- お役立ち記事
- Fundamentals of finite element method, application to CAE analysis, accuracy improvement measures and their key points
月間77,185名の
製造業ご担当者様が閲覧しています*
*2025年2月28日現在のGoogle Analyticsのデータより
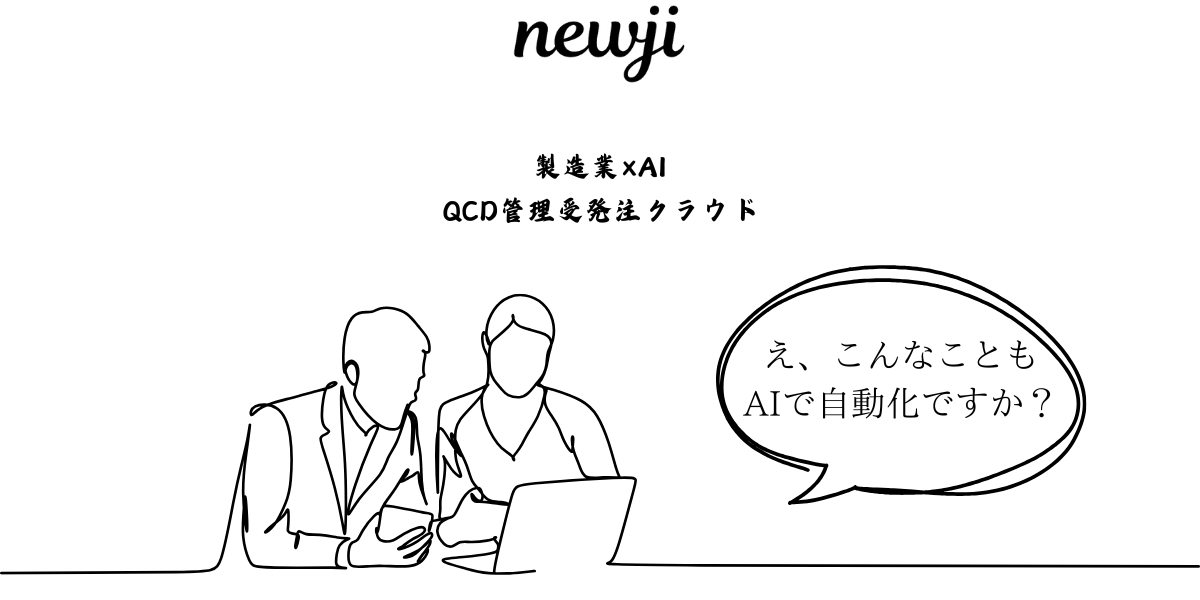
Fundamentals of finite element method, application to CAE analysis, accuracy improvement measures and their key points
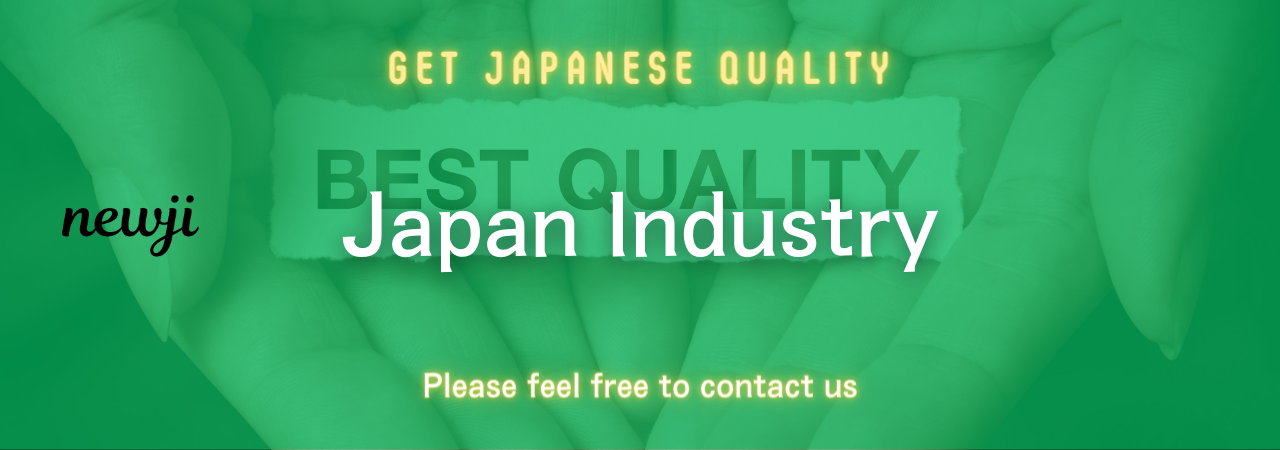
目次
Understanding the Fundamentals of Finite Element Method
The Finite Element Method (FEM) is a powerful computational technique used to solve complex engineering problems.
It plays a pivotal role in predicting how products will react to real-world forces, vibration, heat, fluid flow, and other physical effects.
