- お役立ち記事
- Fundamentals of fatigue fracture and application to life prediction and strength design
月間76,176名の
製造業ご担当者様が閲覧しています*
*2025年3月31日現在のGoogle Analyticsのデータより
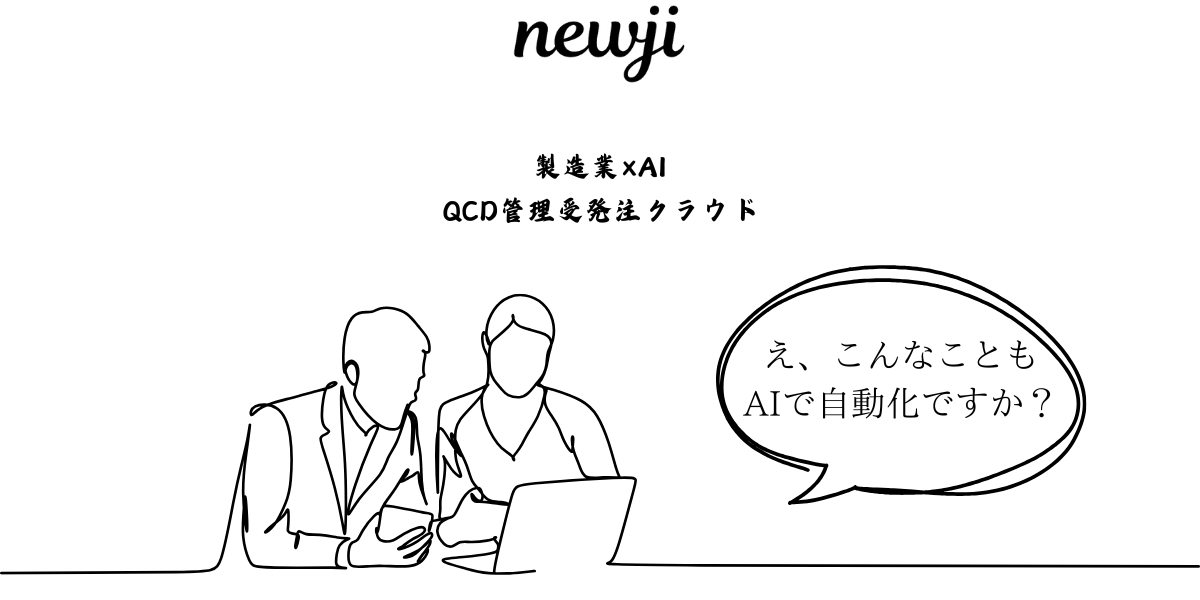
Fundamentals of fatigue fracture and application to life prediction and strength design
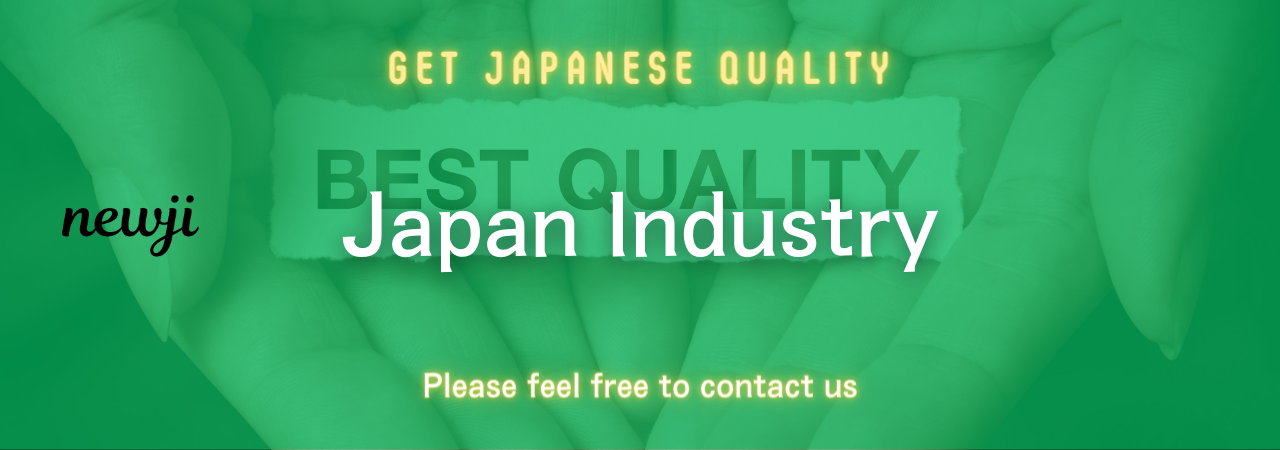
目次
Understanding Fatigue Fracture
Fatigue fracture refers to the progressive and localized structural damage that occurs when a material is subjected to cyclic loading.
Unlike a sudden break or failure, fatigue fracture develops over time and often starts from small cracks that grow with repeated load cycles.
