- お役立ち記事
- Fundamentals of gears, wear prediction, and noise and vibration countermeasure technology
月間76,176名の
製造業ご担当者様が閲覧しています*
*2025年3月31日現在のGoogle Analyticsのデータより
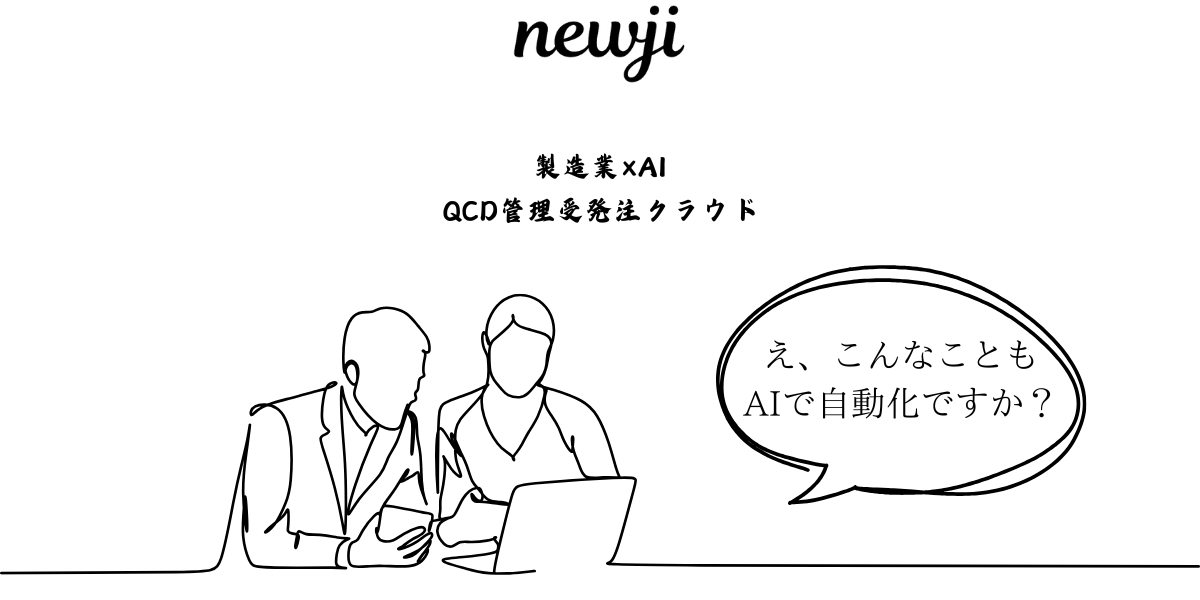
Fundamentals of gears, wear prediction, and noise and vibration countermeasure technology
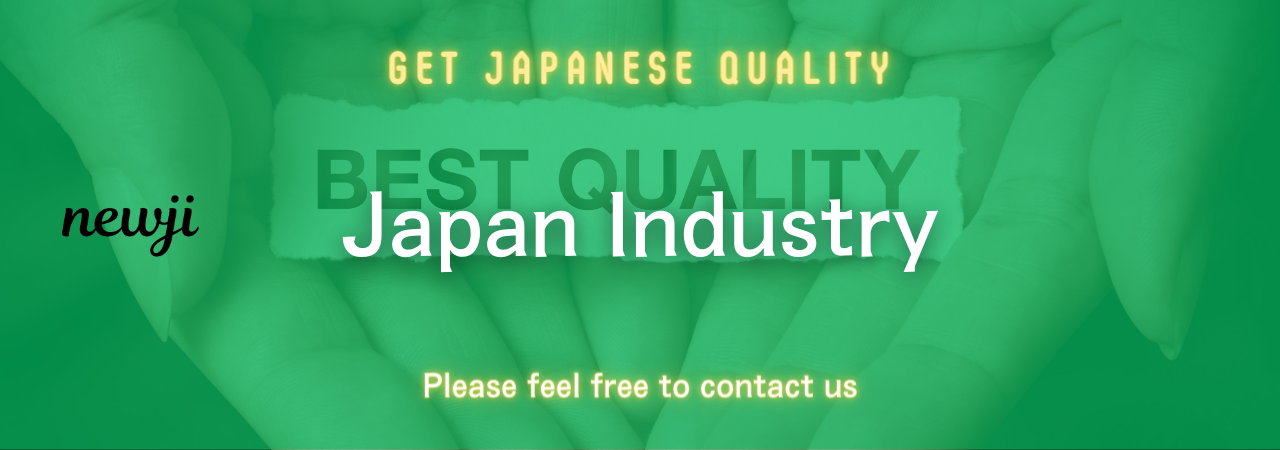
目次
Understanding the Basics of Gears
Gears are fundamental components in many mechanical devices.
They are used to transmit power and motion between different parts of a machine.
Understanding the basics of gears is essential for anyone involved in mechanical engineering or related fields.
Gears can come in various shapes and sizes, but they all function based on the basic principle of interlocking teeth.
There are several types of gears, each serving a unique purpose.
Spur gears are the most common and are used to transfer motion between parallel shafts.
Helical gears are similar to spur gears but have teeth that are cut at an angle, providing smoother and quieter operation.
