- お役立ち記事
- Fundamentals of feedback control technology and application to modeling and control design using MATLAB/Simulink
月間76,176名の
製造業ご担当者様が閲覧しています*
*2025年3月31日現在のGoogle Analyticsのデータより
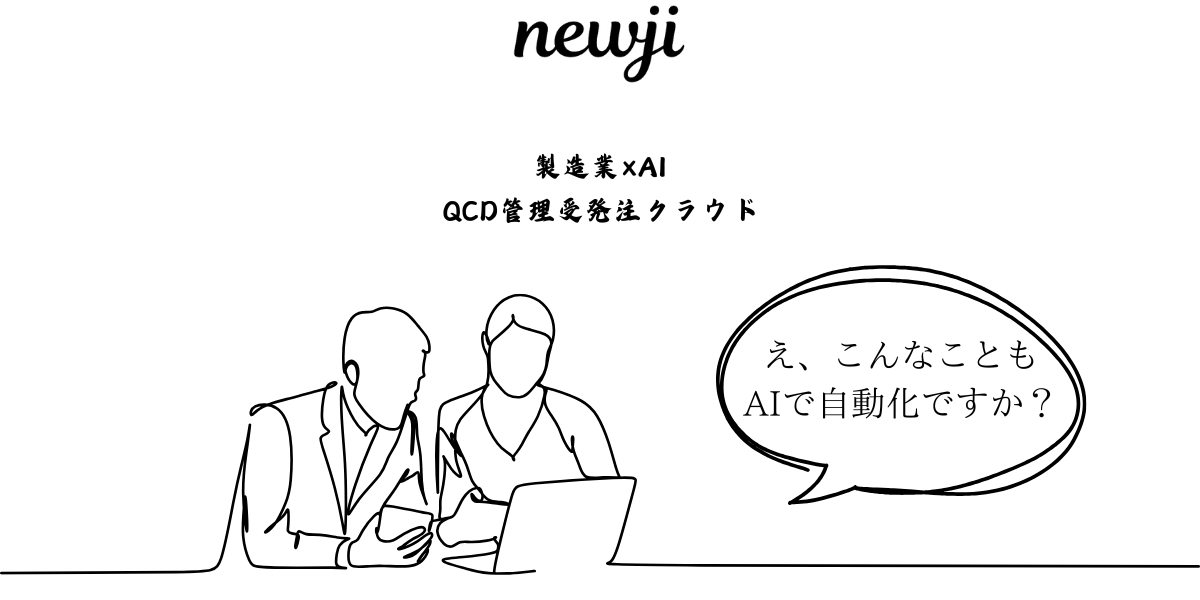
Fundamentals of feedback control technology and application to modeling and control design using MATLAB/Simulink
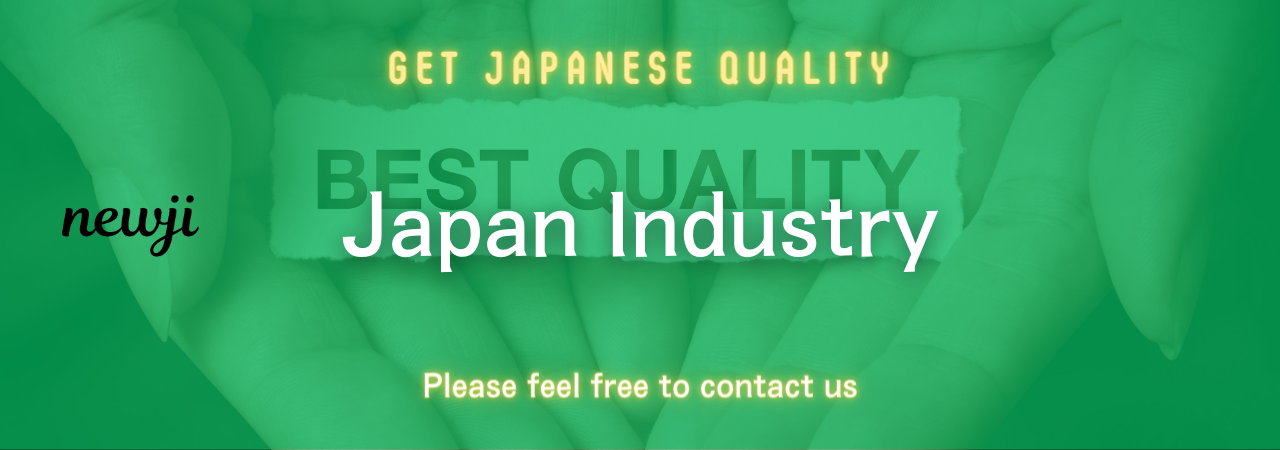
目次
Introduction to Feedback Control Technology
Feedback control technology is a fundamental concept in engineering that allows systems to maintain desired performance by automatically adjusting their operation based on the output’s behavior.
At its core, feedback control involves taking measurements of a system’s output, comparing this output to a desired reference value, and making necessary adjustments to reduce any discrepancies.
These automated adjustments help systems perform efficiently and effectively under varying conditions.
In simple terms, feedback control is all about making sure that a system behaves in a certain way, even if there are changes in the environment or conditions in which it operates.
This technology is applied in various fields such as automotive, aerospace, manufacturing, and robotics.
