- お役立ち記事
- Fundamentals of finite element method and application to strength design using CAE
月間76,176名の
製造業ご担当者様が閲覧しています*
*2025年3月31日現在のGoogle Analyticsのデータより
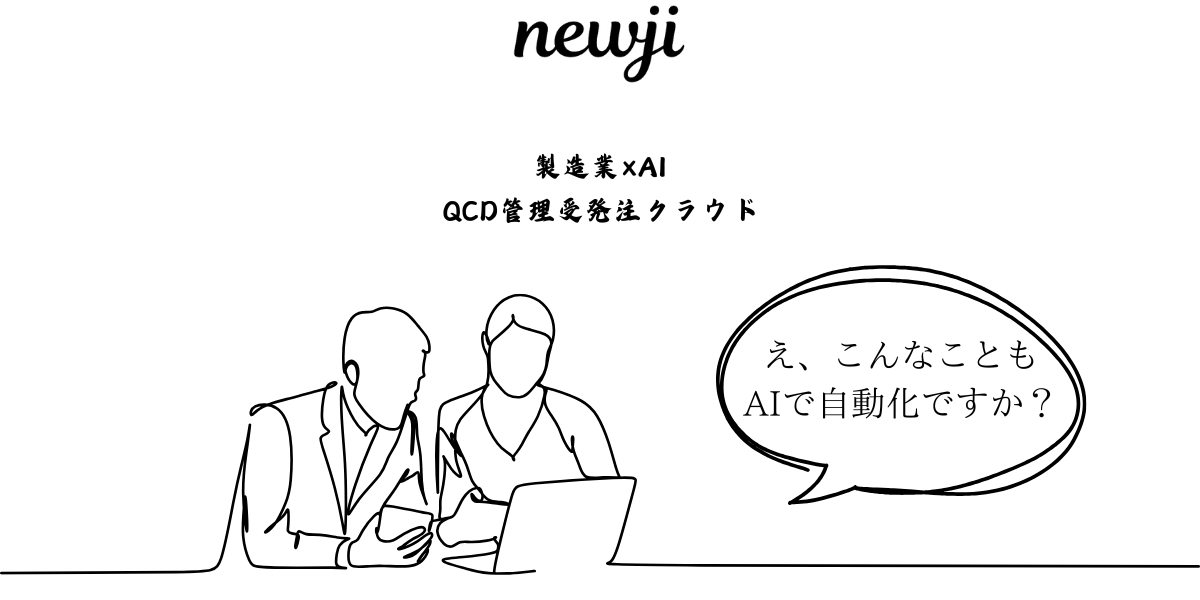
Fundamentals of finite element method and application to strength design using CAE
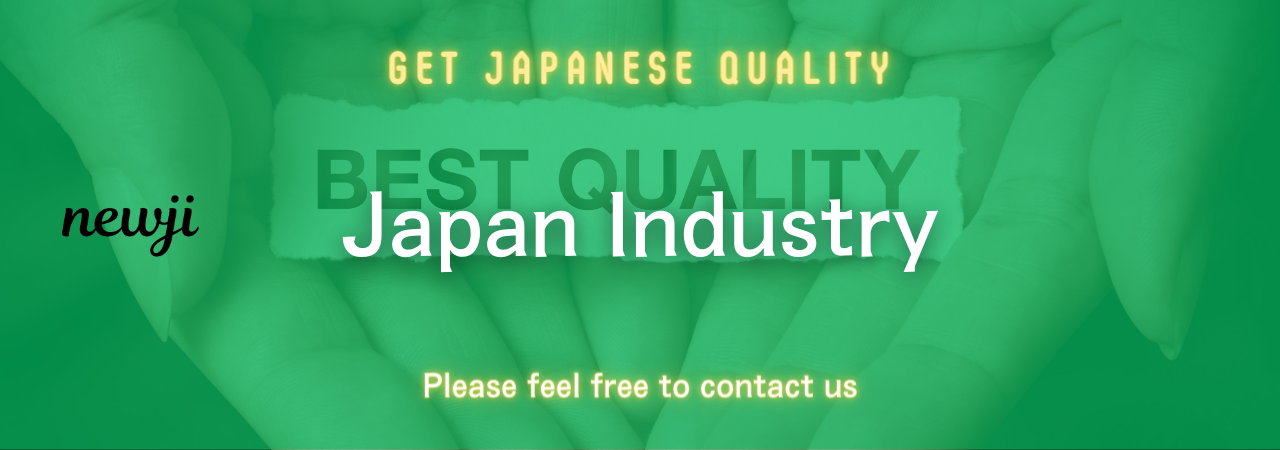
目次
Understanding the Basics of Finite Element Method (FEM)
The Finite Element Method (FEM) is a powerful computational tool used in engineering to find approximate solutions to complex problems.
Fundamentally, FEM breaks down a large, complex problem into smaller, simpler parts known as finite elements.
These elements are connected at various points called nodes.
