- お役立ち記事
- Fundamentals of die casting technology and key points for effective defect countermeasures
月間76,176名の
製造業ご担当者様が閲覧しています*
*2025年3月31日現在のGoogle Analyticsのデータより
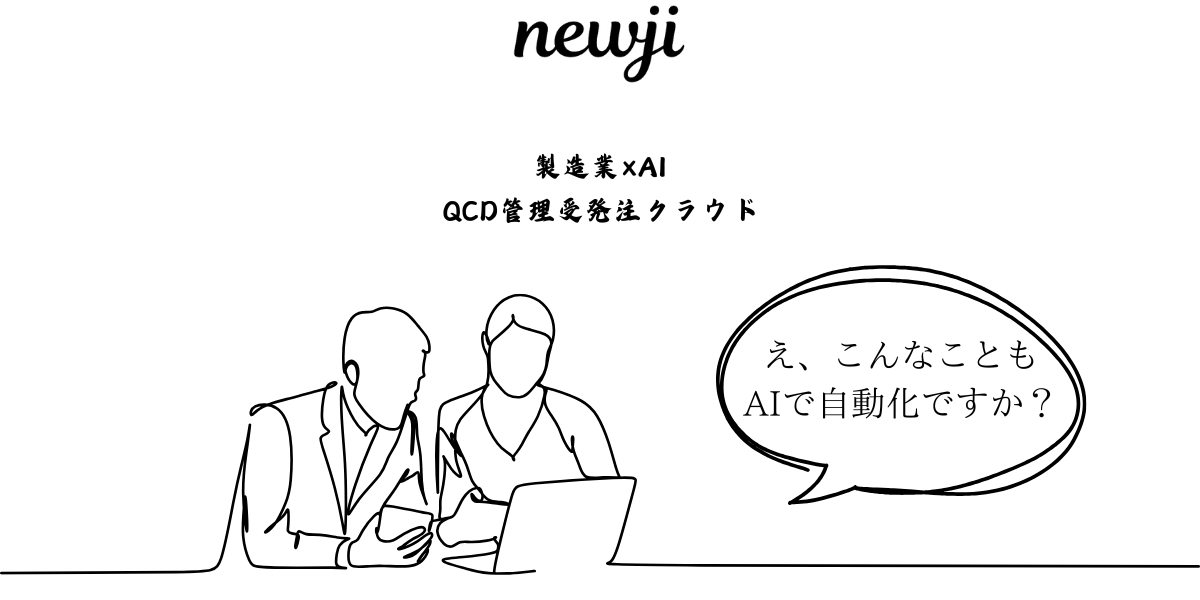
Fundamentals of die casting technology and key points for effective defect countermeasures
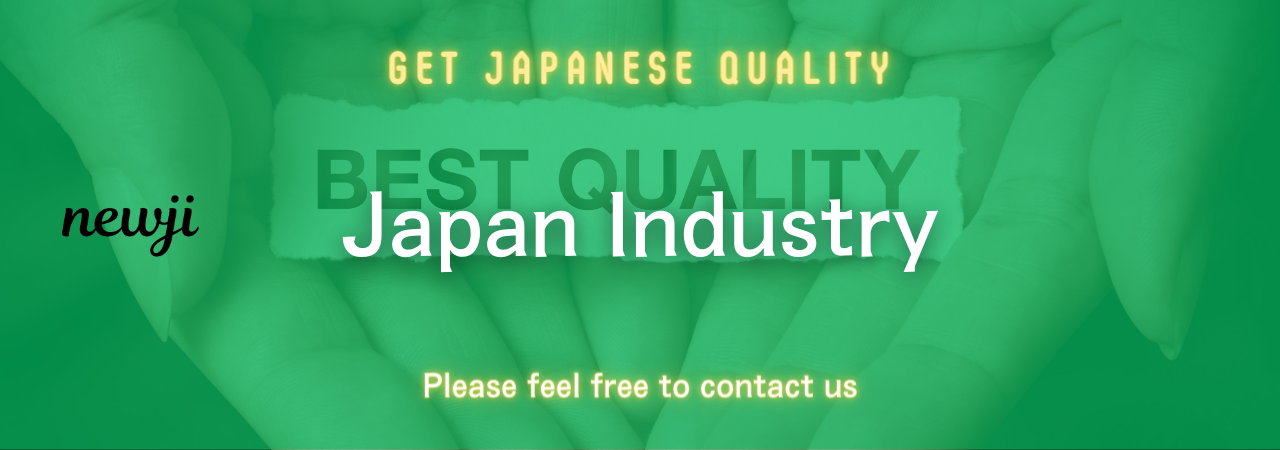
Die casting is a prevalent manufacturing process used to produce metal parts with high precision and smooth surface finishes.
It involves forcing molten metal into a mold cavity under high pressure.
This process is crucial in manufacturing industries, particularly in automotive, aerospace, and electronics, due to its ability to produce complex shapes with tight tolerances and high repeatability.
目次
Understanding Die Casting Technology
Die casting involves several steps, beginning with preparing the mold, also known as a die.
The dies are typically made from hardened steel and consist of two halves: the cover die and the ejector die.
Once the dies are ready, molten metal, usually aluminum, zinc, or magnesium, is injected into the cavity at high speed and pressure.
