- お役立ち記事
- Fundamentals of coating technology and drying technology and key points to prevent defects and troubles
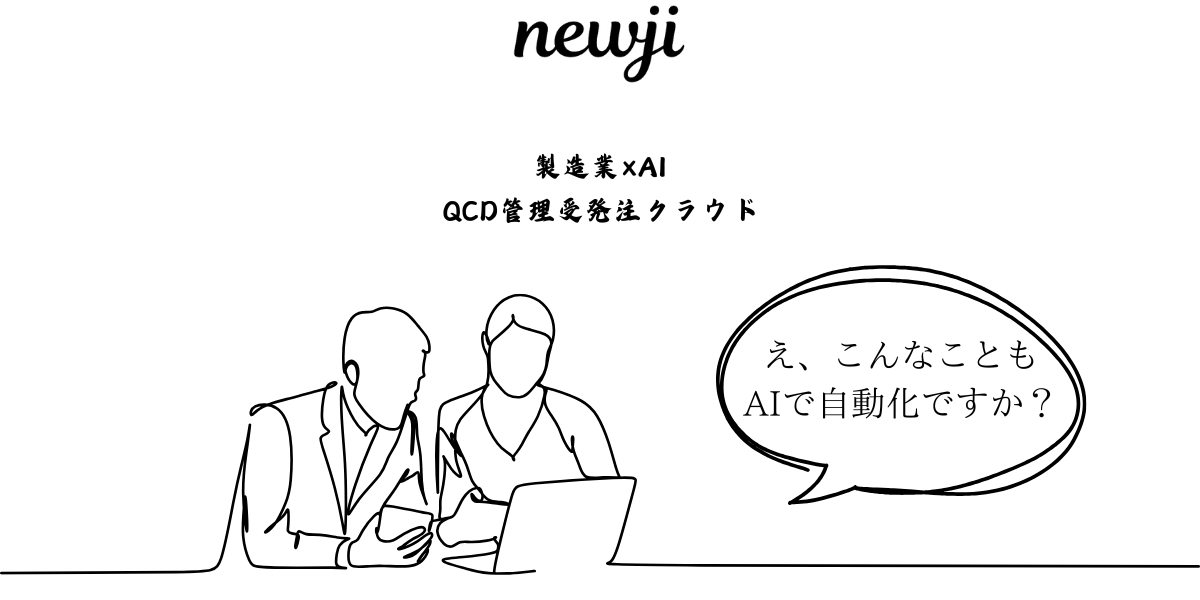
Fundamentals of coating technology and drying technology and key points to prevent defects and troubles
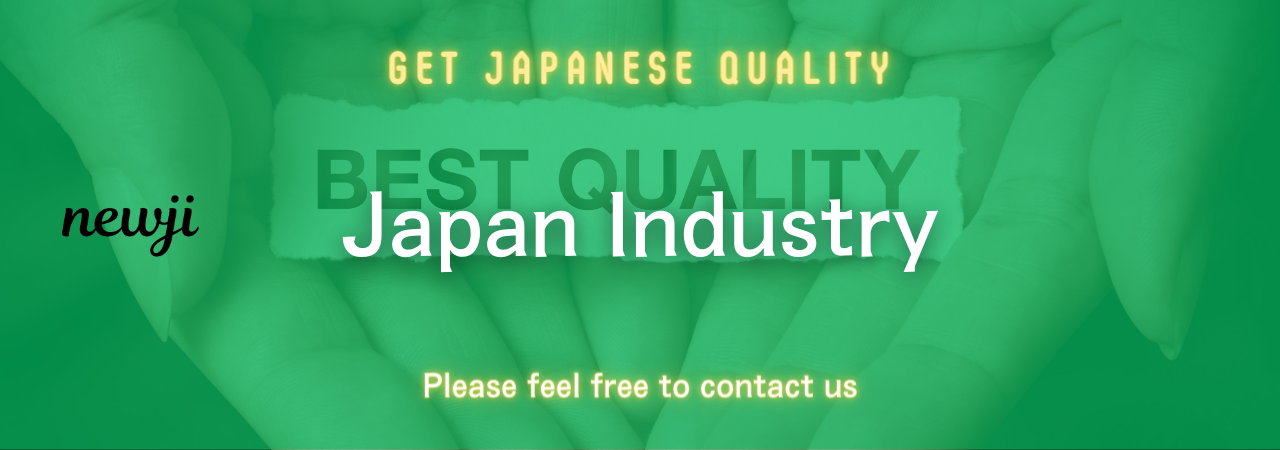
目次
Understanding Coating Technology
Coating technology plays a pivotal role in numerous industries, serving as a protective and decorative layer over various substrates.
From manufacturing to construction, coatings provide essential properties such as corrosion resistance, weather protection, and aesthetic enhancement.
The most fundamental aspect of coating technology involves the selection of appropriate materials and techniques.
This process ensures that the coating serves its intended purpose effectively.
In today’s market, there is a wide range of coatings, including paints, varnishes, and special polymers, each designed for specific applications.
Understanding the unique characteristics of these coatings can significantly influence the outcome of the coating process.
The selection process considers factors such as the type of substrate, the environmental conditions it will be exposed to, and the desired finish.
Types of Coating Technologies
Coating technologies can be categorized into several types, each tailored to specific applications and industries.
