- お役立ち記事
- Fundamentals of gears, strength design, vibration and noise reduction technology and their key points
月間76,176名の
製造業ご担当者様が閲覧しています*
*2025年3月31日現在のGoogle Analyticsのデータより
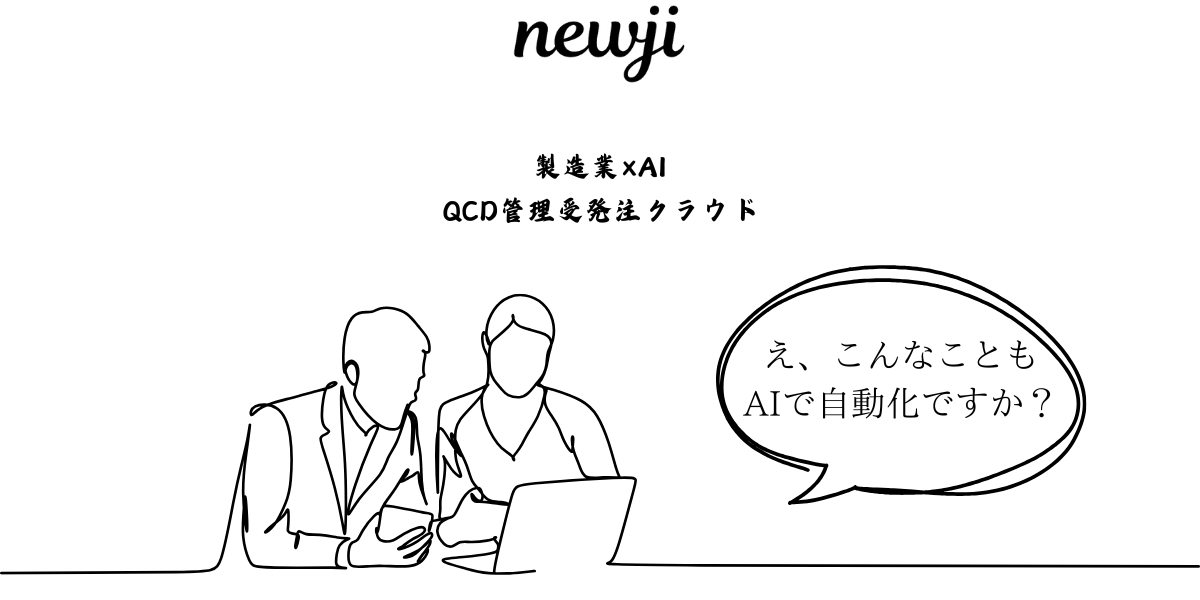
Fundamentals of gears, strength design, vibration and noise reduction technology and their key points
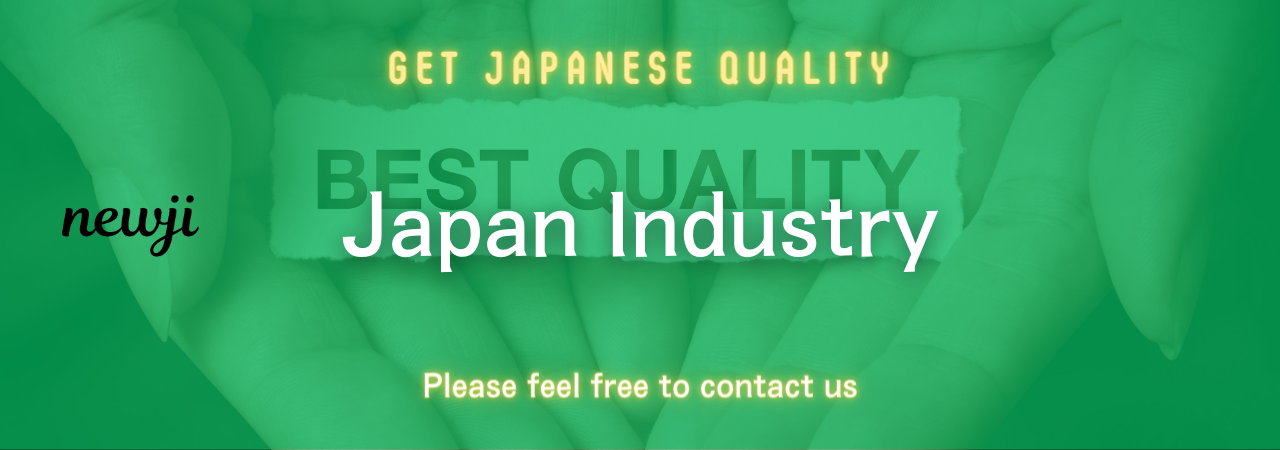
目次
Understanding the Basics of Gears
Gears are essential components in many machines and mechanical systems.
They play a crucial role in the transmission of power and motion.
The basic function of gears is to transfer torque and improve mechanical advantage by meshing together.
