- お役立ち記事
- Fundamentals of Forming Simulation Critical in Press Processing
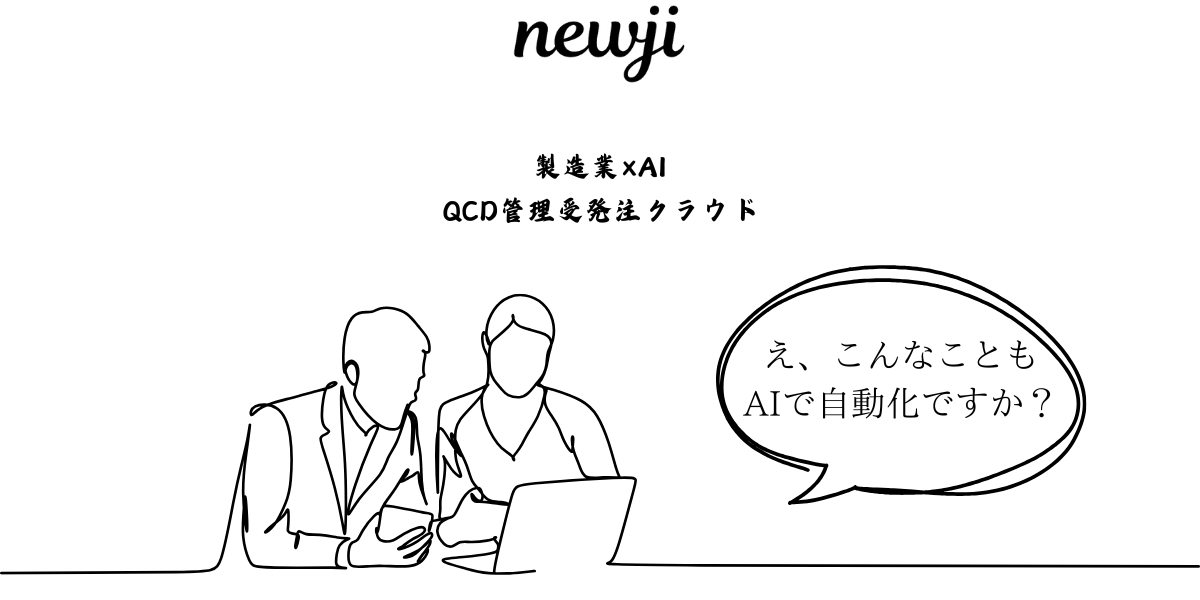
Fundamentals of Forming Simulation Critical in Press Processing
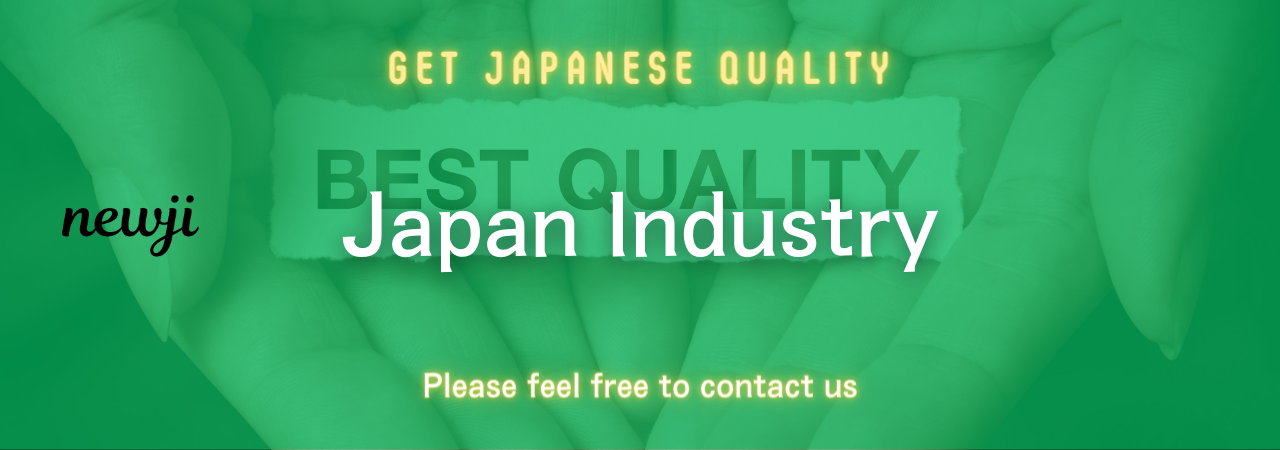
In the world of modern manufacturing, press processing plays a crucial role.
It’s the method by which materials, usually metals, are formed into desired shapes through the application of pressure.
However, understanding and predicting the outcomes of such processes can be challenging.
That’s where forming simulations become essential.
They help in visualizing and planning how materials will behave under certain conditions.
Let’s delve into the fundamentals of forming simulation and why it’s critical in press processing.
目次
What is Forming Simulation?
Forming simulation is a computer-aided process that predicts the deformation and behavior of materials under certain conditions.
It employs mathematical models and finite element analysis (FEA) to mimic the physical processes of press forming, bending, stretching, and other deformation methods.
