- お役立ち記事
- Fundamentals of fracture mechanics and finite element method and application to fatigue life estimation
月間76,176名の
製造業ご担当者様が閲覧しています*
*2025年3月31日現在のGoogle Analyticsのデータより
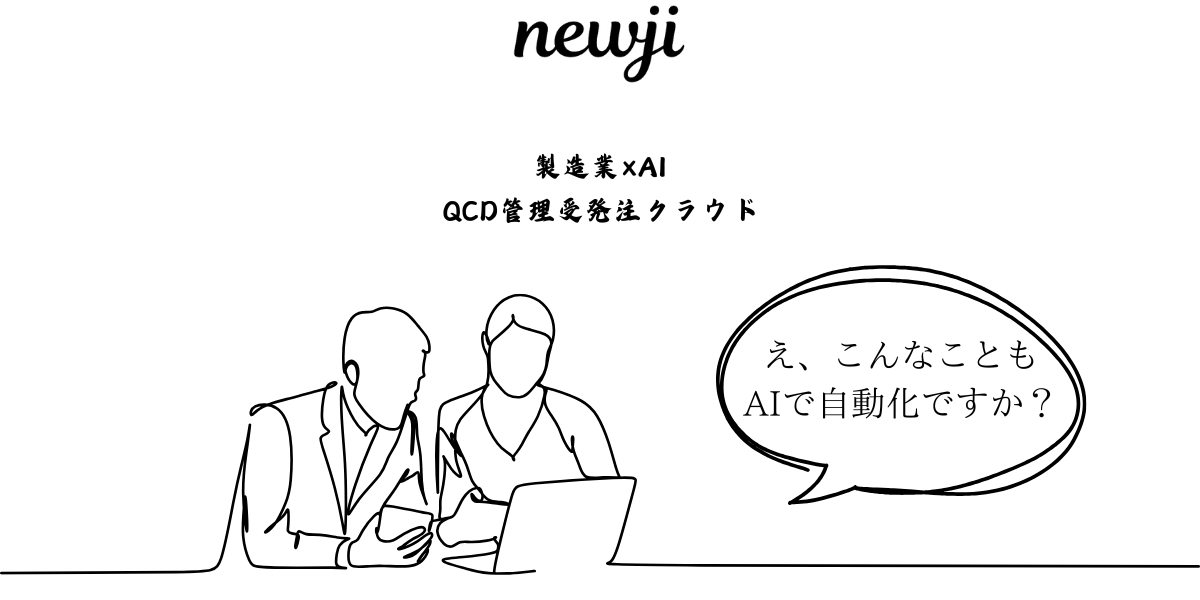
Fundamentals of fracture mechanics and finite element method and application to fatigue life estimation
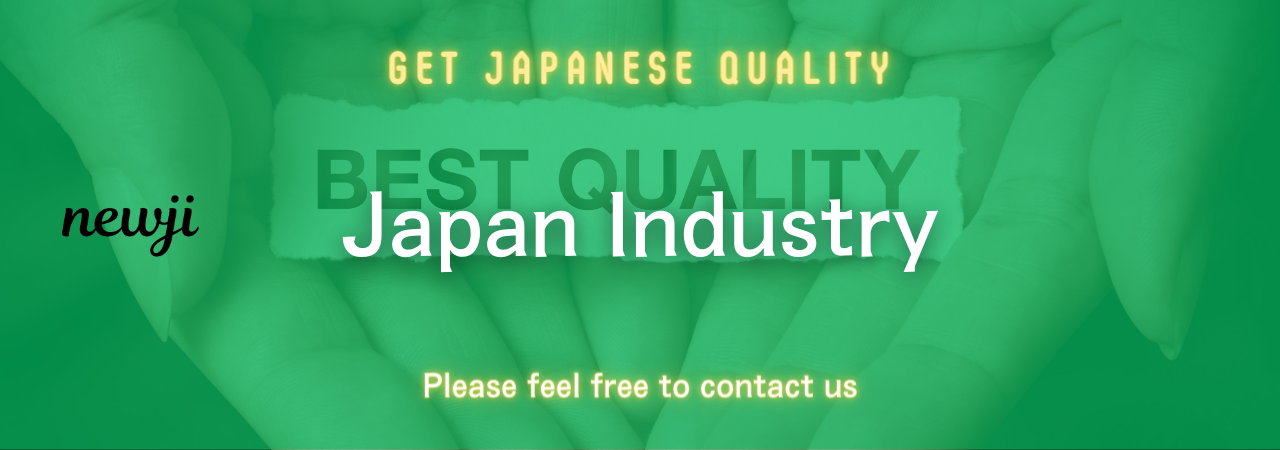
目次
Understanding Fracture Mechanics
Fracture mechanics is a crucial field in materials science that helps us understand how and why materials break under stress.
At its core, it focuses on the study of cracks in materials, investigating how they form, propagate, and lead to failure.
This field is essential for predicting the durability and safety of structures and components across various industries, from aerospace to civil engineering.
The Basics of Fracture Mechanics
Fracture mechanics revolves around three main parameters: stress, strain, and the material’s inherent properties.
