- お役立ち記事
- Fundamentals of fracture surface observation (fractography) of metal materials, key points of analysis, and application to estimating the cause of damage
月間76,176名の
製造業ご担当者様が閲覧しています*
*2025年3月31日現在のGoogle Analyticsのデータより
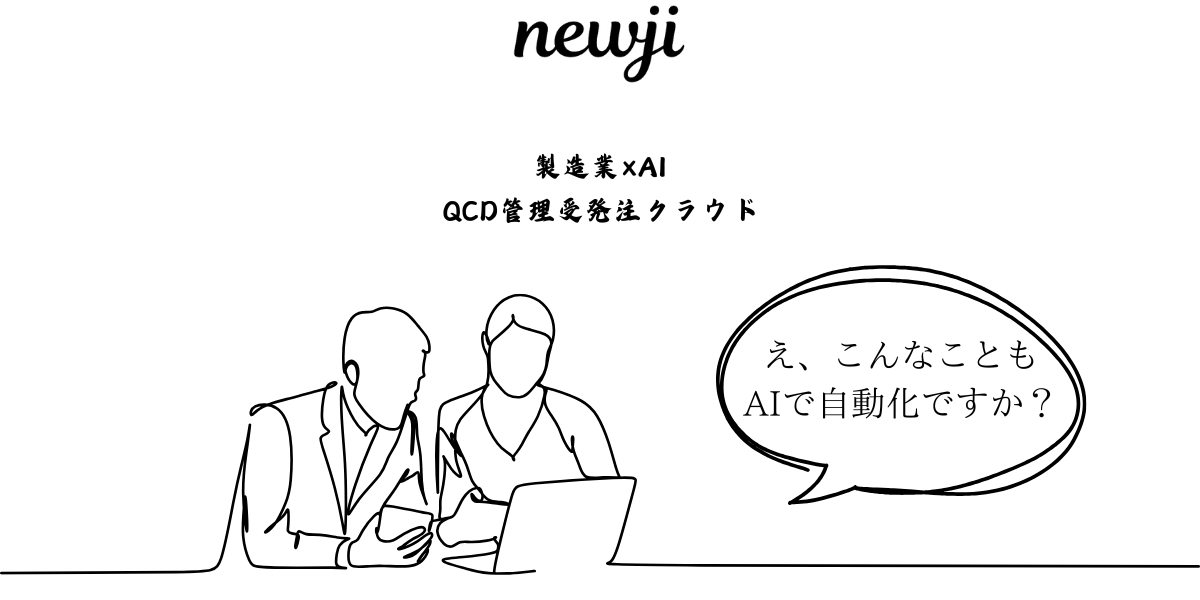
Fundamentals of fracture surface observation (fractography) of metal materials, key points of analysis, and application to estimating the cause of damage
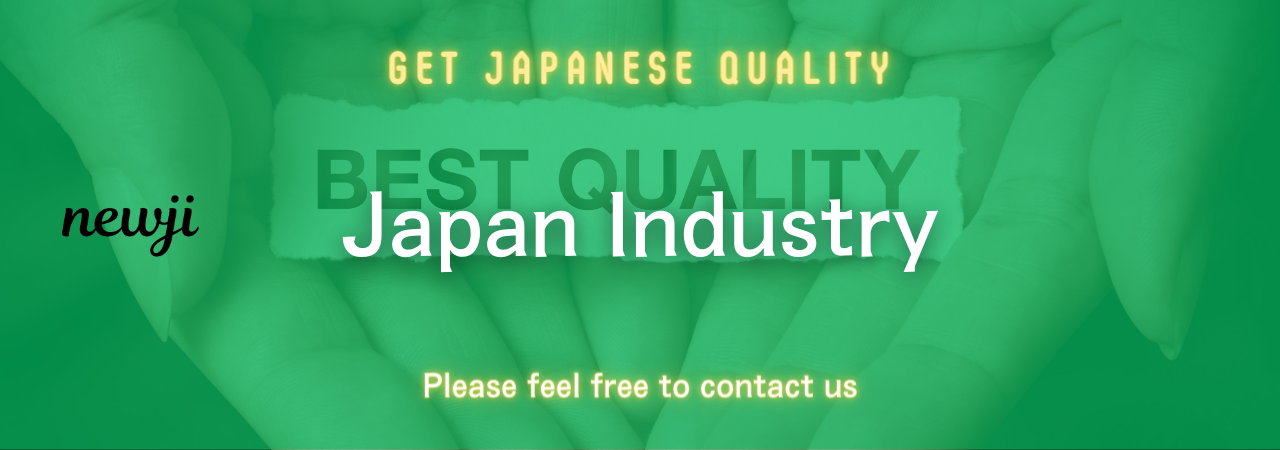
目次
Understanding Fractography and Its Importance
Fractography is the study and analysis of fracture surfaces of materials, primarily metals, to determine the cause of failure and understand the material’s behavior under stress.
