- お役立ち記事
- Fundamentals of Cutting Processing and Sensing Technology for Automation and Efficiency
月間76,176名の
製造業ご担当者様が閲覧しています*
*2025年3月31日現在のGoogle Analyticsのデータより
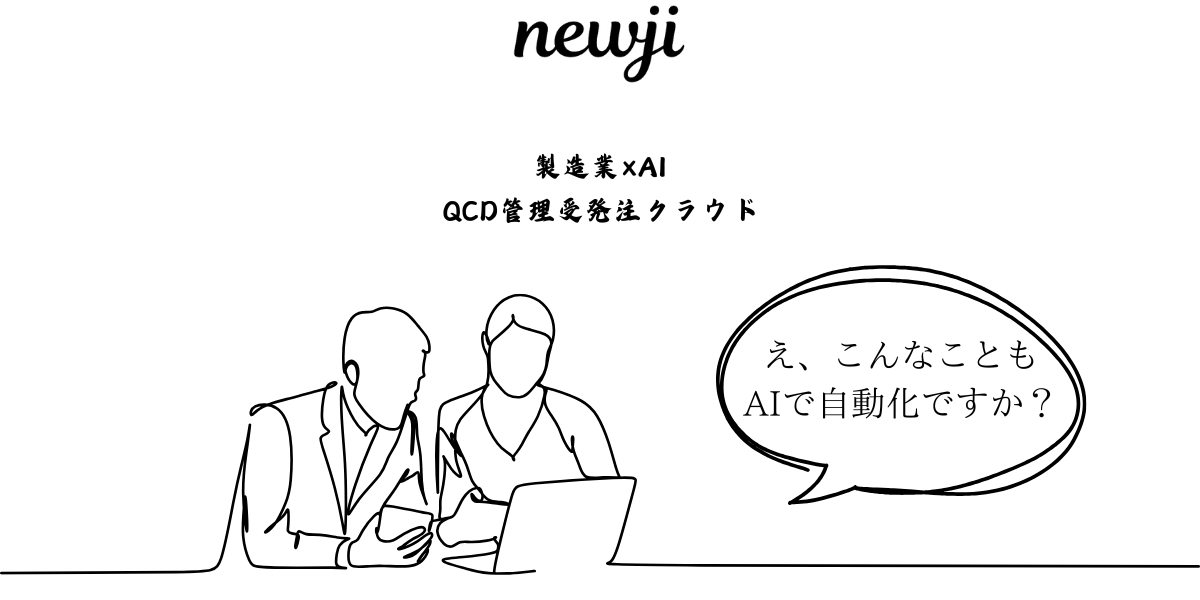
Fundamentals of Cutting Processing and Sensing Technology for Automation and Efficiency
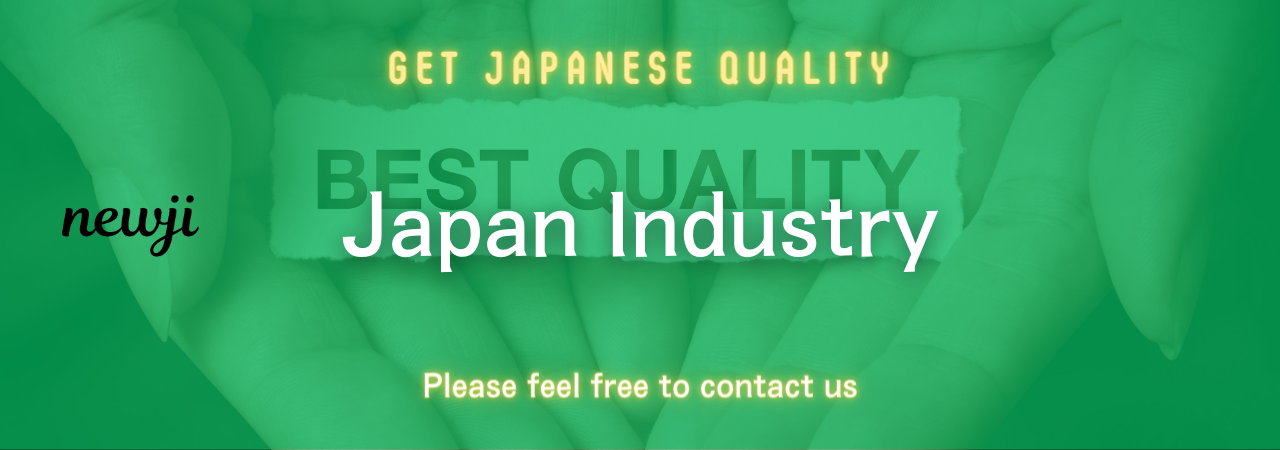
Cutting processing and sensing technology play a vital role in modern manufacturing and automation.
