- お役立ち記事
- Fundamentals of gears, strength design, vibration and noise reduction technology and their key points
月間76,176名の
製造業ご担当者様が閲覧しています*
*2025年3月31日現在のGoogle Analyticsのデータより
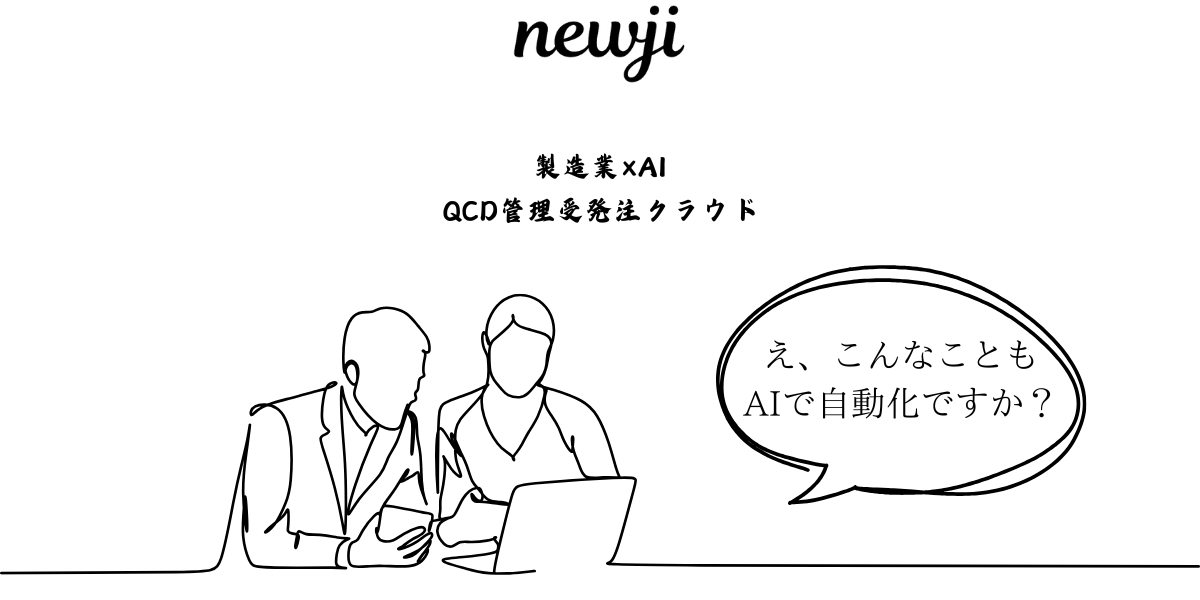
Fundamentals of gears, strength design, vibration and noise reduction technology and their key points
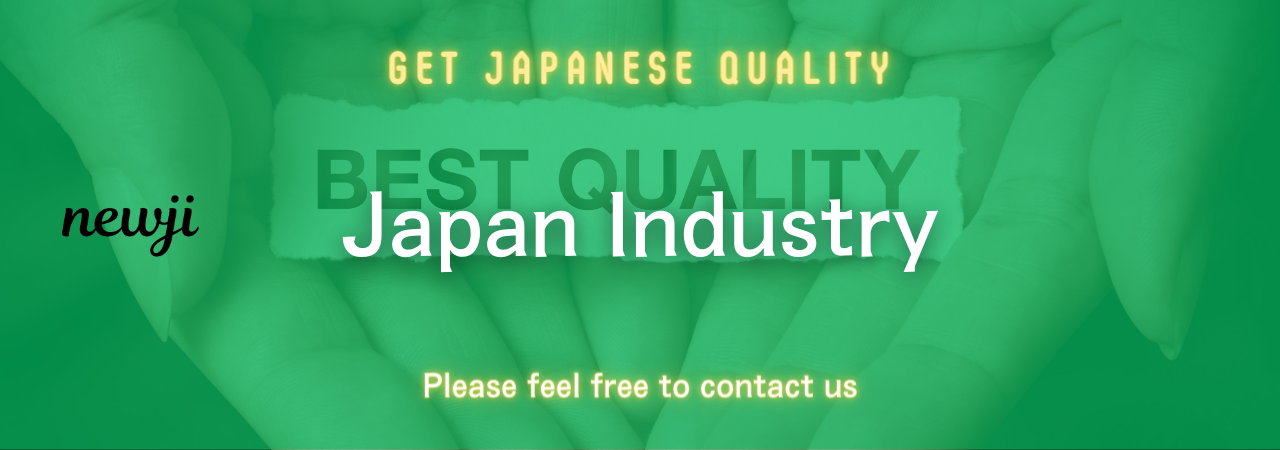
目次
Understanding the Basics of Gears
Gears are essential components in many mechanical devices, from simple machines to complex industrial equipment.
They are designed to transfer torque and rotation from one part of a machine to another, altering speed, direction, and movement.
Understanding the fundamentals of gears is critical for anyone involved in engineering, design, or maintenance of machinery.
Types of Gears
There are several types of gears, each serving different purposes and applications.
– **Spur Gears**: These are the simplest type of gear, having straight teeth and mounted on parallel shafts.
