- お役立ち記事
- Fundamentals of finite element method CAE analysis and application to strength design
月間77,185名の
製造業ご担当者様が閲覧しています*
*2025年2月28日現在のGoogle Analyticsのデータより
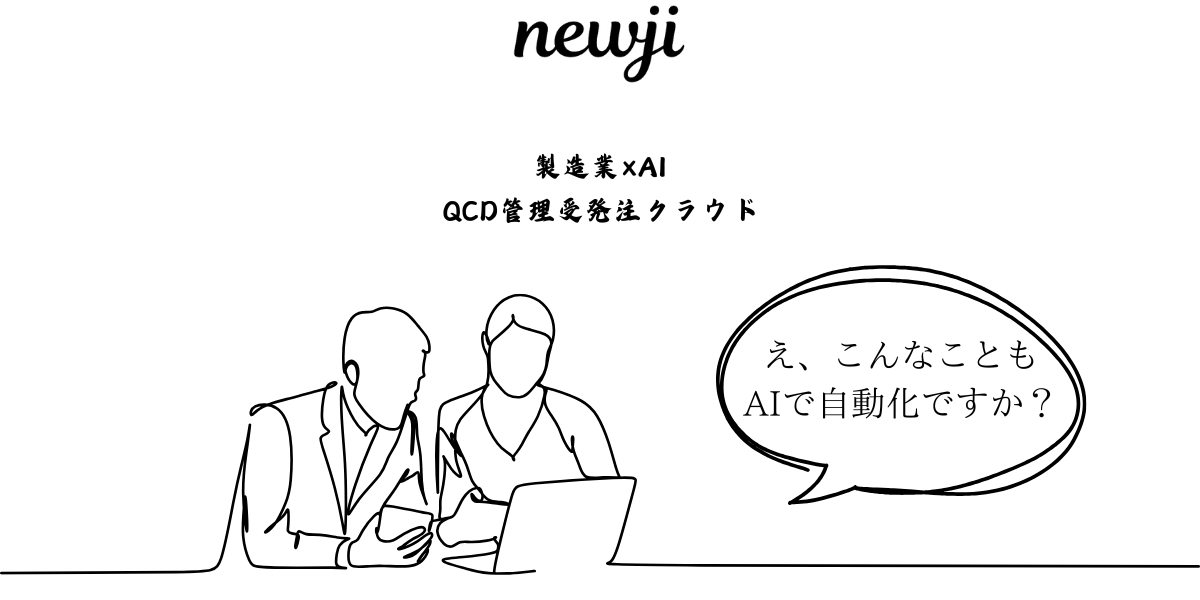
Fundamentals of finite element method CAE analysis and application to strength design
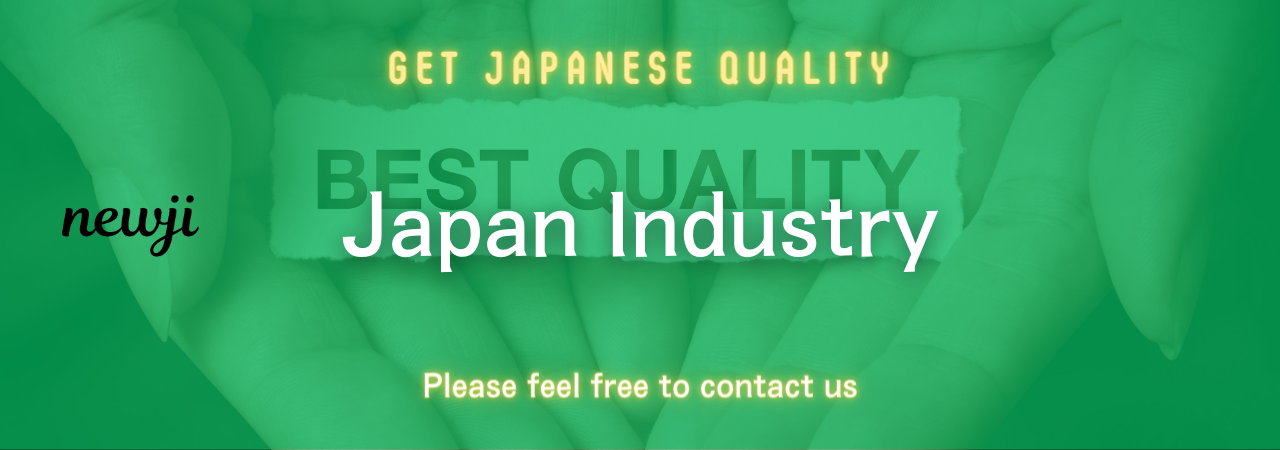
目次
Introduction to Finite Element Method (FEM) in CAE Analysis
The finite element method (FEM) is a powerful computational technique used in computer-aided engineering (CAE) analysis.
