- お役立ち記事
- Fundamentals of gear design, strength design, and key points of low vibration and noise reduction technology
月間76,176名の
製造業ご担当者様が閲覧しています*
*2025年3月31日現在のGoogle Analyticsのデータより
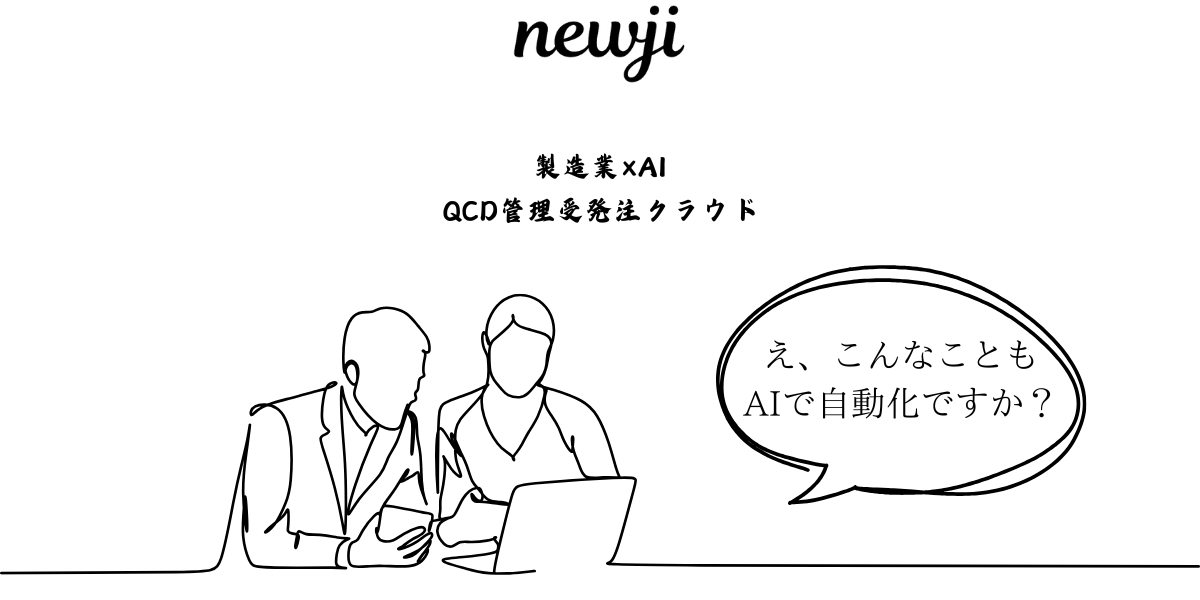
Fundamentals of gear design, strength design, and key points of low vibration and noise reduction technology
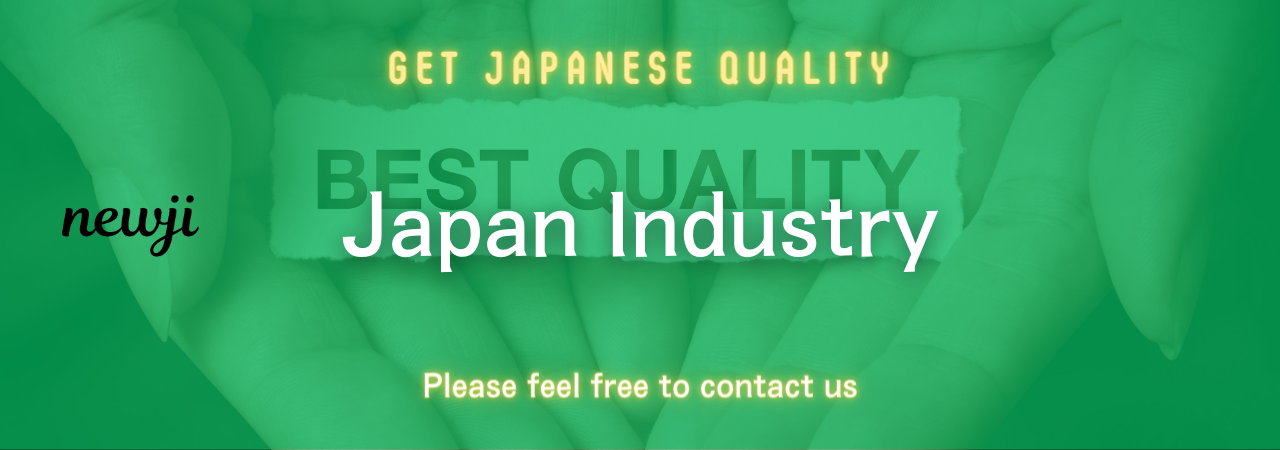
目次
Introduction to Gear Design
Gear design is a fascinating field that blends the intricacies of mechanical engineering with the principles of physics.
At its core, gear design revolves around creating mechanisms that transmit motion and power efficiently between machine parts.
When undertaking gear design, engineers must consider several fundamental concepts to create robust and efficient gears that meet specific needs.
