- お役立ち記事
- Fundamentals of digital twin technology and application to smart manufacturing
Fundamentals of digital twin technology and application to smart manufacturing
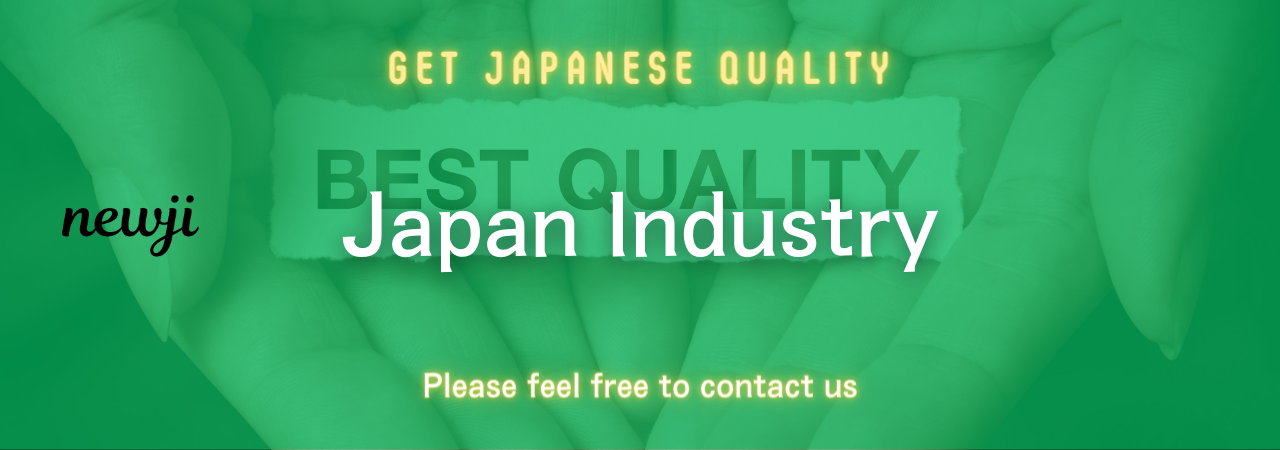
目次
Understanding Digital Twin Technology
Digital twin technology is a concept that is transforming various industries by providing a virtual representation of a physical object or system.
This real-time digital counterpart allows businesses to simulate, analyze, and control their operations more efficiently.
By leveraging digital twin technology, manufacturers can optimize their operations, predict potential failures before they occur, and enhance overall productivity.
This technology serves as a bridge between the physical and digital worlds, enabling manufacturers to create a smart, data-driven environment.
What Is a Digital Twin?
A digital twin is a dynamic software model of a physical object or system that relies on data collected from various sensors.
These sensors gather real-time data to replicate the behavior and characteristics of physical assets in the digital space.
In essence, a digital twin is a virtual mirror of a physical entity, providing insights and information that can be used to improve decision-making and efficiency.
Key Components of Digital Twins
Several components make up a digital twin, working in tandem to create a seamless integration of physical and digital worlds.
1. **Sensors and Data Collection:** One of the most critical aspects of a digital twin is the data it gathers from sensors attached to the physical asset.
2. **Data Processing and Analytics:** Raw data collected from sensors needs to be processed, analyzed, and converted into actionable insights.
3. **Modeling:** This is where the real-time data is used to create a virtual representation of the asset.
4. **Simulation and Visualization:** The digital twin can simulate various scenarios, predict outcomes, and provide visual insight into processes.
5. **Control Systems:** These enable the digital twin to influence the physical object, optimizing processes and improving performance.
Application of Digital Twin in Smart Manufacturing
Digital twin technology is revolutionizing smart manufacturing, paving the way for more efficient, flexible, and intelligent production processes.
It helps manufacturers to remain competitive and meet the changing demands of the market through enhanced productivity, reduced downtime, and efficient resource utilization.
Enhancing Operational Efficiency
Digital twins can greatly enhance operational efficiency by analyzing real-time data to optimize production lines and workflow processes.
