- お役立ち記事
- Fundamentals of fatigue failure of machines and structures and application to fatigue strength design
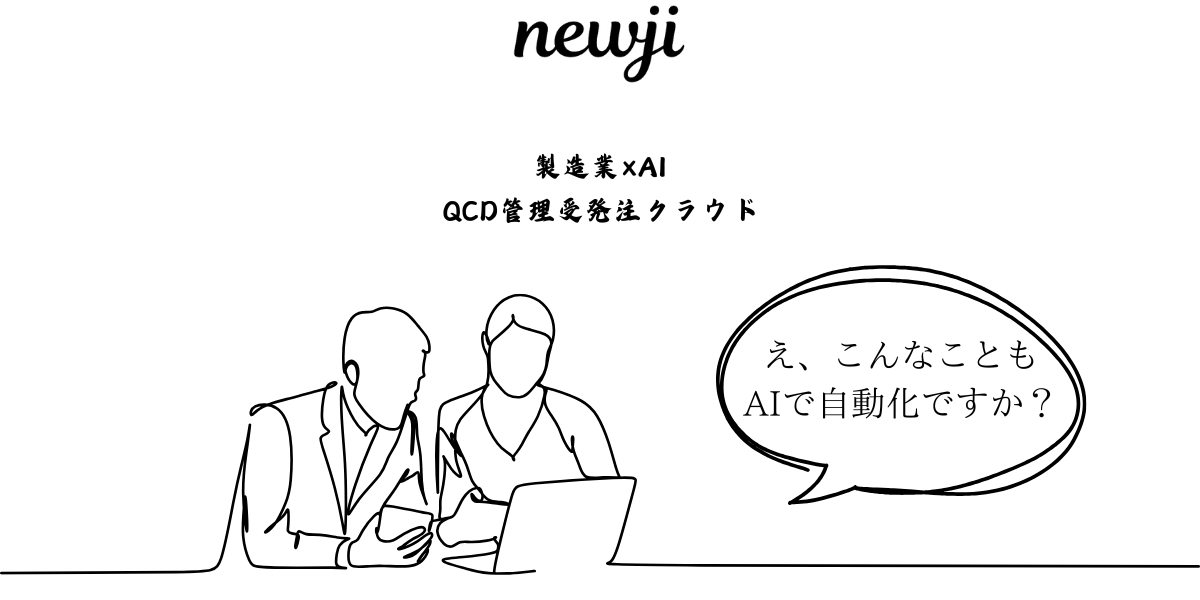
Fundamentals of fatigue failure of machines and structures and application to fatigue strength design
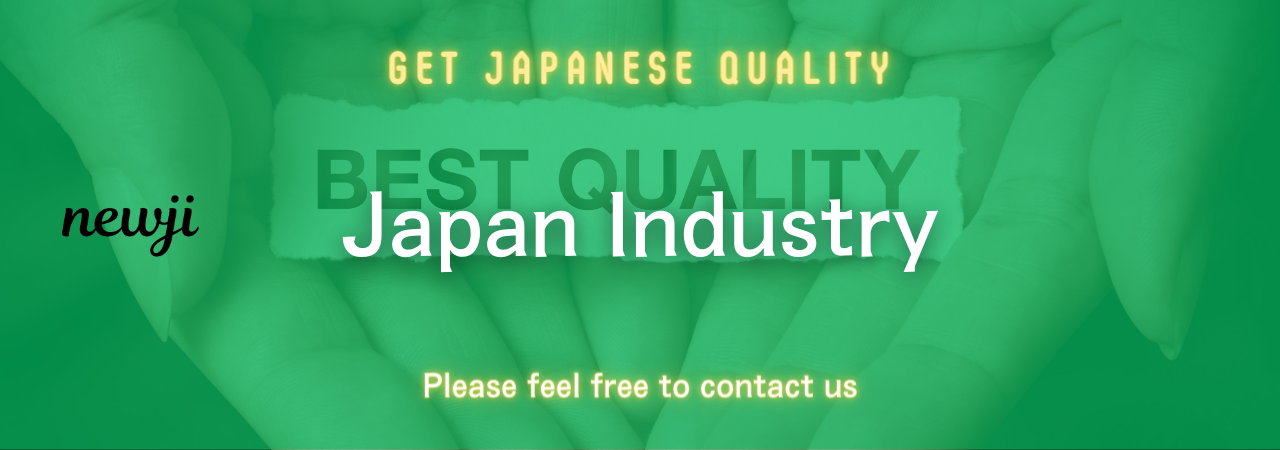
目次
Understanding Fatigue Failure in Machines and Structures
When we talk about machines and structures, we often focus on their design and strength.
However, one critical aspect that engineers must consider is fatigue failure.
This phenomenon can affect everything from bridges to vehicles, and understanding it is essential for ensuring safety and longevity.
Fatigue failure refers to the weakening of a material caused by repeatedly applied loads.
Even materials deemed strong can eventually succumb to fatigue over time, leading to potential catastrophic failures.
It’s crucial for engineers and designers to understand the fundamentals of fatigue to enhance safety and efficiency in structural design.
The Basics of Fatigue Failure
To comprehend fatigue failure, we must first understand how materials behave under stress.
A material experiences fatigue when subjected to repeated cycles of stress, which are often below its ultimate tensile strength.