Gears come in various sizes and types, each tailored to specific applications.
Common types include spur gears, helical gears, bevel gears, and worm gears.
Each of these designs has distinct characteristics that make them suitable for different purposes, such as speed reduction, torque increase, or directional change of mechanical power.
Understanding Gear Strength Design
To ensure that a gear functions effectively and safely, its strength must be adequately designed and calculated.
The strength design of gears involves analyzing the stresses and strains that the gears will encounter during operation.
One primary consideration is the material choice.
Gears can be made from metals, such as steel or brass, or other materials like plastics for specific applications.
The material must withstand the forces applied during operation without failing.
This selection is crucial as it influences the gear’s lifespan and performance under various conditions.
Moreover, engineers must consider the gear’s durability and resistance to wear.
Friction between engaging gears can significantly impact their longevity.
The gear teeth are particularly vulnerable, thus requiring careful consideration of load distribution and pressure angles to minimize stress concentrations.
Bending and Surface Fatigue
Two primary forms of stress impact the gears: bending and surface fatigue.
Bending stress occurs when force is applied to the gear teeth, causing them to bend.
This can lead to gear tooth failure if not properly accounted for.
Surface fatigue, on the other hand, arises from repeated contact stress at the gear tooth surface.
The constant engagement and disengagement of gear teeth can result in pitting, a form of surface wear that can ultimately lead to gear failure.
To mitigate these issues, engineers perform thorough analyses using established calculation methods, such as the Lewis formula for bending stress and the Hertzian contact stress calculation for surface fatigue.
These calculations guide the optimal gear size and shape to handle anticipated loads.
Key Points of Low Vibration and Noise Reduction Technology
Transforming gear systems into quieter and smoother operating units involves addressing noise and vibration, both of which can degrade performance and cause damage over time.
Precision Manufacturing
Manufacturing precision is central to minimizing vibration and noise in gears.
The smoother and more accurately a gear is manufactured, the less acoustic noise it generates.
This precision involves the correct alignment and surface finish of gears, impacting their smooth engagement.
Shape and Material Considerations
The shape and material of the gear significantly influence noise production.
Helical gears, for example, tend to operate more quietly than spur gears due to their angled teeth, which engage gradually rather than all at once.
Additionally, materials that have inherent damping properties can absorb some of the vibrations inherently produced during gear operation.
Selecting such materials, or applying special coatings, can drastically reduce noise levels.
Lubrication and Maintenance
Proper lubrication plays a pivotal role in minimizing noise and vibration.
It reduces friction between gear teeth, thereby decreasing the audible noise produced by gear sets during operation.
Regular maintenance ensures that gears remain well-aligned and that wear patterns are addressed before they lead to significant operational issues.
Dynamic Analysis
Conducting a dynamic analysis of the gear system is crucial for identifying any resonance or harmonic frequencies that might exacerbate vibration and noise.
This analysis helps in designing gears that operate smoothly at intended speeds while introducing damping systems to counteract unwanted oscillations.
Conclusion
Gear design is an integral aspect of mechanical engineering that requires a strong understanding of both theoretical and practical principles.
By focusing on designing robust, high-quality gears, engineers can ensure that these mechanical components operate efficiently, and with minimal noise and vibration.
Understanding the fundamentals of gear design, strength considerations, and methods to reduce vibrations and noise are essential skills for achieving this goal.
By integrating precision manufacturing techniques, selecting the appropriate materials, and adhering to rigorous maintenance schedules, engineers can produce gears that are not only efficient and durable but also quiet and smooth in their operation.
This meticulous approach makes a significant difference in a wide array of applications, from automotive transmissions to intricate machinery, ultimately leading to better-performing mechanical systems.
資料ダウンロード
QCD管理受発注クラウド「newji」は、受発注部門で必要なQCD管理全てを備えた、現場特化型兼クラウド型の今世紀最高の受発注管理システムとなります。
ユーザー登録
受発注業務の効率化だけでなく、システムを導入することで、コスト削減や製品・資材のステータス可視化のほか、属人化していた受発注情報の共有化による内部不正防止や統制にも役立ちます。
NEWJI DX
製造業に特化したデジタルトランスフォーメーション(DX)の実現を目指す請負開発型のコンサルティングサービスです。AI、iPaaS、および先端の技術を駆使して、製造プロセスの効率化、業務効率化、チームワーク強化、コスト削減、品質向上を実現します。このサービスは、製造業の課題を深く理解し、それに対する最適なデジタルソリューションを提供することで、企業が持続的な成長とイノベーションを達成できるようサポートします。
製造業ニュース解説
製造業、主に購買・調達部門にお勤めの方々に向けた情報を配信しております。
新任の方やベテランの方、管理職を対象とした幅広いコンテンツをご用意しております。
お問い合わせ
コストダウンが利益に直結する術だと理解していても、なかなか前に進めることができない状況。そんな時は、newjiのコストダウン自動化機能で大きく利益貢献しよう!
(β版非公開)