- お役立ち記事
- Fundamentals of element stiffness equations
月間76,176名の
製造業ご担当者様が閲覧しています*
*2025年3月31日現在のGoogle Analyticsのデータより
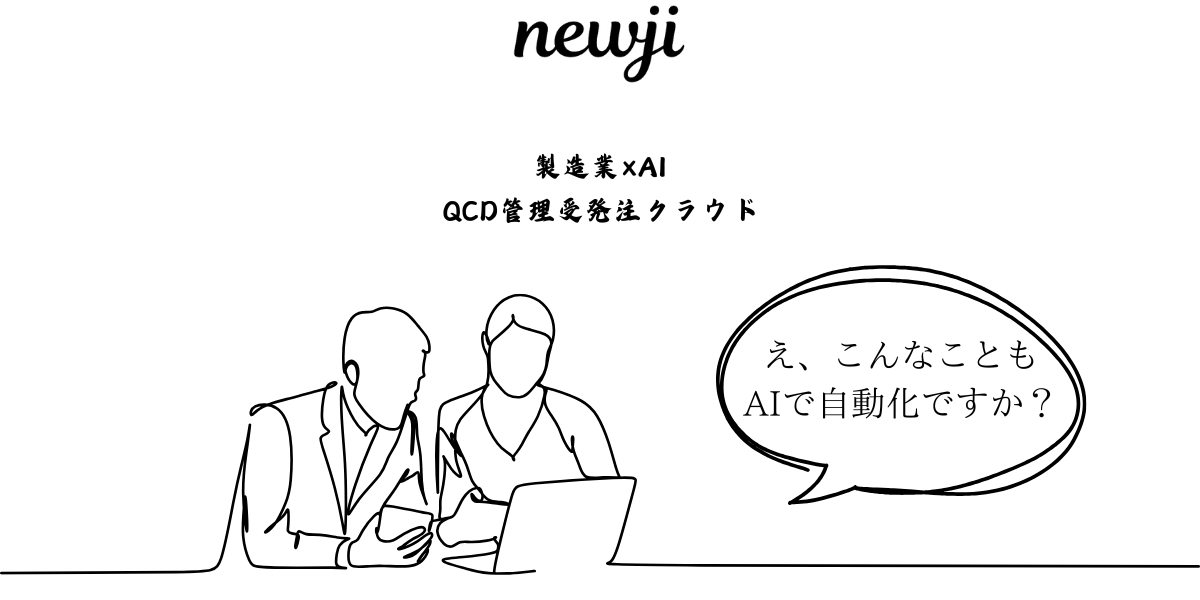
Fundamentals of element stiffness equations
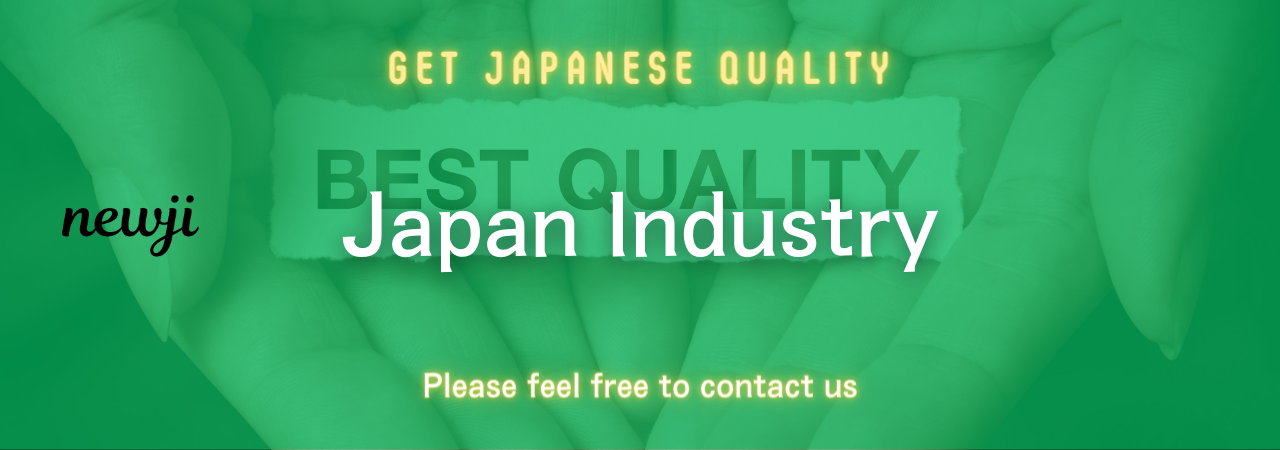
目次
Understanding Element Stiffness
Element stiffness is a fundamental concept in engineering and physics, particularly when it comes to the design and analysis of structures.
Stiffness refers to the resistance of an element to deformation under an applied force.
The element stiffness equation is a mathematical representation that helps engineers determine how different materials and shapes will behave under various load conditions.
It’s essential for designing safe and efficient structures, from buildings to bridges and even vehicles.
To understand this concept, it’s crucial to break it down into its components and explore how these elements interact with each other.
By doing so, you can gain a clearer understanding of how structures are designed to withstand different forces and moments.
The Importance of Element Stiffness
Element stiffness plays a crucial role in the structural integrity and performance of various constructions.
When engineers design a structure, they need to ensure that it can withstand the forces it will encounter throughout its life.
