- お役立ち記事
- Fundamentals of finite element method in CAE and application to structural analysis
月間77,185名の
製造業ご担当者様が閲覧しています*
*2025年2月28日現在のGoogle Analyticsのデータより
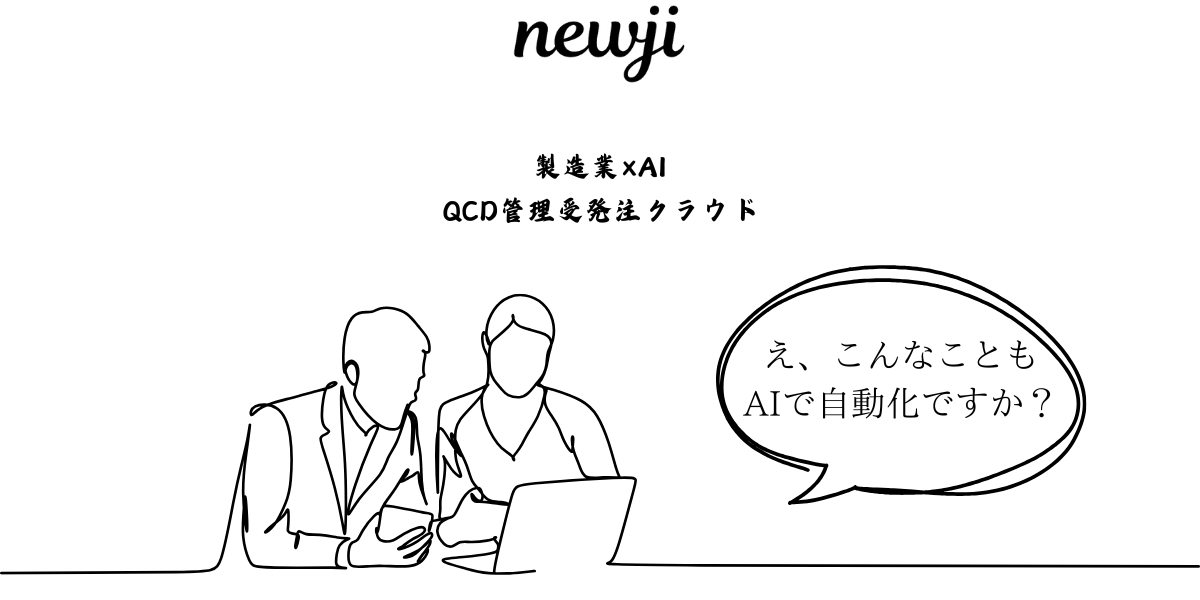
Fundamentals of finite element method in CAE and application to structural analysis
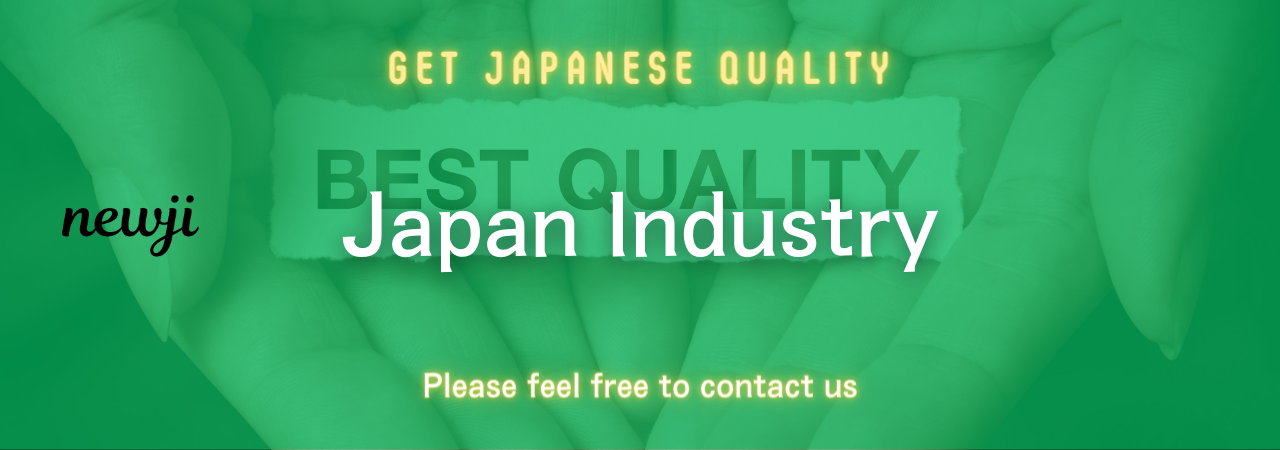
目次
Understanding the Basics of CAE
Computer-Aided Engineering, or CAE, is a broad field that encompasses the use of computer software to aid in engineering tasks.
These tasks can range from simulation, validation, and optimization of products and manufacturing tools.
One of the significant techniques used in CAE is the Finite Element Method (FEM).
FEM is an essential part of CAE as it allows engineers to simulate physical phenomena using mathematical models.
This technique breaks down complex structures into smaller, more manageable pieces called elements.
Because of its versatility, FEM is used in various industries, including automotive, aerospace, and civil engineering.