This method is especially useful in fields such as structural analysis, heat transfer, fluid dynamics, and electromagnetic potential.
The Importance of Discretization
At the heart of FEM lies the concept of discretization, which transforms a continuous domain into a finite number of discrete parts.
Imagine wanting to analyze a material’s stress distribution.
Directly solving the physics in continuous form is often impossible with complex shapes.
Discretization allows you to convert these shapes into a meshgrid of elements, which can be analyzed using mathematical models.
Mathematical Foundation of FEM
FEM operates on the principle of energy minimization.
For mechanical problems, this often involves minimizing potential energy.
Typical equations used are differential equations that describe physical phenomena.
The solution to these equations provides approximate results for each element.
The compilation of these results into a single system provides an overall solution to the model.
The Galerkin method is frequently employed in FEM, which utilizes weighted residual methods to form approximation functions.
This helps interpolate the results between nodes, leading to more precise solutions.
Application of FEM in CAE for Strength Design
Computer-Aided Engineering (CAE) uses FEM extensively for strength design in various engineering disciplines.
This application is critical for both testing and refining designs before physical prototypes are made.
Structural Analysis and Design
In structural engineering, FEM is instrumental in simulating real-world stresses and displacements in materials.
Designers can test how structures like bridges and buildings react to different forces without physically constructing them.
These simulations help predict failure points, allowing for improvements in design that optimize material use while maintaining safety and integrity.
Finite element analysis (FEA) helps in evaluating static and dynamic properties of a design, including load-carrying capacity and the effect of vibration or dynamic loading.
Benefits of FEM in CAE
The integration of FEM with CAE offers numerous advantages:
1. **Accuracy in Predictions**: By using FEM, engineers gain precise insights into how designs will perform under physical constraints.
2. **Optimization**: Allows for iterative testing of designs, leading to optimal configurations that meet strength requirements while minimizing material usage.
3. **Cost Efficiency**: Reduces the need for multiple physical prototypes, thereby saving time and resources.
4. **Versatility**: Easily adapts to various types of analysis, from thermal performance to electrical systems.
5. **Innovation**: Enables engineers to push boundaries by exploring novel materials and geometries that traditional methods cannot assess effectively.
Common Challenges and Solutions
Despite its advantages, FEM can be computationally intensive, especially for large-scale problems.
This requires high-performance computing resources, but advancements in computational power have mitigated this issue significantly.
Understanding the material properties and proper boundary conditions are crucial for accurate modeling.
Errors in meshing or element selection can lead to inaccurate results.
Advanced solvers and preprocessing tools help address these challenges by providing better mesh control and solution algorithms.
Real-World Applications of FEM
Numerous industries utilize FEM for their design and analysis processes.
Aerospace Engineering
In aerospace, FEM aids in understanding the stresses and aerodynamics of aircraft and spacecraft designs.
Given the critical nature of safety in aerospace, FEM ensures the structures can withstand extreme conditions.
Automotive Industry
Automakers leverage FEM to reduce weight while enhancing the safety and performance of vehicles.
This is vital to meet regulatory standards and improve fuel efficiency.
Biomechanical Engineering
FEM models human joints and tissues to predict the impact of medical treatments or the design of medical implants, optimizing patient outcomes.
Conclusion
The Finite Element Method is an indispensable tool in modern engineering.
Its application in strength design through CAE helps refine structures, optimize materials, and reduce costs.
Engineers across industries continue to explore and expand its capabilities, driving innovation and increasing the reliability of engineered systems.
With its foundational principles rooted deeply in mathematical analysis, FEM will undoubtedly remain central to technological advances in the foreseeable future.
資料ダウンロード
QCD管理受発注クラウド「newji」は、受発注部門で必要なQCD管理全てを備えた、現場特化型兼クラウド型の今世紀最高の受発注管理システムとなります。
ユーザー登録
受発注業務の効率化だけでなく、システムを導入することで、コスト削減や製品・資材のステータス可視化のほか、属人化していた受発注情報の共有化による内部不正防止や統制にも役立ちます。
NEWJI DX
製造業に特化したデジタルトランスフォーメーション(DX)の実現を目指す請負開発型のコンサルティングサービスです。AI、iPaaS、および先端の技術を駆使して、製造プロセスの効率化、業務効率化、チームワーク強化、コスト削減、品質向上を実現します。このサービスは、製造業の課題を深く理解し、それに対する最適なデジタルソリューションを提供することで、企業が持続的な成長とイノベーションを達成できるようサポートします。
製造業ニュース解説
製造業、主に購買・調達部門にお勤めの方々に向けた情報を配信しております。
新任の方やベテランの方、管理職を対象とした幅広いコンテンツをご用意しております。
お問い合わせ
コストダウンが利益に直結する術だと理解していても、なかなか前に進めることができない状況。そんな時は、newjiのコストダウン自動化機能で大きく利益貢献しよう!
(β版非公開)