Gears come in various shapes and sizes, but the most common types include spur gears, helical gears, bevel gears, and worm gears.
Spur gears have straight teeth and are mounted on parallel shafts.
They are the simplest type of gear and are primarily used in applications requiring moderate speed and power.
Helical gears, on the other hand, have angled teeth, which allows for smoother and quieter operation compared to spur gears.
They are ideal for high-speed applications.
Bevel gears are designed for shafts that intersect at an angle, typically 90 degrees.
They are used in differentials, where a change in the direction of the rotational motion is required.
Lastly, worm gears consist of a worm (screw) and a worm wheel, and they are used to provide very large gear reductions.
Strength Design of Gears
To ensure the durability and longevity of gears, strength design is a critical aspect.
Strength design involves considering the materials and geometry of the gear teeth to withstand the forces exerted during operation.
Materials used for gears typically include steel, cast iron, and brass.
Steel is favored for its strength and toughness, making it suitable for high-load applications.
Cast iron is known for its excellent damping properties, which help in reducing vibration.
Brass is employed in situations demanding corrosion resistance and quieter operation.
In terms of geometry, the gear tooth profile is a vital factor.
The involute profile is the most common due to its ability to provide a constant velocity ratio between gears.
This geometry ensures that there is no slippage between the gear teeth during meshing.
The design also takes into consideration stresses such as bending and contact stresses.
Bending stress occurs at the root of the gear teeth, while contact stress occurs at the point of contact between meshing gears.
Proper calculations and analysis are necessary to ensure these stresses are within safe limits to prevent gear failure.
Vibration and Noise in Gears
One of the challenges in gear design and application is addressing vibration and noise.
Excessive vibration can lead to increased wear and tear, while noise can be a nuisance in many applications.
The source of vibration and noise in gears often originates from factors such as gear misalignment, manufacturing errors, or insufficient lubrication.
Misalignment causes uneven load distribution, which increases vibration levels.
Manufacturing errors, such as irregularities in the gear tooth profile, can also introduce unwanted vibrations.
Proper lubrication reduces friction and wear, minimizing the noise produced by the gears.
Reducing vibration and noise involves a combination of strategies.
A key approach is ensuring precise alignment during installation.
Using gears with high precision manufacturing standards reduces deviations that can cause vibration.
Advanced materials and coatings can also be used to improve damping and reduce the noise of the gear operation.
Furthermore, applying sound barriers or isolators can effectively decrease noise levels in systems where gear noise cannot be fully eliminated through design changes.
Key Points in Gear Technology
In gear technology, several key points must be considered for optimal performance.
These include gear ratio, lubrication, and proper maintenance.
The gear ratio is vital as it determines the speed and torque output of a gear system.
Choosing the correct gear ratio is essential for achieving the desired performance and efficiency.
A higher gear ratio provides more torque, while a lower ratio results in increased speed.
Lubrication is crucial for the smooth operation of gears.
It reduces friction between the gear teeth and helps dissipate heat generated during operation.
Selecting the appropriate lubricant based on the operating conditions and material of the gears is essential to prevent premature wear.
Regular maintenance is necessary to ensure the longevity of gear systems.
This includes routine inspections for signs of wear and damage, such as pitting or scoring on gear teeth.
Early detection of issues allows for timely repairs or replacements, preventing more significant problems down the line.
In conclusion, a comprehensive understanding of the fundamentals of gears, strength design, vibration, and noise reduction is essential for engineers and technicians working with mechanical systems.
Ensuring the correct gear type, material selection, and addressing potential issues related to vibration and noise will lead to more efficient and reliable gear systems.
Overall, mastering these core aspects of gear technology can significantly contribute to the effective design and maintenance of various mechanical applications.
資料ダウンロード
QCD管理受発注クラウド「newji」は、受発注部門で必要なQCD管理全てを備えた、現場特化型兼クラウド型の今世紀最高の受発注管理システムとなります。
ユーザー登録
受発注業務の効率化だけでなく、システムを導入することで、コスト削減や製品・資材のステータス可視化のほか、属人化していた受発注情報の共有化による内部不正防止や統制にも役立ちます。
NEWJI DX
製造業に特化したデジタルトランスフォーメーション(DX)の実現を目指す請負開発型のコンサルティングサービスです。AI、iPaaS、および先端の技術を駆使して、製造プロセスの効率化、業務効率化、チームワーク強化、コスト削減、品質向上を実現します。このサービスは、製造業の課題を深く理解し、それに対する最適なデジタルソリューションを提供することで、企業が持続的な成長とイノベーションを達成できるようサポートします。
製造業ニュース解説
製造業、主に購買・調達部門にお勤めの方々に向けた情報を配信しております。
新任の方やベテランの方、管理職を対象とした幅広いコンテンツをご用意しております。
お問い合わせ
コストダウンが利益に直結する術だと理解していても、なかなか前に進めることができない状況。そんな時は、newjiのコストダウン自動化機能で大きく利益貢献しよう!
(β版非公開)