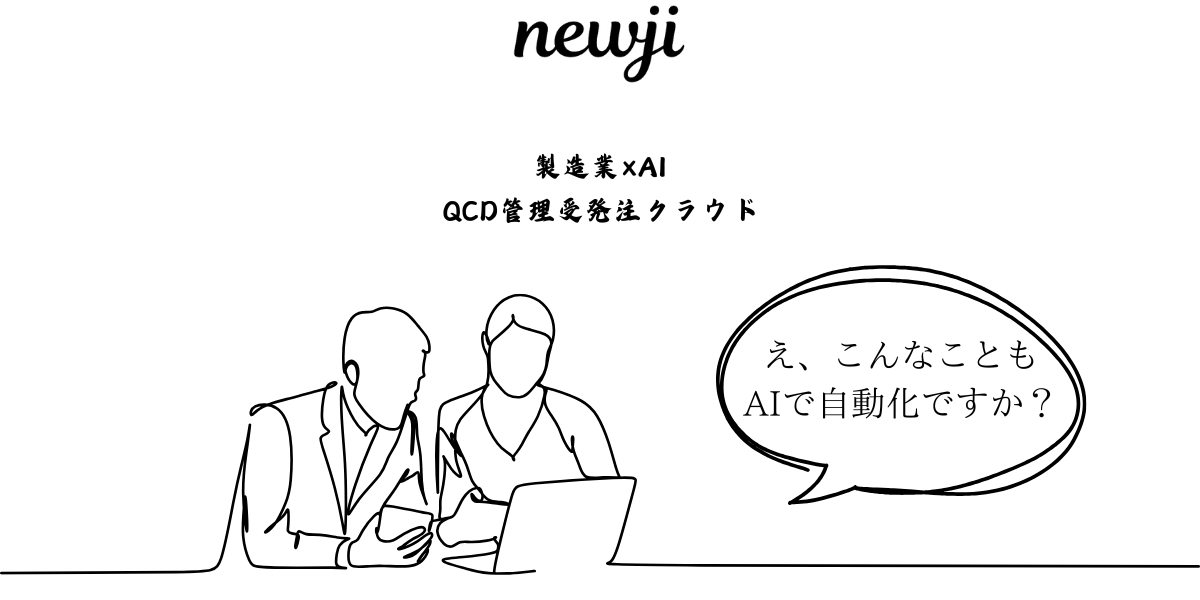
Fundamentals of aluminum alloys, casting technology, and selection points for optimal casting methods
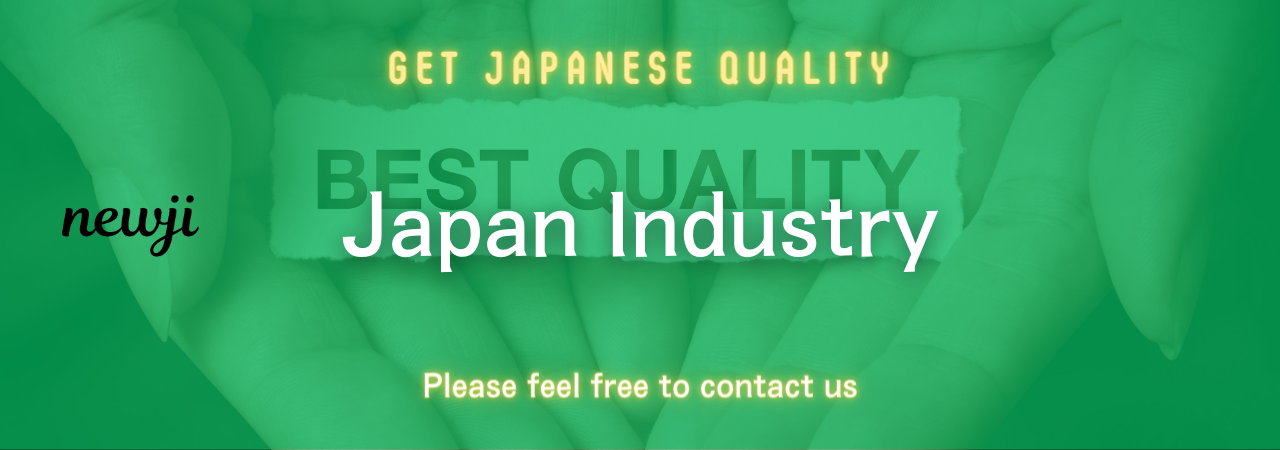
Aluminum alloys have become essential in various industries due to their remarkable properties, such as light weight, high strength, and excellent corrosion resistance.
