- お役立ち記事
- Fundamentals of CFD (Computational Fluid Dynamics) and its application to higher performance through optimal design
月間77,185名の
製造業ご担当者様が閲覧しています*
*2025年2月28日現在のGoogle Analyticsのデータより
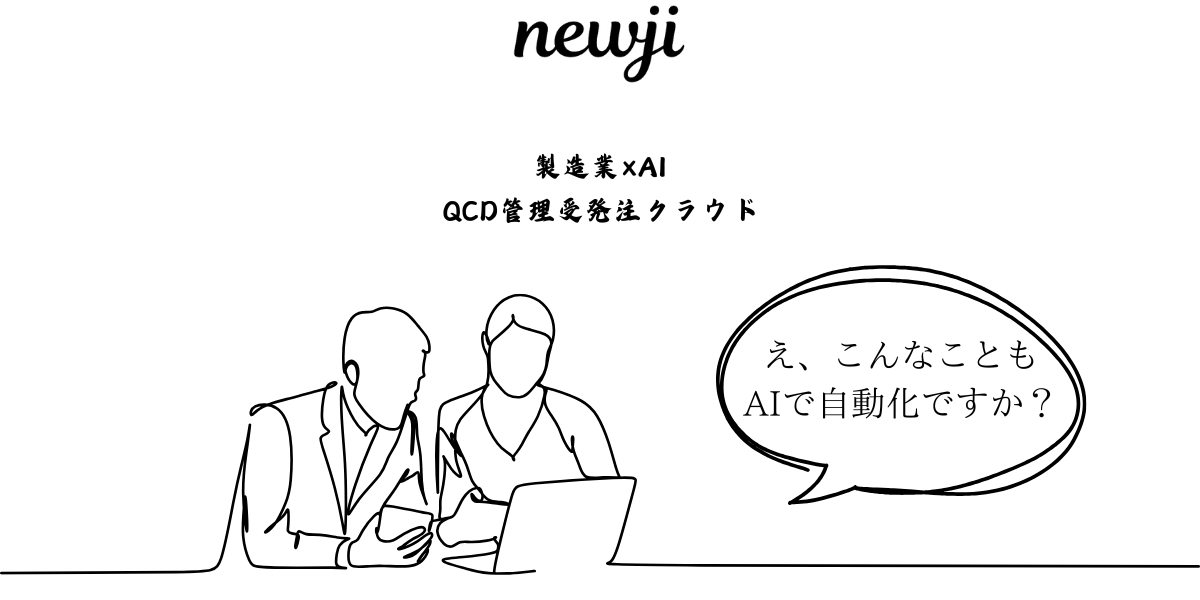
Fundamentals of CFD (Computational Fluid Dynamics) and its application to higher performance through optimal design
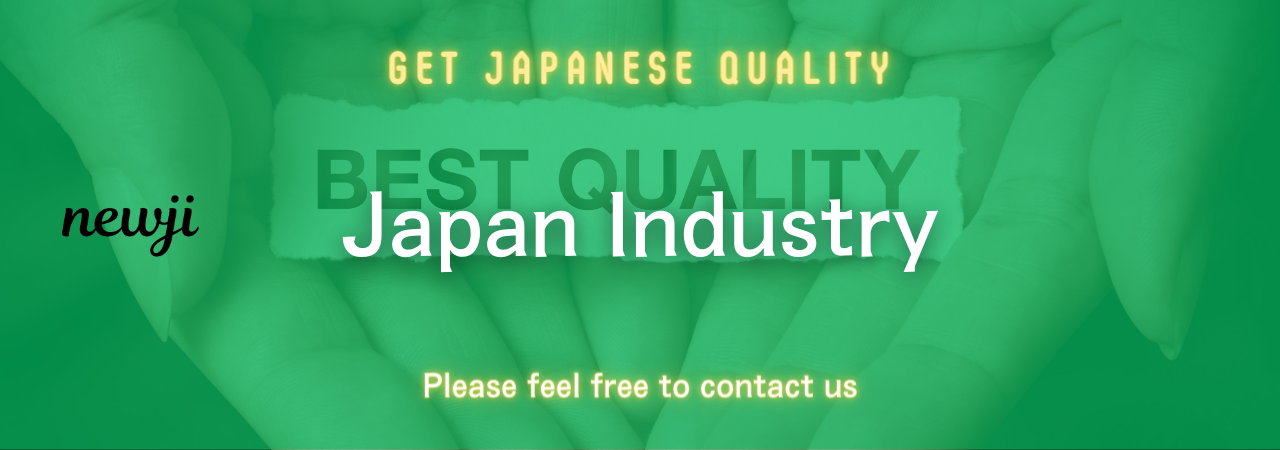
目次
What is Computational Fluid Dynamics (CFD)?
Computational Fluid Dynamics, or CFD, is a branch of fluid mechanics that uses numerical analysis and data structures to solve and analyze problems involving fluid flows.
The fundamental basis of almost all CFD problems are the Navier-Stokes equations, which describe how the velocity, pressure, temperature, and density of a moving fluid are interconnected.
These equations are complex and difficult to solve analytically, which is why numerical methods are employed.
CFD uses algorithms and computational power to perform the simulations, enabling engineers and scientists to predict fluid behavior in various scenarios.
Key Principles of CFD
CFD simulations involve several key principles and methodologies essential for accurate analysis.
