- お役立ち記事
- Fundamentals of fracture mechanics and application to fracture prediction using the finite element method
月間76,176名の
製造業ご担当者様が閲覧しています*
*2025年3月31日現在のGoogle Analyticsのデータより
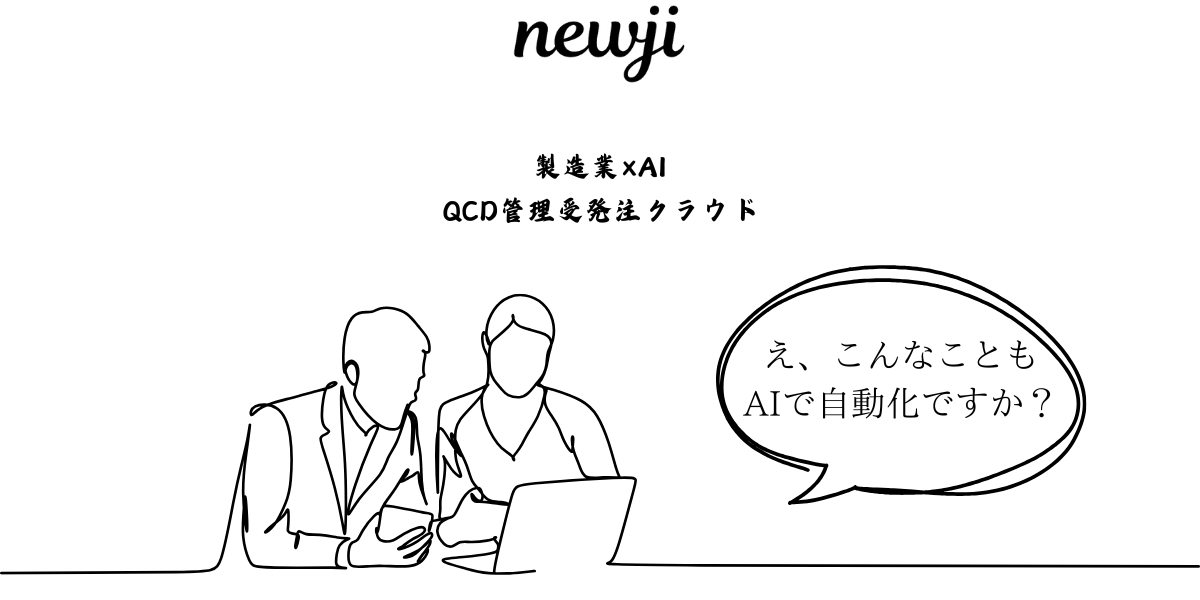
Fundamentals of fracture mechanics and application to fracture prediction using the finite element method
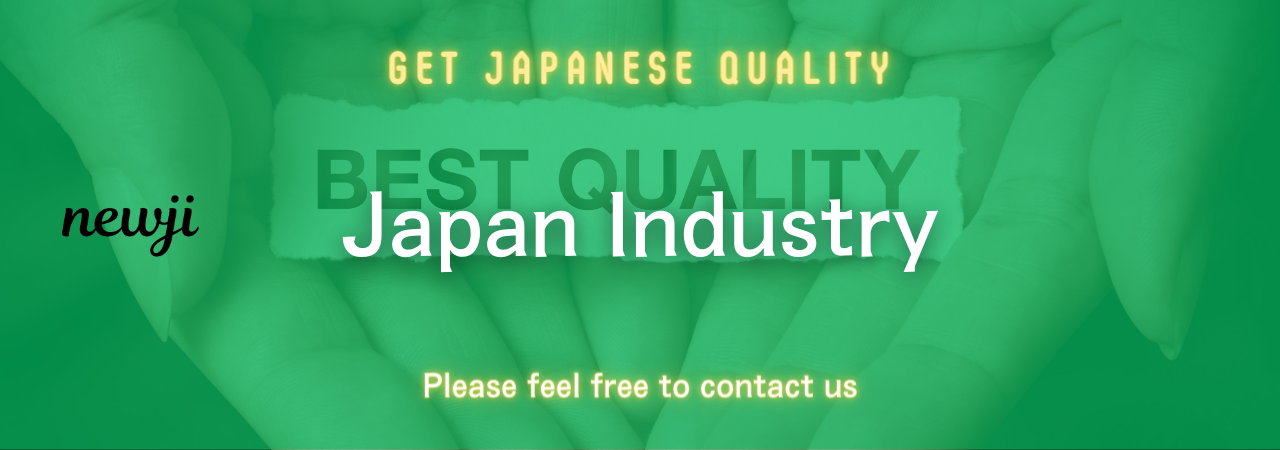
目次
Understanding Fracture Mechanics
Fracture mechanics is an essential field of study in the realm of material science and engineering.
It focuses on understanding the behavior of materials when they are subjected to stress and how fractures propagate through them.
