- お役立ち記事
- Fundamentals of CAN communication and key points for developing in-vehicle electronic control networks
月間76,176名の
製造業ご担当者様が閲覧しています*
*2025年3月31日現在のGoogle Analyticsのデータより
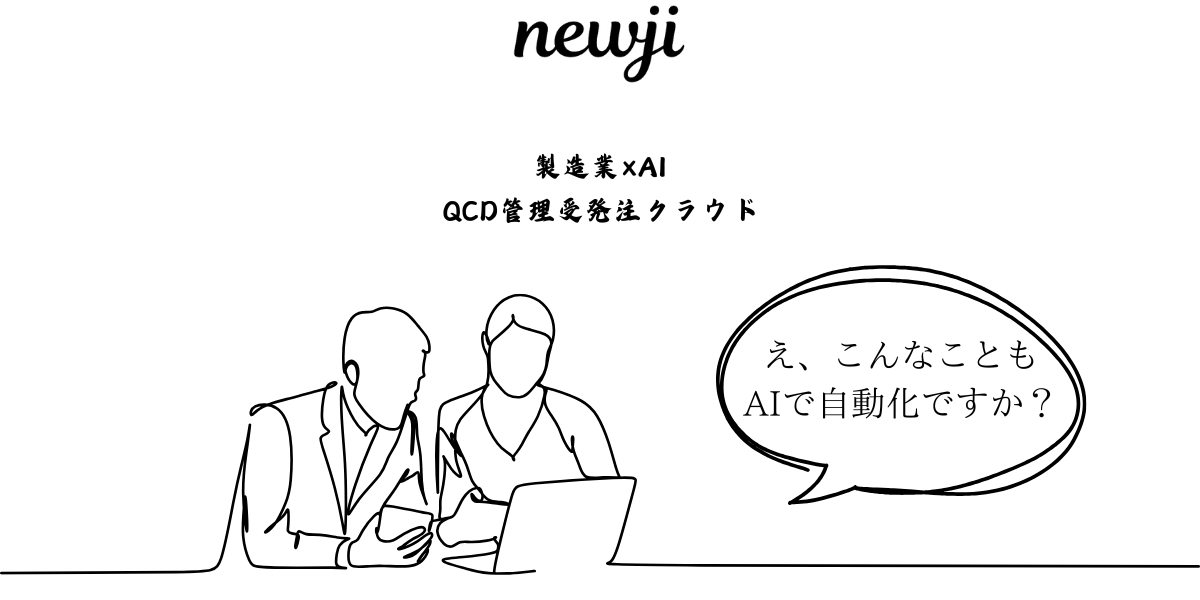
Fundamentals of CAN communication and key points for developing in-vehicle electronic control networks
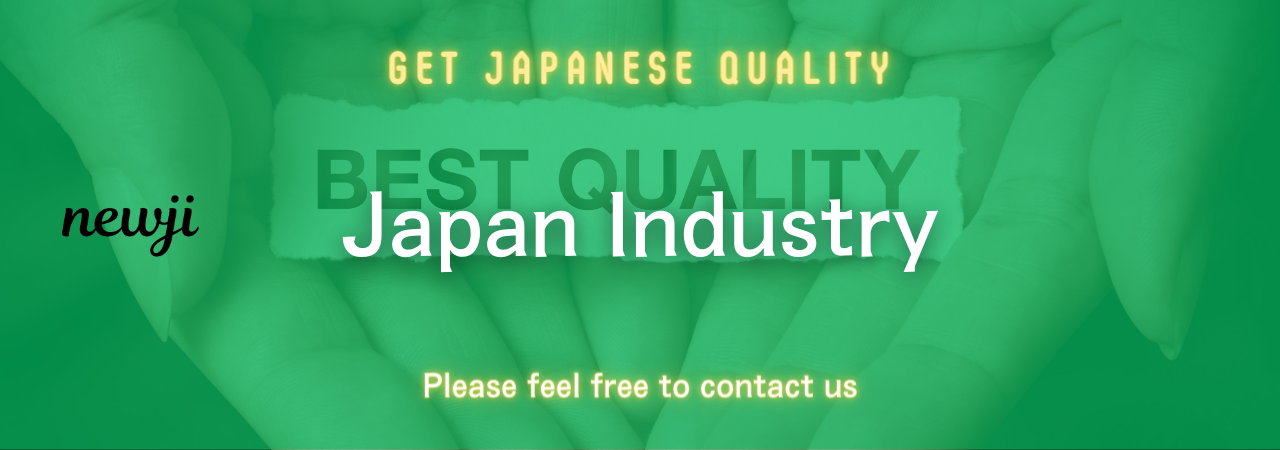
目次
Understanding CAN Communication
The Controller Area Network, commonly known as CAN, is a robust vehicle bus standard designed to allow microcontrollers and devices to communicate with one another without a host computer.
It was originally developed by Bosch in the 1980s for in-vehicle communication, aiming to establish efficient communication between various in-vehicle devices.
Nowadays, CAN is a vital component in the automotive industry and has become a staple in the development of electronic control networks within vehicles.
Why CAN Communication is Essential
CAN communication is integral to the operation of modern vehicles because it enables the transfer of real-time data between multiple electronic control units (ECUs).
These ECUs manage various systems such as the engine, transmission, antilock braking systems, and more.
With CAN, the communication between such systems is both efficient and reliable, reducing the wiring complexity and weight, which in turn, improves vehicle performance and fuel efficiency.
