- お役立ち記事
- Fundamentals of fatigue strength and fracture mechanics and their application to damage tolerance design of rotating machinery
月間76,176名の
製造業ご担当者様が閲覧しています*
*2025年3月31日現在のGoogle Analyticsのデータより
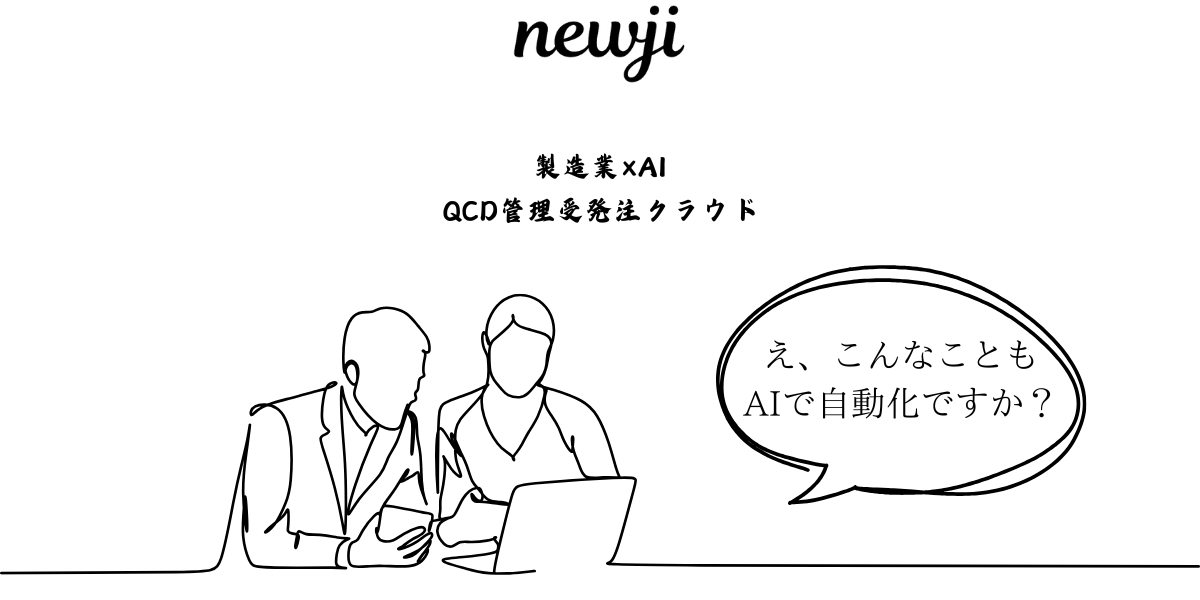
Fundamentals of fatigue strength and fracture mechanics and their application to damage tolerance design of rotating machinery
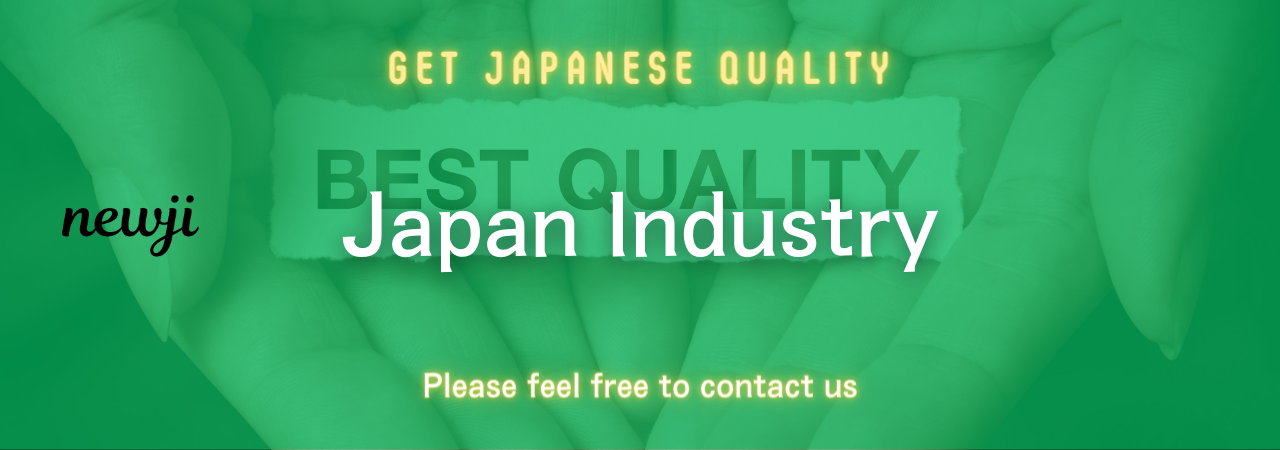
目次
Understanding Fatigue Strength in Rotating Machinery
Rotating machinery is a critical component in many industries, ranging from aerospace to manufacturing.
One of the fundamental aspects of ensuring the reliability and safety of these machines is understanding fatigue strength.
Fatigue strength refers to a material’s ability to withstand repeated loading and unloading cycles without developing cracks or failures over time.
In rotating machinery, components like shafts, gears, and bearings are continuously subjected to cyclic stresses.
These stresses, if not properly accounted for, can lead to fatigue failure, where a crack initiates and propagates until the component ultimately breaks.
To avoid these catastrophic failures, engineers need to assess and optimize the fatigue strength of materials used in these machines.
