- お役立ち記事
- Fundamentals of fluid analysis using the finite volume method and application to fluid-structure interaction analysis using parallel calculations
月間76,176名の
製造業ご担当者様が閲覧しています*
*2025年3月31日現在のGoogle Analyticsのデータより
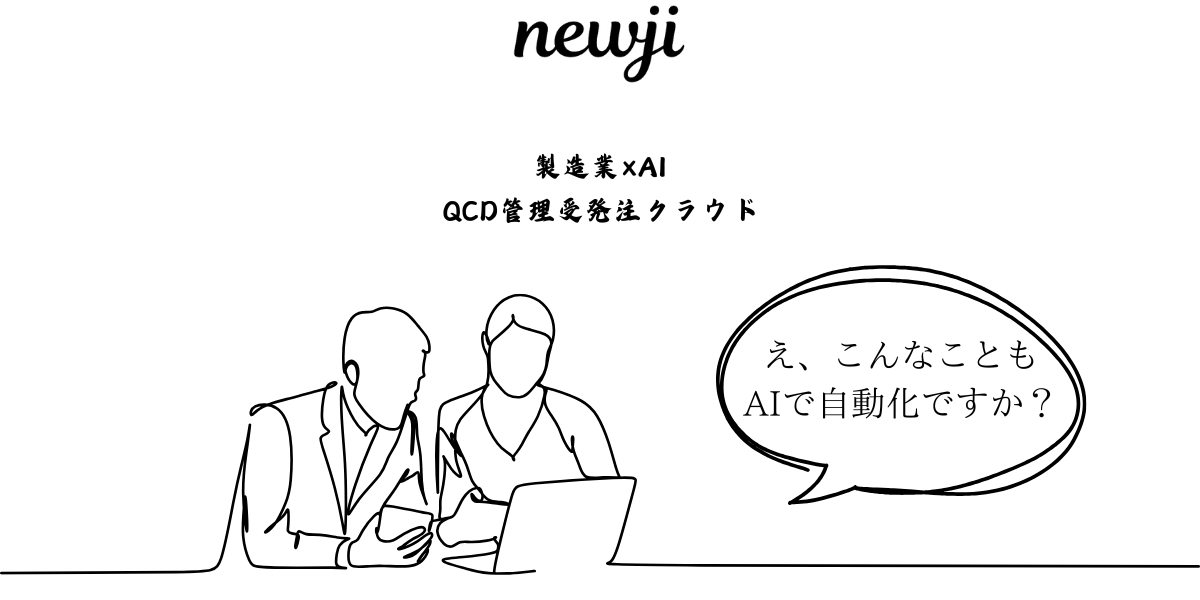
Fundamentals of fluid analysis using the finite volume method and application to fluid-structure interaction analysis using parallel calculations
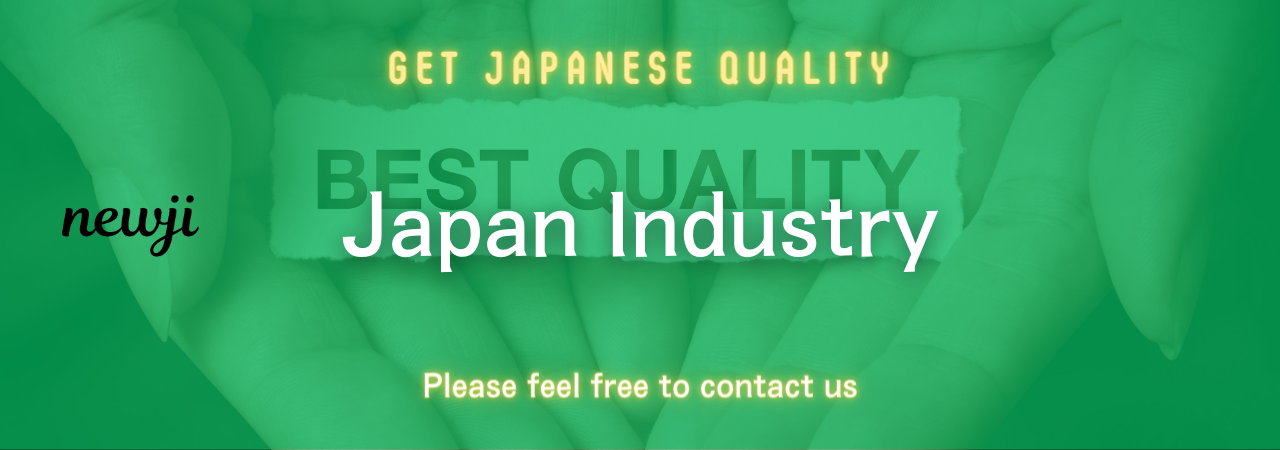
Fluid analysis plays a critical role in understanding how fluids behave under various conditions, which is essential in fields ranging from engineering to environmental science.
The finite volume method (FVM) is one of the most popular techniques for performing fluid analysis due to its robustness and versatility.
Specifically, it is highly effective in solving fluid dynamics problems and can be adapted for complex simulations such as fluid-structure interactions.
目次
What is the Finite Volume Method?
The finite volume method is a numerical approach used to solve partial differential equations that arise in fluid dynamics.
Unlike other methods such as finite difference or finite element, FVM focuses on the integral form of the conservation laws rather than their differential form.