This technique is essential in the field of materials engineering and failure analysis.
By examining the fracture surfaces, experts can identify the origin of the crack, the direction of crack propagation, and ultimately, the root cause of failure.
Fractography is applied in various industries, including aerospace, automotive, and construction, to enhance safety and performance.
The Process of Fracture Surface Observation
The observation of fracture surfaces involves several key steps to ensure accurate analysis.
First, the fractured component is carefully collected and preserved to maintain its integrity.
The next step involves cleaning the fracture surface to remove contaminants that may obscure critical features.
Once clean, the fracture surface is examined using various methods.
Low-magnification observation provides an overall view to locate the fracture origin and other relevant features.
Higher magnification techniques, such as scanning electron microscopy (SEM), allow for detailed analysis of the microstructure and fracture mode.
Key Points in Fractography Analysis
To effectively analyze a fracture surface, several key points should be considered:
Identifying the Fracture Origin
Determining the location where the fracture began is crucial in understanding the failure process.
This typically involves recognizing features such as radial marks, chevron patterns, or subtle surface changes that point to the origin.
Analyzing Fracture Mode
Fracture modes can be classified into ductile, brittle, fatigue, or intergranular.
Each mode presents distinct features; for instance, ductile fractures often exhibit dimple patterns, while brittle fractures show cleavage planes.
Recognizing these modes aids in understanding how the material failed.
Direction of Crack Propagation
The direction in which the crack propagated provides insight into the stress state and loading conditions of the material.
Features such as fatigue striations or beachmarks, which result from cyclic loading, can guide analysts in this determination.
Environmental and Operational Conditions
Assessing the impact of environmental factors, such as temperature, humidity, or corrosive elements, on the fracture surface helps in pinpointing contributing conditions to the failure.
Applications of Fractography in Failure Analysis
Fractography serves as a powerful tool in various applications, primarily focused on improving material performance and preventing future failures.
Failure Investigation
In industries where safety is paramount, like aerospace or nuclear energy, understanding the cause of material failure is critical.
Fractography helps engineers and researchers to reconstruct the failure event, allowing them to implement design improvements or corrective actions.
Quality Control
Fractography can be used during the manufacturing process to evaluate the quality of materials.
By analyzing sample fractures, manufacturers can detect defects, such as inclusions or voids, that might compromise the integrity of a component.
Material Development
When developing new materials or alloys, understanding their fracture behavior under different conditions is essential.
Fractography provides insights into how modifications in composition or processing affect a material’s strength, durability, and reliability.
Estimation of Service Life
By analyzing previous fracture surfaces, engineers can estimate the remaining service life of similar components still in use.
This predictive maintenance approach allows for informed decisions about repairs or replacements, optimizing resource allocation and preventing unexpected downtimes.
Conclusion
Fractography is a vital technique in the field of materials science, offering detailed insights into the causes and nature of material failure.
By utilizing this tool, industries can enhance safety, improve material performance, and prevent future failures.
A thorough understanding of fracture surface observation and analysis yields invaluable information that drives innovation and ensures the reliability of metal materials in various applications.
資料ダウンロード
QCD管理受発注クラウド「newji」は、受発注部門で必要なQCD管理全てを備えた、現場特化型兼クラウド型の今世紀最高の受発注管理システムとなります。
ユーザー登録
受発注業務の効率化だけでなく、システムを導入することで、コスト削減や製品・資材のステータス可視化のほか、属人化していた受発注情報の共有化による内部不正防止や統制にも役立ちます。
NEWJI DX
製造業に特化したデジタルトランスフォーメーション(DX)の実現を目指す請負開発型のコンサルティングサービスです。AI、iPaaS、および先端の技術を駆使して、製造プロセスの効率化、業務効率化、チームワーク強化、コスト削減、品質向上を実現します。このサービスは、製造業の課題を深く理解し、それに対する最適なデジタルソリューションを提供することで、企業が持続的な成長とイノベーションを達成できるようサポートします。
製造業ニュース解説
製造業、主に購買・調達部門にお勤めの方々に向けた情報を配信しております。
新任の方やベテランの方、管理職を対象とした幅広いコンテンツをご用意しております。
お問い合わせ
コストダウンが利益に直結する術だと理解していても、なかなか前に進めることができない状況。そんな時は、newjiのコストダウン自動化機能で大きく利益貢献しよう!
(β版非公開)