They are commonly used in various applications due to their simplicity and efficiency in transmitting motion and power.
– **Helical Gears**: Unlike spur gears, helical gears have teeth that are cut at an angle to the face of the gear.
This angle allows for smoother and quieter operation, making them ideal for high-speed and heavy-load applications.
– **Bevel Gears**: These gears are used to transmit power between shafts that are at an angle to each other, most commonly at 90 degrees.
They come in straight, spiral, or hypoid forms and are used in different machinery, including car differentials.
– **Worm Gears**: This type of gear consists of a screw (the worm) that meshes with a gear (the worm wheel).
They are known for providing high reduction ratios and are commonly used in applications requiring precise motion control.
Strength Design in Gears
The strength design of gears is crucial to ensure they can withstand operational stresses without failure.
Several factors influence the strength of gears, including material selection, gear geometry, and load conditions.
Material Selection
The choice of material is pivotal in the strength design of gears.
Materials such as steel, brass, and composites are commonly used based on their properties.
– **Steel**: Known for its strength and durability, steel is the most popular material for gears.
Its resistance to wear and high fatigue strength make it suitable for demanding applications.
– **Brass**: This is a softer material often used for gears that do not bear heavy loads.
It is known for its anti-corrosive properties and is typically used in low-friction applications.
– **Composites**: Used for lightweight and corrosion-resistant properties, composite materials are increasingly employed in specialized gear designs.
Load and Stress Analysis
Understanding the loads and stresses acting on gears is essential for designing them to withstand operational challenges.
– **Static Load**: It involves calculating the forces acting on gears when stationary and designing them to resist deformation under these loads.
– **Dynamic Load**: Dynamic loading considers forces that occur when gears are in motion.
These forces can vary significantly and require careful analysis to predict and mitigate potential stress points.
Vibration Reduction in Gears
Vibration in gears can lead to noise, reduced performance, and even failure.
Effective strategies to reduce vibration are important for long-lasting and efficient gear operation.
Optimization of Gear Profiles
One approach to minimizing vibration is optimizing gear profiles.
The design and cutting of gear teeth can be adjusted to improve the smoothness of gear contact, reducing the potential for vibration.
Balancing and Alignment
Proper balancing and alignment are crucial in mitigating vibration.
Misalignment of gears can cause uneven load distribution, leading to increased vibration and noise.
Regular maintenance checks and adjustments can help maintain precise alignment.
Use of Dampening Materials
Incorporating dampening materials into gear systems can help absorb and dissipate vibrations.
Materials such as rubber or specialized coatings are often used in gear housings to reduce the transmission of vibration and noise.
Noise Reduction Techniques
In addition to vibration, noise generated by gear operation can be a significant concern, especially in environments where quiet operation is critical.
Smooth Surface Finishes
Ensuring that gear surfaces are smooth can greatly reduce noise levels.
Rough surfaces increase friction and lead to higher noise production during gear rotation.
Precision Manufacturing
Precision in the manufacturing of gears ensures that all components fit together seamlessly, reducing the potential for noise-generating gaps and misalignments.
Proper Lubrication
Adequate lubrication reduces friction between gear teeth, which not only minimizes wear but also reduces noise.
Using high-quality lubricants suitable for specific gear types and operational conditions is an effective way to maintain quiet gear operation.
Key Points to Remember
Understanding and applying the fundamentals of gear design, strength, and vibration and noise reduction can lead to more efficient and reliable machinery.
– **Invest in Quality Materials**: The selection of appropriate materials significantly impacts gear durability and performance.
– **Focus on Precision**: Precision in gear design and manufacturing is essential for reducing vibration, noise, and increasing gear lifespan.
– **Prioritize Maintenance**: Regular maintenance checks are crucial to ensure gears remain aligned and well-lubricated.
By mastering these aspects of gear technology, engineers and designers can significantly enhance the efficiency and longevity of mechanical systems.
資料ダウンロード
QCD管理受発注クラウド「newji」は、受発注部門で必要なQCD管理全てを備えた、現場特化型兼クラウド型の今世紀最高の受発注管理システムとなります。
ユーザー登録
受発注業務の効率化だけでなく、システムを導入することで、コスト削減や製品・資材のステータス可視化のほか、属人化していた受発注情報の共有化による内部不正防止や統制にも役立ちます。
NEWJI DX
製造業に特化したデジタルトランスフォーメーション(DX)の実現を目指す請負開発型のコンサルティングサービスです。AI、iPaaS、および先端の技術を駆使して、製造プロセスの効率化、業務効率化、チームワーク強化、コスト削減、品質向上を実現します。このサービスは、製造業の課題を深く理解し、それに対する最適なデジタルソリューションを提供することで、企業が持続的な成長とイノベーションを達成できるようサポートします。
製造業ニュース解説
製造業、主に購買・調達部門にお勤めの方々に向けた情報を配信しております。
新任の方やベテランの方、管理職を対象とした幅広いコンテンツをご用意しております。
お問い合わせ
コストダウンが利益に直結する術だと理解していても、なかなか前に進めることができない状況。そんな時は、newjiのコストダウン自動化機能で大きく利益貢献しよう!
(β版非公開)