This allows it to naturally conserve quantities like mass, momentum, and energy, which makes it particularly suited for fluid flow problems.
The main idea behind FVM is to divide the domain of interest into small control volumes or cells.
The fluxes of conserved variables are then computed at the faces of each control volume.
By ensuring that the net flux across each control volume is balanced, FVM maintains the conservation laws inherent in fluid dynamics.
Steps Involved in the Finite Volume Method
FVM involves several key steps, starting with the discretization of the domain.
This involves dividing the domain into a finite number of control volumes.
Next, the governing equations, like the Navier-Stokes equations, are integrated over each control volume.
This integration leads to algebraic equations that represent the fluxes across the control volume surfaces.
The boundary conditions must also be defined carefully, as they affect the results significantly.
Once the boundary conditions are applied, these algebraic equations are solved iteratively using numerical techniques.
Finally, the solution is assessed for convergence to ensure that it satisfies the physical laws of fluid motion.
Advantages of Using FVM
The finite volume method stands out due to its several advantages:
– **Conservation Properties**: FVM conserves quantities like mass, momentum, and energy, which are critical in fluid dynamics.
– **Adaptability**: It can handle complex geometries, making it convenient for engineering applications.
– **Versatility**: FVM is suitable for a wide range of problems, including multiphase flows and heat transfer.
Application to Fluid-Structure Interaction (FSI) Analysis
Fluid-structure interaction analysis represents a complex domain where the motion of fluids and structures influence each other.
FSI is crucial for designing structures that can withstand fluid forces, be they in aerodynamics, civil engineering, or biomedical fields.
Role of Finite Volume Method in FSI
In FSI analysis, the finite volume method is used to simulate the fluid flow while the structure’s response is calculated using structural analysis methods.
FVM is effective here because it can handle transient and nonlinear fluid behavior, which are essential aspects of FSI problems.
The integration of FVM with structural models usually involves coupling techniques.
Among the common coupling techniques are one-way and two-way coupling.
In one-way coupling, the fluid affects the structure without feedback, whereas, in two-way coupling, both the fluid and structure influence each other.
Two-way coupling is more computationally intensive but provides a more accurate simulation of FSI problems.
Parallel Calculations in Fluid Analysis
With the increasing complexity of fluid analysis and FSI simulations, parallel calculations have become vital.
Parallel calculations involve splitting computations across multiple processors, significantly reducing computation time and enhancing the capability of solving large-scale problems.
Parallel computational techniques leverage the power of distributed and shared-memory architectures, allowing for more efficient processing.
These techniques can be applied in various stages of the FVM, from mesh generation to solving the governing equations.
Benefits of Using Parallel Calculations
– **Increased Efficiency**: Reduces computational time, allowing for quicker results.
– **Scalability**: Capable of handling large and complex simulations that would be infeasible on single processors.
– **Enhanced Precision**: Enables finer mesh resolutions, improving the accuracy of the simulations.
Considerations for Effective Implementation
When implementing FVM for fluid analysis with parallel computing, certain considerations must be taken into account to ensure maximum effectiveness.
Firstly, the choice of discretization and mesh size can significantly impact the accuracy and efficiency of the analysis.
Mesh generation tools should be utilized to produce high-quality meshes that can accurately capture fluid behavior.
Secondly, boundary conditions should be properly defined to accurately reflect the physical environment of the problem.
Inaccurate boundary conditions can lead to significant errors in simulation results.
Lastly, the choice of numerical solvers is important.
Choosing solvers that are well-suited for parallel computing architectures can greatly enhance performance.
Conclusion
The finite volume method is a powerful tool for fluid analysis and forms the basis for many advanced simulations, including fluid-structure interaction analysis.
Its conservation properties and versatility make it ideal for a wide range of applications.
When coupled with parallel calculations, FVM becomes even more powerful, allowing for efficient and accurate simulation of complex fluid problems.
Effective implementation requires careful consideration of discretization, boundary conditions, and numerical solvers, ensuring a precise and efficient analysis.
As computational capabilities continue to grow, the use of FVM in tandem with parallel computing will expand further, opening new frontiers in fluid dynamics research and applications.
資料ダウンロード
QCD管理受発注クラウド「newji」は、受発注部門で必要なQCD管理全てを備えた、現場特化型兼クラウド型の今世紀最高の受発注管理システムとなります。
ユーザー登録
受発注業務の効率化だけでなく、システムを導入することで、コスト削減や製品・資材のステータス可視化のほか、属人化していた受発注情報の共有化による内部不正防止や統制にも役立ちます。
NEWJI DX
製造業に特化したデジタルトランスフォーメーション(DX)の実現を目指す請負開発型のコンサルティングサービスです。AI、iPaaS、および先端の技術を駆使して、製造プロセスの効率化、業務効率化、チームワーク強化、コスト削減、品質向上を実現します。このサービスは、製造業の課題を深く理解し、それに対する最適なデジタルソリューションを提供することで、企業が持続的な成長とイノベーションを達成できるようサポートします。
製造業ニュース解説
製造業、主に購買・調達部門にお勤めの方々に向けた情報を配信しております。
新任の方やベテランの方、管理職を対象とした幅広いコンテンツをご用意しております。
お問い合わせ
コストダウンが利益に直結する術だと理解していても、なかなか前に進めることができない状況。そんな時は、newjiのコストダウン自動化機能で大きく利益貢献しよう!
(β版非公開)