- お役立ち記事
- Fundamentals of functional safety in machinery and key points for functional safety design and evaluation
月間76,176名の
製造業ご担当者様が閲覧しています*
*2025年3月31日現在のGoogle Analyticsのデータより
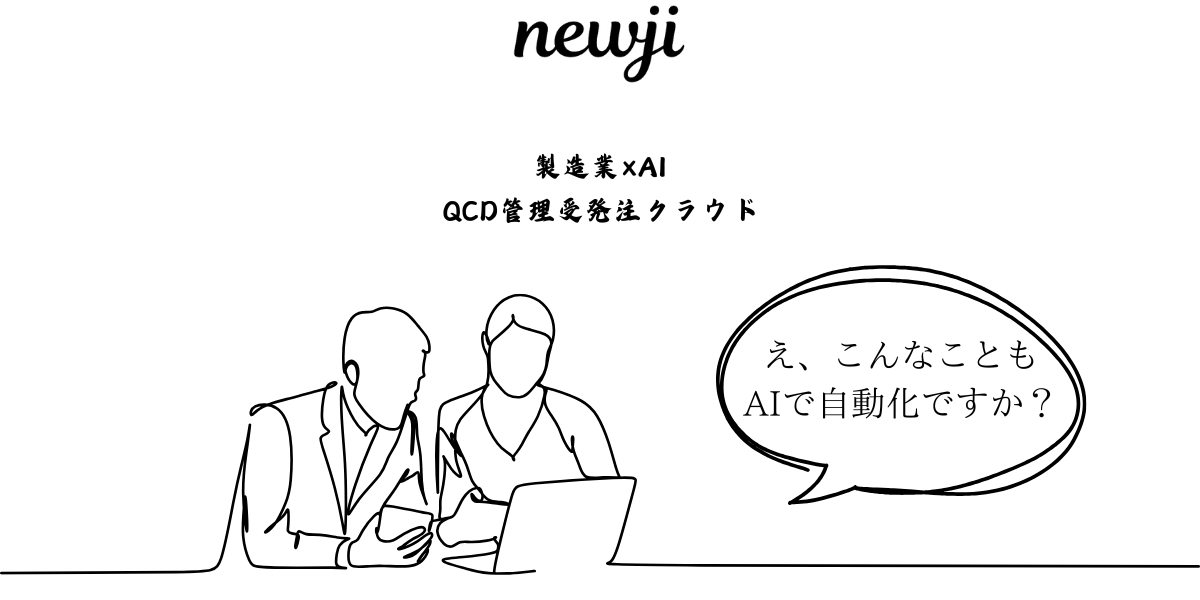
Fundamentals of functional safety in machinery and key points for functional safety design and evaluation
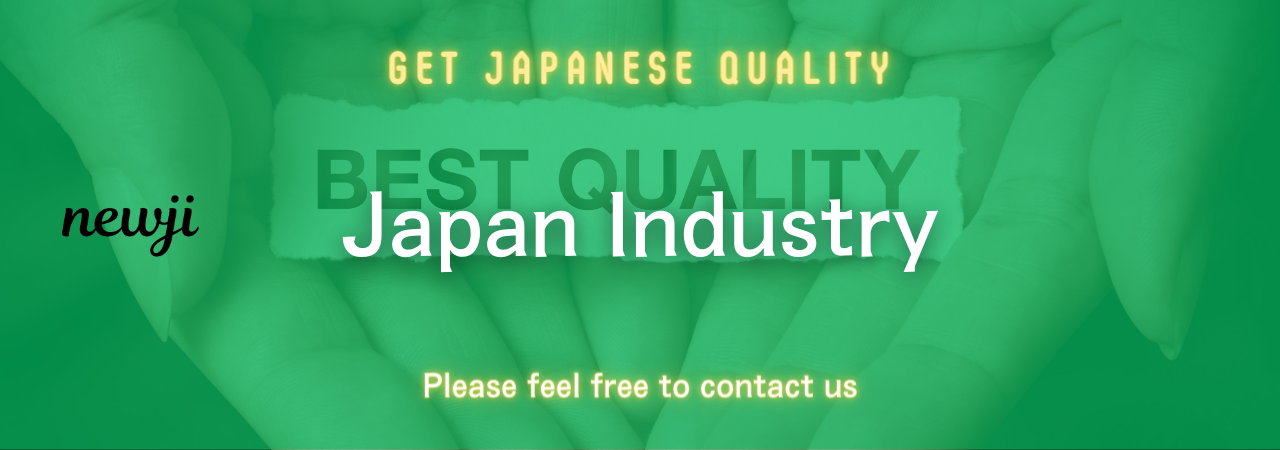
目次
Understanding Functional Safety in Machinery
Functional safety is a critical element in the design and operation of machinery that ensures systems are designed to automatically manage equipment or system failures without causing harm to people, the environment, or equipment itself.
It’s an essential concept in engineering that helps in minimizing risks associated with machine operation.
The core principle of functional safety is to reduce the risks to an acceptable level by implementing safety controls, systems, and processes.
Functional safety manages possible hazards by preventing dangerous failures or controlling them when they arise.
The Importance of Functional Safety
In any industrial setting, safety is paramount.
