- お役立ち記事
- Fundamentals of elastic mechanics and applications to CAE
月間77,185名の
製造業ご担当者様が閲覧しています*
*2025年2月28日現在のGoogle Analyticsのデータより
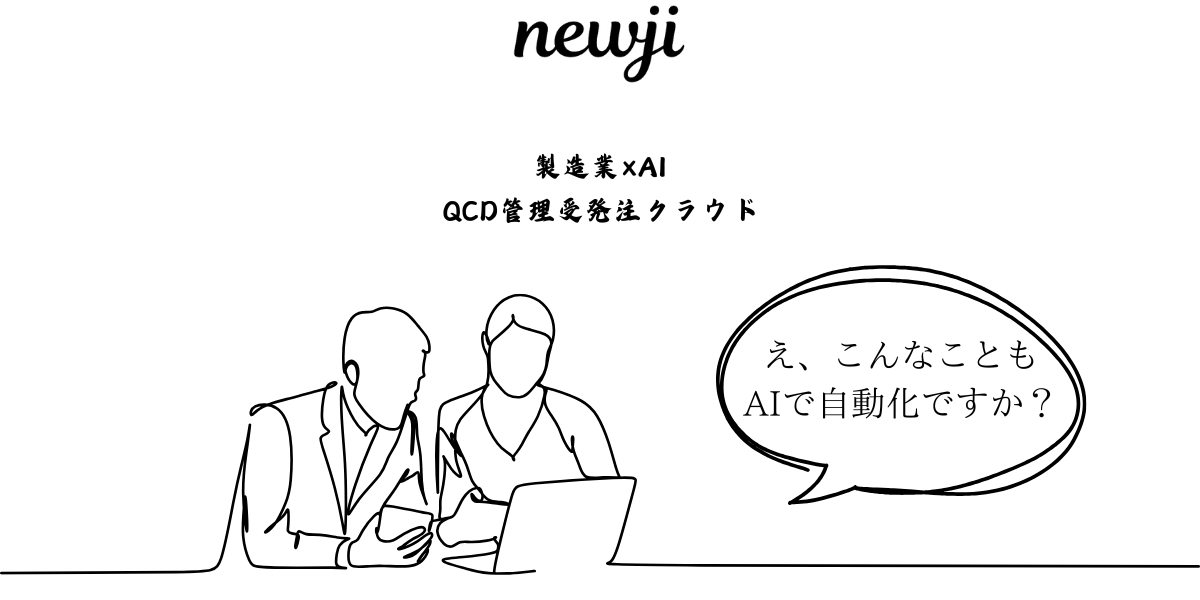
Fundamentals of elastic mechanics and applications to CAE
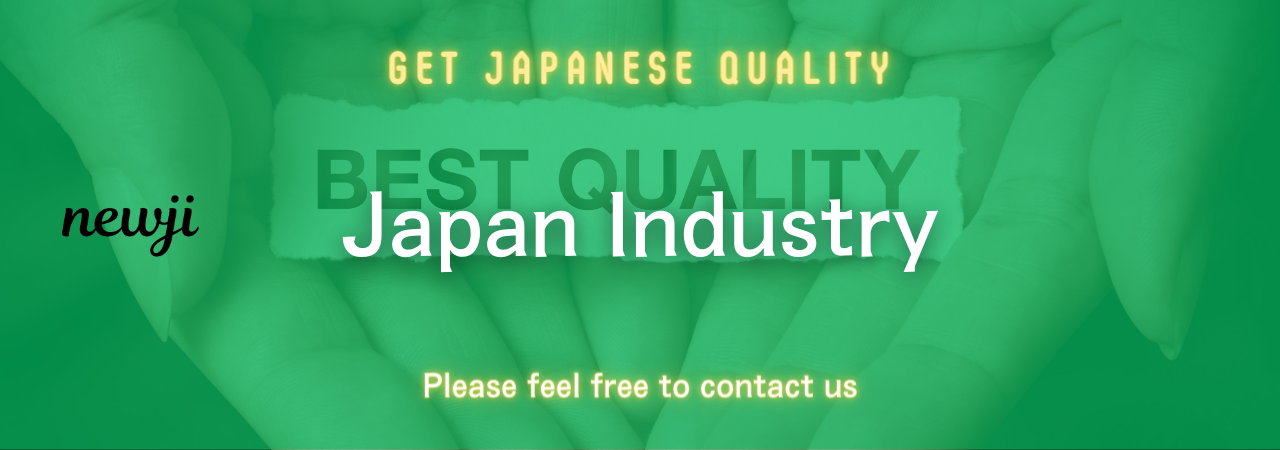
目次
Understanding Elastic Mechanics
Elastic mechanics is a fascinating field that focuses on the behavior of solid materials that deform and return to their original shape when subjected to external forces.
Think of a rubber band – when you stretch it, it expands; once you let go, it returns to its original form.
This simple concept of material elasticity underlies numerous applications in engineering and design.
To grasp the fundamentals of elastic mechanics, it’s crucial to understand the two primary properties: stress and strain.
Stress refers to the force applied to an object, usually measured in units such as Pascals (Pa) in the metric system.
On the other hand, strain is a measure of how much an object deforms in response to that stress.
It is expressed as a dimensionless ratio since it compares the change in dimensions to the original size.
Stress-Strain Relationship
A key concept in elastic mechanics is the stress-strain relationship, often represented by Hooke’s Law in its simplest form.
