- お役立ち記事
- Fundamentals of fatigue strength in metal materials, application to fatigue design, and latest technology
Fundamentals of fatigue strength in metal materials, application to fatigue design, and latest technology
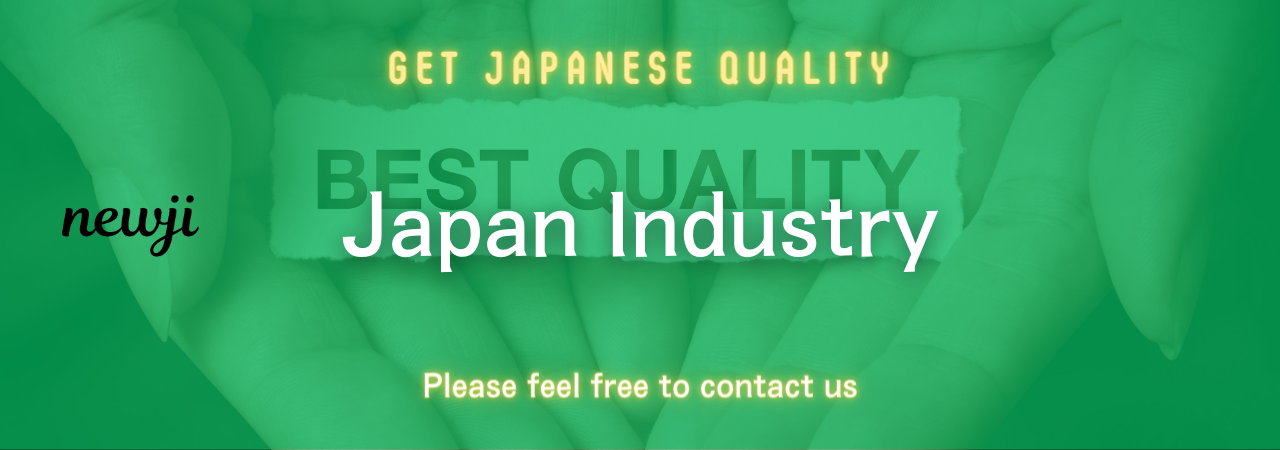
Fatigue strength is a critical property of metal materials that determines their ability to withstand repeated loading and unloading cycles without failure.
Understanding the fundamentals of fatigue strength is essential for designing durable structures and components in industries such as automotive, aerospace, and construction.
In this article, we will explore the basic principles of fatigue strength, how it is applied in fatigue design, and the latest technologies that are enhancing our capabilities in this area.
目次
What Is Fatigue Strength?
Fatigue strength is the maximum stress a material can endure for a specified number of cycles without experiencing failure.
Unlike static loads, which apply a constant force, fatigue involves dynamic and fluctuating stresses that can lead to gradual material degradation over time.
The concept of fatigue is crucial because many components in machinery and structures are subject to cyclic loading.
This can include anything from the wing of an aircraft experiencing fluctuating wind forces to a bridge dealing with varying traffic loads.
Factors Affecting Fatigue Strength
Several factors can influence the fatigue strength of metal materials:
– **Material Type**: Different metals have varying inherent fatigue properties.
Steel, for instance, typically has higher fatigue strength than aluminum.
– **Surface Condition**: Surface imperfections, such as scratches or pitting, can act as stress concentrators and significantly reduce fatigue strength.
– **Temperature**: High temperatures can lower fatigue strength by promoting microstructural changes in the material.
– **Loading Type**: The pattern and frequency of the applied load cycles can impact fatigue strength.
Fully reversing loads are generally more damaging than repeated tension loads.
– **Environmental Conditions**: Corrosive environments can lead to chemical reactions that weaken the material on a microscopic level, thus reducing fatigue strength.
Application to Fatigue Design
Understanding fatigue strength is crucial in the process of fatigue design, which involves predicting the lifespan of components and ensuring that products do not fail unexpectedly during their service life.
Engineers use several strategies and methodologies to incorporate fatigue considerations into their designs.