These technologies enhance efficiency, accuracy, and overall productivity in various industries.
Understanding the basics of these technologies can help businesses stay competitive in an ever-evolving market.
目次
What is Cutting Processing?
Cutting processing refers to the methods and techniques used to shape and size materials such as metal, wood, plastic, and composites.
The process involves removing unwanted material to achieve the desired shape and size.
There are different types of cutting processing techniques, each suitable for specific applications and materials.
Types of Cutting Processing Techniques
There are several cutting processing techniques, including mechanical, thermal, and chemical methods.
Each technique has its pros and cons, making it suitable for different applications.
Mechanical Cutting
Mechanical cutting uses physical force to remove material.
Common methods include milling, turning, and grinding.
**Milling:** Involves rotating a cutting tool to remove material from a workpiece.
**Turning:** Uses a lathe to rotate the workpiece while a cutting tool shapes it.
**Grinding:** Utilizes an abrasive wheel to remove material from the workpiece.
Thermal Cutting
Thermal cutting uses heat to melt or vaporize material.
This technique includes methods like laser cutting, plasma cutting, and oxy-fuel cutting.
**Laser Cutting:** Uses a high-powered laser beam to cut materials with precision.
**Plasma Cutting:** Employs a stream of ionized gas to cut through conductive materials.
**Oxy-fuel Cutting:** Involves burning a mixture of oxygen and fuel gas to cut materials.
Chemical Cutting
Chemical cutting, also known as etching, uses chemicals to remove material.
This method is often used for intricate designs and small-scale applications.
**Etching:** Involves applying a chemical solution to a material’s surface to remove unwanted areas.
Sensing Technology in Automation
Sensing technology is essential for automation, as it allows machines to detect and respond to changes in their environment.
Sensors collect data and send it to control systems, enabling automated processes to run smoothly and efficiently.
Types of Sensors
There are various types of sensors used in automation, each designed to detect specific parameters such as temperature, pressure, position, and more.
Temperature Sensors
Temperature sensors measure the temperature of an object or environment.
Common types include thermocouples, RTDs (Resistance Temperature Detectors), and infrared sensors.
**Thermocouples:** Generate a voltage proportional to the temperature difference between two dissimilar metals.
**RTDs:** Measure temperature by correlating the resistance of a metal with temperature.
**Infrared Sensors:** Detect temperature by measuring the infrared radiation emitted by an object.
Pressure Sensors
Pressure sensors measure the force exerted by a fluid (liquid or gas) on a surface.
Types of pressure sensors include piezoelectric, capacitive, and strain gauge sensors.
**Piezoelectric Sensors:** Generate an electric charge in response to pressure changes.
**Capacitive Sensors:** Measure pressure by detecting changes in capacitance caused by pressure variations.
**Strain Gauge Sensors:** Detect pressure by measuring the deformation of a material under pressure.
Position Sensors
Position sensors determine the position of an object in space.
Examples include encoders, potentiometers, and linear variable differential transformers (LVDTs).
**Encoders:** Convert the position or motion of an object into an electrical signal.
**Potentiometers:** Measure the position by varying resistance with the movement of a wiper along a resistive element.
**LVDTs:** Measure linear displacement by detecting variations in the inductance of a coil.
Proximity Sensors
Proximity sensors detect the presence or absence of an object without physical contact.