Bevel gears are used to change the direction of a shaft’s rotation.
Worm gears are used for significant speed reduction.
Each type of gear has its own set of applications and advantages.
Key Components of a Gear System
A basic gear system consists of two or more gears working together.
The gear that receives power is referred to as the “driving” gear, while the gear that is moved by the driving gear is known as the “driven” gear.
Key components of a gear system include the gear teeth, the gear wheel, and the shaft.
The teeth of a gear are crucial for its function.
They are designed to mesh precisely with the teeth of another gear, allowing for efficient power transmission.
The gear wheel is the circular part of the gear that the teeth are mounted on, providing the structure to hold the teeth in place.
The shaft is the rod that connects the gears to the rest of the mechanical system, allowing them to rotate and transmit motion.
Wear Prediction in Gears
Gears in operation face wear and damage over time due to friction and other factors.
Predicting and mitigating wear is essential to extend the lifespan of gear systems.
Many factors can influence gear wear, including material quality, load, speed, lubrication, and operating conditions.
One common method for predicting gear wear is through mathematical models.
These models consider the gear’s material properties, expected load, and other operational parameters to estimate the rate of wear.
Advanced analysis tools, such as finite element analysis (FEA), can also simulate gear operation to predict wear patterns and potential failure points.
Regular maintenance is another crucial aspect of wear prediction.
Routine inspections can identify early signs of wear, allowing for timely intervention.
Visual inspections may reveal surface damage or deformation in gears.
Oil analysis can also provide insights into the condition of the lubrication and detect any foreign particles that may indicate wear.
Design Considerations to Reduce Wear
Choosing the right materials is vital in reducing gear wear.
Materials with high strength, toughness, and wear resistance are preferred.
Common materials for gears include steel, cast iron, and various composites.
Each material has its advantages and disadvantages that should be considered in the design phase.
Proper lubrication is another critical factor in reducing wear.
Lubricants minimize friction between the gear teeth, reducing heat and wear.
Selecting the right type of lubricant and maintaining optimal lubrication levels are essential for gear longevity.
In some applications, specialized coatings may be applied to the gear teeth to enhance wear resistance.
Addressing Noise and Vibration in Gear Systems
Noise and vibration are common issues in gear systems, affecting not only performance but also the comfort and health of machine operators.
Several factors can contribute to noise and vibration in gears, including gear misalignment, manufacturing errors, and inadequate lubrication.
Improving gear design is one way to address noise and vibration issues.
Using helical gears instead of spur gears can provide smoother operation and reduce noise.
Ensuring precise manufacturing tolerances can also prevent misalignment and reduce noise levels.
Advanced gear design software can help engineers optimize gear profiles to minimize noise.
Vibration damping devices can be employed to mitigate vibrations.
These devices absorb and dissipate vibrational energy, maintaining system stability.
Regular maintenance, such as checking alignment and lubrication, can further reduce noise and vibration in gear systems.
Monitoring and Diagnostic Tools
Modern technology provides a range of monitoring and diagnostic tools to address noise and vibration in gear systems.
Vibration analysis tools can detect changes in vibration patterns, indicating potential issues within the system.
Acoustic monitoring can be used to measure noise levels and identify their sources.
Predictive maintenance is another effective approach to managing noise and vibration.
By continually monitoring the condition of gears and their environment, predictive maintenance identifies potential problems before they lead to system failure.
This approach reduces downtime and enhances the reliability of gear systems.
Conclusion
Understanding the fundamentals of gears, wear prediction, and noise and vibration countermeasure technology is vital for the effective design and maintenance of mechanical systems.
By selecting the appropriate materials, employing design improvements, and utilizing modern monitoring tools, engineers can enhance gear performance and longevity.
Investing in predictive maintenance and timely interventions will not only extend the lifespan of gears but also ensure smoother and quieter operation.
資料ダウンロード
QCD管理受発注クラウド「newji」は、受発注部門で必要なQCD管理全てを備えた、現場特化型兼クラウド型の今世紀最高の受発注管理システムとなります。
ユーザー登録
受発注業務の効率化だけでなく、システムを導入することで、コスト削減や製品・資材のステータス可視化のほか、属人化していた受発注情報の共有化による内部不正防止や統制にも役立ちます。
NEWJI DX
製造業に特化したデジタルトランスフォーメーション(DX)の実現を目指す請負開発型のコンサルティングサービスです。AI、iPaaS、および先端の技術を駆使して、製造プロセスの効率化、業務効率化、チームワーク強化、コスト削減、品質向上を実現します。このサービスは、製造業の課題を深く理解し、それに対する最適なデジタルソリューションを提供することで、企業が持続的な成長とイノベーションを達成できるようサポートします。
製造業ニュース解説
製造業、主に購買・調達部門にお勤めの方々に向けた情報を配信しております。
新任の方やベテランの方、管理職を対象とした幅広いコンテンツをご用意しております。
お問い合わせ
コストダウンが利益に直結する術だと理解していても、なかなか前に進めることができない状況。そんな時は、newjiのコストダウン自動化機能で大きく利益貢献しよう!
(β版非公開)