- お役立ち記事
- Fundamentals of CAE analysis and finite element methods and points for effective use in strength design
月間76,176名の
製造業ご担当者様が閲覧しています*
*2025年3月31日現在のGoogle Analyticsのデータより
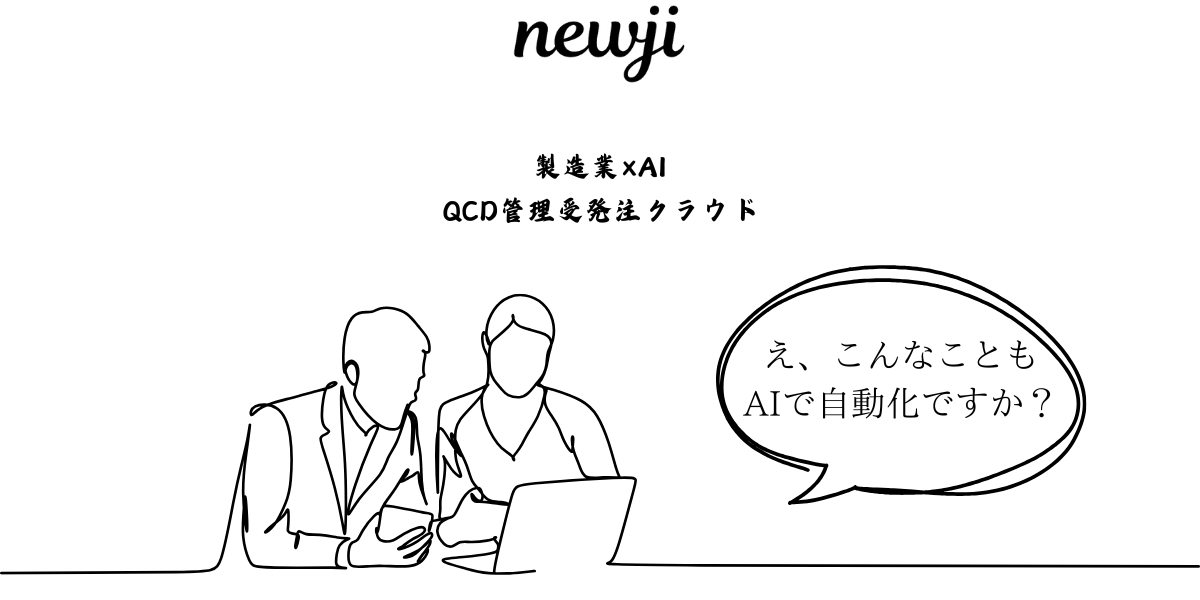
Fundamentals of CAE analysis and finite element methods and points for effective use in strength design
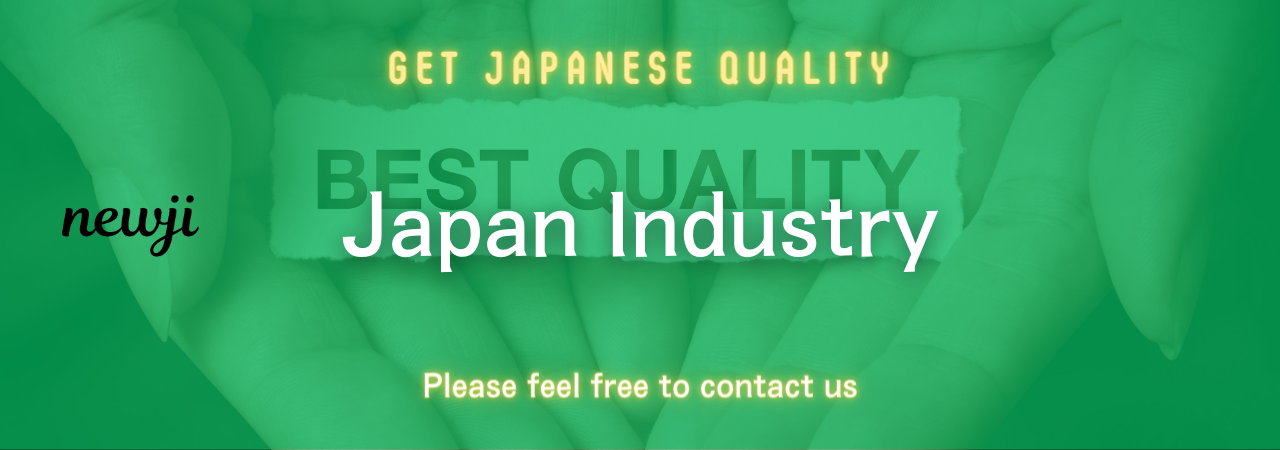
目次
Understanding CAE Analysis and Finite Element Methods
What is CAE Analysis?
Computer-Aided Engineering (CAE) is a critical technology in the field of engineering design and analysis.
It involves the use of computer software to simulate performance and improve product designs.
CAE provides engineers with the ability to assess the behavior of structures, systems, or components under various conditions.
It helps in predicting how a product will perform and assists in design optimization.
CAE encompasses a wide range of analyses, including stress and structural analysis, thermal and fluid flow analysis, and dynamic and kinematic simulations.
By incorporating CAE tools in the design process, engineers can reduce prototyping costs, improve product quality, and accelerate time to market.