In essence, feedback control is widely useful for maintaining stability and performance in both simple and complex systems.
The Basic Principles of Feedback Control
Open-Loop vs. Closed-Loop Control
In open-loop control, the control action is not influenced by the output of the system.
This means that the system operates based on a fixed set of inputs, regardless of the outcome.
An example of open-loop control is a basic washing machine that runs for a set time regardless of the cleanliness of the clothes.
Closed-loop control, on the other hand, involves continuous monitoring of the system’s output.
The system utilizes this information to compare the actual output with the desired output (reference value) and makes adjustments accordingly.
This is more complex than open-loop control but allows for more accurate and efficient system operation.
For example, a thermostat in a heating system constantly measures the temperature and regulates the heat output to maintain a set temperature.
The Importance of Feedback
Feedback is critical in closed-loop control systems.
It provides real-time data on how the system is performing.
By using this information, the system can make precise and timely adjustments to ensure optimal performance.
Feedback can be taken from different sensors and inputs depending on the desired output.
Feedback can be either positive or negative, depending on the nature of the system.
Negative feedback reduces the error between the actual and desired outputs, leading to stability and control.
Positive feedback amplifies errors and is generally used in systems where increasing the output is desired, such as in amplifiers.
Modeling and Control Design with MATLAB/Simulink
Introduction to MATLAB/Simulink
MATLAB and Simulink are powerful tools used extensively in the field of control system design and analysis.
MATLAB is a high-level programming language and environment for numerical computation, visualization, and programming.
Simulink, which runs on MATLAB, is a graphical editor for modeling, simulating, and analyzing dynamic systems.
These tools allow engineers to model a system, simulate its behavior, and design controllers to meet desired performance specifications.
By using MATLAB and Simulink, complex mathematical models can be created easily, and simulations can be run efficiently to predict system behavior under different conditions.
Building Models in Simulink
To begin modeling in Simulink, you first define the system’s dynamics using a block diagram approach.
This involves laying out blocks that represent different components, such as integrators, gains, and input/output elements.
The graphical nature of Simulink makes it easier to understand and visualize the control system.
Blocks are interconnected to form a complete representation of the system, where mathematical relationships and differential equations are translated into on-screen models.
Once the model is complete, you can run simulations to observe how the system responds to different inputs and disturbance scenarios.
Designing Control Systems
With the model ready, the next step is the design and implementation of a control strategy.
Simulink’s Control Design toolbox provides tools to design and analyze controllers, such as Proportional-Integral-Derivative (PID) controllers or state-space controllers.
You can adjust controller parameters to improve system response, like settling time, overshoot, and steady-state error.
By using simulation results, you can iteratively refine the controller design to achieve desired system performance.
MATLAB/Simulink supports various advanced techniques such as model predictive control and adaptive control, offering flexibility in tackling complex control problems.
Application of Feedback Control Technology
Automotive Industry
In vehicles, feedback control is essential for systems such as anti-lock braking systems (ABS), cruise control, and stability control.
These systems use sensors to detect changes and adjust vehicle dynamics to enhance safety and comfort.
Aerospace Engineering
In the aerospace sector, feedback control ensures the stability and performance of aircraft during flight.
Flight control systems, autopilot features, and engine control systems utilize feedback mechanisms to maintain desired trajectories and performance levels.
Robotics
Robotics heavily rely on feedback control technology to ensure precision and accuracy.
Sensors provide feedback on position, speed, and orientation, allowing robots to perform tasks efficiently, from assembly lines to surgical procedures.
Conclusion
Feedback control technology is a fundamental aspect of modern engineering, providing the tools necessary for maintaining system stability and performance.
Using MATLAB/Simulink, engineers can design, simulate, and refine control systems for various applications.
By understanding the principles of feedback control, you can apply these techniques to diverse fields, improving the efficiency and reliability of systems.
As technology evolves, the applications of feedback control technology continue to expand, offering new solutions for complex engineering challenges.
資料ダウンロード
QCD管理受発注クラウド「newji」は、受発注部門で必要なQCD管理全てを備えた、現場特化型兼クラウド型の今世紀最高の受発注管理システムとなります。
ユーザー登録
受発注業務の効率化だけでなく、システムを導入することで、コスト削減や製品・資材のステータス可視化のほか、属人化していた受発注情報の共有化による内部不正防止や統制にも役立ちます。
NEWJI DX
製造業に特化したデジタルトランスフォーメーション(DX)の実現を目指す請負開発型のコンサルティングサービスです。AI、iPaaS、および先端の技術を駆使して、製造プロセスの効率化、業務効率化、チームワーク強化、コスト削減、品質向上を実現します。このサービスは、製造業の課題を深く理解し、それに対する最適なデジタルソリューションを提供することで、企業が持続的な成長とイノベーションを達成できるようサポートします。
製造業ニュース解説
製造業、主に購買・調達部門にお勤めの方々に向けた情報を配信しております。
新任の方やベテランの方、管理職を対象とした幅広いコンテンツをご用意しております。
お問い合わせ
コストダウンが利益に直結する術だと理解していても、なかなか前に進めることができない状況。そんな時は、newjiのコストダウン自動化機能で大きく利益貢献しよう!
(β版非公開)