- お役立ち記事
- Fundamentals of fatigue and fracture and applied technology for life prediction and strength design
Fundamentals of fatigue and fracture and applied technology for life prediction and strength design
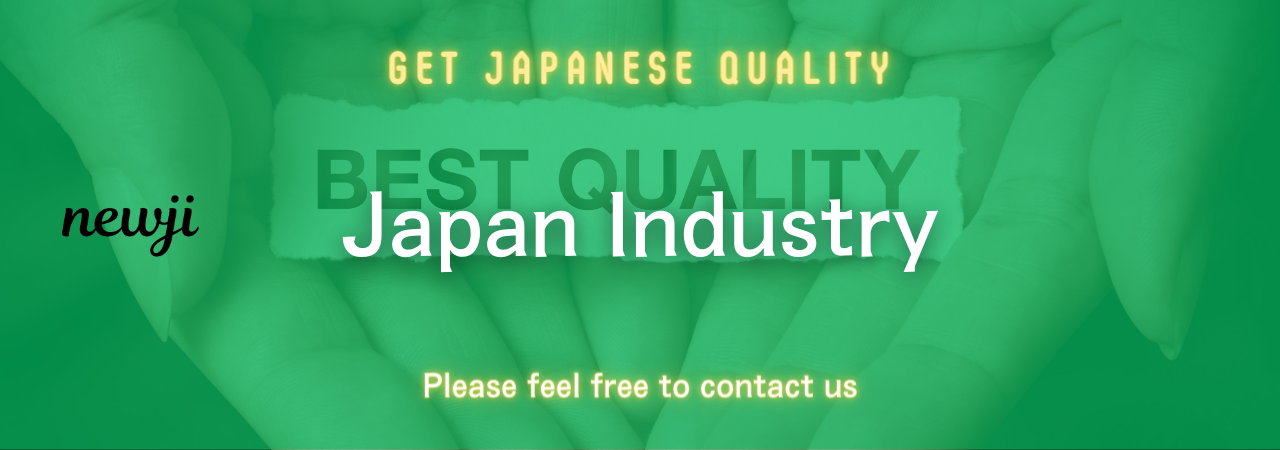
目次
Understanding Fatigue and Fracture
Fatigue and fracture are critical concepts in the field of material science and engineering.
They describe how materials respond to stress and strain over time, impacting their longevity and safety.
Let’s delve into these concepts to understand their fundamentals.
Fatigue refers to the weakening of a material caused by repeated load cycles.
Over time, these cycles lead to microscopic damages that can grow into cracks, eventually causing failure.
Fatigue is insidious because it occurs under loads that are significantly lower than an object’s tensile strength.
This makes it crucial for engineers to consider fatigue when designing components that undergo repetitive stress, such as bridges, aircraft, and machinery.
Fracture, on the other hand, relates to the propagation of cracks resulting from applied stress.
This can occur in a single, sudden event or as a result of an ongoing fatigue process.
Fractures are categorized into two types: ductile and brittle.
Ductile fractures occur when materials deform before failing, while brittle fractures happen without noticeable deformation.
Understanding the mechanism of fracture is essential for predicting material failure and improving design practices.
Factors Influencing Fatigue and Fracture
Several factors influence how materials experience fatigue and fracture.
Material properties, environmental conditions, and load characteristics all play significant roles.
Material properties such as toughness, hardness, and ductility define how a material responds to stress.
Some materials, like metals, are more ductile, meaning they can endure significant deformation.
Others, like ceramics, are brittle and more prone to sudden fracture.
Environmental conditions can also cause variations in fatigue and fracture behavior.
For instance, temperature extremes can exacerbate fatigue, while corrosive environments can accelerate crack growth.
Hence, environmental considerations are crucial when designing for durability and safety.
The nature of the load itself impacts material fatigue and fracture.
Factors such as load magnitude, frequency, and form (tension, compression, or torsion) need to be carefully evaluated.
