- お役立ち記事
- Fundamentals of casting in aluminum alloys, causes of defects and defects, and troubleshooting
Fundamentals of casting in aluminum alloys, causes of defects and defects, and troubleshooting
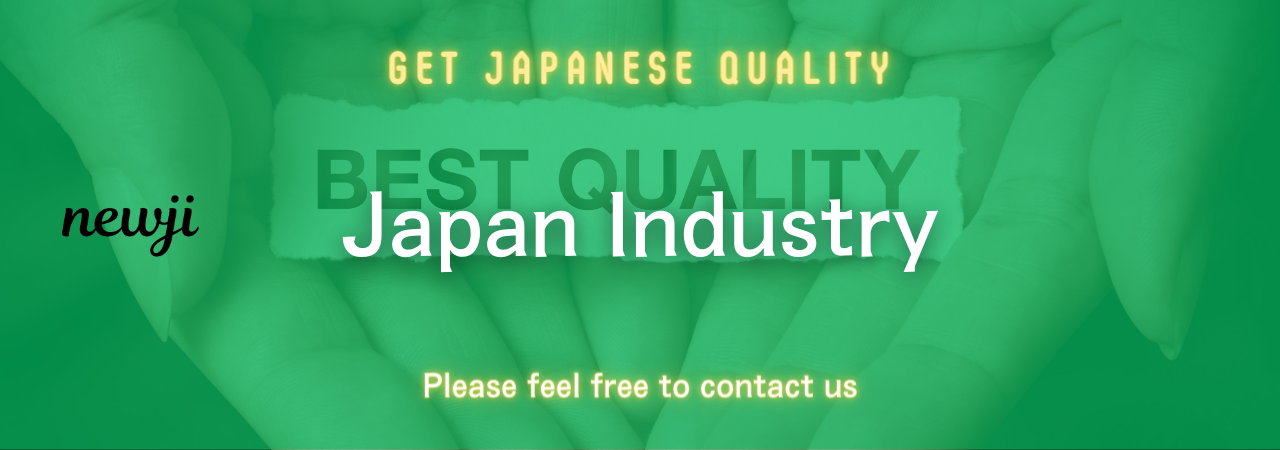
目次
Introduction to Casting in Aluminum Alloys
Casting is a vital manufacturing process used to shape aluminum alloys into desired forms.
It involves pouring molten aluminum into a mold and allowing it to solidify.
This method is popular due to its ability to produce complex shapes with high precision and excellent surface finish.
Aluminum alloys are a preferred choice in casting because of their lightweight nature and corrosion resistance.
These properties make them ideal for various industries, such as automotive, aerospace, and construction.
Understanding the fundamentals of casting in aluminum alloys, along with potential defects and solutions, is crucial for achieving high-quality products.
Basic Principles of Aluminum Casting
Types of Aluminum Casting Techniques
Several casting techniques are used for aluminum alloys, each offering distinct advantages.
Some of the common methods include:
– **Sand Casting**: This is one of the oldest casting methods.
Sand is used to create a mold cavity where molten aluminum is poured.
This technique is economical and flexible in terms of size and shape.
– **Die Casting**: Ideal for high-volume production, die casting uses a metal mold, known as a die.
It provides excellent dimensional accuracy and surface finish, making it suitable for intricate designs.
– **Permanent Mold Casting**: Similar to die casting, permanent mold casting uses reusable molds.
It’s effective for producing parts with consistent structural integrity.
– **Investment Casting**: Also known as lost-wax casting, this method is useful for creating complex geometries with fine detail.
A wax pattern is coated with a ceramic material, leaving a hollow shell after the wax is melted away.
Aluminum Alloy Selection
Choosing the right aluminum alloy is crucial for casting success.
Alloys are graded based on their composition and characteristics, such as strength, corrosion resistance, and thermal properties.
Common aluminum alloys used in casting include:
– **A356.0**: Known for its excellent castability and corrosion resistance, often used in automotive parts.