It is designed to solve complex structural, thermal, and electromagnetic problems by subdividing a large system into smaller, simpler parts called finite elements.
These finite elements are interconnected at points known as nodes.
By breaking down a complex problem into manageable elements, engineers can simulate real-world conditions with great accuracy.
FEM is widely employed in various industries, including aerospace, automotive, civil engineering, and consumer electronics.
Understanding the Fundamentals of FEM
To effectively use the finite element method, it is imperative to comprehend its basic principles and components.
This understanding enables engineers to apply FEM analysis to design processes efficiently, enhancing product quality and performance.
Discretization of the Domain
One of the primary steps in FEM is the discretization of the domain.
This process involves dividing a complex geometry into smaller elements, which can be of various shapes such as triangles, quadrilaterals, tetrahedrons, or hexahedrons.
The choice of element shape and size significantly impacts the accuracy and computational cost of the analysis.
Different types of elements are used depending on the nature of the problem.
For instance, 1D elements are used for line-like structures, 2D elements for surface structures, and 3D elements for volumetric structures.
Formulation of Element Equations
Once the domain is discretized, the next step is formulating the element equations.
This involves creating mathematical models that capture the behavior of each element based on governing equations, such as the equations of motion, heat conduction, or electromagnetic field equations.
Each element is governed by these localized equations, derived using principles from physics.
Assembly of Global System Equations
The locally defined element equations are then assembled into a global system of equations.
The global equations take into account the interconnectivity of the elements through the shared nodes.
The objective is to represent the entire structure or system in terms of these assembled equations.
In solving the global system, boundary conditions and initial conditions are also incorporated to ensure the results are applicable to the real-world scenario.
Solution of the Global System
Solving the global system of equations is a critical step in FEM analysis.
Typically, numerical methods, such as the Gaussian elimination or iterative solvers, are used to find approximate solutions to these equations.
The accuracy of the FEM solution depends on the numerical method employed and the quality of the discretization.
Application of FEM in Strength Design
The finite element method is extensively applied in the strength design of components.
By simulating the performance and behavior of a product under various loads and conditions, engineers can optimize designs to ensure durability, safety, and compliance with standards.
Structural Analysis
Structural analysis is one of the most common applications of FEM in strength design.
By analyzing the stresses and deformations of structures under different loads (such as forces, pressures, or moments), engineers can identify potential failure points and redesign the structure to enhance its strength and stability.
Thermal Analysis
In thermal analysis, FEM is used to study how heat transfer affects a structure or component.
It helps in predicting temperature distributions, identifying thermal hotspots, and optimizing thermal management strategies.
This is particularly important for components subjected to high temperatures or significant thermal cycles.
Vibration Analysis
Vibration analysis is essential in ensuring that components remain stable under dynamic conditions.
By using FEM, engineers can evaluate the natural frequencies and mode shapes of a component, preventing resonance phenomena which can lead to catastrophic failures.
This application is particularly crucial in the design of mechanical systems, automotive parts, and aerospace components.
Fatigue and Fracture Analysis
FEM is also valuable in predicting the lifespan of components subjected to cyclic loading, known as fatigue analysis.
Engineers can simulate the propagation of cracks and potential fracture points, allowing for proactive design improvements.
This type of analysis is critical in industries where component failure can have severe safety or financial repercussions.
Conclusion
The finite element method is an indispensable tool in computer-aided engineering analysis and strength design.
Its ability to provide accurate simulations of real-world behavior makes it invaluable in various industries, enhancing product performance, safety, and reliability.
By mastering the fundamentals of FEM, engineers can effectively apply this method to tackle complex design challenges and innovate in their respective fields.
資料ダウンロード
QCD管理受発注クラウド「newji」は、受発注部門で必要なQCD管理全てを備えた、現場特化型兼クラウド型の今世紀最高の受発注管理システムとなります。
ユーザー登録
受発注業務の効率化だけでなく、システムを導入することで、コスト削減や製品・資材のステータス可視化のほか、属人化していた受発注情報の共有化による内部不正防止や統制にも役立ちます。
NEWJI DX
製造業に特化したデジタルトランスフォーメーション(DX)の実現を目指す請負開発型のコンサルティングサービスです。AI、iPaaS、および先端の技術を駆使して、製造プロセスの効率化、業務効率化、チームワーク強化、コスト削減、品質向上を実現します。このサービスは、製造業の課題を深く理解し、それに対する最適なデジタルソリューションを提供することで、企業が持続的な成長とイノベーションを達成できるようサポートします。
製造業ニュース解説
製造業、主に購買・調達部門にお勤めの方々に向けた情報を配信しております。
新任の方やベテランの方、管理職を対象とした幅広いコンテンツをご用意しております。
お問い合わせ
コストダウンが利益に直結する術だと理解していても、なかなか前に進めることができない状況。そんな時は、newjiのコストダウン自動化機能で大きく利益貢献しよう!
(β版非公開)