Types include inductive, capacitive, and ultrasonic sensors.
**Inductive Sensors:** Detect metallic objects by generating an electromagnetic field.
**Capacitive Sensors:** Sense non-metallic and metallic objects by measuring changes in capacitance.
**Ultrasonic Sensors:** Use sound waves to detect objects and measure distance.
The Role of Sensing Technology in Cutting Processing
Integrating sensing technology into cutting processing improves accuracy, efficiency, and safety.
Sensors help monitor and control various parameters, ensuring optimal performance and preventing damage to tools and materials.
Quality Control
Sensors play a crucial role in quality control by monitoring the dimensions and surface finish of the workpiece.
Position and displacement sensors ensure that the cutting tools operate within specified tolerances, while surface finish sensors detect defects and irregularities.
Tool Condition Monitoring
Sensing technology helps monitor the condition of cutting tools, detecting wear and breakage before they cause damage.
Vibration sensors and acoustic emission sensors can identify abnormalities, allowing for timely maintenance and reducing downtime.
Process Optimization
Sensors collect data on various process parameters, such as cutting force, temperature, and tool wear.
This information helps optimize cutting conditions, improving efficiency and extending the life of cutting tools.
Using advanced algorithms and data analysis, manufacturers can fine-tune their processes for maximum productivity.
Benefits of Integrating Cutting Processing and Sensing Technology
Combining cutting processing and sensing technology offers several benefits, making manufacturing processes more efficient and cost-effective.
Increased Efficiency
Automation and sensing technology help streamline cutting processes, reducing manual intervention and increasing productivity.
Real-time monitoring and control enable faster adjustments, minimizing downtime and maximizing output.
Improved Accuracy
Sensing technology ensures that cutting tools operate within precise tolerances, resulting in higher-quality products.
Accurate measurements and real-time feedback help reduce errors and rework, saving time and resources.
Enhanced Safety
Sensors detect potential issues before they become critical, preventing accidents and equipment damage.
Automated systems can shut down or adjust processes in response to sensor data, ensuring a safer working environment.
Cost Savings
Integrating cutting processing and sensing technology reduces material waste, tool wear, and downtime.
Optimized processes and predictive maintenance minimize operating costs and extend equipment life.
Conclusion
Understanding the fundamentals of cutting processing and sensing technology is essential for businesses looking to improve efficiency and automation.
These technologies enhance accuracy, safety, and overall productivity, making them indispensable in modern manufacturing.
By staying informed about the latest advancements and integrating them into their processes, companies can remain competitive and achieve long-term success.
資料ダウンロード
QCD管理受発注クラウド「newji」は、受発注部門で必要なQCD管理全てを備えた、現場特化型兼クラウド型の今世紀最高の受発注管理システムとなります。
ユーザー登録
受発注業務の効率化だけでなく、システムを導入することで、コスト削減や製品・資材のステータス可視化のほか、属人化していた受発注情報の共有化による内部不正防止や統制にも役立ちます。
NEWJI DX
製造業に特化したデジタルトランスフォーメーション(DX)の実現を目指す請負開発型のコンサルティングサービスです。AI、iPaaS、および先端の技術を駆使して、製造プロセスの効率化、業務効率化、チームワーク強化、コスト削減、品質向上を実現します。このサービスは、製造業の課題を深く理解し、それに対する最適なデジタルソリューションを提供することで、企業が持続的な成長とイノベーションを達成できるようサポートします。
製造業ニュース解説
製造業、主に購買・調達部門にお勤めの方々に向けた情報を配信しております。
新任の方やベテランの方、管理職を対象とした幅広いコンテンツをご用意しております。
お問い合わせ
コストダウンが利益に直結する術だと理解していても、なかなか前に進めることができない状況。そんな時は、newjiのコストダウン自動化機能で大きく利益貢献しよう!
(β版非公開)