These repeated stresses lead to the initiation and growth of cracks within the material.
The process begins with several small defects or imperfections present within the structure.
When a load is repeatedly applied, these imperfections act as stress concentrators.
Over time, cracks start to form and grow, ultimately leading to fracture or failure of the component if not addressed.
Fatigue is not a sudden event; it’s a progressive issue.
The rate at which a crack grows can vary based on various factors including the material properties, frequency of loading, and environmental conditions.
The Importance of Stress Concentration
Stress concentration plays a significant role in fatigue failure.
It refers to the localized increase in stress within a material, often caused by irregularities such as notches, holes, or sudden changes in design geometry.
These imperfections result in certain areas experiencing higher stress compared to the rest of the structure.
Understanding and managing stress concentration is an integral part of designing to prevent fatigue failure.
Reducing these concentrations might involve design changes like smooth transitions, the addition of fillets, or the use of reinforcement.
S-N Curves and Fatigue Strength
One of the key tools used to understand and design against fatigue failure is the S-N curve, also known as the Wohler curve.
S-N curves plot the relationship between the stress amplitude (S) and the number of cycles to failure (N).
From these curves, engineers can determine the fatigue strength of materials, which is the maximum stress a material can endure for a specified number of cycles without failure.
This information is vital for selecting materials and designing components to handle expected load cycles during their use.
Design Strategies to Mitigate Fatigue Failure
To prevent fatigue failure, engineers employ various design strategies aimed at increasing the fatigue life of a component.
These strategies are crucial in industries where safety and reliability are non-negotiable, such as aerospace, automotive, and civil engineering.
Material Selection and Treatment
The choice of material significantly impacts fatigue resistance.
Materials are selected based on their inherent fatigue properties, and treatments such as surface hardening or protective coatings are applied to improve performance.
Heat treatments can also enhance the material’s fatigue resistance by altering the microstructure, while treatments like shot peening introduce compressive stresses that oppose the tensile stresses experienced during loading cycles.
Careful Design and Engineering
Design plays a pivotal role in mitigating fatigue.
Engineers focus on minimizing stress concentrations by incorporating smooth curves instead of sharp transitions and avoiding abrupt cross-sectional changes.
Good practice includes ensuring evenly distributed loads and utilizing redundancy where possible.
Redundancy provides alternate load paths and increases safety should parts of a structure begin to fail.
Another important aspect is regular inspection and maintenance.
Early detection of crack initiation can save structures from significant degradation.
Balancing Loads and Enhancing Durability
Designing for balanced loads involves evenly distributing forces across a structure.
This prevents any single point from experiencing excessive stress, which can lead to fatigue.
Additionally, increasing the durability of components by using fatigue-resistant materials ensures they perform optimally over a long period.
Materials like high-strength alloys and composites are often preferred for their impressive fatigue properties.
Applications of Fatigue Strength Design
Fatigue strength design finds application across multiple domains, ensuring structures and machines can withstand the demands of their intended use.
Aerospace and Automotive Engineering
In these fields, lightweight structures are critical, but they must also be robust enough to endure extensive cycling.
Fatigue strength design ensures aircraft wings or vehicle frames are safe and reliable over millions of stress cycles.
Engineers use simulations and real-world testing to predict when and where fatigue might occur so they can design accordingly.
Civil Engineering Applications
Bridges, buildings, and other large infrastructures also need to be designed with fatigue in mind.
For example, the repetitive loads from traffic can induce fatigue in bridge materials over time.
Design elements like expansion joints and flexible materials are used to absorb loads and reduce stress concentrations, prolonging the life of these critical structures.
Conclusion
Fatigue failure poses a significant challenge in the engineering of machines and structures.
A thorough understanding of its principles allows for informed design choices that prioritize safety and durability.
By selecting the right materials, employing strategic design, and understanding stress distribution, engineers can effectively mitigate the risks associated with fatigue failure.
This comprehensive approach ensures that structures are not only strong and functional but also capable of enduring the demands of their service life.
資料ダウンロード
QCD調達購買管理クラウド「newji」は、調達購買部門で必要なQCD管理全てを備えた、現場特化型兼クラウド型の今世紀最高の購買管理システムとなります。
ユーザー登録
調達購買業務の効率化だけでなく、システムを導入することで、コスト削減や製品・資材のステータス可視化のほか、属人化していた購買情報の共有化による内部不正防止や統制にも役立ちます。
NEWJI DX
製造業に特化したデジタルトランスフォーメーション(DX)の実現を目指す請負開発型のコンサルティングサービスです。AI、iPaaS、および先端の技術を駆使して、製造プロセスの効率化、業務効率化、チームワーク強化、コスト削減、品質向上を実現します。このサービスは、製造業の課題を深く理解し、それに対する最適なデジタルソリューションを提供することで、企業が持続的な成長とイノベーションを達成できるようサポートします。
オンライン講座
製造業、主に購買・調達部門にお勤めの方々に向けた情報を配信しております。
新任の方やベテランの方、管理職を対象とした幅広いコンテンツをご用意しております。
お問い合わせ
コストダウンが利益に直結する術だと理解していても、なかなか前に進めることができない状況。そんな時は、newjiのコストダウン自動化機能で大きく利益貢献しよう!
(Β版非公開)