- お役立ち記事
- Fundamentals of equipment management/equipment diagnosis technology, practical know-how of various diagnostic methods, and key points for utilizing predictive maintenance IoT systems
Fundamentals of equipment management/equipment diagnosis technology, practical know-how of various diagnostic methods, and key points for utilizing predictive maintenance IoT systems
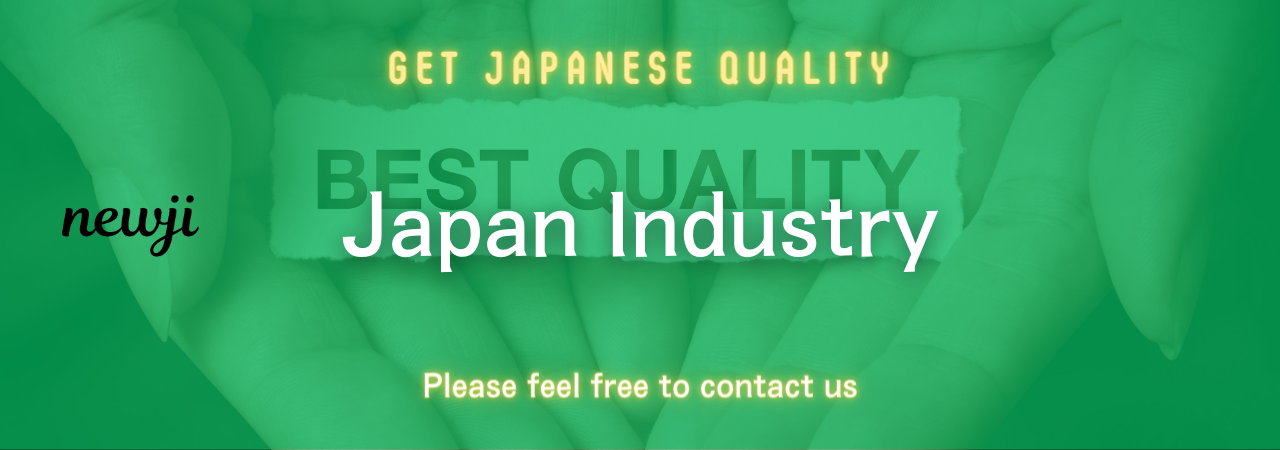
目次
Understanding Equipment Management and Diagnostic Technology
Equipment management is a crucial aspect of any industrial operation, ensuring that machinery and tools are functioning optimally.
At the heart of equipment management lies equipment diagnostic technology, which plays a vital role in detecting issues before they lead to severe failures.
Equipment diagnosis involves various methods to assess the condition of machinery and predict potential breakdowns.
By employing these diagnostic techniques, businesses can enhance operational efficiency, reduce downtime, and extend the lifespan of their equipment.
Learning the fundamentals of equipment management and diagnosis technology is essential for any maintenance team aiming to keep operations smooth and cost-effective.
Importance of Equipment Management
Effective equipment management is vital for maintaining productivity in industrial settings.
Proper management involves regular maintenance checks, careful monitoring of equipment performance, and immediate addressing of any arising issues.
This proactive approach minimizes disruption, maximizes uptime, and ensures safety in the workplace.
Moreover, well-managed equipment is more energy-efficient, which translates into cost savings.
It also leads to fewer unexpected breakdowns, reducing the need for expensive emergency repairs.
Diagnostic Methods for Equipment Maintenance
Understanding diagnostic methods is at the core of effective equipment maintenance.
There are several techniques used to assess the condition of machinery:
1. Vibration Analysis
Vibration analysis is a widely used diagnostic method that involves measuring the vibrations of equipment.
Changes in vibration patterns can indicate wear, imbalance, or misalignment in machinery components.
By identifying these issues early, maintenance teams can address them before they escalate into more significant problems.
2. Infrared Thermography
This method uses infrared cameras to detect heat variations in equipment components.
Excessive heat in machinery can be a sign of friction, electrical faults, or other underlying issues.
Infrared thermography allows for non-contact assessment, making it safer and efficient in diagnosing problems.