Hooke’s Law states that, within the elastic limit, the stress is directly proportional to the strain.
This relationship is visualized through a stress-strain curve, a fundamental tool for understanding material properties.
Materials exhibit different stress-strain curves, reflecting their unique mechanical characteristics.
For example, metals have a linear portion where they behave elastically, followed by a yield point where permanent deformation occurs.
On the other hand, materials like rubber have a non-linear stress-strain relationship, showing significant elastic behavior over a broad range.
Types of Elasticity
Elasticity is not uniform across all materials, and understanding different types helps in various applications:
– **Linear Elasticity**: This type is observed in materials where the stress-strain relationship is linear.
Materials like metals often exhibit linear elasticity under moderate stress, making them predictable and useful in engineering calculations.
– **Non-linear Elasticity**: Some materials do not have a linear stress-strain relationship, such as rubber.
These materials show more complex behaviors and require advanced mathematical models for analysis.
– **Anisotropic Elasticity**: In materials exhibiting different properties in different directions, anisotropic elasticity is observed.
Examples include composite materials and wood, where the directional differences significantly impact mechanical performance.
– **Viscoelasticity**: Certain materials have both elastic and viscous responses to stress, known as viscoelastic behavior.
This type is typical in polymers and biological tissues, where time-dependent deformation occurs.
Applications in Computer-Aided Engineering (CAE)
The principles of elastic mechanics are pivotal in computer-aided engineering (CAE), empowering engineers to design and analyze complex systems effectively.
CAE uses simulations to predict how products will behave under various conditions, and elasticity plays a critical role in these analyses.
Finite Element Analysis (FEA)
One of the most popular methods in CAE, Finite Element Analysis (FEA), relies heavily on elastic mechanics.
FEA divides a complex structure into smaller elements, allowing engineers to analyze stress, strain, and displacement in each part.
By applying elasticity principles, FEA predicts how materials will react to forces, enabling optimized designs that withstand real-world conditions.
Material Selection and Optimization
Engineers employ elastic mechanics in CAE to choose materials best suited for specific applications.
By understanding the elastic properties of various materials, they can select those that will provide the best performance while minimizing weight and cost.
This process is crucial in industries like aerospace, automotive, and construction, where material efficiency is paramount.
Design and Prototyping
Elastic mechanics allows engineers to create more accurate prototypes and innovative designs.
By simulating how different stresses and strains affect materials, designers can refine their products before physical testing, saving time and resources.
This capability is particularly beneficial in developing advanced technologies like wearable devices and flexible electronics.
Structural Analysis
In infrastructure and civil engineering, elastic mechanics enables thorough structural analysis.
Engineers can assess bridges, buildings, and other structures’ stability and integrity, ensuring safety and reliability.
By understanding how materials will behave under load, potential problems can be identified and rectified before they arise in reality.
The Future of Elastic Mechanics in CAE
As technology advances, the role of elastic mechanics in CAE is becoming more sophisticated.
With the integration of artificial intelligence and machine learning, simulations can become more predictive and dynamic, enhancing design capabilities.
These innovations will allow for more accurate predictions of material behavior and facilitate the development of advanced materials with tailor-made properties.
Sustainability and Efficiency
The improved understanding of elastic mechanics contributes to creating more sustainable and efficient products.
Engineers can design structures and devices that use fewer resources and have longer lifespans by optimizing material use.
This trend is essential in addressing global challenges, such as reducing carbon footprints and conserving natural resources.
Interdisciplinary Collaboration
Elastic mechanics is increasingly finding applications beyond traditional engineering, such as in biomedical fields where understanding the mechanical properties of biological tissues is crucial.
Collaborative efforts between engineers, material scientists, and biologists are leading to breakthroughs in medical devices and therapies.
In summary, grasping the fundamentals of elastic mechanics and its applications in CAE is essential for engineers and designers.
By understanding how materials respond to forces, innovations can be pursued across various industries, leading to more efficient, safe, and sustainable products and structures.
As CAE technology evolves, so too will the opportunities to push the boundaries of what is possible, driven by the principles of elasticity.
資料ダウンロード
QCD管理受発注クラウド「newji」は、受発注部門で必要なQCD管理全てを備えた、現場特化型兼クラウド型の今世紀最高の受発注管理システムとなります。
ユーザー登録
受発注業務の効率化だけでなく、システムを導入することで、コスト削減や製品・資材のステータス可視化のほか、属人化していた受発注情報の共有化による内部不正防止や統制にも役立ちます。
NEWJI DX
製造業に特化したデジタルトランスフォーメーション(DX)の実現を目指す請負開発型のコンサルティングサービスです。AI、iPaaS、および先端の技術を駆使して、製造プロセスの効率化、業務効率化、チームワーク強化、コスト削減、品質向上を実現します。このサービスは、製造業の課題を深く理解し、それに対する最適なデジタルソリューションを提供することで、企業が持続的な成長とイノベーションを達成できるようサポートします。
製造業ニュース解説
製造業、主に購買・調達部門にお勤めの方々に向けた情報を配信しております。
新任の方やベテランの方、管理職を対象とした幅広いコンテンツをご用意しております。
お問い合わせ
コストダウンが利益に直結する術だと理解していても、なかなか前に進めることができない状況。そんな時は、newjiのコストダウン自動化機能で大きく利益貢献しよう!
(β版非公開)