- お役立ち記事
- Fundamentals of fatigue fracture, fatigue property evaluation techniques, and measures to improve fatigue strength through mechanical surface modification
月間76,176名の
製造業ご担当者様が閲覧しています*
*2025年3月31日現在のGoogle Analyticsのデータより
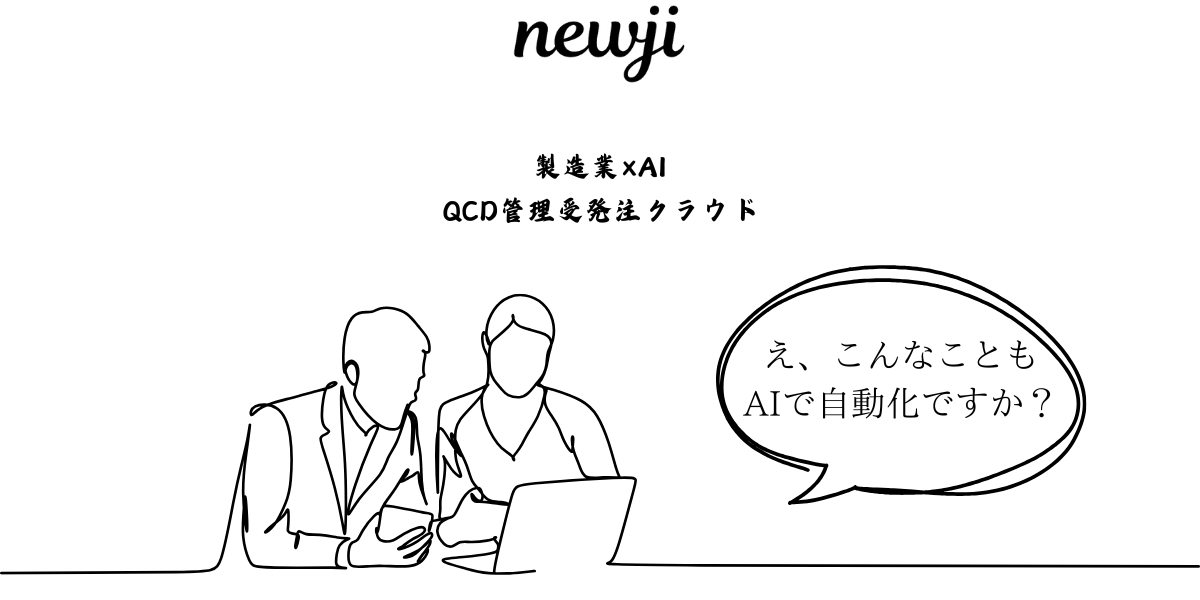
Fundamentals of fatigue fracture, fatigue property evaluation techniques, and measures to improve fatigue strength through mechanical surface modification
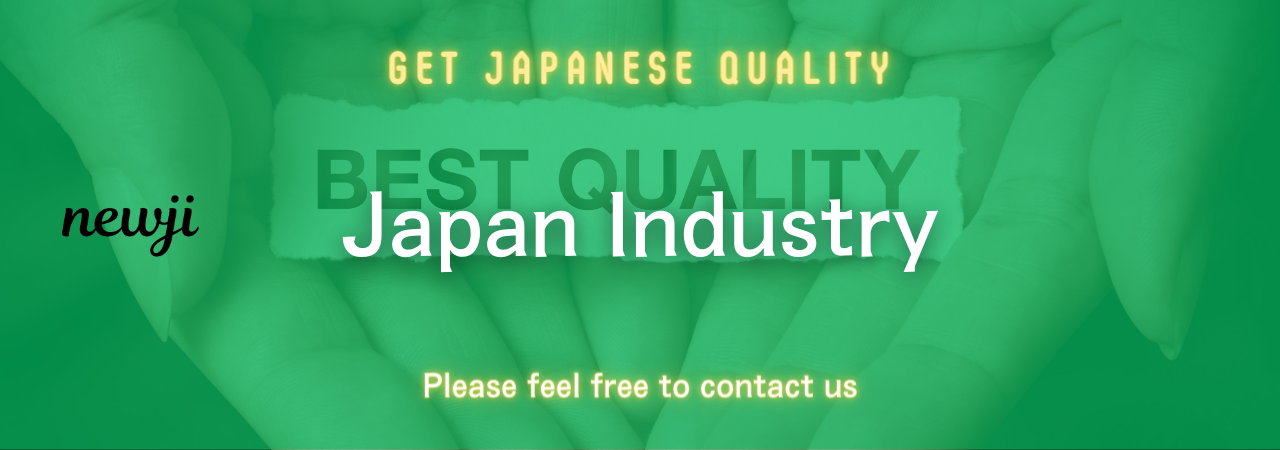
目次
Understanding Fatigue Fracture
Fatigue fracture is a common failure mode in materials subjected to cyclic loads over time.
