- お役立ち記事
- Fundamentals of factory layout design and improvements to improve productivity and their key points
月間76,176名の
製造業ご担当者様が閲覧しています*
*2025年3月31日現在のGoogle Analyticsのデータより
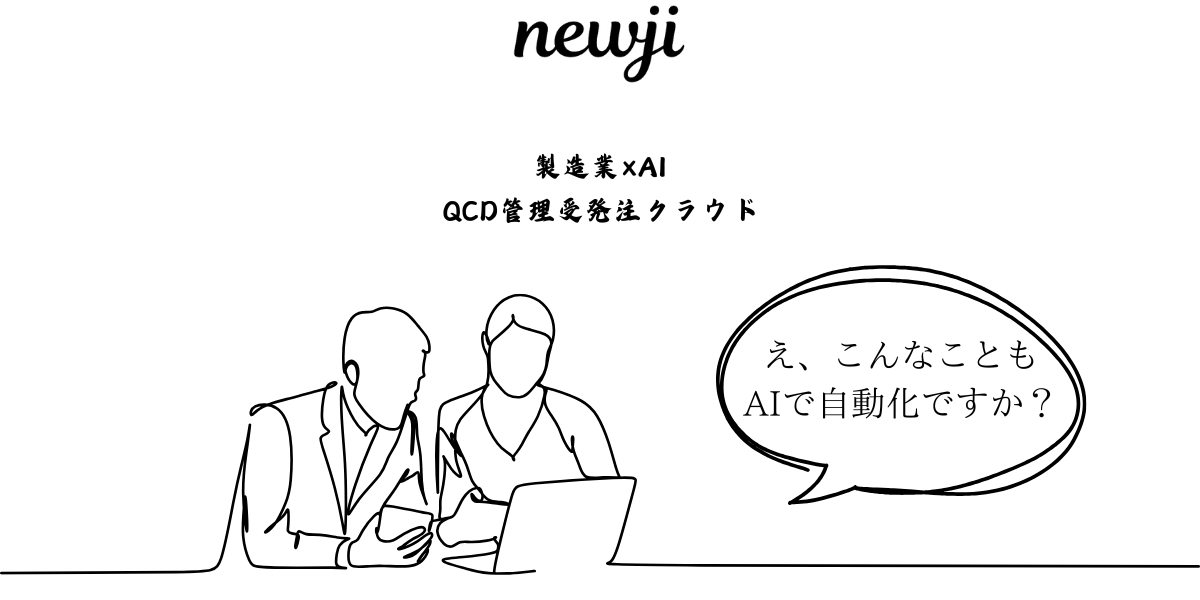
Fundamentals of factory layout design and improvements to improve productivity and their key points
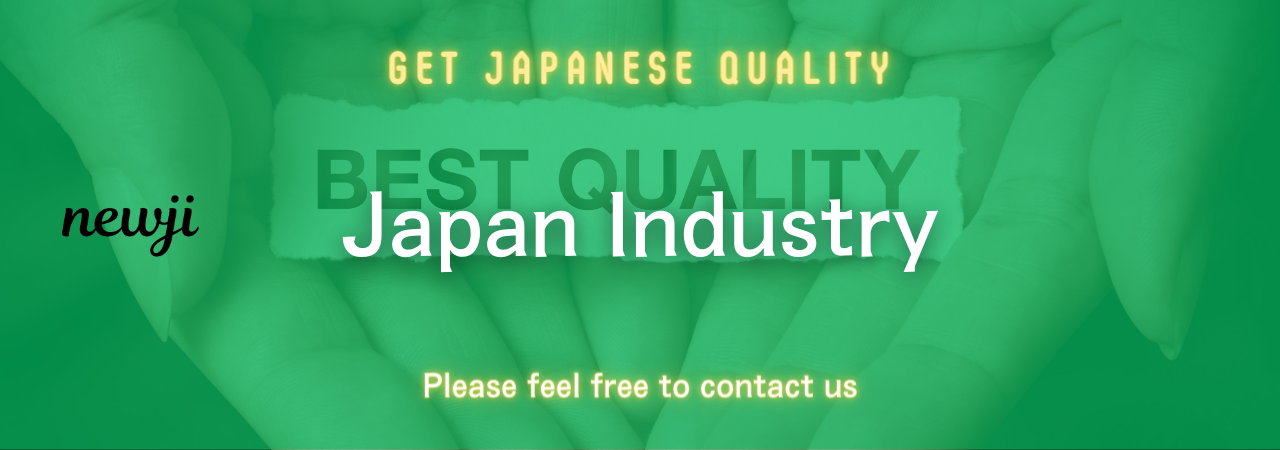
目次
Understanding Factory Layout Design
Factory layout design is a critical aspect of manufacturing and production processes.
