- お役立ち記事
- Fundamentals of casting simulation and application to defect prevention using visualization technology
月間76,176名の
製造業ご担当者様が閲覧しています*
*2025年3月31日現在のGoogle Analyticsのデータより
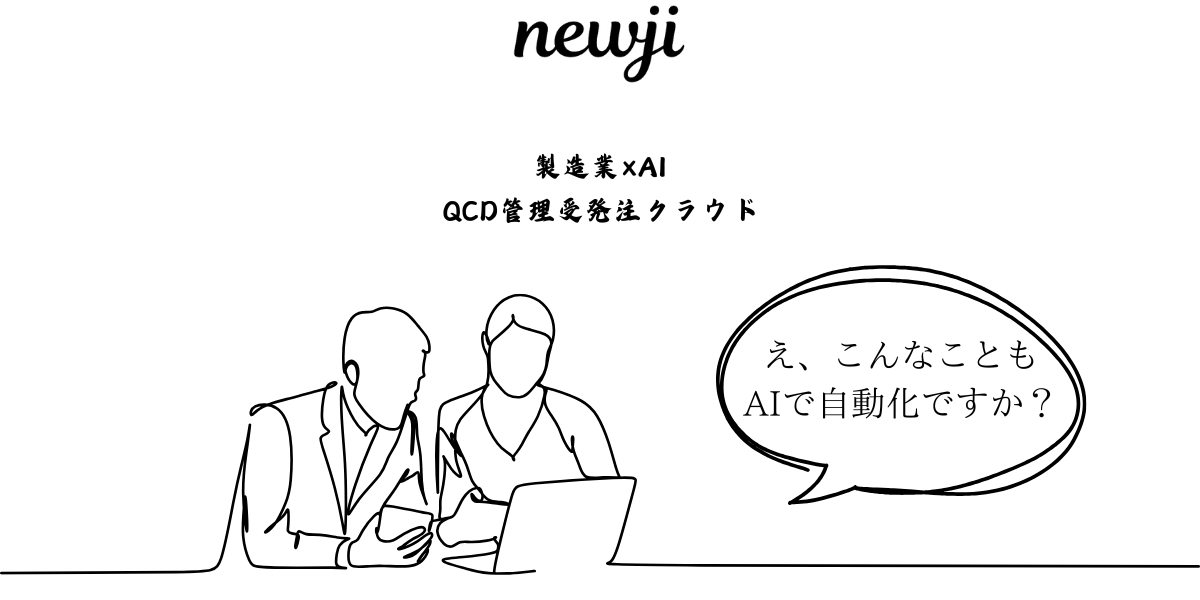
Fundamentals of casting simulation and application to defect prevention using visualization technology
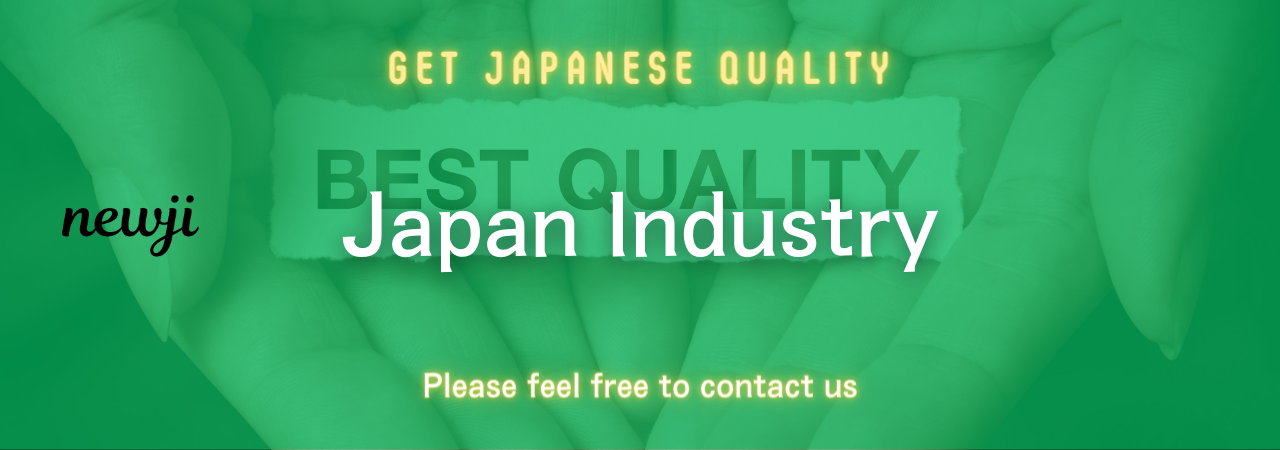
目次
Understanding Casting Simulation
Casting simulation is a crucial aspect of modern manufacturing, allowing industries to anticipate and mitigate potential defects in cast components.
At its core, casting simulation involves creating a digital representation of the casting process.
This digital model mimics the physical phenomena that occur when molten metal is poured into a mold, cools, and solidifies.
By employing advanced computational techniques, engineers can predict the behavior of the material as it transitions from liquid to solid.