These include liquid coatings, powder coatings, and specialty coatings.
Liquid coatings are the most common and consist of a solvent or water-based liquid applied to a surface.
They are ideal for achieving smooth finishes and are commonly used in automotive and consumer goods industries.
Powder coatings, on the other hand, involve applying a dry, powdered substance that is cured under heat.
This type of coating is known for its durability and resistance to chipping, making it suitable for metal items like bicycles and furniture.
Specialty coatings, catering to niche markets, offer unique properties such as anti-static, anti-graffiti, and fire-retardant capabilities.
These coatings are used in environments where additional material protection is needed.
Drying Technology in Coating Processes
Drying technology is a critical component of the coating process.
Proper drying is essential to ensure that coatings adhere correctly to surfaces and do not develop defects.
Inadequate drying can lead to problems such as blistering, peeling, and cracking, compromising the coating’s integrity and appearance.
There are several drying techniques used in the coating industry.
These include air drying, forced air drying, and oven drying.
Air drying is the simplest and most natural approach, relying on atmosphere to dry the coating.
However, it is often slow and susceptible to environmental conditions.
Forced air drying speeds up the process by using fans or blowers, thereby reducing the drying time significantly.
Oven drying involves baking the coated substrate at high temperatures, leading to faster and more uniform drying.
This method is highly efficient but requires substantial energy and equipment investment.
Factors Influencing Drying
Several factors influence the drying process, affecting the performance and quality of the coating.
These include temperature, humidity, airflow, and the coating’s chemical composition.
Temperature plays a vital role in speeding up the evaporation rate of solvents or water in the coating.
Higher temperatures generally accelerate drying, but they must be balanced to avoid damaging the substrate or the coating itself.
Humidity affects how efficiently moisture escapes from the coating.
High humidity levels can slow down the drying process and lead to condensation, which might result in defects.
Airflow is important as it facilitates the removal of moisture and solvents from the coating surface.
Proper ventilation enhances drying efficiency and prevents premature skinning or film formation.
The chemical composition of the coating material also determines drying time and method.
Solvent-based coatings generally dry faster than water-based ones.
Preventing Defects and Troubles in Coating
Preventing defects in coating technology and drying demands a thorough understanding and meticulous attention to detail.
By implementing preventive measures, manufacturers can ensure high-quality finishes and long-lasting performance.
One of the primary causes of coating defects is contamination.
Ensuring that substrates are clean and free from oil, dust, or other particles is crucial before applying any coating.
Poor surface preparation can lead to adhesion failure, resulting in blistering, flaking, or peeling.
Cleaning, sanding, and priming are essential steps to prepare surfaces adequately.
Another factor contributing to defects is the inappropriate choice of coating for the intended application.
Selecting a coating that does not align with the substrate type or environmental conditions can lead to premature wear and weathering.
Proper application techniques are vital in preventing defects and troubles.
Ensuring the correct thickness, smoothness, and coverage can sidestep common issues like sags, runs, and uneven surfaces.
Implementing quality control measures such as regular inspections and testing helps identify and rectify potential issues before they become significant problems.
Key Points to Consider
To mitigate coating troubles and enhance drying efficiency, consider the following key points:
1. **Material Compatibility**: Ensure that coating materials are compatible with the substrate and the environmental conditions they will face.
2. **Surface Preparation**: Dedicate time to appropriately clean and prepare surfaces before coating to enhance adhesion and longevity.
3. **Application Techniques**: Employ precise application methods, applying the right amount of coating at the recommended thickness.
4. **Environmental Factors**: Monitor and control factors like temperature and humidity to optimize the drying process.
5. **Regular Quality Checks**: Conduct routine inspections and perform quality tests on coated items to catch and address issues promptly.
By adhering to these guidelines and understanding the intricacies of coating and drying technology, manufacturers can produce superior products with durable, high-quality finishes.
The interplay of these technologies, when effectively managed, results in enhanced performance, aesthetic appeal, and extended lifespan of coated substrates.
資料ダウンロード
QCD調達購買管理クラウド「newji」は、調達購買部門で必要なQCD管理全てを備えた、現場特化型兼クラウド型の今世紀最高の購買管理システムとなります。
ユーザー登録
調達購買業務の効率化だけでなく、システムを導入することで、コスト削減や製品・資材のステータス可視化のほか、属人化していた購買情報の共有化による内部不正防止や統制にも役立ちます。
NEWJI DX
製造業に特化したデジタルトランスフォーメーション(DX)の実現を目指す請負開発型のコンサルティングサービスです。AI、iPaaS、および先端の技術を駆使して、製造プロセスの効率化、業務効率化、チームワーク強化、コスト削減、品質向上を実現します。このサービスは、製造業の課題を深く理解し、それに対する最適なデジタルソリューションを提供することで、企業が持続的な成長とイノベーションを達成できるようサポートします。
オンライン講座
製造業、主に購買・調達部門にお勤めの方々に向けた情報を配信しております。
新任の方やベテランの方、管理職を対象とした幅広いコンテンツをご用意しております。
お問い合わせ
コストダウンが利益に直結する術だと理解していても、なかなか前に進めることができない状況。そんな時は、newjiのコストダウン自動化機能で大きく利益貢献しよう!
(Β版非公開)