How CAN Communication Works
At the core of CAN communication is its message-based protocol.
This protocol is designed to handle error detection and fault confinement automatically, making it reliable under harsh conditions.
Message-Based Protocol
In a CAN network, each node can send and receive messages.
Unlike other network protocols that assign addresses to individual units, CAN uses message identifiers to determine priority.
When a node transmits a message, it listens on the bus to determine if one or more nodes have a higher priority message.
Should a conflict arise, the node with the higher priority message continues, while the others withdraw.
Error Detection and Handling
CAN communication incorporates multiple levels of error detection.
These include bit monitoring, cyclic redundancy checks, and message validation.
When an error is detected, error counters are incremented, and the system can classify nodes as faulty, isolating them from the rest of the network until the issue is resolved.
This robust error handling is crucial for maintaining data integrity and ensuring system reliability.
The Structure of a CAN Frame
A CAN frame, the primary data unit of CAN communication, consists of the following components:
CAN Data Frame
1. **Start of Frame (SOF):** A single dominant bit marking the start of a message.
2. **Arbitration Field:** Comprises the identifier and the remote transmission request (RTR) bit.
3. **Control Field:** Includes the data length code to specify the number of data bytes in the message.
4. **Data Field:** Carries the actual data, which can range from 0 to 8 bytes.
5. **CRC Field:** Contains the cyclic redundancy check bits for error detection.
6. **ACK Field:** Used for acknowledging receipt of a message.
7. **End of Frame:** Marks the end of the frame with seven recessive bits.
Advantages of CAN Communication in Vehicles
The adoption of CAN communication in vehicles offers significant advantages:
Reduced Wiring Complexity
Traditional automotive systems often required point-to-point connections between devices.
CAN minimizes this by allowing multiple devices to be connected on a single bus, effectively reducing the total amount of wiring needed.
This reduction in wiring not only decreases the vehicle’s weight but also simplifies installation and maintenance.
Cost-Effectiveness
By minimizing the amount of wiring needed, CAN technology also reduces production costs.
Furthermore, with fewer physical connections to maintain, the likelihood of mechanical failures decreases, improving overall vehicle reliability.
Scalability and Flexibility
CAN networks can be easily extended by simply adding more ECUs to the system.
This scalability is crucial as vehicle technology evolves, allowing new features to be integrated without significant overhauls to the infrastructure.
Real-Time Data Transmission
CAN facilitates real-time communication between different vehicle systems, which is essential for advanced driver-assistance systems (ADAS) and critical safety functions.
These systems require rapid and accurate data exchanges to function effectively, making CAN an ideal choice.
Key Considerations for Developing In-Vehicle Electronic Control Networks
When developing in-vehicle electronic control networks using CAN, there are several key points to consider:
Network Design and Layout
Designing a well-structured CAN network layout is critical.
The network should be designed to optimize data flow, ensuring that high-priority messages are transmitted efficiently.
Consideration must also be given to the physical placement of devices to minimize potential interference and signal degradation.
Understanding CAN Limitations
While CAN is highly efficient, it has limitations, such as the maximum bus length and the speed of data transmission.
Designers must balance these limitations with the network’s requirements to ensure optimal performance without sacrificing reliability or speed.
Security Measures
With the increasing integration of Internet of Things (IoT) technologies and connectivity features in vehicles, security is paramount.
Although CAN was not initially designed with security in mind, robust security measures, such as message authentication and encryption, should be implemented to protect against unauthorized access and data tampering.
Compliance with Standards
Developers should ensure that their CAN network complies with industry standards, such as ISO 11898.
Compliance ensures reliability, safety, and interoperability with other systems and devices, which are crucial factors in automotive design and engineering.
Conclusion
CAN communication has fundamentally transformed in-vehicle communication by offering a reliable and efficient method for electronic control units to interact.
Its robust architecture and scalability make it an essential component of modern automotive systems.
As technology and vehicle design continue to advance, understanding the fundamentals of CAN communication and developing effective in-vehicle electronic control networks will remain crucial in creating safe and efficient vehicles.
資料ダウンロード
QCD管理受発注クラウド「newji」は、受発注部門で必要なQCD管理全てを備えた、現場特化型兼クラウド型の今世紀最高の受発注管理システムとなります。
ユーザー登録
受発注業務の効率化だけでなく、システムを導入することで、コスト削減や製品・資材のステータス可視化のほか、属人化していた受発注情報の共有化による内部不正防止や統制にも役立ちます。
NEWJI DX
製造業に特化したデジタルトランスフォーメーション(DX)の実現を目指す請負開発型のコンサルティングサービスです。AI、iPaaS、および先端の技術を駆使して、製造プロセスの効率化、業務効率化、チームワーク強化、コスト削減、品質向上を実現します。このサービスは、製造業の課題を深く理解し、それに対する最適なデジタルソリューションを提供することで、企業が持続的な成長とイノベーションを達成できるようサポートします。
製造業ニュース解説
製造業、主に購買・調達部門にお勤めの方々に向けた情報を配信しております。
新任の方やベテランの方、管理職を対象とした幅広いコンテンツをご用意しております。
お問い合わせ
コストダウンが利益に直結する術だと理解していても、なかなか前に進めることができない状況。そんな時は、newjiのコストダウン自動化機能で大きく利益貢献しよう!
(β版非公開)