The term “fatigue” in this context refers to the results of the stress and strain placed on a material beyond its elastic limit.
Once a material is stressed repeatedly, the initiation of micro-cracks begins at a microscopic level.
These micro-cracks gradually propagate until the material ultimately fails.
The study of fatigue fracture is invaluable for engineers and designers as it significantly affects the durability and safety of materials used in construction, manufacturing, and many other fields.
Stages of Fatigue Fracture
Fatigue fracture generally occurs in three stages:
Initiation
Cracks begin to develop in the material due to stress concentrations.
These are often present in areas with structural irregularities, such as holes, notches, or surface imperfections.
The critical aspect of this stage is that these cracks are initially microscopic and can appear insignificant to the naked eye.
Propagation
This stage involves the growth of the initial cracks.
With each load cycle, these cracks expand, moving perpendicularly to the applied stress.
Propagation can continue for a significant part of the component’s service life before becoming critically large.
Final Fracture
The final fracture occurs when the remaining uncracked section of the material is no longer able to sustain the load.
This stage is rapid, and the material breaks suddenly.
Factors Influencing Fatigue Fracture
Several factors influence fatigue fracture, which include:
Material Properties
Different materials have different resistance to fatigue.
These properties are critical in determining a material’s fatigue strength, often dictating the choice of material in design applications.
Load Characteristics
The magnitude and frequency of cyclic loads greatly influence fatigue.
High-stress cycles or repeated applications of stress below the material’s original tensile strength can encourage fatigue fracture.
Environment
Environmental conditions, such as humidity, temperature, and corrosive elements, can accelerate fatigue.
For example, metals exposed to moisture may corrode faster, leading to a weakened structure more susceptible to crack development.
Design and Geometry
The geometry of components influences stress distribution.
Components with sharp edges or notches may have stress concentrations, making them more vulnerable to fatigue fracture.
Life Prediction in Fatigue Fracture
Estimating the lifespan of components subject to fatigue is critical, especially in sectors like aerospace, automotive, and civil engineering.
Several methods are used to predict the lifespan:
S-N Curve
The S-N curve (also known as the Wöhler curve) represents the relationship between the cyclic stress (S) applied to a material and the number of cycles to failure (N).
The curve provides insights into how long a material can endure varying stress levels.
Fracture Mechanics
This method focuses on the characterization of material properties and flaws.
Fracture mechanics helps in understanding how cracks grow and how long it takes for them to reach a critical size.
Miner’s Rule
Miner’s rule is a cumulative damage rule used to estimate fatigue life.
The rule assumes that damage accumulates linearly, so each level of stress cycle contributes to life consumption.
Strength Design Considering Fatigue Fracture
Designing components to withstand fatigue involves several strategies:
Material Selection
Choosing materials with high fatigue strength or those better suited for the expected environmental conditions can mitigate fatigue fracture.
Design Optimization
Design optimization involves altering the geometry of components to minimize stress concentrations.
Smooth transitions and rounded corners can help manage and distribute stresses more evenly.
Surface Treatment
Processes like shot peening or carburizing can enhance surface properties, making them more resistant to crack initiation.
Regular Inspection and Maintenance
Proactive inspection and maintenance can detect early signs of fatigue before visible fractures occur.
This preventive approach helps extend the lifespan of components.
Conclusion
Understanding the fundamentals of fatigue fracture allows engineers and designers to predict and prevent structural failures effectively.
Considering factors influencing fatigue, employing life prediction techniques, and designing for strength are all crucial aspects of managing fatigue fractures.
With precise planning and comprehensive knowledge, it is possible to enhance safety and longevity across a range of applications.
資料ダウンロード
QCD管理受発注クラウド「newji」は、受発注部門で必要なQCD管理全てを備えた、現場特化型兼クラウド型の今世紀最高の受発注管理システムとなります。
ユーザー登録
受発注業務の効率化だけでなく、システムを導入することで、コスト削減や製品・資材のステータス可視化のほか、属人化していた受発注情報の共有化による内部不正防止や統制にも役立ちます。
NEWJI DX
製造業に特化したデジタルトランスフォーメーション(DX)の実現を目指す請負開発型のコンサルティングサービスです。AI、iPaaS、および先端の技術を駆使して、製造プロセスの効率化、業務効率化、チームワーク強化、コスト削減、品質向上を実現します。このサービスは、製造業の課題を深く理解し、それに対する最適なデジタルソリューションを提供することで、企業が持続的な成長とイノベーションを達成できるようサポートします。
製造業ニュース解説
製造業、主に購買・調達部門にお勤めの方々に向けた情報を配信しております。
新任の方やベテランの方、管理職を対象とした幅広いコンテンツをご用意しております。
お問い合わせ
コストダウンが利益に直結する術だと理解していても、なかなか前に進めることができない状況。そんな時は、newjiのコストダウン自動化機能で大きく利益貢献しよう!
(β版非公開)