At its core, fracture mechanics aims to predict the conditions under which materials fail or break.
This understanding is crucial for designing structures that are safe, reliable, and efficient.
Fractures can occur in different ways, and understanding these mechanisms is the first step toward predicting and preventing them.
Types of Fractures
Fractures can be broadly classified into two categories: brittle and ductile fractures.
Brittle fractures happen suddenly and without any significant deformation.
Materials like glass and ceramics often exhibit this kind of fracture.
When the stress exceeds a material’s strength, it snaps almost instantaneously.
On the other hand, ductile fractures occur slowly and are preceded by noticeable deformations.
Metals like steel and aluminum demonstrate ductile behavior.
These materials may stretch or bend before eventually failing.
Understanding the type of fracture a material is likely to experience is vital for engineers when they select materials for specific applications.
The Principles of Fracture Mechanics
Fracture mechanics relies on several key principles to predict material failure.
One important concept is the stress intensity factor, which quantifies the stress field near the tip of a crack.
This factor helps in understanding whether a crack will grow or remain stable.
Another crucial concept is the energy release rate.
This measures the amount of energy available for crack propagation.
When the energy release rate exceeds a certain threshold, the crack will advance.
Furthermore, the fracture toughness of a material is a critical property.
It defines a material’s ability to resist fracture in the presence of flaws or cracks.
Materials with high fracture toughness can endure higher stress without fracturing.
Fracture Prediction Using the Finite Element Method
The Finite Element Method (FEM) is a powerful numerical tool used in engineering to understand and predict the behavior of structures under various conditions.
It plays a significant role in fracture mechanics by allowing engineers to simulate the propagation of fractures in materials.
What is the Finite Element Method?
FEM is a computational technique that breaks down a complex structure into smaller, manageable parts called elements.
By solving equations for these elements, engineers can approximate the behavior of the entire structure.
This method allows for a detailed analysis of how materials will respond to applied stresses, helping to predict possible fracture points.
Application of FEM in Fracture Mechanics
In fracture mechanics, FEM can simulate the stress distribution within a material and capture how cracks propagate under various loads.
This ability is invaluable for predicting the life span of components and ensuring their safety and reliability.
FEM can model complex geometries and material behaviors that might be difficult to study using traditional experimental methods.
By creating a detailed simulation, engineers can identify critical stress points and optimize designs to prevent fractures.
Benefits of Using FEM for Fracture Prediction
The application of FEM in fracture mechanics offers several advantages:
1. **Accuracy**: FEM provides a highly accurate representation of stress and strain distributions within materials, allowing for precise predictions of fracture behavior.
2. **Flexibility**: It is adaptable to various materials and structures, accommodating complex geometries and different loading conditions.
3. **Cost-Effectiveness**: Conducting physical experiments to study fracture behavior can be expensive and time-consuming.
FEM simulations reduce the need for costly testing by providing virtual testing environments.
4. **Risk Reduction**: By predicting fractures before they occur, FEM enables the design of safer and more reliable structures, reducing the risk of unexpected failures.
5. **Optimization**: Engineers can use FEM to explore different material configurations and design alternatives, leading to more efficient and robust structures.
Conclusion
Fracture mechanics is a foundational aspect of understanding how and why materials fail.
Its principles are instrumental in predicting and preventing fractures in engineering applications.
By leveraging tools like the Finite Element Method, engineers can simulate fracture behavior and develop more reliable and safe structures.
The accurate predictions and insights provided by FEM help optimize designs, reduce costs, and minimize risks associated with material failure.
Ultimately, the integration of fracture mechanics with computational methods ensures that we build structures that stand the test of time.
資料ダウンロード
QCD管理受発注クラウド「newji」は、受発注部門で必要なQCD管理全てを備えた、現場特化型兼クラウド型の今世紀最高の受発注管理システムとなります。
ユーザー登録
受発注業務の効率化だけでなく、システムを導入することで、コスト削減や製品・資材のステータス可視化のほか、属人化していた受発注情報の共有化による内部不正防止や統制にも役立ちます。
NEWJI DX
製造業に特化したデジタルトランスフォーメーション(DX)の実現を目指す請負開発型のコンサルティングサービスです。AI、iPaaS、および先端の技術を駆使して、製造プロセスの効率化、業務効率化、チームワーク強化、コスト削減、品質向上を実現します。このサービスは、製造業の課題を深く理解し、それに対する最適なデジタルソリューションを提供することで、企業が持続的な成長とイノベーションを達成できるようサポートします。
製造業ニュース解説
製造業、主に購買・調達部門にお勤めの方々に向けた情報を配信しております。
新任の方やベテランの方、管理職を対象とした幅広いコンテンツをご用意しております。
お問い合わせ
コストダウンが利益に直結する術だと理解していても、なかなか前に進めることができない状況。そんな時は、newjiのコストダウン自動化機能で大きく利益貢献しよう!
(β版非公開)