- お役立ち記事
- Fundamentals of die casting technology and countermeasures against defects
Fundamentals of die casting technology and countermeasures against defects
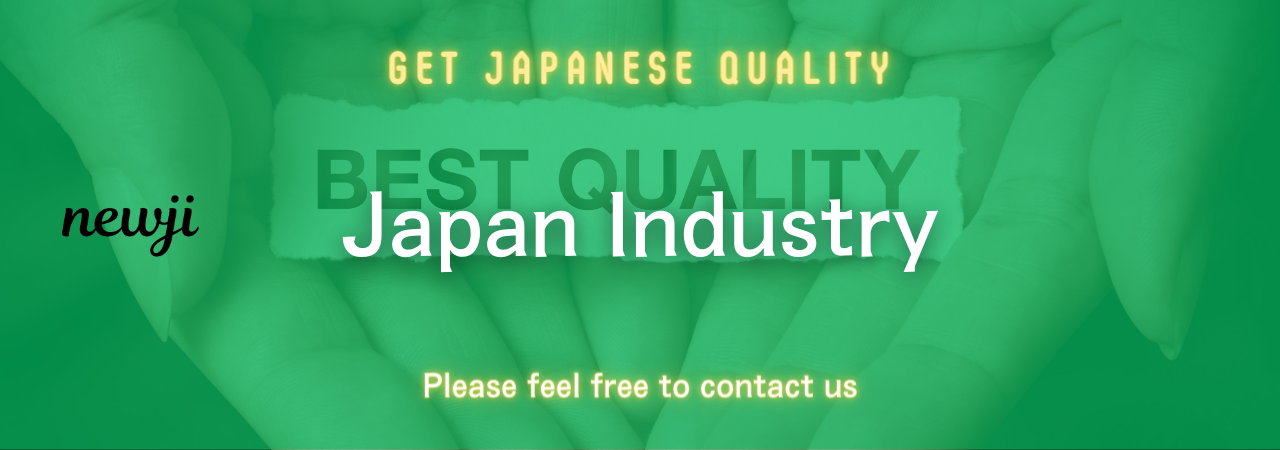
目次
Understanding Die Casting Technology
Die casting is a versatile and reliable manufacturing process used to produce intricately shaped metal parts with high precision and excellent surface finish.
The process involves injecting molten metal into a mold cavity under high pressure, where it solidifies into the desired shape.
This technique is popular in industries such as automotive, aerospace, and consumer electronics due to its ability to produce complex components with minimal waste and superior mechanical properties.
Types of Die Casting
There are primarily two types of die casting processes: hot chamber and cold chamber.
Hot Chamber Die Casting
In hot chamber die casting, the metal chamber is immersed in molten metal.
The process is suitable for metals with low melting points, such as zinc, magnesium, and lead.
Its main advantage is that it allows rapid cycling, making it ideal for high-volume production.
Cold Chamber Die Casting
Cold chamber die casting is used for metals with high melting points, such as aluminum, copper, and brass.
In this process, molten metal is poured into a cold chamber, then injected into the mold.
Though slower than hot chamber die casting, it’s essential for working with metals that would corrode the metal chamber if the components remained in contact.
Materials Used in Die Casting
Common materials used in die casting include zinc, aluminum, magnesium, copper, tin, and lead.
Each material offers unique properties:
– **Zinc** offers strength, high ductility, and easy alloying.
– **Aluminum** is lightweight, robust, and reflects heat well.
– **Magnesium** is the lightest of all structural metals and provides good machinability.
– **Copper** is known for high resistance to corrosion and excellent thermal conductivity.
Die Casting Process Steps
The die casting process can be broken down into several critical steps:
1. Mold Preparation
Before metal injection, the mold is prepared by applying a lubricant to facilitate the easy ejection of the cast part and extend the mold’s life.
This is followed by closing the mold and securing it under hydraulic pressure.