These include:
Discretization
Discretization involves breaking down a large domain into smaller, finite parts known as grids or elements.
This process transforms continuous partial differential equations into algebraic equations that can be solved numerically.
Common discretization techniques include Finite Volume, Finite Element, and Finite Difference methods.
Mesh Generation
Mesh generation is a critical part of CFD and involves creating a grid over the domain in which simulations are conducted.
The quality of the mesh can significantly influence the accuracy and efficiency of the simulation.
Meshes can be structured or unstructured, with finer meshes generally providing more detailed solutions but requiring more computational resources.
Turbulence Modeling
Turbulence is a complex and chaotic movement of fluid particles that is often encountered in practical fluid flow problems.
Modeling turbulence accurately is essential for reliable CFD results.
Various models like Large Eddy Simulation (LES) and Reynolds-Averaged Navier-Stokes (RANS) are used to approximate the effects of turbulence in CFD simulations.
Applications of CFD
CFD has widespread applications in various industries and fields.
Here are some notable applications:
Aerospace Industry
In the aerospace industry, CFD is used to simulate and analyze airflow over aircraft surfaces.
It helps in improving aircraft design to enhance aerodynamic performance and fuel efficiency.
Engineers can simulate different flight conditions and optimize designs without the need for expensive and time-consuming wind tunnel tests.
Automotive Industry
CFD is pivotal in automotive design for optimizing aerodynamics, reducing drag, and enhancing fuel efficiency.
Manufacturers use CFD to simulate airflow over vehicles to determine the effects on performance, handling, and stability.
Additionally, CFD helps in improving the thermal management of engine components and the efficiency of HVAC systems.
Energy Sector
In the energy sector, CFD is used to optimize the design and operation of turbines, both in wind and hydroelectric power generation.
It helps in predicting and analyzing fluid flow conditions to enhance efficiency and output.
CFD also assists in modeling combustion processes in power plants to reduce emissions and improve energy efficiency.
Biomedical Engineering
CFD plays a significant role in biomedical engineering by simulating blood flow through arteries and medical devices.
It helps in designing better cardiovascular devices and understanding the effects of different conditions on blood flow dynamics.
CFD assists researchers and engineers in finding optimal solutions for medical implants and prosthetics.
Enhanced Performance through Optimal Design
One of the main benefits of using CFD is the ability to improve system performance through optimal design.
With CFD, engineers can explore a vast range of design parameters and configurations to identify the best solutions.
Design Iteration and Optimization
CFD allows for the quick evaluation of multiple design iterations, providing valuable insights into how changes affect performance.
By using optimization algorithms within the CFD software, engineers can systematically explore design space and identify optimal configurations.
This approach reduces the need for physical prototypes and speeds up the design process.
Integration with Machine Learning
Recently, the integration of machine learning techniques with CFD has opened new avenues for optimization.
Machine learning can process and analyze vast amounts of simulation data to identify patterns and correlations.
This integration enables predictive modeling and real-time adjustments in simulations, leading to better design decisions.
Real-World Scenarios
CFD can simulate real-world conditions with precision, considering factors such as varying temperatures, pressures, and fluid properties.
This capability allows engineers to predict and mitigate potential issues that might arise in actual operating conditions.
Ultimately, this leads to designs that not only perform optimally but also have higher reliability and safety.
Challenges in CFD
High Computational Demand
One of the primary challenges in CFD is the high computational demand required for complex simulations.
High-resolution meshes and detailed models require significant computing power and time.
Advancements in hardware and parallel computing have alleviated some of these demands, but efficient resource management is still necessary.
Modeling Complex Phenomena
Although CFD has advanced significantly, modeling complex phenomena such as multiphase flows, chemical reactions, and highly turbulent flows remains challenging.
Accurate modeling still requires improvements in numerical methods and turbulence models to handle these intricate scenarios.
Validation and Verification
Ensuring the accuracy of CFD simulations through validation and verification is crucial.
CFD models must be validated against experimental data or established benchmarks to ensure their reliability.
Establishing confidence in the simulation results requires ongoing efforts in validation and verification processes.
資料ダウンロード
QCD管理受発注クラウド「newji」は、受発注部門で必要なQCD管理全てを備えた、現場特化型兼クラウド型の今世紀最高の受発注管理システムとなります。
ユーザー登録
受発注業務の効率化だけでなく、システムを導入することで、コスト削減や製品・資材のステータス可視化のほか、属人化していた受発注情報の共有化による内部不正防止や統制にも役立ちます。
NEWJI DX
製造業に特化したデジタルトランスフォーメーション(DX)の実現を目指す請負開発型のコンサルティングサービスです。AI、iPaaS、および先端の技術を駆使して、製造プロセスの効率化、業務効率化、チームワーク強化、コスト削減、品質向上を実現します。このサービスは、製造業の課題を深く理解し、それに対する最適なデジタルソリューションを提供することで、企業が持続的な成長とイノベーションを達成できるようサポートします。
製造業ニュース解説
製造業、主に購買・調達部門にお勤めの方々に向けた情報を配信しております。
新任の方やベテランの方、管理職を対象とした幅広いコンテンツをご用意しております。
お問い合わせ
コストダウンが利益に直結する術だと理解していても、なかなか前に進めることができない状況。そんな時は、newjiのコストダウン自動化機能で大きく利益貢献しよう!
(β版非公開)