Manufacturers can proactively address bottlenecks, identify areas for improvement, and streamline operations to maximize output.
Predictive Maintenance
One of the most impactful uses of digital twins in manufacturing is predictive maintenance.
By continuously monitoring the condition of machinery, digital twins can predict when a piece of equipment is likely to fail, allowing for repairs or replacements before any downtime occurs.
This approach not only increases operational uptime but also extends the lifespan of the equipment, reducing costs associated with unscheduled repairs.
Product Design and Development
Digital twins enable manufacturers to prototype and test new products in a virtual environment before they are physically created.
This makes it possible to identify design flaws early in the development process, saving both time and money.
In addition, by simulating how a product will perform under various conditions, manufacturers can enhance quality and performance before proceeding to mass production.
Supply Chain Optimization
With a digital twin, manufacturers can gain an in-depth understanding of their supply chain, identifying potential delays and inefficiencies.
By visualizing the supply chain from end to end, manufacturers can optimize logistics, reduce lead times, and minimize the risk of disruptions.
This helps maintain a smooth production process and ensures that products are delivered on time to customers.
Challenges in Implementing Digital Twin Technology
While digital twin technology offers significant advantages, its implementation comes with certain challenges that manufacturers must overcome.
Data Management and Integration
Handling vast amounts of data and ensuring seamless integration with existing systems can be daunting.
Manufacturers need the infrastructure and expertise to manage and analyze this data effectively to create and maintain an accurate digital twin.
Cybersecurity Concerns
Since digital twins rely on data from connected devices, they can be vulnerable to cyber threats.
Maintaining data security and protecting intellectual property is crucial, requiring robust cybersecurity measures.
High Initial Costs
The initial investment required to implement digital twin technology can be substantial.
However, manufacturers need to weigh these upfront costs against the long-term benefits of improved efficiency, reduced downtime, and enhanced product quality.
Skill Gaps
There is often a need for skilled professionals who understand both the physical and digital aspects of manufacturing operations.
Training existing staff and hiring new employees with the necessary knowledge is essential to leverage digital twins effectively.
The Future of Digital Twins in Smart Manufacturing
As technology continues to evolve, the potential of digital twins in manufacturing will expand, offering new opportunities for innovation and efficiency.
The integration of artificial intelligence and machine learning will make digital twins even more powerful, enabling smarter decision-making and autonomous operations.
In the future, digital twins could become central to the concept of Industry 4.0, ushering in an era of fully connected, intelligent manufacturing.
As companies continue to explore and adopt digital twin technology, they will unlock new levels of performance and growth, ultimately redefining how industries operate in the digital age.
The journey toward smart manufacturing is just beginning, and digital twins will surely play a pivotal role in shaping the future landscape.
資料ダウンロード
QCD調達購買管理クラウド「newji」は、調達購買部門で必要なQCD管理全てを備えた、現場特化型兼クラウド型の今世紀最高の購買管理システムとなります。
ユーザー登録
調達購買業務の効率化だけでなく、システムを導入することで、コスト削減や製品・資材のステータス可視化のほか、属人化していた購買情報の共有化による内部不正防止や統制にも役立ちます。
NEWJI DX
製造業に特化したデジタルトランスフォーメーション(DX)の実現を目指す請負開発型のコンサルティングサービスです。AI、iPaaS、および先端の技術を駆使して、製造プロセスの効率化、業務効率化、チームワーク強化、コスト削減、品質向上を実現します。このサービスは、製造業の課題を深く理解し、それに対する最適なデジタルソリューションを提供することで、企業が持続的な成長とイノベーションを達成できるようサポートします。
オンライン講座
製造業、主に購買・調達部門にお勤めの方々に向けた情報を配信しております。
新任の方やベテランの方、管理職を対象とした幅広いコンテンツをご用意しております。
お問い合わせ
コストダウンが利益に直結する術だと理解していても、なかなか前に進めることができない状況。そんな時は、newjiのコストダウン自動化機能で大きく利益貢献しよう!
(Β版非公開)