3. Oil Analysis
Oil analysis is a technique that involves examining used lubricating oil to identify contamination, wear particles, and progressive wear.
This method provides insights into the internal condition of machinery components, allowing for preventive maintenance actions.
4. Ultrasonic Analysis
Ultrasonic analysis involves using high-frequency sound waves to detect changes in equipment operation.
It is particularly useful for identifying air leaks, electrical discharges, and lubrication issues.
Ultrasonic sensors help pinpoint problem areas that might be missed during a visual inspection.
Practical Know-How for Equipment Diagnostics
Implementing these diagnostic methods requires practical know-how and understanding of the equipment in question.
Here are some key points to consider:
Regular Training and Skill Development
Ensuring that maintenance personnel are well-trained in diagnostic technologies is essential.
Regular workshops and courses help keep teams updated on the latest techniques and tools available in the industry.
Integration of Technology
Incorporating modern diagnostic tools like IoT systems can significantly enhance equipment monitoring and diagnostics.
These systems provide real-time data collection and analysis, offering predictive insights into equipment health.
Documentation and Record Keeping
Maintaining accurate records of diagnostic tests and findings is crucial for tracking the health of your equipment over time.
These records help in predicting failures and planning maintenance activities.
Leveraging Predictive Maintenance with IoT Systems
Predictive maintenance driven by IoT systems has transformed the landscape of equipment management.
These systems use sensors and data analytics to predict equipment failures before they occur, allowing for timely interventions.
Benefits of Predictive Maintenance
Predictive maintenance reduces downtime by scheduling maintenance activities based on actual equipment conditions rather than fixed intervals.
This approach ensures that machinery is serviced only when necessary, extending its lifespan and saving costs related to unnecessary maintenance.
Implementing IoT Systems
For successful predictive maintenance, integrating IoT sensors with your equipment is crucial.
These sensors collect data on variables such as temperature, vibration, and power usage.
Integrating this data into a centralized management system allows for comprehensive monitoring and analysis.
Data Analysis and Action
The data collected from IoT devices need to be analyzed to provide actionable insights.
Advanced analytics software can process this data, alerting maintenance teams to potential issues and scheduling necessary actions.
Conclusion
Understanding the fundamentals of equipment management and diagnostic technology is essential for efficient operation and maintenance.
Employing various diagnostic methods allows businesses to detect potential failures early, minimizing downtime and reducing costs.
With the advent of IoT-driven predictive maintenance, businesses are empowered to monitor equipment conditions in real-time, ensuring timely and effective maintenance.
Integrating these technologies into routine practice not only boosts productivity but also enhances the longevity and performance of industrial equipment.
By focusing on regular skill development, technology integration, and careful record-keeping, maintenance teams can maximize the benefits of modern diagnostic technologies and predictive maintenance systems.
資料ダウンロード
QCD調達購買管理クラウド「newji」は、調達購買部門で必要なQCD管理全てを備えた、現場特化型兼クラウド型の今世紀最高の購買管理システムとなります。
ユーザー登録
調達購買業務の効率化だけでなく、システムを導入することで、コスト削減や製品・資材のステータス可視化のほか、属人化していた購買情報の共有化による内部不正防止や統制にも役立ちます。
NEWJI DX
製造業に特化したデジタルトランスフォーメーション(DX)の実現を目指す請負開発型のコンサルティングサービスです。AI、iPaaS、および先端の技術を駆使して、製造プロセスの効率化、業務効率化、チームワーク強化、コスト削減、品質向上を実現します。このサービスは、製造業の課題を深く理解し、それに対する最適なデジタルソリューションを提供することで、企業が持続的な成長とイノベーションを達成できるようサポートします。
オンライン講座
製造業、主に購買・調達部門にお勤めの方々に向けた情報を配信しております。
新任の方やベテランの方、管理職を対象とした幅広いコンテンツをご用意しております。
お問い合わせ
コストダウンが利益に直結する術だと理解していても、なかなか前に進めることができない状況。そんな時は、newjiのコストダウン自動化機能で大きく利益貢献しよう!
(Β版非公開)