- お役立ち記事
- Fundamentals of fretting fatigue design method and fatigue fracture countermeasure technology
月間76,176名の
製造業ご担当者様が閲覧しています*
*2025年3月31日現在のGoogle Analyticsのデータより
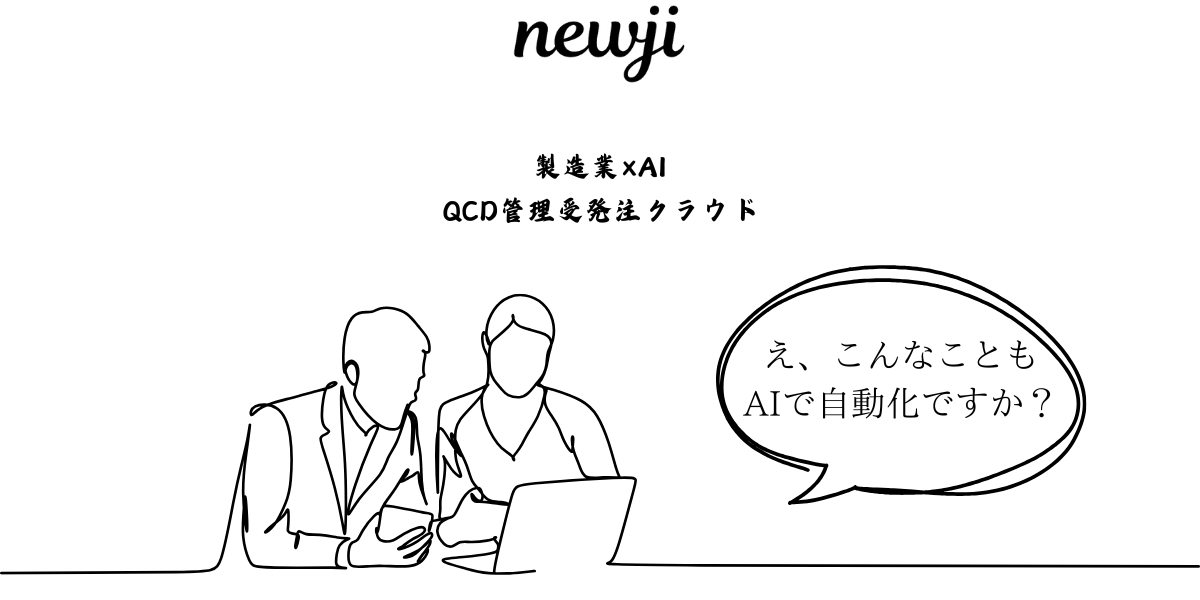
Fundamentals of fretting fatigue design method and fatigue fracture countermeasure technology
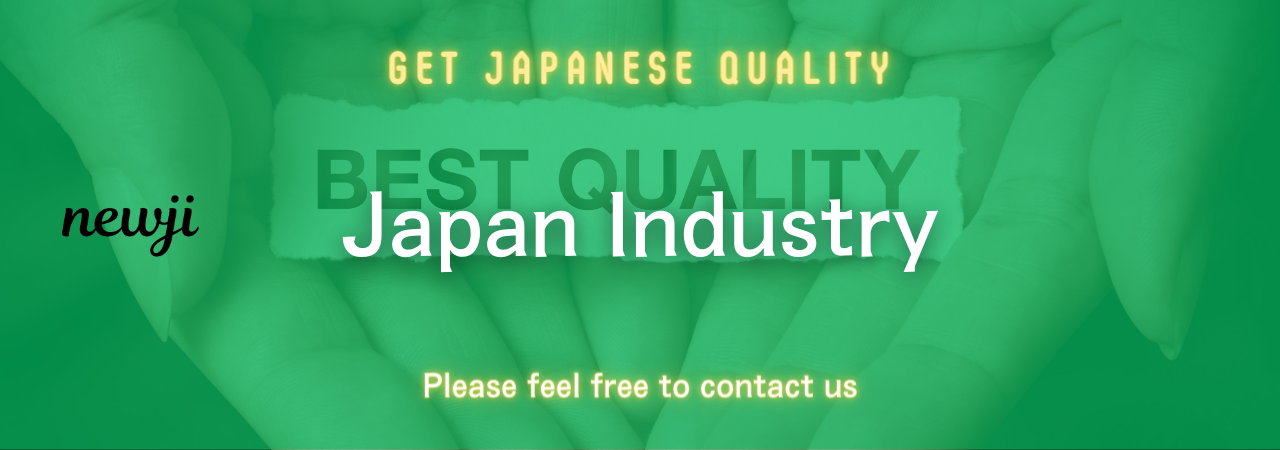
目次
Understanding Fretting Fatigue
Fretting fatigue is a specific type of wear and fatigue damage that occurs when two contact surfaces experience small oscillatory relative motion under high contact pressure.
This phenomenon often leads to material surface damage, resulting in micro-cracks that evolve into larger cracks over time.
Understanding the fundamentals of fretting fatigue is essential for engineers and designers as they strive to enhance the durability and longevity of components subjected to cyclic loads.
Fretting fatigue is most commonly observed in engineering applications where two components are pressed against each other under a cyclic load.
The surfaces may appear stationary but microscopic relative motion occurs, causing damage.
It is this repetitive rubbing motion at a high load that leads to wear and fatigue.