This rapid injection helps the metal fill the entire cavity before it solidifies, achieving detailed and precise components.
There are two main types of die casting processes: cold-chamber and hot-chamber.
In the cold-chamber process, molten metal is ladled into the injection chamber, and a piston pushes it into the die cavity.
In the hot-chamber process, the injection mechanism itself is immersed in the molten metal, allowing for a more efficient injection cycle.
The choice between these processes depends on the type of metal being used and production requirements.
Materials Used in Die Casting
The three most common metals used in die casting are aluminum, zinc, and magnesium.
Aluminum is favored for its lightweight and excellent corrosion resistance, making it ideal for automotive and aerospace parts.
Zinc, with its low melting point and ability to produce intricate details, is often used for consumer goods and electronic components.
Magnesium is selected for its lightweight characteristics, allowing the production of components that require minimal mass without compromising strength.
Key Steps in the Die Casting Process
The die casting process consists of several critical steps:
Mold Preparation
The first step is mold preparation, which ensures the die is clean and free from defects.
The dies are preheated and lubricated to facilitate metal flow and prevent sticking.
Metal Injection
Molten metal is then injected into the die at high pressure.
The short cycle times, typically ranging from a few milliseconds to seconds, help achieve precise dimensions.
Cooling and Solidification
After injection, the metal cools and solidifies quickly, forming the desired shape.
Rapid cooling helps maintain the integrity of the structure and reduces the risk of defects.
Ejection
Once the metal is solidified, the die halves are opened, and the casting is ejected using ejector pins.
Proper ejection is crucial to maintaining the component’s shape and surface finish.
Trimming and Finishing
Excess material, or flash, is trimmed from the casting, and further finishing processes like machining or painting are applied if necessary.
Common Die Casting Defects
Even with the precision of die casting, defects can occur.
Identifying and mitigating these defects is essential for maintaining product quality.
Porosity
Porosity refers to the presence of air pockets or voids within the casting, which can weaken the part.
This defect can occur during metal injection if air is trapped in the die cavity.
Flash
Flash is excess material that seeps out of the die cavity at parting lines.
This defect typically results from incorrect clamping force or die misalignment.
Cold Shut
Cold shut occurs when two fronts of molten metal do not fuse properly, leading to a line or seam in the casting.
This defect usually arises from low metal temperature or inadequate injection speed.
Misrun
A misrun occurs when molten metal solidifies before filling the entire cavity, leading to incomplete castings.
This can result from low metal temperature or slow injection speed.
Effective Countermeasures for Die Casting Defects
Understanding and implementing effective countermeasures for die casting defects is critical in ensuring high-quality production.
Optimizing Mold Design
Proper mold design is essential in preventing many common defects.
Using computer simulations and flow analysis can help optimize gate and runner systems, leading to improved metal flow and reduced risk of cold shuts and misruns.
Controlling Metal Temperature
Maintaining the correct molten metal temperature is vital.
Too high temperatures can exacerbate porosity, while too low temperatures can lead to cold shuts and misruns.
Adjusting Injection Parameters
Optimizing injection speed and pressure can minimize defects like misruns and cold shuts.
It’s essential to balance these parameters to ensure complete cavity filling without causing excessive flash.
Ensuring Proper Die Maintenance
Regular die maintenance, including cleaning and lubrication, helps prevent defects caused by die wear and tear.
It also ensures consistent production quality and prolongs the die’s lifespan.
Implementing Quality Control Measures
Incorporating robust quality control methods, such as non-destructive testing and inspection, can help detect and address defects before products reach the market.
Timely feedback from quality control allows for process adjustments, preventing defect recurrence.
Die casting technology is integral to modern manufacturing, providing the means to produce complex metal components efficiently and accurately.
Understanding the fundamentals of this technology, its common defects, and effective countermeasures can significantly enhance production quality and efficiency.
By implementing these strategies, manufacturers can minimize defects and achieve superior results, ensuring they meet industry standards and customer expectations.
資料ダウンロード
QCD管理受発注クラウド「newji」は、受発注部門で必要なQCD管理全てを備えた、現場特化型兼クラウド型の今世紀最高の受発注管理システムとなります。
ユーザー登録
受発注業務の効率化だけでなく、システムを導入することで、コスト削減や製品・資材のステータス可視化のほか、属人化していた受発注情報の共有化による内部不正防止や統制にも役立ちます。
NEWJI DX
製造業に特化したデジタルトランスフォーメーション(DX)の実現を目指す請負開発型のコンサルティングサービスです。AI、iPaaS、および先端の技術を駆使して、製造プロセスの効率化、業務効率化、チームワーク強化、コスト削減、品質向上を実現します。このサービスは、製造業の課題を深く理解し、それに対する最適なデジタルソリューションを提供することで、企業が持続的な成長とイノベーションを達成できるようサポートします。
製造業ニュース解説
製造業、主に購買・調達部門にお勤めの方々に向けた情報を配信しております。
新任の方やベテランの方、管理職を対象とした幅広いコンテンツをご用意しております。
お問い合わせ
コストダウンが利益に直結する術だと理解していても、なかなか前に進めることができない状況。そんな時は、newjiのコストダウン自動化機能で大きく利益貢献しよう!
(β版非公開)