2. Injection
The molten metal is injected into the mold cavity at high pressures.
This rapid process ensures that the metal fills the cavity before it starts to solidify.
3. Cooling
Once injected, the metal is allowed to cool and solidify within the mold.
The cooling time varies based on the metal used and the part’s complexity and size.
4. Ejection
After sufficient cooling, the mold opens, and the solidified part is ejected by pins.
Care is taken to ensure that the cast part does not deform during this stage.
5. Trimming
Trimming removes any excess material or flash that occurs when molten metal leaks into the parting line of the mold.
This process ensures the die cast part meets the required specifications and dimensions.
Common Defects in Die Casting
While die casting is an efficient manufacturing process, it is not without potential defects.
It’s crucial to identify and implement countermeasures to maintain quality and functionality.
Porosity
Porosity, often seen as voids or air bubbles within the cast part, can compromise the part’s strength and integrity.
This defect is usually caused by insufficient metal pressure or trapped air.
Cold Shut
Cold shuts occur when two metal streams within the mold do not fuse properly, resulting in weak sections within the part.
Improper filling and cooling rates usually cause this defect.
Flash
Flash is excess metal that leaks between the mold and the plunger or surrounding parts.
It can be a result of excessive injection pressure or worn-out molds.
Surface Defects
Surface defects, such as rough textures or small imperfections, can occur due to inadequate lubrication, poor mold design, or incorrect temperature settings.
Countermeasures Against Defects
Implementing effective countermeasures can significantly reduce defects in die casting, enhancing the quality and reliability of the final products.
Optimize Mold Design
A well-designed mold ensures proper metal flow and reduces the risk of defects such as cold shuts and porosity.
Engineers should pay attention to gate and runner size and location to ensure optimal metal distribution.
Control Process Parameters
Careful control of process parameters, including temperature, pressure, and cycle time, can minimize defects.
Consistent monitoring allows for quick adjustments to prevent issues during production.
Regular Maintenance
Keeping equipment and molds in top condition reduces the likelihood of defects.
Regular maintenance can identify wear and tear before it leads to issues like flashing.
Use Quality Lubricants
Applying the right type and amount of lubricant to the molds ensures smooth ejection, improves the surface finish, and extends mold life.
Proper lubrication is crucial in avoiding surface defects.
Conclusion
Understanding the fundamentals of die casting technology and addressing its inherent challenges is vital for producing high-quality metal components.
Through a combination of innovative design, precise process control, and routine maintenance, manufacturers can minimize defects and consistently deliver robust and reliable die cast products.
As industries continue to demand more complex parts, improvements in die casting techniques will remain imperative for meeting these evolving needs.
資料ダウンロード
QCD調達購買管理クラウド「newji」は、調達購買部門で必要なQCD管理全てを備えた、現場特化型兼クラウド型の今世紀最高の購買管理システムとなります。
ユーザー登録
調達購買業務の効率化だけでなく、システムを導入することで、コスト削減や製品・資材のステータス可視化のほか、属人化していた購買情報の共有化による内部不正防止や統制にも役立ちます。
NEWJI DX
製造業に特化したデジタルトランスフォーメーション(DX)の実現を目指す請負開発型のコンサルティングサービスです。AI、iPaaS、および先端の技術を駆使して、製造プロセスの効率化、業務効率化、チームワーク強化、コスト削減、品質向上を実現します。このサービスは、製造業の課題を深く理解し、それに対する最適なデジタルソリューションを提供することで、企業が持続的な成長とイノベーションを達成できるようサポートします。
オンライン講座
製造業、主に購買・調達部門にお勤めの方々に向けた情報を配信しております。
新任の方やベテランの方、管理職を対象とした幅広いコンテンツをご用意しております。
お問い合わせ
コストダウンが利益に直結する術だと理解していても、なかなか前に進めることができない状況。そんな時は、newjiのコストダウン自動化機能で大きく利益貢献しよう!
(Β版非公開)