Examples of areas where fretting fatigue occurs include bolted joints, riveted connections, shaft couplings, and spline connections.
Mechanism of Fretting Fatigue
The mechanism of fretting fatigue is complex and differs from traditional fatigue owing to the presence of very small amplitude oscillatory movements between contacting surfaces.
This results in localized plastic deformation and crack nucleation.
The primary stages include:
1. **Initial Contact and Adhesion**: At the beginning, the contacting surfaces may adhere or stick partially due to asperities or irregularities on the surfaces.
2. **Slip and Debonding**: As the mechanical component is subjected to load, micro-slips occur at the contact interface, causing debonding at the asperities.
3. **Material Transfer and Oxidation**: The movement results in wear debris formation, often oxidizing quickly and exacerbating the damage due to abrasive and adhesive wear.
4. **Crack Initiation**: With continued stress cycling, wear accelerates crack initiation, generally starting from surface imperfections introduced during the wear process.
5. **Crack Propagation and Fracture**: Once initiated, cracks propagate quickly leading to ultimate fracture.
Factors Influencing Fretting Fatigue
Several key factors influence the onset and propagation of fretting fatigue, including:
– **Material Properties**: Materials with high hardness and toughness are generally more resistant to the onset of fretting fatigue. Surface treatments like nitriding and shot peening can enhance these properties.
– **Contact Pressure and Slip Amplitude**: High contact pressure combined with small amplitude oscillations exacerbates fretting fatigue. Optimal design minimizes these factors.
– **Environmental Conditions**: Conditions such as temperature and humidity can significantly affect the fatigue behavior. For instance, elevated temperatures accelerate oxidation, increasing wear rates.
– **Load and Stress Concentration**: The magnitude of applied normal and tangential loads as well as stress concentrations can influence fatigue life.
Fretting Fatigue Design Methods
Designing to prevent fretting fatigue involves careful consideration of various aspects:
Material Selection
Choosing the right material for components experiencing potential fretting is crucial.
Materials with inherent high resistance to wear and fatigue should be prioritized.
It’s beneficial to apply surface treatments, such as carburizing or coating with anti-fretting layers like titanium nitride, to enhance material properties.
Optimizing Geometry
The geometric design of components plays a significant role in reducing fretting fatigue.
Fillet radius, contact surface dimensions, and minimizing micro-slips through interference fitting can help.
Using a precise design for joint interfaces can reduce opportunity for fretting-related slippage.
Pre-Loading and Tightening Techniques
Ensuring appropriate pre-loading through controlled tightening in fasteners can prevent fretting.
This reduces the micro-slips that result in fretting fatigue.
Techniques such as lubrication help to diminish relative motions.
Surface Engineering
Applying protective coatings is a preventive technique.
Surface coatings act as a barrier reducing direct metal-to-metal contact.
Employing anti-corrosive agents in the lubrication can also mitigate wear in corrosive environments.
Counteracting Fretting Fatigue
Despite preventive measures, encountering fretting is sometimes inevitable.
Implementing targeted countermeasures can significantly reduce the adverse effects of fretting fatigue.
Regular Monitoring and Maintenance
Routine inspections enable early detection of wear patterns and fatigue cracks.
Identify and replace worn components before substantial damage occurs to avoid catastrophic failures.
Adopting Advanced Monitoring Techniques
Techniques such as Acoustic Emission Testing (AET) enable detection of even minor cracks before they propagate significantly.
Coupling real-time monitoring sensors with sensitive predictive models helps manage fatigue effectively.
Post-Failure Analysis
In event of failure, analyzing the fracture surfaces provides insights into fatigue mechanisms.
Understanding the root cause, whether environmental, mechanical, or material, creates a feedback loop for design improvement.
Conclusion
Mastering the fundamentals of fretting fatigue and implementing strategic design methodologies are critical in prolonging the lifespan of mechanical components.
Understanding the specifics of fretting fatigue aids in selecting appropriate materials, enhancing design structures, and preempting failure through rigorous monitoring and innovation in surface technology.
Adopting a comprehensive approach empowers engineers and designers to tackle the challenges posed by fretting fatigue, ensuring reliable and durable operation in mechanical applications.
資料ダウンロード
QCD管理受発注クラウド「newji」は、受発注部門で必要なQCD管理全てを備えた、現場特化型兼クラウド型の今世紀最高の受発注管理システムとなります。
ユーザー登録
受発注業務の効率化だけでなく、システムを導入することで、コスト削減や製品・資材のステータス可視化のほか、属人化していた受発注情報の共有化による内部不正防止や統制にも役立ちます。
NEWJI DX
製造業に特化したデジタルトランスフォーメーション(DX)の実現を目指す請負開発型のコンサルティングサービスです。AI、iPaaS、および先端の技術を駆使して、製造プロセスの効率化、業務効率化、チームワーク強化、コスト削減、品質向上を実現します。このサービスは、製造業の課題を深く理解し、それに対する最適なデジタルソリューションを提供することで、企業が持続的な成長とイノベーションを達成できるようサポートします。
製造業ニュース解説
製造業、主に購買・調達部門にお勤めの方々に向けた情報を配信しております。
新任の方やベテランの方、管理職を対象とした幅広いコンテンツをご用意しております。
お問い合わせ
コストダウンが利益に直結する術だと理解していても、なかなか前に進めることができない状況。そんな時は、newjiのコストダウン自動化機能で大きく利益貢献しよう!
(β版非公開)