This type of fracture occurs when a material is repeatedly stressed, leading to the development of cracks and eventual failure.
It often happens at stress levels significantly lower than the material’s ultimate tensile strength.
The fatigue process generally consists of three stages: crack initiation, crack propagation, and final fracture.
The initiation phase involves the formation of tiny cracks at stress concentrators such as surface imperfections or inclusions.
During the propagation phase, these cracks grow with each cycle of loading.
Finally, in the fracture stage, the cracks reach a critical size, and the material fails catastrophically.
Fatigue fracture poses significant challenges because it can occur without warning, causing unexpected and potentially dangerous failures in components and structures.
Understanding the fundamentals of fatigue fracture is essential in designing products and structures that can withstand repetitive stresses without falling apart prematurely.
Fatigue Property Evaluation Techniques
Evaluating the fatigue properties of a material involves assessing how it responds to cyclic loading.
Several techniques help in understanding fatigue behavior and predicting the life of materials under such conditions.
Fatigue Testing
Fatigue testing is a crucial method for evaluating material behavior under cyclic loads.
The tests typically involve applying a fluctuating stress or strain to a specimen and recording the number of cycles it can endure before failure.
S-N curves (Stress-Number of cycles) are commonly used to represent fatigue test data, showing the relationship between cyclic stress and number of cycles to failure.
Crack Growth Rate Analysis
The crack growth rate analysis measures the rate at which a crack propagates through a material under cyclic loading.
This approach helps in predicting the remaining useful life of a component after a crack is detected.
Understanding crack growth rates allows engineers to set inspection intervals and enhance maintenance strategies, minimizing the risk of unexpected failures.
Fractography
Fractography involves examining the fracture surfaces of a material, often with scanning electron microscopy (SEM), to identify the features and mechanisms involved in the fatigue fracture process.
Analyzing the fracture surfaces provides insights into the location of crack initiation, propagation paths, and overload zones, offering valuable information for improving material and component designs.
Measures to Improve Fatigue Strength
Improving fatigue strength is critical for extending the life of components under cyclic loading.
One effective approach involves mechanical surface modification techniques.
Shot Peening
Shot peening is a surface treatment process that involves bombarding the surface of a material with small spherical media.
This action introduces compressive residual stresses on the surface, preventing the initiation and growth of fatigue cracks.
Shot peening is widely used in the automotive and aerospace industries to improve fatigue strength and lifespan of components such as gears and springs.
Surface Hardening
Surface hardening techniques, such as carburizing or nitriding, enhance the wear resistance and fatigue strength of materials by modifying their surface chemistry and microstructure.
These processes involve introducing carbon or nitrogen into the surface layer, creating a hardened outer shell with improved mechanical properties.
The increased surface hardness reduces the likelihood of crack initiation and improves the component’s overall fatigue performance.
Burnishing
Burnishing is a mechanical treatment that improves surface finish and induces compressive residual stresses, enhancing fatigue strength.
During burnishing, a hard, smooth tool applies pressure to the surface of a material, flattening peaks and filling valleys.
This process increases surface hardness, reduces roughness, and effectively enhances the material’s resistance to fatigue failure.
Conclusion
Understanding fatigue fracture and employing appropriate evaluation techniques are fundamental in assessing material performance under cyclic loading.
Implementing mechanical surface modification methods can significantly enhance fatigue strength, leading to more durable and reliable components.
These strategies are particularly important in industries where the safety and longevity of products are paramount.
By incorporating these measures, engineers can design components that better withstand the rigors of repeated stresses, ultimately resulting in safer, more reliable products and structures.
資料ダウンロード
QCD管理受発注クラウド「newji」は、受発注部門で必要なQCD管理全てを備えた、現場特化型兼クラウド型の今世紀最高の受発注管理システムとなります。
ユーザー登録
受発注業務の効率化だけでなく、システムを導入することで、コスト削減や製品・資材のステータス可視化のほか、属人化していた受発注情報の共有化による内部不正防止や統制にも役立ちます。
NEWJI DX
製造業に特化したデジタルトランスフォーメーション(DX)の実現を目指す請負開発型のコンサルティングサービスです。AI、iPaaS、および先端の技術を駆使して、製造プロセスの効率化、業務効率化、チームワーク強化、コスト削減、品質向上を実現します。このサービスは、製造業の課題を深く理解し、それに対する最適なデジタルソリューションを提供することで、企業が持続的な成長とイノベーションを達成できるようサポートします。
製造業ニュース解説
製造業、主に購買・調達部門にお勤めの方々に向けた情報を配信しております。
新任の方やベテランの方、管理職を対象とした幅広いコンテンツをご用意しております。
お問い合わせ
コストダウンが利益に直結する術だと理解していても、なかなか前に進めることができない状況。そんな時は、newjiのコストダウン自動化機能で大きく利益貢献しよう!
(β版非公開)