- お役立ち記事
- Fundamentals of fluid mechanics, vortex control, and flow resistance reduction methods
月間76,176名の
製造業ご担当者様が閲覧しています*
*2025年3月31日現在のGoogle Analyticsのデータより
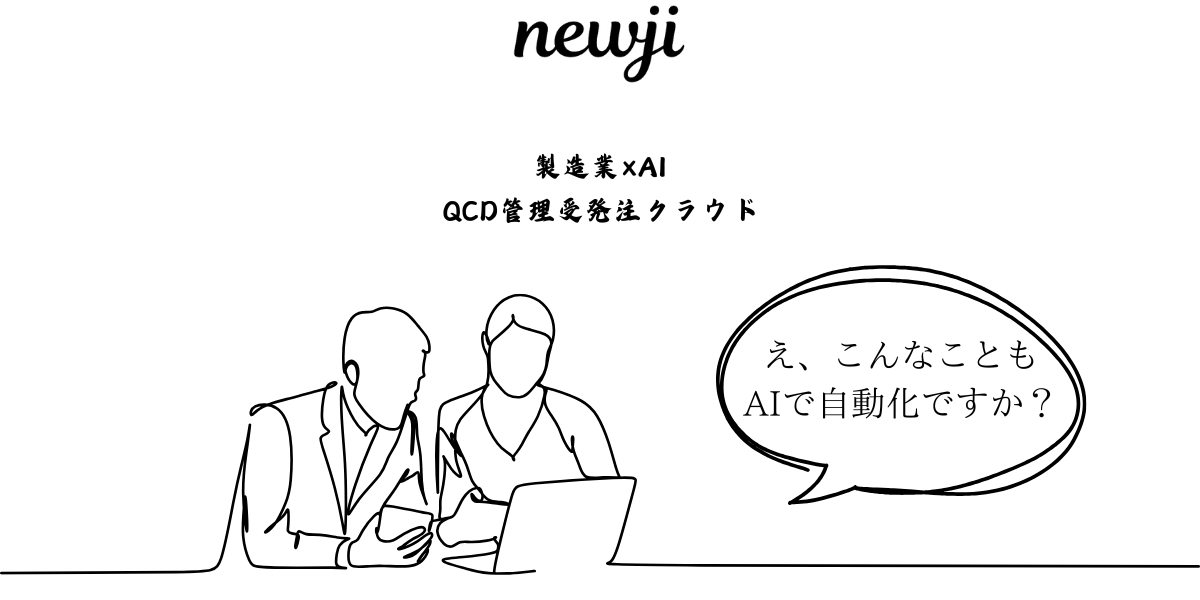
Fundamentals of fluid mechanics, vortex control, and flow resistance reduction methods
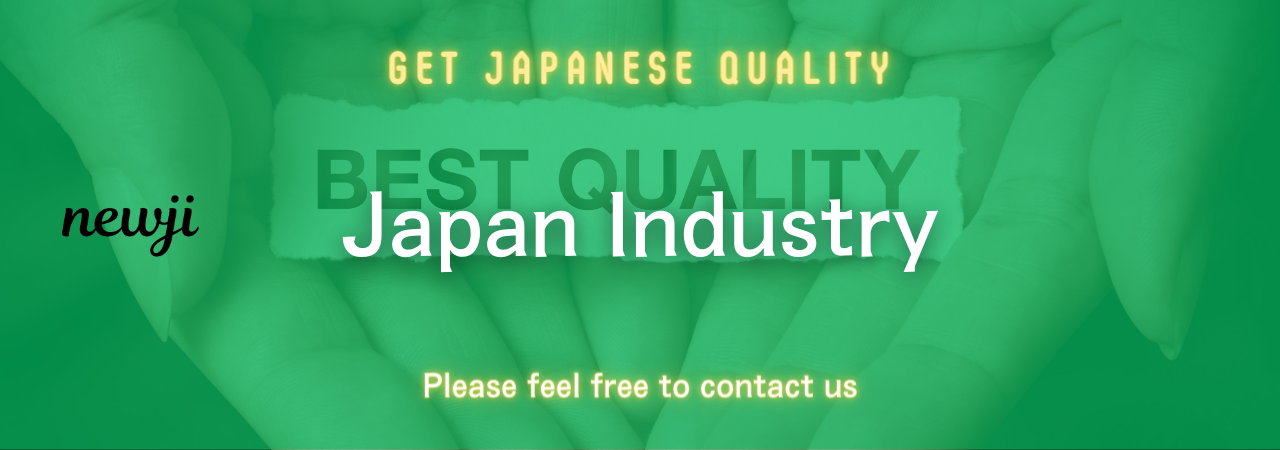
目次
Understanding Fluid Mechanics
Fluid mechanics is a branch of physics concerned with the behavior of fluids (liquids and gases) and the forces acting upon them.
Fundamentally, fluid mechanics can be divided into fluid statics, the study of fluids at rest, and fluid dynamics, the study of fluids in motion.
Grasping these concepts is critical as they apply to numerous fields such as engineering, meteorology, and even medicine.
One of the bedrock principles of fluid mechanics is Bernoulli’s equation.
