- お役立ち記事
- Fundamentals of dissimilar material joining technology (plastic/rubber/metal) and application to products
月間77,185名の
製造業ご担当者様が閲覧しています*
*2025年2月28日現在のGoogle Analyticsのデータより
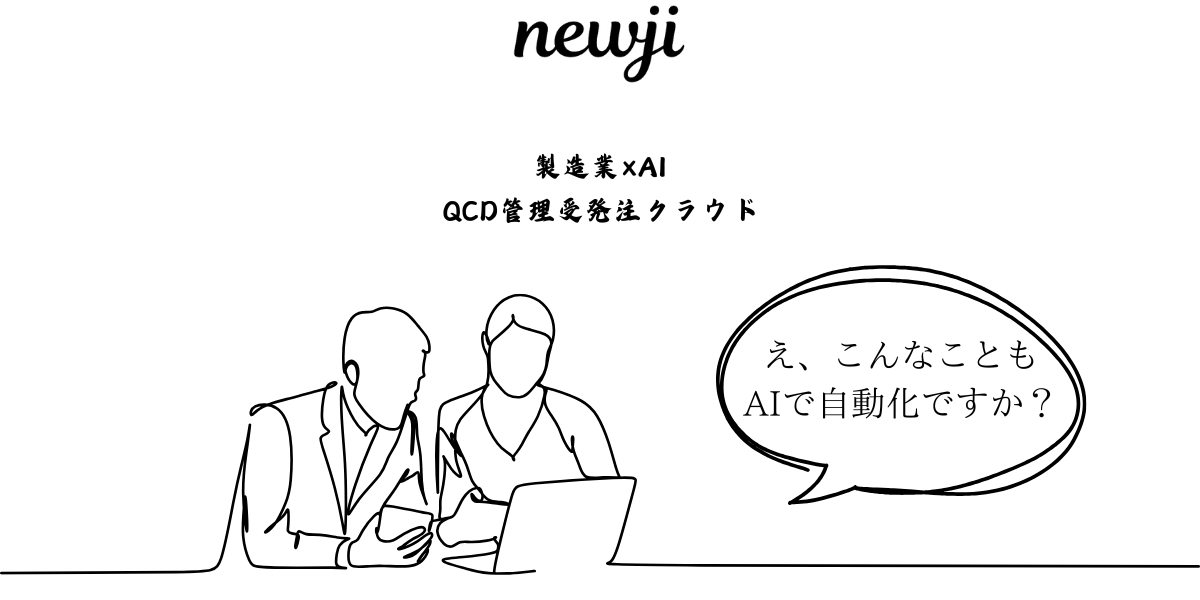
Fundamentals of dissimilar material joining technology (plastic/rubber/metal) and application to products
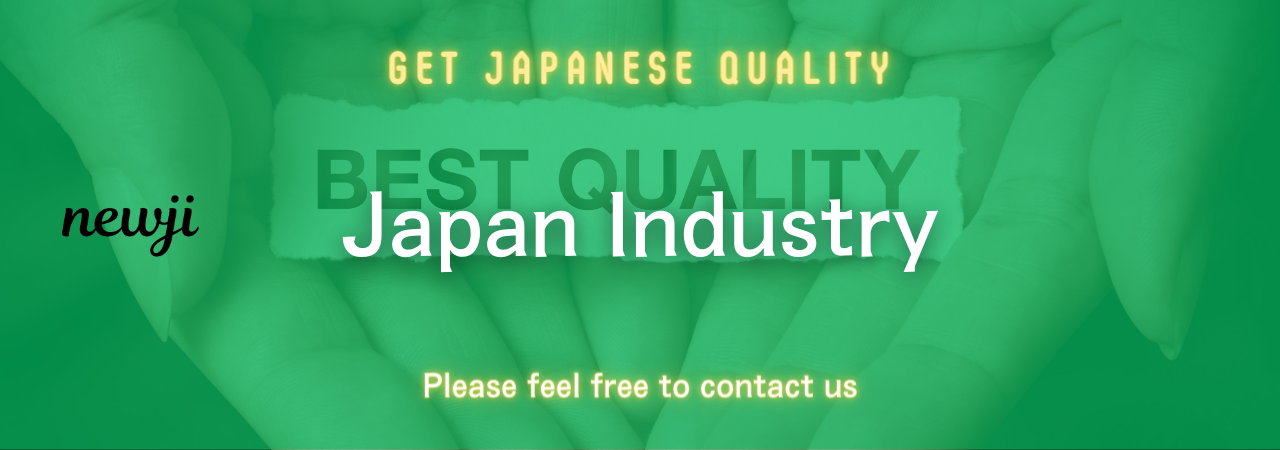
目次
Understanding Dissimilar Material Joining
Dissimilar material joining is an essential aspect of modern manufacturing processes.
This technology involves the combination of different materials — such as plastics, rubber, and metals — to create a single, cohesive product.
The need for strong, lightweight, and durable goods in various industries has driven the demand for innovative joining solutions.
In this article, we will explore the fundamentals of dissimilar material joining technology, focusing on its applications and benefits within the manufacturing sector.
The Importance of Dissimilar Material Joining
The integration of different materials can result in products that boast enhanced properties.
For example, metals offer superior strength, while plastics and rubber can be more flexible and lighter in weight.