It involves arranging physical equipment, workstations, and storage areas within a factory to enhance efficiency and productivity.
An effective layout can minimize production time, reduce costs, and improve product quality.
There are various types of factory layouts, including product layouts, process layouts, and fixed-position layouts.
A product layout is ideal for mass production and involves setting up machines in a sequential order.
Process layouts, on the other hand, are organized based on similar processes or functions.
A fixed-position layout is used when the product is too large or heavy to move and remains stationary throughout the production process.
The Importance of a Well-Designed Layout
A well-designed factory layout is pivotal for several reasons.
Firstly, it reduces material handling costs, as materials move seamlessly between processes.
Additionally, it enhances workflow, ensuring that production processes are smooth and uninterrupted.
A proper layout also reduces the time workers spend moving between stations, boosting their efficiency.
Safety is another critical factor; a good layout minimizes risks by preventing workplace accidents and injuries.
Lastly, an effective layout provides flexibility, allowing for future expansion or modifications as production needs change.
Improving Productivity Through Layout Design
Productivity improvements are a key focus in factory layout design.
By optimizing the arrangement of equipment and workstations, factories can increase their output without additional resources.
One approach is to implement lean manufacturing principles, which focus on eliminating waste and maximizing value.
Another method is to streamline communication and coordination between departments.
Clear pathways and easily accessible equipment reduce delays and enhance collaboration among team members.
Regular assessment and adjustment of the layout based on feedback can lead to continuous improvements.
By evaluating performance metrics, such as production speed and defect rates, managers can identify areas for enhancement.
Key Points in Factory Layout Improvement
When aiming to improve factory layouts, there are several key points to consider.
Analyzing Workflow
First, it’s important to conduct a thorough analysis of the current workflow and identify bottlenecks or inefficiencies.
Understanding how materials and information flow through the production process can highlight areas that require optimization.
Space Utilization
Effective space utilization is another crucial aspect.
Ensure that equipment and workstations are placed in a way that maximizes available space while allowing for smooth movement and transportation.
Avoid overcrowed areas, as they can lead to slowdowns and safety hazards.
Ergonomics and Safety
Prioritize ergonomics and safety in the design.
Ensure that the layout minimizes physical strain on workers and reduces the potential for accidents.
This not only improves productivity but also enhances employee satisfaction and reduces absenteeism.
Incorporating Technology
Technology plays a significant role in modern factory layouts.
Incorporating automated systems and data-driven solutions can optimize processes and enhance decision-making.
For instance, using robotics for repetitive tasks can increase precision and speed, while monitoring systems can provide real-time data for immediate adjustments.
Conclusion
The fundamentals of factory layout design are crucial for enhancing productivity and achieving efficient operations.
By understanding the different types of layouts and the benefits of a well-designed setup, businesses can achieve higher output and better quality.
Moreover, by focusing on key points such as workflow analysis, space utilization, ergonomics, safety, and technology integration, factories can continuously improve and adapt to changing needs.
Investing time and resources in optimizing factory layouts not only leads to immediate gains but also paves the way for sustainable growth and competitiveness in the manufacturing industry.
資料ダウンロード
QCD管理受発注クラウド「newji」は、受発注部門で必要なQCD管理全てを備えた、現場特化型兼クラウド型の今世紀最高の受発注管理システムとなります。
ユーザー登録
受発注業務の効率化だけでなく、システムを導入することで、コスト削減や製品・資材のステータス可視化のほか、属人化していた受発注情報の共有化による内部不正防止や統制にも役立ちます。
NEWJI DX
製造業に特化したデジタルトランスフォーメーション(DX)の実現を目指す請負開発型のコンサルティングサービスです。AI、iPaaS、および先端の技術を駆使して、製造プロセスの効率化、業務効率化、チームワーク強化、コスト削減、品質向上を実現します。このサービスは、製造業の課題を深く理解し、それに対する最適なデジタルソリューションを提供することで、企業が持続的な成長とイノベーションを達成できるようサポートします。
製造業ニュース解説
製造業、主に購買・調達部門にお勤めの方々に向けた情報を配信しております。
新任の方やベテランの方、管理職を対象とした幅広いコンテンツをご用意しております。
お問い合わせ
コストダウンが利益に直結する術だと理解していても、なかなか前に進めることができない状況。そんな時は、newjiのコストダウン自動化機能で大きく利益貢献しよう!
(β版非公開)