Understanding the fundamentals of aluminum alloys, casting technologies, and knowing how to select the optimal casting methods are crucial for engineers and manufacturers aiming to produce high-quality components.
目次
Understanding Aluminum Alloys
Aluminum alloys are composed primarily of aluminum, which is often combined with other elements to enhance specific properties.
These elements include copper, magnesium, silicon, manganese, and zinc, among others.
Each element contributes differently, resulting in alloys suitable for a wide range of applications.
Properties of Aluminum Alloys
Aluminum alloys are preferred for their lightweight nature, which contributes to fuel efficiency in automotive and aerospace industries.
They also exhibit high tensile strength and excellent corrosion resistance, making them ideal for marine and outdoor applications.
Additionally, aluminum alloys have good thermal and electrical conductivity, which are beneficial in electronics and electrical engineering.
Casting Technologies for Aluminum Alloys
Casting is a crucial process in manufacturing aluminum alloy components.
It involves pouring molten aluminum into a mold to achieve the desired shape and size.
Selecting the appropriate casting technology is essential for optimal performance and cost-efficiency.
Sand Casting
Sand casting is one of the oldest and most versatile casting methods.
It involves creating a mold using sand, into which molten aluminum is poured.
This method is cost-effective and suitable for producing large components or low production runs.
However, it may not be ideal for intricate designs due to its lower dimensional accuracy.
Die Casting
Die casting is a high-pressure casting method that uses a metal mold made of steel.
It is ideal for producing complex shapes with tight tolerances and smooth surfaces.
This method is commonly used in the automotive and electronics industries, where precision and surface finish are critical.
While die casting involves higher initial costs due to mold fabrication, it is cost-effective for large production volumes.
Investment Casting
Investment casting, also known as lost-wax casting, allows for the creation of intricate parts with excellent surface finish and dimensional accuracy.
The process involves creating a wax model, coating it with a ceramic material to form a mold, and then melting the wax away before pouring the aluminum alloy.
This method is suitable for producing components with complex geometries and is widely used in aerospace and medical industries.
Choosing the Right Casting Method
Selecting the appropriate casting method for aluminum alloys depends on a variety of factors, including part complexity, production volume, and budget.
Understanding these factors will help in choosing the optimal casting method.
Part Complexity
For parts with simple geometries, sand casting may be the most economical choice.
However, for intricate designs with fine details, investment casting or die casting is recommended due to their ability to produce precise molds.
Production Volume
The production volume plays a significant role in casting method selection.
For low to medium production volumes, sand casting or investment casting could be the best choice.
In contrast, die casting is more cost-effective for high-volume production due to its efficiency and speed.
Budget Considerations
The overall cost of the casting process, including mold preparation and labor, should be evaluated.
Sand casting has relatively low initial costs but may incur additional finishing costs.
Die casting requires substantial upfront investment for mold manufacturing, but it reduces unit cost for large production volumes.
Investment casting sits between the two, balancing cost and quality for parts requiring high precision.
Conclusion
Aluminum alloys offer a wide array of advantages, making them a popular choice across different industries.
By understanding the properties of these alloys and evaluating casting technologies, manufacturers can make informed decisions to optimize the production of high-quality components.
Choosing the right casting method requires consideration of part complexity, production volume, and budget constraints.
With these considerations in mind, manufacturers can ensure the durability, performance, and cost-effectiveness of their components, meeting the demands of their respective industries.
資料ダウンロード
QCD管理受発注クラウド「newji」は、受発注部門で必要なQCD管理全てを備えた、現場特化型兼クラウド型の今世紀最高の受発注管理システムとなります。
ユーザー登録
受発注業務の効率化だけでなく、システムを導入することで、コスト削減や製品・資材のステータス可視化のほか、属人化していた受発注情報の共有化による内部不正防止や統制にも役立ちます。
NEWJI DX
製造業に特化したデジタルトランスフォーメーション(DX)の実現を目指す請負開発型のコンサルティングサービスです。AI、iPaaS、および先端の技術を駆使して、製造プロセスの効率化、業務効率化、チームワーク強化、コスト削減、品質向上を実現します。このサービスは、製造業の課題を深く理解し、それに対する最適なデジタルソリューションを提供することで、企業が持続的な成長とイノベーションを達成できるようサポートします。
製造業ニュース解説
製造業、主に購買・調達部門にお勤めの方々に向けた情報を配信しております。
新任の方やベテランの方、管理職を対象とした幅広いコンテンツをご用意しております。
お問い合わせ
コストダウンが利益に直結する術だと理解していても、なかなか前に進めることができない状況。そんな時は、newjiのコストダウン自動化機能で大きく利益貢献しよう!
(β版非公開)