By joining these materials, manufacturers can develop products that exploit the best qualities of each component.
This approach is particularly beneficial in industries like automotive, aerospace, and electronics, where performance and efficiency are paramount.
Challenges in Joining Dissimilar Materials
Combining different materials presents several challenges owing to their inherent differences.
Issues like thermal expansion, chemical compatibility, and mechanical properties need consideration.
The varying melting points, for instance, can make creating a strong bond difficult.
Furthermore, the potential for corrosion and lack of adhesion between metal and non-metal surfaces adds another layer of complexity.
Key Techniques for Successful Joining
A variety of techniques are employed to join dissimilar materials, each with its advantages and challenges.
Selecting the appropriate method depends on the specific materials involved and the intended use of the finished product.
Adhesive Bonding
Adhesive bonding is a popular technique due to its versatility.
It involves using a specialized adhesive to bond materials together.
This method is effective in joining metals to non-metals as it can accommodate different thermal expansions and provide insulation against corrosion.
However, choosing the right adhesive is crucial to ensure the bond’s strength and longevity.
Mechanical Fastening
Mechanical fastening involves using fasteners like screws, bolts, and rivets to join materials.
This method is practical for joining materials that are challenging to bond chemically.
It allows for easy disassembly and repositioning, which can be beneficial in applications requiring maintenance.
However, mechanical fastening may add weight and could lead to stress concentrations, potentially weakening the materials.
Welding and Brazing
Welding and brazing are traditional methods predominantly used for metal-to-metal joining.
However, advancements in technology have allowed these techniques to be adapted for dissimilar materials.
Laser welding, for example, can be effective for joining metals to plastics by focusing energy precisely to avoid damaging the polymer.
Brazing involves melting a filler metal to join different materials, suitable for cases where a strong bond is needed without melting the base materials.
Ultrasonic Welding
Ultrasonic welding is increasingly popular for joining plastics and metals.
It uses high-frequency ultrasonic vibrations to generate heat at the interface, allowing materials to bond without additional adhesives or fasteners.
This method is energy-efficient and can produce strong, consistent bonds, making it ideal for the electronics and automotive industries.
Applications in Various Industries
The ability to join dissimilar materials opens up a world of possibilities across multiple industries.
Automotive Industry
In the automotive sector, manufacturers strive to reduce vehicle weight to improve fuel efficiency while ensuring safety and performance.
Dissimilar material joining allows for lighter vehicle components without compromising strength.
Plastics and metals are commonly joined to create parts like dashboards, bumpers, and structural components.
Aerospace Industry
Aerospace engineers are continually seeking ways to optimize aircraft performance.
The use of lightweight materials such as titanium with enhanced composites is essential to reduce fuel consumption and increase payload capacity.
Dissimilar material joining aids in producing components that can withstand the harsh conditions of aerospace applications while maintaining structural integrity.
Electronics Industry
The miniaturization of electronic devices demands materials that offer superior thermal management and electrical insulation.
Joining technologies enable manufacturers to combine metals for conducting electricity with polymers for insulation, ensuring devices perform at optimal levels without overheating.
Future Prospects and Innovations
As industries demand even more sophisticated materials and components, the technology and techniques for dissimilar material joining will continue to evolve.
Nanotechnology Integration
The integration of nanotechnology into joining techniques holds great promise.
Nanoparticles could be used to create stronger, lighter adhesives or act as fillers in welding processes, enhancing the performance and longevity of the joined materials.
Sustainability and Environmental Impact
Developments in eco-friendly adhesives and solvents are on the rise, driven by the need for sustainable manufacturing processes.
Improving the recyclability of mixed-material products is a primary focus, as industries aim to reduce waste and environmental impact.
In conclusion, the fundamentals of dissimilar material joining technology are pivotal for creating innovative, efficient, and durable products in today’s competitive market.
With ongoing advancements and the potential for future innovations, the applications for this technology are limitless, offering opportunities for growth and improvement across various sectors.
資料ダウンロード
QCD管理受発注クラウド「newji」は、受発注部門で必要なQCD管理全てを備えた、現場特化型兼クラウド型の今世紀最高の受発注管理システムとなります。
ユーザー登録
受発注業務の効率化だけでなく、システムを導入することで、コスト削減や製品・資材のステータス可視化のほか、属人化していた受発注情報の共有化による内部不正防止や統制にも役立ちます。
NEWJI DX
製造業に特化したデジタルトランスフォーメーション(DX)の実現を目指す請負開発型のコンサルティングサービスです。AI、iPaaS、および先端の技術を駆使して、製造プロセスの効率化、業務効率化、チームワーク強化、コスト削減、品質向上を実現します。このサービスは、製造業の課題を深く理解し、それに対する最適なデジタルソリューションを提供することで、企業が持続的な成長とイノベーションを達成できるようサポートします。
製造業ニュース解説
製造業、主に購買・調達部門にお勤めの方々に向けた情報を配信しております。
新任の方やベテランの方、管理職を対象とした幅広いコンテンツをご用意しております。
お問い合わせ
コストダウンが利益に直結する術だと理解していても、なかなか前に進めることができない状況。そんな時は、newjiのコストダウン自動化機能で大きく利益貢献しよう!
(β版非公開)