Functional safety provides an extra layer of protection by addressing the potential risks associated with unexpected failures or human error.
Through the implementation of functional safety measures, potential accidents can be prevented, protecting both workers and machinery.
This not only ensures the well-being of employees but also minimizes downtime and avoids costly repairs.
Furthermore, regulatory requirements demand that companies comply with specific safety standards.
Keeping up with these regulations can help organizations avoid legal penalties and maintain their credibility in the industry.
Key Components of Functional Safety
Functional safety systems are made up of several crucial elements that work together to ensure the safe operation of machinery.
Safety Instrumented Systems (SIS)
Safety Instrumented Systems are designed to monitor the operation of equipment and intervene when unsafe conditions arise.
They use sensors, logic solvers, and actuators to detect and prevent hazardous incidents.
These systems are vital in carrying out safety functions and ensuring that machinery operates within specified limits.
Risk Assessment and Management
Before implementing any functional safety measures, a thorough risk assessment must be carried out.
This process involves identifying potential hazards, evaluating the risks, and determining the necessary safety measures to minimize those risks.
Effective risk management involves the continuous monitoring and updating of safety systems, ensuring they remain relevant and effective over time.
Safety Integrity Levels (SILs)
Safety Integrity Levels are benchmarks used to assess the performance of safety functions.
They define the probability of a safety function’s failure on demand.
There are four levels of SIL, with SIL 1 being the lowest and SIL 4 being the highest.
Selecting the appropriate SIL for a safety function is critical, as it determines the system’s ability to minimize risk.
Validation and Verification
Validation and verification are essential steps in the functional safety process.
Validation ensures that the safety systems meet the required performance standards, while verification verifies that the systems operate as intended.
These processes involve rigorous testing and analysis, providing assurance that safety systems are fit for purpose.
Key Considerations for Functional Safety Design
Designing functional safety systems requires meticulous planning and execution.
Here are some points to consider when designing systems for safety.
Define Safety Objectives
The first step in designing a functional safety system is to define clear safety objectives.
These objectives should guide the design process and ensure that the final system adequately addresses all identified risks.
Use Proven Design Principles
Implement well-established design principles when creating safety systems.
This includes redundancy, diversity, and fail-safe designs, which enhance system reliability and ensure operation even in the event of a component failure.
Consider Human Factors
Human factors play a significant role in the functional safety of machinery.
Designers should consider user interaction with the equipment, ensuring interfaces are intuitive and that operational procedures are clear and understandable.
Integration with Existing Systems
When implementing new safety systems, it’s crucial to ensure they integrate seamlessly with existing machinery and processes.
Compatibility with current systems will enhance overall safety and prevent potential conflicts or malfunctions.
Regular Maintenance and Testing
Functional safety design doesn’t end with implementation; regular maintenance and testing are essential to ensure continued effectiveness.
Frequent checks and updates will help identify any changes in the operating environment that may affect the safety performance.
Evaluating Functional Safety Performance
Once designed and implemented, it is vital to evaluate the performance of functional safety systems periodically.
This evaluation helps to verify that safety objectives are being met and that systems remain effective.
Safety Audits
Carrying out regular safety audits allows you to assess the performance of your safety systems.
These audits can identify potential weaknesses or inefficiencies, providing opportunities for improvement.
Incident Analysis
In the event of an incident, comprehensive analysis should be conducted to determine the root cause.
This analysis can provide valuable insights that inform future design improvements and prevent reoccurrence.
Performance Monitoring
Continuous monitoring of safety system performance is crucial for identifying trends that may signify impending failures or inefficiencies.
This monitoring allows for proactive maintenance and timely interventions.
Feedback Loops
Feedback loops within the organization can provide useful information for enhancing functional safety systems.
Employee feedback, management reviews, and lessons learned from past incidents can all contribute to continuous improvement.
Adhering to these principles and continuously evaluating performance ensures that functional safety systems remain robust and effective.
By prioritizing functional safety, companies can safeguard their workforce and machinery while ensuring compliance with industry regulations.
資料ダウンロード
QCD管理受発注クラウド「newji」は、受発注部門で必要なQCD管理全てを備えた、現場特化型兼クラウド型の今世紀最高の受発注管理システムとなります。
ユーザー登録
受発注業務の効率化だけでなく、システムを導入することで、コスト削減や製品・資材のステータス可視化のほか、属人化していた受発注情報の共有化による内部不正防止や統制にも役立ちます。
NEWJI DX
製造業に特化したデジタルトランスフォーメーション(DX)の実現を目指す請負開発型のコンサルティングサービスです。AI、iPaaS、および先端の技術を駆使して、製造プロセスの効率化、業務効率化、チームワーク強化、コスト削減、品質向上を実現します。このサービスは、製造業の課題を深く理解し、それに対する最適なデジタルソリューションを提供することで、企業が持続的な成長とイノベーションを達成できるようサポートします。
製造業ニュース解説
製造業、主に購買・調達部門にお勤めの方々に向けた情報を配信しております。
新任の方やベテランの方、管理職を対象とした幅広いコンテンツをご用意しております。
お問い合わせ
コストダウンが利益に直結する術だと理解していても、なかなか前に進めることができない状況。そんな時は、newjiのコストダウン自動化機能で大きく利益貢献しよう!
(β版非公開)