The stress is the force applied to a material, strain is the deformation or displacement, and material properties determine how the material behaves under these forces.
Cracks tend to originate from defects or flaws within a material, such as voids, inclusions, or surface scratches.
When a material with a crack is subjected to an external load, stress concentrations develop at the crack tip, potentially leading to crack growth and eventual failure.
Toughness and the Crack Tip
Material toughness plays a crucial role in fracture mechanics.
Toughness is a material’s ability to absorb energy and deform without fracturing.
The resistance to crack growth is described by parameters like the stress intensity factor (K) and the energy release rate (G).
The area around the crack tip is of particular interest because it determines whether a crack will grow.
Finite Element Method (FEM)
The finite element method is a numerical technique used to solve complex engineering and physics problems.
In the context of fracture mechanics, FEM plays a significant role in modeling and analyzing the behavior of materials and structures under stress.
Basics of Finite Element Method
FEM involves breaking down a complex structure into smaller, manageable elements.
These elements are connected at nodes, forming an interconnected mesh that represents the original structure.
The equations governing the behavior of each element are formulated, and a computer program solves these equations to predict how the entire structure will respond to given conditions.
Applying FEM in Fracture Mechanics
FEM is particularly valuable in fracture mechanics for investigating crack growth and propagation.
By simulating different loading conditions, engineers can predict how cracks will behave over time.
This method allows for a detailed understanding of stress and displacement fields around cracks, which is crucial for assessing material durability and safety.
FEM also enables the study of complex geometries and heterogeneous materials, providing insights that traditional analytical methods cannot achieve.
Fatigue Life Estimation
Fatigue refers to the weakening of a material caused by repeated loading and unloading cycles.
Over time, even small stresses can accumulate and result in material failure.
Fatigue life estimation is a key application of fracture mechanics and FEM, helping to predict how long a structure or component can withstand cyclic loads before failure.
Significance of Fatigue
Fatigue is a phenomenon that leads to progressive and localized structural damage.
It’s a critical concern in industries like aerospace, automotive, and civil engineering, where cyclic loading is common.
By accurately estimating fatigue life, engineers can design safer and more reliable structures, minimizing the risk of catastrophic failure.
Methods for Fatigue Life Estimation
There are various approaches to estimating fatigue life, including experimental, analytical, and numerical methods.
Experimental methods involve physical testing, while analytical methods use mathematical models to predict fatigue life.
Numerical methods like FEM provide a comprehensive approach by simulating the stress and strain distribution within a material.
Integrating Fracture Mechanics and FEM for Fatigue Life Estimation
The combination of fracture mechanics and finite element method is powerful for fatigue life estimation.
Fracture mechanics provides the theoretical foundation for understanding crack behavior under cyclic loading.
Meanwhile, FEM offers the computational tools to analyze complex structures and predict their fatigue life.
Practical Applications
In engineering applications, this integration allows for more accurate predictions of when and how a component will fail due to fatigue.
Engineers can input material properties, loading conditions, and other relevant factors into an FEM model to simulate the behavior of components over time.
This approach is essential for industries where high reliability is a must, such as in designing aircraft, bridges, and machinery.
Challenges and Considerations
Despite its advantages, the integration of fracture mechanics and FEM for fatigue life estimation comes with challenges.
Accurate material properties and loading conditions must be known to produce reliable results.
Additionally, FEM simulations can be computationally intensive and require specialized software and expertise.
Continued advances in computational power and modeling techniques are making these challenges more manageable, expanding the possibilities for fatigue life estimation in engineering design.
Conclusion
Understanding the fundamentals of fracture mechanics and its integration with the finite element method is essential for predicting material behavior and ensuring the safety and longevity of structures.
This combined approach allows engineers to estimate fatigue life with greater accuracy, addressing an essential aspect of design and maintenance across various industries.
As technology evolves, the applications and capabilities of these methods will continue to grow, offering even greater insights into material behavior and structural integrity.
資料ダウンロード
QCD管理受発注クラウド「newji」は、受発注部門で必要なQCD管理全てを備えた、現場特化型兼クラウド型の今世紀最高の受発注管理システムとなります。
ユーザー登録
受発注業務の効率化だけでなく、システムを導入することで、コスト削減や製品・資材のステータス可視化のほか、属人化していた受発注情報の共有化による内部不正防止や統制にも役立ちます。
NEWJI DX
製造業に特化したデジタルトランスフォーメーション(DX)の実現を目指す請負開発型のコンサルティングサービスです。AI、iPaaS、および先端の技術を駆使して、製造プロセスの効率化、業務効率化、チームワーク強化、コスト削減、品質向上を実現します。このサービスは、製造業の課題を深く理解し、それに対する最適なデジタルソリューションを提供することで、企業が持続的な成長とイノベーションを達成できるようサポートします。
製造業ニュース解説
製造業、主に購買・調達部門にお勤めの方々に向けた情報を配信しております。
新任の方やベテランの方、管理職を対象とした幅広いコンテンツをご用意しております。
お問い合わせ
コストダウンが利益に直結する術だと理解していても、なかなか前に進めることができない状況。そんな時は、newjiのコストダウン自動化機能で大きく利益貢献しよう!
(β版非公開)