By doing so, manufacturers can foresee potential issues and optimize their processes before actual production begins.
Importance of Forming Simulation in Press Processing
Cost Reduction
One of the primary benefits of forming simulation is cost reduction.
By predicting how the material will behave, manufacturers can minimize waste and avoid costly trial-and-error methods.
Every scrap of metal that is not utilized translates to wasted resources and added expenses.
Forming simulation allows companies to make more informed decisions, saving on material costs.
Improved Quality
Forming simulation aids in achieving better quality in the final product.
By understanding the material behavior, manufacturers can anticipate defects such as wrinkling, tearing, or improper thickness distribution.
This foresight enables adjustments to be made before actual production, ensuring a higher quality end product.
Time Efficiency
The traditional approach to resolving forming issues often involves making and testing multiple prototypes.
This process can be time-consuming.
With forming simulation, potential problems can be identified and resolved in the virtual environment, significantly speeding up the development cycle.
This time efficiency translates to a faster time-to-market for products.
Key Components of Forming Simulation
Material Models
Material models are at the core of forming simulation.
They describe the properties and behaviors of the materials being simulated.
These models must be accurate to ensure realistic simulations.
Different materials, such as steel, aluminum, and composite materials, require different models to account for their unique properties.
Finite Element Analysis (FEA)
FEA is a computational technique used to approximate the behavior of materials under various conditions.
The material being studied is divided into a finite number of elements.
Equations based on physical laws are then solved for each element, providing a detailed picture of how the material will behave.
FEA is crucial for understanding complex interactions in press processing.
Tool Design
The design of the tools and dies used in press processing significantly impacts the final product’s quality and accuracy.
Forming simulation allows for the optimization of these tools before they are physically manufactured.
This step is essential to ensure that the tools will perform as expected and produce the desired outcomes.
Applications of Forming Simulation
Automotive Industry
In the automotive sector, forming simulation plays a vital role in designing and manufacturing various components.
Automakers rely on forming simulation to develop body panels, chassis, and other parts, ensuring they meet safety and performance standards.
By simulating press processes, manufacturers can achieve the desired strength and weight specifications efficiently.
Aerospace Industry
The aerospace industry demands high precision and performance from its components.
Forming simulation helps in the development of aircraft parts, ensuring they can withstand extreme conditions while being lightweight.
Aerospace engineers use simulations to refine processes and materials, resulting in safer and more efficient aircraft.
Consumer Electronics
In consumer electronics, forming simulation aids in the production of casing and structural components.
With the increasing trend towards miniaturization, having precise forming processes becomes even more critical.
Simulations allow companies to innovate and produce more durable, lighter, and more aesthetically pleasing products.
Challenges in Forming Simulation
Accurate Material Data
One of the critical challenges in forming simulation is obtaining accurate material data.
The simulations are only as good as the material models they use.
A slight deviation in material properties can lead to significant errors in the simulation results.
Therefore, it’s crucial to have precise and comprehensive material characterization.
Computational Complexity
Forming simulations, especially for complex parts, can be computationally intensive.
This complexity requires powerful computers and efficient algorithms to handle the calculations within a reasonable time frame.
As technology advances, these computational challenges are gradually being mitigated, but they remain a consideration.
Integration with Manufacturing Processes
Integrating forming simulation with actual manufacturing processes can sometimes be challenging.
The transition from a virtual environment to real-world application requires careful consideration of various factors.
Ensuring that the simulation accurately mirrors the physical processes needs meticulous calibration and validation.
Forming simulation is an indispensable tool in modern press processing.
It provides manufacturers with valuable insights, enabling them to optimize their processes, reduce costs, and improve product quality.
Despite the challenges, the benefits of forming simulation far outweigh the hurdles, making it a critical component in the manufacturing industry.
As technology continues to evolve, the precision and utility of forming simulations will only improve, heralding a new era of efficiency and innovation in press processing.
資料ダウンロード
QCD調達購買管理クラウド「newji」は、調達購買部門で必要なQCD管理全てを備えた、現場特化型兼クラウド型の今世紀最高の購買管理システムとなります。
ユーザー登録
調達購買業務の効率化だけでなく、システムを導入することで、コスト削減や製品・資材のステータス可視化のほか、属人化していた購買情報の共有化による内部不正防止や統制にも役立ちます。
NEWJI DX
製造業に特化したデジタルトランスフォーメーション(DX)の実現を目指す請負開発型のコンサルティングサービスです。AI、iPaaS、および先端の技術を駆使して、製造プロセスの効率化、業務効率化、チームワーク強化、コスト削減、品質向上を実現します。このサービスは、製造業の課題を深く理解し、それに対する最適なデジタルソリューションを提供することで、企業が持続的な成長とイノベーションを達成できるようサポートします。
オンライン講座
製造業、主に購買・調達部門にお勤めの方々に向けた情報を配信しております。
新任の方やベテランの方、管理職を対象とした幅広いコンテンツをご用意しております。
お問い合わせ
コストダウンが利益に直結する術だと理解していても、なかなか前に進めることができない状況。そんな時は、newjiのコストダウン自動化機能で大きく利益貢献しよう!
(Β版非公開)