What is the Finite Element Method?
The Finite Element Method is a numerical technique for solving problems in engineering and mathematical physics.
It is particularly useful for problems where the geometry is complicated, material properties are complex, and where the physical loading conditions are challenging.
In FEM, an object is divided into a finite number of sub-units or ‘elements.’
These elements are interconnected at points called nodes.
Each node is associated with one or more unknown parameters, such as displacement.
The behavior of the nodes can be used to understand how the whole structure behaves.
Historical Development of FEM
FEM originated from the need to solve complex elasticity and structural analysis problems in civil and aeronautical engineering.
The method initially gained traction in the 1950s through the work of engineers like Ray Clough.
Over the subsequent decades, advancements in computer technology have allowed FEM techniques to become even more sophisticated and widely applicable.
How FEM Works
To perform an analysis using FEM, the first step is to create a geometric representation of the structure.
This representation is then used to generate a finite element model that incorporates the material properties, boundary conditions, and applied loads.
Once the model is set up, it is discretized into elements and nodes.
The behavior of these elements is governed by differential equations, which are then converted into algebraic equations using numerical methods.
These equations are assembled into a larger system that represents the entire structure.
Solving this system of equations provides the values of unknown parameters at each node, which helps predict the structure’s response to external influences.
Mesh Generation
A crucial aspect of FEM is mesh generation, which involves dividing the geometry into smaller elements.
The quality of the mesh can significantly impact the accuracy of the results.
A finer mesh, with smaller elements, generally produces more accurate results but requires more computational resources.
Material Properties and Boundary Conditions
Another critical component of FEM analysis is defining material properties and boundary conditions.
Material properties include characteristics such as elasticity, density, and thermal conductivity.
Boundary conditions specify how the model is constrained or loaded, influencing how the simulated structure behaves under different scenarios.
Applications of FEM in Structural Analysis
FEM is particularly powerful in structural analysis, which involves evaluating the strength and stability of structures under various loads.
This application is vital in multiple fields, including the design of bridges, buildings, aircraft, and automobiles.
Stress and Strain Analysis
One of the primary uses of FEM in structural analysis is stress and strain analysis.
Engineers use FEM to predict how a structure will react to external loads, such as forces or pressures.
By understanding these reactions, engineers can design structures that are safe and efficient, ensuring they can withstand anticipated loads without failure.
Dynamic Analysis
Dynamic analysis is another area where FEM is extensively used.
This type of analysis is crucial for structures subject to dynamic loads, such as earthquakes or impacts.
By simulating how these dynamic loads affect structures, FEM helps engineers design buildings and other constructions that can resist such forces, thereby protecting lives and maintaining structural integrity.
Thermal Analysis
FEM is also used for thermal analysis, which examines how structures respond to temperature changes.
This is particularly important in fields like electronics and aerospace, where thermal management is critical for system performance and reliability.
Advantages of Using FEM
There are several advantages to using FEM in CAE, particularly in structural analysis.
Precision and Flexibility
FEM allows for precise modeling of complex geometries and material properties.
It provides flexibility in testing various design scenarios and modifications without requiring physical prototypes.
Cost-Effectiveness
While setting up FEM models requires computational resources, it is often more cost-effective than traditional testing methods.
This reduces the need for building multiple prototypes, saving both time and money.
Challenges and Considerations
Despite its advantages, FEM also has its challenges.
Building accurate and reliable models can be time-consuming and requires a good understanding of the physics and mathematics involved.
Moreover, the solutions to FEM models can sometimes be computationally expensive, requiring significant processing power and memory.
Conclusion
The Finite Element Method is integral to modern engineering, providing critical insights into the behavior of structures under various conditions.
While there are challenges in its application, the benefits, such as precision and cost-effectiveness, make it an invaluable tool in the engineering domain.
As technology advances, the capabilities and applications of FEM in CAE will continue to expand, driving innovations across industries.
資料ダウンロード
QCD管理受発注クラウド「newji」は、受発注部門で必要なQCD管理全てを備えた、現場特化型兼クラウド型の今世紀最高の受発注管理システムとなります。
ユーザー登録
受発注業務の効率化だけでなく、システムを導入することで、コスト削減や製品・資材のステータス可視化のほか、属人化していた受発注情報の共有化による内部不正防止や統制にも役立ちます。
NEWJI DX
製造業に特化したデジタルトランスフォーメーション(DX)の実現を目指す請負開発型のコンサルティングサービスです。AI、iPaaS、および先端の技術を駆使して、製造プロセスの効率化、業務効率化、チームワーク強化、コスト削減、品質向上を実現します。このサービスは、製造業の課題を深く理解し、それに対する最適なデジタルソリューションを提供することで、企業が持続的な成長とイノベーションを達成できるようサポートします。
製造業ニュース解説
製造業、主に購買・調達部門にお勤めの方々に向けた情報を配信しております。
新任の方やベテランの方、管理職を対象とした幅広いコンテンツをご用意しております。
お問い合わせ
コストダウンが利益に直結する術だと理解していても、なかなか前に進めることができない状況。そんな時は、newjiのコストダウン自動化機能で大きく利益貢献しよう!
(β版非公開)