This principle describes the conservation of energy in streamline flow and helps us understand why there are pressure differences which, among other applications, allow airplanes to fly and filter systems to function effectively.
Another essential concept is viscosity, which measures a fluid’s resistance to gradual deformation by shear or tensile stresses.
Simply put, it is the “thickness” or “internal friction” of the fluid.
While water has low viscosity, honey has a high viscosity.
The Concept of Vortex Control
A vortex is a region in a fluid where a rotating motion occurs, often leading to a spiral-like effect.
Vortex control plays a significant role in fluid mechanics, particularly in minimizing resistance and optimizing the efficient flow of different fluids.
One application of vortex control is in the aerospace industry.
When an aircraft moves, vortices naturally form at the tips of the wings.
These can increase drag and reduce lift.
To counter this, engineers design winglets that help control these vortices, reducing the drag and improving the aircraft’s fuel efficiency.
In automotive design, vortex control techniques are used to enhance the aerodynamics of high-speed vehicles.
By managing airflow to reduce drag and improve stability, designers can ensure vehicles operate efficiently at higher speeds.
Similarly, vortex control is pivotal in improving the performance of marine vessels by optimizing the flow around hulls to reduce drag.
Exploring Flow Resistance Reduction
Reducing flow resistance is crucial in fluid mechanics as it leads to enhanced performance in various systems.
Flow resistance, or drag, directly impacts energy consumption and efficiency in both natural and engineered systems.
The first step in reducing flow resistance is streamlining.
Streamlining involves shaping objects to minimize resistance.
For example, bullet trains are designed with streamlined shapes to move through air rapidly with reduced drag, increasing speed and efficiency.
Another technique involves the use of special coatings or surfaces.
These surfaces are designed to reduce surface friction.
In pipelines, for instance, reducing flow resistance allows for the more efficient transport of oil and gas, minimizing costs and energy usage.
In the case of fluid flow over surfaces, the concept of boundary layers is essential.
A boundary layer is a thin layer of fluid near the surface where viscous forces are significant.
Methods like boundary layer suction can be employed to delay boundary layer separation, reducing drag significantly.
This method is often used in high-speed aircraft and car designs.
Applying Fluid Mechanics in Real-World Scenarios
Fluid mechanics is not just a theoretical concept; it finds applications across various industries.
In the medical field, understanding blood flow through arteries and veins is crucial for diagnosing cardiovascular issues.
Techniques borrowed from fluid mechanics help simulate and analyze blood flow patterns, aiding in surgical planning and the design of medical devices like stents.
In environmental science, fluid mechanics principles help in modeling ocean currents, which are essential for understanding climate patterns and predicting weather changes.
Wind farm layout design also heavily relies on fluid mechanics to optimize turbine placement for maximum energy capture and efficiency.
In the energy sector, optimizing fluid flow in turbines is essential for both wind and hydroelectric power generation.
Better designs lead to higher efficiency and lower operational costs.
The Future of Fluid Mechanics
As we move forward, advancements in computational fluid dynamics (CFD) – the use of computers to simulate fluid flow – are revolutionizing how industries approach problem-solving related to fluid mechanics.
CFD allows for complex simulations that were previously impossible, improving design efficiency and reducing the time needed for physical testing.
The integration of artificial intelligence and machine learning in fluid mechanics is another promising development.
These technologies offer predictive analysis, optimizing designs even further by learning from vast datasets to predict the outcomes of fluid interactions before physical testing.
Furthermore, with increasing environmental concerns, fluid mechanics will continue playing a vital role in innovating sustainable solutions.
Whether it’s improving fuel efficiencies in vehicles or designing effective water treatment systems, the field is poised to offer solutions for some of the most pressing global challenges.
In summary, fluid mechanics, vortex control, and flow resistance reduction are intertwined concepts that provide the foundation for numerous practical applications.
From everyday technologies to cutting-edge research areas, the implications of advancements in these fields are vast and transformative.
資料ダウンロード
QCD管理受発注クラウド「newji」は、受発注部門で必要なQCD管理全てを備えた、現場特化型兼クラウド型の今世紀最高の受発注管理システムとなります。
ユーザー登録
受発注業務の効率化だけでなく、システムを導入することで、コスト削減や製品・資材のステータス可視化のほか、属人化していた受発注情報の共有化による内部不正防止や統制にも役立ちます。
NEWJI DX
製造業に特化したデジタルトランスフォーメーション(DX)の実現を目指す請負開発型のコンサルティングサービスです。AI、iPaaS、および先端の技術を駆使して、製造プロセスの効率化、業務効率化、チームワーク強化、コスト削減、品質向上を実現します。このサービスは、製造業の課題を深く理解し、それに対する最適なデジタルソリューションを提供することで、企業が持続的な成長とイノベーションを達成できるようサポートします。
製造業ニュース解説
製造業、主に購買・調達部門にお勤めの方々に向けた情報を配信しております。
新任の方やベテランの方、管理職を対象とした幅広いコンテンツをご用意しております。
お問い合わせ
コストダウンが利益に直結する術だと理解していても、なかなか前に進めることができない状況。そんな時は、newjiのコストダウン自動化機能で大きく利益貢献しよう!
(β版非公開)