High-frequency, alternating loads can expedite the fatigue process, while the presence of notches or other stress concentrators often precipitates fractures.
Life Prediction and Strength Design
Predicting the lifespan of materials and designing them for strength are vital to ensuring safety and functionality.
Applied technology enables engineers to make informed choices in this regard.
Fatigue Life Prediction
Fatigue life prediction involves estimating how long a material can withstand cyclic loading before failure.
This process employs both analytical and experimental approaches.
One common method is the S-N curve, which represents the relationship between the stress amplitude and the number of cycles to failure.
These curves help predict life expectancy, allowing engineers to assess whether a component can survive under expected stress conditions.
Advanced computational tools like Finite Element Analysis (FEA) further enhance prediction accuracy.
FEA simulates complex load scenarios, enabling the visualization of stress distributions and potential failure points.
Designing for Strength
Designing for strength requires careful selection of materials and design methodologies to ensure structures can endure expected loads without failing.
Engineers often employ factor of safety (FoS) in their design processes.
This involves designing components to withstand loads several times greater than the maximum expected.
While this ensures durability, it also raises the cost and weight, making optimization essential.
Material selection is another critical element.
Choosing the appropriate material for the application—considering its mechanical properties, environmental resistance, and cost—can greatly affect the success of a design.
Applied Technologies in Fatigue and Fracture Analysis
Technological advancements have significantly enhanced our capabilities in fatigue and fracture analysis, offering more accurate assessments and insights.
Non-Destructive Testing (NDT)
NDT methods like ultrasonic testing, magnetic particle inspection, and radiographic testing allow for the detection of flaws without damaging the object.
These techniques are pivotal in identifying fatigue cracks early in their development, preventing catastrophic failure.
Digital Twins
The integration of digital twins—virtual models reflecting real-time conditions of physical objects—into fatigue and fracture analysis provides dynamic insights.
These models can predict how materials respond to operational stresses, assisting in proactive maintenance and design optimization.
Machine Learning and AI
Machine learning and AI are revolutionizing fatigue and fracture prediction.
By analyzing vast datasets, AI models can identify patterns and predict failure points more accurately than traditional methods.
This leads to improved predictive maintenance and enhanced design frameworks.
Conclusion
Understanding the fundamentals of fatigue and fracture is crucial for designing durable materials and structures.
By leveraging advanced technologies and methodologies, engineers can predict life expectancies and design for strength more effectively.
This ensures safety, reliability, and performance, minimizing the risks of failure in critical applications.
As technology progresses, our capacity for accurate fatigue and fracture analysis will only continue to improve, leading to innovative designs that meet ever-growing challenges.
資料ダウンロード
QCD調達購買管理クラウド「newji」は、調達購買部門で必要なQCD管理全てを備えた、現場特化型兼クラウド型の今世紀最高の購買管理システムとなります。
ユーザー登録
調達購買業務の効率化だけでなく、システムを導入することで、コスト削減や製品・資材のステータス可視化のほか、属人化していた購買情報の共有化による内部不正防止や統制にも役立ちます。
NEWJI DX
製造業に特化したデジタルトランスフォーメーション(DX)の実現を目指す請負開発型のコンサルティングサービスです。AI、iPaaS、および先端の技術を駆使して、製造プロセスの効率化、業務効率化、チームワーク強化、コスト削減、品質向上を実現します。このサービスは、製造業の課題を深く理解し、それに対する最適なデジタルソリューションを提供することで、企業が持続的な成長とイノベーションを達成できるようサポートします。
オンライン講座
製造業、主に購買・調達部門にお勤めの方々に向けた情報を配信しております。
新任の方やベテランの方、管理職を対象とした幅広いコンテンツをご用意しております。
お問い合わせ
コストダウンが利益に直結する術だと理解していても、なかなか前に進めることができない状況。そんな時は、newjiのコストダウン自動化機能で大きく利益貢献しよう!
(Β版非公開)