The process involves determining the maximum stress amplitude a material can endure for a specified number of cycles before failure.
This information is crucial for predicting the lifespan of components and designing them to withstand operational demands.
Factors Affecting Fatigue Strength
Several factors influence the fatigue strength of a material:
– **Surface Finish:** The surface condition of a component can significantly affect its fatigue strength.
Rough surfaces with imperfections serve as stress concentrators, leading to crack initiation.
– **Material Composition:** Different materials exhibit varying fatigue strengths due to their unique mechanical properties.
Metals, composites, and polymers will each respond differently to cyclic loading.
– **Temperature:** Operating conditions, such as temperature, can alter the fatigue strength of materials.
Elevated temperatures may reduce strength, while low temperatures might increase brittleness.
– **Size and Geometry:** The size and shape of a component influence stress distribution.
Larger components or those with complex geometries might have lower fatigue strength due to uneven stress distribution.
Introduction to Fracture Mechanics
Fracture mechanics is a field of study that analyzes the formation and growth of cracks in materials.
It plays a critical role in understanding how and why materials break under stress.
By applying principles of fracture mechanics, engineers can predict the behavior of cracks and develop strategies to prevent them from leading to failure.
One of the fundamental concepts in fracture mechanics is the stress intensity factor, which quantifies stress concentration at the tip of a crack.
This factor helps determine whether a crack will propagate or remain stable.
The fracture toughness of a material is also crucial.
It represents the material’s resistance to crack propagation.
A material with high fracture toughness can withstand significant stress before a crack advances, making it ideal for applications where durability is essential.
Importance of Fracture Mechanics in Rotating Machinery
In rotating machinery, fracture mechanics is particularly important for the following reasons:
– **Predictive Maintenance:** By understanding how cracks develop and grow, engineers can implement maintenance schedules that address potential failures before they occur.
– **Material Selection:** Choosing materials with appropriate fracture toughness ensures components are more resistant to crack propagation, enhancing overall machine reliability.
– **Design Optimization:** Applying fracture mechanics allows for the design of components that distribute stress more evenly, reducing the risk of crack initiation.
Damage Tolerance Design in Rotating Machinery
Damage tolerance design is an approach that integrates fatigue strength and fracture mechanics to ensure machinery can withstand damage without catastrophic failure.
This design philosophy assumes that flaws or cracks might be present in components due to manufacturing processes or operational conditions.
The goal is to create machines capable of tolerating these imperfections while maintaining functionality and safety.
By adopting a damage tolerance approach, engineers can enhance the longevity of rotating machinery and minimize unexpected downtime.
Key Elements of Damage Tolerance Design
– **Regular Inspection:** Implementing rigorous inspection protocols helps detect and monitor existing flaws before they compromise machine integrity.
– **Non-Destructive Testing:** Utilizing advanced methods like ultrasonic or radiographic testing ensures flaws are identified without damaging components.
– **Residual Stress Analysis:** Analyzing residual stresses within materials helps engineers understand and mitigate conditions that contribute to crack initiation.
– **Design Redundancy:** Incorporating redundant systems or components that can continue to function if others fail is essential for maintaining operational safety.
Application in Industries
Damage tolerance design, supported by principles of fatigue strength and fracture mechanics, finds application across various industries:
– **Aerospace:** Aircraft engines and structures undergo tremendous cyclic loading.
Applying damage tolerance design ensures these components meet stringent safety standards.
– **Automotive:** Drive shafts, gears, and other rotating parts require robust fatigue and fracture resistance to ensure vehicle reliability.
– **Energy:** In wind turbines, for instance, rotating components face continuous cycles of stress.
A damage-tolerance approach helps manage these stresses, extending the life of the turbines.
Conclusion
Understanding fatigue strength and fracture mechanics is crucial for designing rotating machinery that can tolerate damage without failure.
By incorporating these principles into damage tolerance design, engineers can create machines that are not only reliable but also safe and efficient over their operational lifespan.
With ongoing advances in material science and engineering techniques, the application of these concepts will continue to play a vital role in developing more resilient and dependable rotating machinery across various industries.
資料ダウンロード
QCD管理受発注クラウド「newji」は、受発注部門で必要なQCD管理全てを備えた、現場特化型兼クラウド型の今世紀最高の受発注管理システムとなります。
ユーザー登録
受発注業務の効率化だけでなく、システムを導入することで、コスト削減や製品・資材のステータス可視化のほか、属人化していた受発注情報の共有化による内部不正防止や統制にも役立ちます。
NEWJI DX
製造業に特化したデジタルトランスフォーメーション(DX)の実現を目指す請負開発型のコンサルティングサービスです。AI、iPaaS、および先端の技術を駆使して、製造プロセスの効率化、業務効率化、チームワーク強化、コスト削減、品質向上を実現します。このサービスは、製造業の課題を深く理解し、それに対する最適なデジタルソリューションを提供することで、企業が持続的な成長とイノベーションを達成できるようサポートします。
製造業ニュース解説
製造業、主に購買・調達部門にお勤めの方々に向けた情報を配信しております。
新任の方やベテランの方、管理職を対象とした幅広いコンテンツをご用意しております。
お問い合わせ
コストダウンが利益に直結する術だと理解していても、なかなか前に進めることができない状況。そんな時は、newjiのコストダウン自動化機能で大きく利益貢献しよう!
(β版非公開)