– **6061**: Offers good mechanical properties and is used in aerospace components and frames.
– **319.0**: Suitable for high-temperature applications, often found in engine blocks.
Causes of Defects in Aluminum Casting
Casting defects can compromise the integrity and quality of the final product.
Understanding their causes is key to prevention.
Poor Mold Design
The design of the mold plays a significant role in the quality of the casting.
Inadequate mold design can lead to various problems, such as:
– **Misruns**: When the molten metal does not completely fill the mold cavity, often due to improper gating systems or insufficient pouring temperature.
– **Cold Shuts**: Cold shuts occur when two streams of molten metal fail to merge smoothly, causing an incomplete filling.
Improper Cooling Rates
The cooling rate of aluminum alloys is crucial for preventing defects.
Uneven or rapid cooling can cause:
– **Porosity**: The presence of gas pockets or voids within the casting, affecting its structural integrity.
– **Shrinkage**: As aluminum contracts upon cooling, improper cooling may lead to shrinkage cavities within the casting.
Contamination
Impurities can enter the molten aluminum during the casting process, leading to defects.
Common contaminants include oxides, dross, and slag, which can cause:
– **Inclusions**: Non-metallic particles trapped within the casting, affecting its mechanical properties.
– **Cracks**: Contaminants may act as stress concentrators, resulting in cracks or fractures.
Troubleshooting Casting Defects
Addressing casting defects involves careful analysis and adjustments in the manufacturing process.
Optimizing Mold Design
To prevent defects related to mold design, consider the following:
– **Gating System**: Ensure proper design and placement of the gating system to facilitate smooth metal flow.
– **Risers and Vents**: Implement adequate risers and vents to allow gases to escape and compensate for shrinkage.
Controlling Cooling Rates
Proper cooling management is crucial for quality casting.
– **Cooling Techniques**: Use controlled cooling methods, such as annealing, to relieve internal stresses and minimize porosity.
– **Thermal Analysis**: Conduct thermal analysis to optimize cooling rates and ensure uniform solidification.
Ensuring Cleanliness and Purity
Prevent contamination by maintaining a clean casting environment.
– **Filtration**: Use filtration techniques to remove impurities from the molten metal before pouring.
– **Material Handling**: Ensure that all tools and equipment are free from contaminants and moisture.
Conclusion
Casting in aluminum alloys is a complex yet rewarding process essential for producing high-quality, reliable components.
A thorough understanding of the fundamentals of casting techniques, along with the causes of casting defects, enables manufacturers to identify and rectify issues effectively.
By optimizing mold design, cooling rates, and cleanliness of materials, it is possible to achieve defect-free aluminum castings that meet industry standards and customer expectations.
資料ダウンロード
QCD調達購買管理クラウド「newji」は、調達購買部門で必要なQCD管理全てを備えた、現場特化型兼クラウド型の今世紀最高の購買管理システムとなります。
ユーザー登録
調達購買業務の効率化だけでなく、システムを導入することで、コスト削減や製品・資材のステータス可視化のほか、属人化していた購買情報の共有化による内部不正防止や統制にも役立ちます。
NEWJI DX
製造業に特化したデジタルトランスフォーメーション(DX)の実現を目指す請負開発型のコンサルティングサービスです。AI、iPaaS、および先端の技術を駆使して、製造プロセスの効率化、業務効率化、チームワーク強化、コスト削減、品質向上を実現します。このサービスは、製造業の課題を深く理解し、それに対する最適なデジタルソリューションを提供することで、企業が持続的な成長とイノベーションを達成できるようサポートします。
オンライン講座
製造業、主に購買・調達部門にお勤めの方々に向けた情報を配信しております。
新任の方やベテランの方、管理職を対象とした幅広いコンテンツをご用意しております。
お問い合わせ
コストダウンが利益に直結する術だと理解していても、なかなか前に進めることができない状況。そんな時は、newjiのコストダウン自動化機能で大きく利益貢献しよう!
(Β版非公開)