These forces can include anything from wind and seismic activity to the weight of the structure itself and the loads it will carry.
By calculating the stiffness of different elements within a structure, engineers can predict how these elements will perform under various conditions.
This allows them to make informed decisions about the materials to use and the overall design of the structure.
Applications of Element Stiffness
Element stiffness is used in numerous fields of engineering and physics.
In civil engineering, it helps in designing buildings, bridges, and other structures to ensure they can withstand environmental forces and loads.
In mechanical engineering, it’s crucial for designing mechanical components and systems that need to perform reliably under load.
Even in aerospace engineering, stiffness calculations are vital for ensuring the structural integrity of aircraft and spacecraft components.
Components of Element Stiffness
To understand element stiffness fully, it’s essential to break it down into its fundamental components.
These include the material properties, the geometry of the element, and the boundary conditions.
Material Properties
The properties of the material used in an element significantly affect its stiffness.
Young’s modulus, a measure of a material’s ability to resist deformation under stress, is a primary factor in stiffness calculations.
Materials with a high Young’s modulus, such as steel, are typically stiffer than those with a low modulus, like rubber.
Geometry of the Element
The shape and size of an element also play a significant role in determining its stiffness.
For example, a thin beam will generally be less stiff than a thicker one.
Similarly, the cross-sectional area and moment of inertia of a beam can greatly influence its stiffness.
Engineers often optimize the geometry of an element to achieve the desired level of stiffness while minimizing material use and weight.
Boundary Conditions
Boundary conditions refer to how an element is supported or constrained at its ends or surfaces.
These conditions can significantly impact the stiffness of an element.
For instance, a beam that is fixed at both ends will be stiffer than one that is simply supported and free to rotate at its ends.
Different boundary conditions lead to different stiffness characteristics, which are crucial for accurate structural analysis.
Calculating Element Stiffness
Element stiffness is calculated using a set of mathematical equations that consider the material properties, geometry, and boundary conditions.
These equations form the basis of what’s known as the “stiffness matrix,” a tool used extensively in finite element analysis (FEA).
The Stiffness Matrix
The stiffness matrix is a mathematical representation of the relationship between the forces applied to an element and the resulting displacements.
Each entry in this matrix corresponds to how much force is required to produce a unit displacement in a particular direction.
In finite element analysis, the overall stiffness of a structure is determined by assembling the stiffness matrices of all the individual elements.
This comprehensive matrix allows engineers to simulate how the structure will respond to various loads and conditions.
Finite Element Analysis
Finite element analysis is a computational method used to analyze the mechanical behavior of complex structures.
By breaking down a large structure into smaller, more manageable parts, or elements, engineers can apply the element stiffness equations to each part.
This approach provides a detailed understanding of how the entire structure will behave, ensuring that all elements work together effectively to withstand the applied loads.
Ensuring Safety and Performance
Understanding and applying element stiffness equations is critical for ensuring both the safety and performance of engineered structures.
By accurately predicting how materials and shapes will behave under different conditions, engineers can design structures that are not only safe but also efficient and cost-effective.
Optimizing Structural Design
The insights gained from element stiffness calculations allow for optimizing the design of structures.
This means that engineers can use fewer materials while ensuring that the structure remains strong enough to support the required loads.
In turn, this leads to cost savings and a reduction in the environmental impact of construction projects.
Enhancing Reliability
When structures are designed with a clear understanding of their stiffness characteristics, they are more likely to perform reliably over their lifespan.
This reliability is crucial in mitigating risks associated with structural failures, thereby safeguarding human lives and investments.
Conclusion
Element stiffness is a fundamental aspect of engineering and plays an integral role in the design and analysis of structures.
By understanding the material properties, geometry, and boundary conditions, engineers can accurately predict how structures will react to various forces.
This enables them to design safe, efficient, and reliable structures that meet the demands of modern life.
Understanding element stiffness not only aids in creating robust designs but also contributes to innovation in engineering solutions, ensuring that constructions can endure and perform as intended under a wide range of conditions.
資料ダウンロード
QCD管理受発注クラウド「newji」は、受発注部門で必要なQCD管理全てを備えた、現場特化型兼クラウド型の今世紀最高の受発注管理システムとなります。
ユーザー登録
受発注業務の効率化だけでなく、システムを導入することで、コスト削減や製品・資材のステータス可視化のほか、属人化していた受発注情報の共有化による内部不正防止や統制にも役立ちます。
NEWJI DX
製造業に特化したデジタルトランスフォーメーション(DX)の実現を目指す請負開発型のコンサルティングサービスです。AI、iPaaS、および先端の技術を駆使して、製造プロセスの効率化、業務効率化、チームワーク強化、コスト削減、品質向上を実現します。このサービスは、製造業の課題を深く理解し、それに対する最適なデジタルソリューションを提供することで、企業が持続的な成長とイノベーションを達成できるようサポートします。
製造業ニュース解説
製造業、主に購買・調達部門にお勤めの方々に向けた情報を配信しております。
新任の方やベテランの方、管理職を対象とした幅広いコンテンツをご用意しております。
お問い合わせ
コストダウンが利益に直結する術だと理解していても、なかなか前に進めることができない状況。そんな時は、newjiのコストダウン自動化機能で大きく利益貢献しよう!
(β版非公開)