Fatigue Analysis
Fatigue analysis is a quantitative assessment method that predicts how long a material or component can withstand cyclic loads before failure occurs.
This involves detailed calculations and simulations that consider all the above-mentioned factors affecting fatigue strength.
The process typically includes:
– **S-N Curve Analysis**: This involves plotting the relationship between stress (S) and the number of cycles to failure (N) on a graph to predict fatigue life.
– **Finite Element Analysis (FEA)**: A computer-based technique that models the stresses and strains in complex geometries to locate areas prone to fatigue failure.
– **Fatigue Crack Growth Modeling**: This method tracks the progression of a crack through a material and predicts when it will become critical.
Design for Fatigue
To design components that are resistant to fatigue, engineers often employ the following strategies:
– **Material Selection**: Choosing materials with high fatigue strength and conducive qualities for the environment and application.
– **Surface Treatment**: Techniques like shot peening, case hardening, or coatings can enhance surface characteristics and improve fatigue life.
– **Load Management**: Implementing design changes to redistribute loads more evenly or avoid stress concentrations can prolong component life.
– **Redundancy and Safety Factors**: Designing with additional safety margins and redundancy to account for unforeseen variations in load or material properties.
Latest Technology in Fatigue Strength
Advances in technology are continually improving our ability to predict, detect, and enhance fatigue strength in metal materials.
These technologies are pushing the boundaries of fatigue resistance and offering new capabilities for engineers and designers.
Non-Destructive Testing (NDT)
Innovations in NDT allow for the inspection of components for fatigue damage without causing harm.
Advanced methods such as ultrasonic testing, phased array, and digital radiography provide detailed analyses of material integrity, making it easier to spot potential issues before they lead to failure.
Additive Manufacturing
Additive manufacturing or 3D printing is revolutionizing the production of components with complex geometries that were previously difficult or impossible to create.
This technology enables more efficient stress distribution designs and the incorporation of internal structures that enhance fatigue resistance.
Smart Materials and Sensors
The use of smart materials and embedded sensors provides real-time monitoring of stress, temperature, and fatigue life in critical components.
These systems can alert operators to potential fatigue issues, allowing for preemptive maintenance and reducing unexpected downtimes.
AI and Machine Learning
Artificial intelligence and machine learning algorithms are being used to sift through vast amounts of data from fatigue tests and service monitoring systems.
These tools can identify patterns and predict fatigue life with greater accuracy, providing engineers with actionable insights for design improvement.
In conclusion, the fundamentals of fatigue strength in metal materials are integral to creating reliable and long-lasting components.
By applying fatigue design principles and embracing the latest technological advancements, we can enhance the performance and safety of engineering systems worldwide.
Continuing research and development in this field promise further improvements in fatigue resistance and the overall durability of metal materials.
資料ダウンロード
QCD調達購買管理クラウド「newji」は、調達購買部門で必要なQCD管理全てを備えた、現場特化型兼クラウド型の今世紀最高の購買管理システムとなります。
ユーザー登録
調達購買業務の効率化だけでなく、システムを導入することで、コスト削減や製品・資材のステータス可視化のほか、属人化していた購買情報の共有化による内部不正防止や統制にも役立ちます。
NEWJI DX
製造業に特化したデジタルトランスフォーメーション(DX)の実現を目指す請負開発型のコンサルティングサービスです。AI、iPaaS、および先端の技術を駆使して、製造プロセスの効率化、業務効率化、チームワーク強化、コスト削減、品質向上を実現します。このサービスは、製造業の課題を深く理解し、それに対する最適なデジタルソリューションを提供することで、企業が持続的な成長とイノベーションを達成できるようサポートします。
オンライン講座
製造業、主に購買・調達部門にお勤めの方々に向けた情報を配信しております。
新任の方やベテランの方、管理職を対象とした幅広いコンテンツをご用意しております。
お問い合わせ
コストダウンが利益に直結する術だと理解していても、なかなか前に進めることができない状況。そんな時は、newjiのコストダウン自動化機能で大きく利益貢献しよう!
(Β版非公開)