This process is vital for identifying and addressing issues that might arise during the casting.
Simulation tools use mathematical algorithms to predict the flow, heat transfer, and solidification patterns of the metal.
With these insights, manufacturers can optimize their processes, leading to higher-quality products and reduced time to market.
The Role of Visualization Technology
Visualization technology plays a pivotal role in casting simulation by providing a tangible and interactive representation of the simulated processes.
Through detailed graphics and animations, engineers can visualize the entire casting operation from start to finish.
This capability transforms complex data into an understandable format, enabling more informed decision-making.
For instance, visualization can highlight areas of high thermal stress or potential hotspots where defects like porosity might develop.
By highlighting these critical areas, manufacturers can implement corrective measures before actual production begins.
This proactive approach not only improves product quality but also significantly reduces waste and manufacturing costs.
Common Defects in Casting
Before delving into defect prevention, it’s essential to understand the common issues that can arise during casting.
These defects can compromise the structural integrity and aesthetic appeal of the final product.
1. Porosity
Porosity refers to the presence of small voids or cavities within the casting.
These voids are often caused by trapped gases or shrinkage during solidification.
Porous castings can lead to weaknesses, making the component unsuitable for its intended function.
2. Cold Shut
A cold shut occurs when two streams of liquid metal meet but do not fuse together completely.
This defect is typically the result of insufficient temperatures or slow pouring rates, leaving visible lines or seams on the casting.
3. Misrun
Misruns happen when the molten metal solidifies before completely filling the mold.
This can lead to incomplete parts and is often caused by inadequate pouring temperatures or complex mold designs.
4. Shrinkage
Shrinkage defects occur due to volume reduction as the metal cools and solidifies.
These defects can manifest as internal cavities or surface depressions, compromising the part’s durability.
Applying Simulation to Prevent Casting Defects
Utilizing casting simulation paired with visualization technology can prevent these defects, enhancing the manufacturing process’s efficiency and reliability.
Optimizing Pouring Temperature
Simulation allows manufacturers to experiment with different pouring temperatures to ensure complete mold filling.
By visualizing how temperature variations affect the metal flow, engineers can identify the optimal range to prevent cold shuts and misruns.
Managing Solidification
Accurate prediction and control of the solidification process are essential for preventing porosity and shrinkage.
Simulation provides insights into cooling rates and solidification times, helping manufacturers adjust parameters to minimize void formation.
Enhancing Mold Design
Through simulation, engineers can evaluate and modify mold designs for optimal flow paths and cooling.
This helps in minimizing turbulence and air entrapment, significantly reducing the chance of forming defects.
Assessing Material Properties
Different materials behave uniquely during casting.
Simulation software can model these material-specific behaviors, allowing manufacturers to choose the best material and casting method for their specific needs.
Quality Control and Testing
In addition to defect prevention, casting simulation aids in post-production quality control.
Virtual testing environments simulate stress and load conditions, ensuring the casting meets all safety and durability standards before physical testing.
Future of Casting Simulation
The future of casting simulation is promising, with continuous advancements in computational power and algorithms enhancing its precision and usability.
Incorporating machine learning and artificial intelligence can further streamline defect prevention by identifying patterns and predicting outcomes with greater accuracy.
As industries move towards more sustainable practices, simulation will also play a key role in minimizing resource consumption and reducing carbon footprints.
By optimizing the entire casting process from start to finish, manufacturers can achieve significant efficiency gains while minimizing waste.
In conclusion, casting simulation coupled with visualization technology is a game-changer in the field of manufacturing.
By understanding and addressing potential defects before production, companies can produce higher quality, more reliable components.
As technology evolves, the scope and impact of casting simulation will continue to expand, paving the way for innovation in manufacturing processes.
資料ダウンロード
QCD管理受発注クラウド「newji」は、受発注部門で必要なQCD管理全てを備えた、現場特化型兼クラウド型の今世紀最高の受発注管理システムとなります。
ユーザー登録
受発注業務の効率化だけでなく、システムを導入することで、コスト削減や製品・資材のステータス可視化のほか、属人化していた受発注情報の共有化による内部不正防止や統制にも役立ちます。
NEWJI DX
製造業に特化したデジタルトランスフォーメーション(DX)の実現を目指す請負開発型のコンサルティングサービスです。AI、iPaaS、および先端の技術を駆使して、製造プロセスの効率化、業務効率化、チームワーク強化、コスト削減、品質向上を実現します。このサービスは、製造業の課題を深く理解し、それに対する最適なデジタルソリューションを提供することで、企業が持続的な成長とイノベーションを達成できるようサポートします。
製造業ニュース解説
製造業、主に購買・調達部門にお勤めの方々に向けた情報を配信しております。
新任の方やベテランの方、管理職を対象とした幅広いコンテンツをご用意しております。
お問い合わせ
コストダウンが利益に直結する術だと理解していても、なかなか前に進めることができない状況。そんな時は、newjiのコストダウン自動化機能で大きく利益貢献しよう!
(β版非公開)