Fundamentally, FEM breaks down a large, complex system into smaller, simpler parts known as finite elements.
These elements are then analyzed individually and reassembled to predict the performance of the entire system.
Finite Element Analysis (FEA) is synonymous with FEM.
It involves creating a mesh, which is a network of elements and nodes, over the geometry of the physical object.
Once the mesh is established, equations based on the physics of the problem are solved to simulate the behavior of the object under various conditions.
Applications of Finite Element Method in CAE Analysis
Computer-Aided Engineering (CAE) relies heavily on FEM for its diverse applications in various industries.
By allowing engineers to perform simulations, FEM can greatly improve the design and reliability of products without the need for exhaustive physical testing.
Aerospace and Automotive Industries
In aerospace and automotive sectors, FEM is crucial for testing and designing components like airframes, wings, engines, and suspension systems.
It helps in assessing stress and fatigue life, as well as optimizing structures to reduce weight while maintaining strength and safety.
Civil Engineering
For civil engineering, FEM aids in the design of structures such as bridges, dams, and skyscrapers.
It provides insights into load-bearing capacities and helps prevent catastrophic failures by predicting how these structures will react to environmental conditions and usage over time.
Bioengineering
In bioengineering, FEM is utilized to simulate the mechanical behavior of biological tissues.
It assists in designing medical devices, understanding bone fractures, and developing prosthetics by analyzing the interactions between tissues and medical technologies.
Measures for Improving Accuracy in FEM
Accuracy in FEM is pivotal to obtaining reliable results from CAE analyses.
Various measures can be taken to enhance the accuracy of finite element models:
Mesh Refinement
Mesh quality significantly influences the accuracy of FEM results.
Refining the mesh, especially in areas with high gradients of stress or deformation, can lead to more accurate simulations.
Adaptive meshing techniques, where the mesh density adapts based on the solution, can be employed to achieve optimal results.
Material Properties
Another important factor is the accurate representation of material properties.
Incorrect or overly simplified material data can lead to errors.
Incorporating non-linear material properties and considering factors like temperature and strain rate dependency can improve model fidelity.
Boundary Conditions
Correct application of boundary conditions and loads is critical.
Physical constraints should be accurately modeled to reflect real-world scenarios.
Mischaracterized boundary conditions often result in significant deviations from expected outcomes.
Validation and Verification
Validating the simulation model against experimental or already known results is essential to ensure the reliability of FEM outcomes.
Verification, which involves checking that the model is implemented correctly, also plays a crucial role in improving accuracy.
Key Points for Successful FEM Implementation
For the successful implementation of FEM, there are several key points to keep in mind:
Understanding the Problem
A thorough understanding of the problem at hand ensures the correct formulation of the finite element model.
Defining the scope, objectives, and assumptions appropriately sets the foundation for credible simulations.
Software and Hardware
Choosing the right FEM software and ensuring sufficient computational resources are paramount.
Advanced software with capabilities for multi-physics simulations and user-friendly interfaces enhances productivity.
Likewise, powerful hardware reduces computation times and allows for more complex analyses.
Skills and Expertise
Skilled personnel with expertise in both FEM and the specific field of application are indispensable.
They can make informed decisions about modeling techniques, result interpretation, and validation processes.
Iterative Process
FEM is often an iterative process.
Starting with simplified models and gradually increasing complexity allows for better management of uncertainties and refinements.
Iteration helps in honing the model and improving the accuracy of results.
In conclusion, the Finite Element Method is an indispensable tool in modern engineering, enabling detailed analysis and design optimization for diverse applications.
By focusing on mesh refinement, accurate material properties, boundary conditions, and a robust validation process, engineers can harness the full power of FEM to produce reliable and insightful CAE analyses.
資料ダウンロード
QCD管理受発注クラウド「newji」は、受発注部門で必要なQCD管理全てを備えた、現場特化型兼クラウド型の今世紀最高の受発注管理システムとなります。
ユーザー登録
受発注業務の効率化だけでなく、システムを導入することで、コスト削減や製品・資材のステータス可視化のほか、属人化していた受発注情報の共有化による内部不正防止や統制にも役立ちます。
NEWJI DX
製造業に特化したデジタルトランスフォーメーション(DX)の実現を目指す請負開発型のコンサルティングサービスです。AI、iPaaS、および先端の技術を駆使して、製造プロセスの効率化、業務効率化、チームワーク強化、コスト削減、品質向上を実現します。このサービスは、製造業の課題を深く理解し、それに対する最適なデジタルソリューションを提供することで、企業が持続的な成長とイノベーションを達成できるようサポートします。
製造業ニュース解説
製造業、主に購買・調達部門にお勤めの方々に向けた情報を配信しております。
新任の方やベテランの方、管理職を対象とした幅広いコンテンツをご用意しております。
お問い合わせ
コストダウンが利益に直結する術だと理解していても、なかなか前に進めることができない状況。そんな時は、newjiのコストダウン自動化機能で大きく利益貢献しよう!
(β版非公開)