The Role of Finite Element Methods
Finite Element Methods (FEM) are at the core of CAE analysis.
FEM is a numerical technique used to find approximate solutions to complex problems in engineering.
This method subdivides a large system into simpler parts, called finite elements, which are then solved in relation to one another.
Each element is essentially a small piece of the structure being analyzed.
This subdivision allows for precise modeling of geometries, loadings, and material properties.
The finite element model transforms these elements into an algebraic form that a computer can solve.
As a result, FEM enables engineers to predict how structures will respond to external forces, thermal changes, and other physical effects.
Fundamentals of Finite Element Analysis
Discretization of the Domain
The first step in finite element analysis is discretization.
Discretization involves breaking down a complex structure into smaller, manageable pieces.
These pieces are the finite elements, and they can take various shapes like triangles, quadrilaterals, or hexahedra, depending on the complexity of the geometry.
Discretizing the entire structure helps to convert a seemingly unmanageable model into a format that can be solved using computers.
Selection of Element Type
The element type selection is crucial since it impacts the accuracy and efficiency of the FEA.
Different types of elements serve different purposes, such as modeling thin shells, thick plates, or solid structures.
Selecting the appropriate element type ensures that the analysis accurately reflects the real-world behavior of the component or system being analyzed.
Elements can be linear or higher-order, with the latter offering greater accuracy but at the cost of increased computational effort.
Material Properties and Boundary Conditions
In FEM, specifying the material properties is essential as it influences the element’s response to external forces.
The material properties include Young’s Modulus, Poisson’s ratio, density, and other physical properties relevant to the analysis.
Boundary conditions define how the component is supported or restrained.
They can be applied in terms of displacements, forces, or thermal effects.
Correctly setting these parameters is vital for the accuracy of simulations.
Meshing the Model
Mesh generation is the process of creating a network (mesh) of elements over the CAD model.
The quality of the mesh greatly influences the FEA results.
A finer mesh, with smaller elements, usually offers more accurate results but requires more computational resources.
Conversely, a coarse mesh might not capture all the nuances of a structure’s behavior but can save time in simpler analyses.
Effective Use of CAE and FEA in Strength Design
Integration in the Design Process
To effectively utilize CAE tools, integration into the design process from the early stages is vital.
Conducting FEA early allows engineers to make informed decisions and address potential issues before they escalate.
This proactive approach fosters innovative solutions and refined product designs.
Incorporating CAE analysis during the conceptual and pre-production phases aids in developing robust products without incurring high costs.
Verification and Validation
After performing FEA, verifying and validating the results are crucial steps.
Verification ensures that the simulation was set up correctly, while validation confirms that the simulation results align with real-world behaviors.
Testing physical prototypes alongside simulated models helps in fine-tuning the CAE results, thus bridging the gap between theoretical calculations and empirical observations.
Optimization for Performance and Cost
One of the key benefits of CAE analysis is its ability to optimize designs for both performance and cost.
FEA can help identify weaknesses in a design, allowing engineers to redistribute material or alter geometries to enhance strength without excessive material usage.
The use of optimization algorithms – derived from CAE results – enables engineers to test various design scenarios quickly, ultimately selecting the most efficient design.
Iterative Improvement and Risk Reduction
CAE enables iterative improvement by facilitating modifications and retesting of designs without physical prototypes.
This enhances the overall design quality significantly by providing data-driven insights into potential failure points.
Engineers can confidently predict how the final product will perform, thus reducing risks associated with launching new products.
Conclusion
In understanding and applying CAE analysis and finite element methods, engineers can substantially enhance the strength design process.
By leveraging FEM, engineers gain detailed, quantitative insights into the structural behavior of materials and components under various conditions.
This vital information drives innovation and efficiency within engineering projects.
Ensuring effective integration of CAE tools throughout the design stages, while conducting thorough verification and validation, paves the way for high-quality, reliable products.
As design challenges evolve, mastering CAE analysis and FEA methods will remain crucial to delivering competitive and economically viable engineering solutions.
資料ダウンロード
QCD管理受発注クラウド「newji」は、受発注部門で必要なQCD管理全てを備えた、現場特化型兼クラウド型の今世紀最高の受発注管理システムとなります。
ユーザー登録
受発注業務の効率化だけでなく、システムを導入することで、コスト削減や製品・資材のステータス可視化のほか、属人化していた受発注情報の共有化による内部不正防止や統制にも役立ちます。
NEWJI DX
製造業に特化したデジタルトランスフォーメーション(DX)の実現を目指す請負開発型のコンサルティングサービスです。AI、iPaaS、および先端の技術を駆使して、製造プロセスの効率化、業務効率化、チームワーク強化、コスト削減、品質向上を実現します。このサービスは、製造業の課題を深く理解し、それに対する最適なデジタルソリューションを提供することで、企業が持続的な成長とイノベーションを達成できるようサポートします。
製造業ニュース解説
製造業、主に購買・調達部門にお勤めの方々に向けた情報を配信しております。
新任の方やベテランの方、管理職を対象とした幅広いコンテンツをご用意しております。
お問い合わせ
コストダウンが利益に直結する術だと理解していても、なかなか前に進めることができない状況。そんな時は、newjiのコストダウン自動化機能で大きく利益貢献しよう!
(β版非公開)